Расчет состава пенобетона: Страница не найдена — Бетон
- Состав и пропорции пенобетона
- Описание состава
- Основные компоненты и стандарты, определяющие их свойства
- Пропорции смеси пеноблока
- Вяжущие
- Какие соблюдают пропорции при изготовлении пеноблока?
- Наполнители
- Как отдельные составляющие влияют на прочность продукции?
- Другие
- Что еще добавляют в раствор для улучшения показателей?
- Пенообразователь
- Вода
- Добавки
- Ускорители
- Пластификаторы
- Противоморозные добавки
- Пропорции для получения 1 м3 пенобетона
- Вывод
- Расчет состава ячеистых бетонов
- Состав и пропорции для пенобетона
- Компоненты бетона: для производства пенобетона, газобетона
- Какие компоненты входят в состав пенобетона?
- Описание состава
- Вяжущие
- Цемент
- Известь
- Наполнители
- Песок
- Зола
- Другие
- Пенообразователь
- Вода
- Добавки
- Ускорители
- Пластификаторы
- Противоморозные добавки
- Пропорции для получения 1 м3 пенобетона
- Марки D400
- Марки от D600 до D1000
- Марки D800
- Вывод
- Что входит в состав пенобетона
- Выпуск пенобетонных блоков
- Создание жидкого пенобетонного состава
- Формирование пенобетонных блоков
- Литьевой метод
- Резательный метод
- Высушивание изделий из пенобетона и уровень прочности
- Основные компоненты и стандарты, определяющие их свойства
- его изготовка в домашних условиях, пропорции на на 1 м3
- Расчет расхода материалов на пробный замес исходного состава ячеистого бетона
- (PDF) Исследование расчета пропорций смеси цементного пенобетона
- Материальный дизайн и оценка характеристик пенобетона для цифрового производства
- Реферат
- 1. Введение
- 2. Материалы и методы
- 2.1. Методология проектирования смесей и экспериментальная программа
- 2.2. Определение потребности в воде
- Таблица 1
- 2.3. Сырье
- Таблица 2
- 2.4. Процедура смешивания
- Таблица 3
- Таблица 4
- 2.5. Процесс 3D-печати
- 2.6. Подготовка образца
- 2.7. Механические испытания
- 2,8. Измерения теплопроводности
- 2.9. Сканирующая электронная микроскопия и световая микроскопия
- Расчет состава и состава пенобетона с легкими хвостовиками
- Производство пенобетона
- Базовый RGB
- Экспериментальные исследования соединителей сдвига в пенобетоне с заделкой канала C
- Проектирование пенобетонной смеси
Состав и пропорции пенобетона
Пенобетонные блоки являются одними из немногих материалов для строительства домов, которые можно изготавливать самостоятельно. Именно поэтому состав пенобетона интересен для многих начинающих, а иногда и достаточно опытных строителей. Дальше мы перечислим и подробно опишем все его составляющие, а также пропорции на 1 м3.
Блок: 1/3 | Кол-во символов: 389
Источник: https://KameDom.ru/penobeton/sostav.html
Описание состава
Состав пенобетона должен соответствовать нормативным документам. Раствор включает: цемент, песок, воду, образователи пены, дополнительные составляющие. Все ингредиенты должны отвечать стандартам. В зависимости от пропорций создают пенобетон разных марок, прочности.
Вернуться к оглавлению
Блок: 2/13 | Кол-во символов: 304
Источник: https://kladembeton.ru/raschety/sostav-penobetona.html
Основные компоненты и стандарты, определяющие их свойства
Свойства материала определяет ГОСТ 25485-89, в соответствии с которым производится классификация. В нем указаны основные требования к составу пенобетона и технические характеристики различных его марок. Кроме того, каждый из ингредиентов также должен соответствовать определенному стандарту. Вот список основных компонентов, из которых создается материал:
- цемент;
- песок;
- вода;
- пенообразователь;
- разнообразные необязательные добавки.
Рецепт семеси для пенобетона.
Вяжущим ингредиентом, участвующим в создании пенобетона, является портландцемент марок М500 Д20, М400 Д0, М400 Д20 (ГОСТ 10178). В качестве заполнителя используют песок, который должен содержать не менее 75% кварца (ГОСТ 8736). В песке допускается присутствие не более 3% примесей, содержащих ил и глину. Свойства воды определяет ГОСТ 23732. Пенообразователи могут быть как синтетическими, так и белковыми. Натуральные пенообразователи являются экологически чистыми, а изделия, в состав которых они входят — особо прочными.
Характеристики отдельных компонентов пенообразователя определяются следующими стандартами:
- сосновая канифоль — ГОСТ 191113;
- костный клей — ГОСТ 2067;
- мездровый клей — ГОСТ 3252;
- едкий натр (технический) — ГОСТ 2263;
- скрубберная паста — ТУ 38-107101.
Что касается необязательных добавок, то они у каждого производителя свои. К примеру, на некоторых заводах в пенобетон добавляют фиброволокно. Благодаря этому почти на четверть повышается прочность материала. Грани его блоков имеют четкий контур и практически не подвержены разрушению. В состав материала может входить и мелкодисперсная зола, образующаяся после сгорания твердого топлива. Самые крупные ее частицы не превышают 0,14 мм. Такая добавка позволяет увеличить прочность перегородок между отдельными порами материала и сэкономить до 30% цемента. К прочим добавкам относятся ускорители твердения, пластификаторы, биологически разлагаемые смазочные материалы для форм, красители.
Блок: 2/5 | Кол-во символов: 1984
Источник: https://ostroymaterialah.ru/smesi/sostav-penobetona.html
Пропорции смеси пеноблока
В зависимости от назначения готового изделия варьируется требуемая плотность, различная плотность достигается определенными особенностями в пропорции состава пеноблока.
Итак, если на выходе нам необходимо получить пеноблок плотностью менее 1800 кг на кубометр, то для смеси потребуются элементы в следующем соотношении (на фото можно увидеть разрез пеноблока такой плотности):
- 1320 кг песка кварцевого;
- 410 кг портландцемента;
- 184 л технической воды;
- 430 г пеноконцентрата
В результате такого замеса получаем 1930 кг пенобетона.
Если нам необходимо получить более легкий продукт с меньшей плотностью на кубометр, например 450 кг на куб.м., то схема состава сырья останется прежней, но песок будет исключен:
- портландцемент – 350 кг;
- техническая вода 150 л;
- пенообразователь в концентрированном виде – 1,5 кг.
Вес готового пенобетона на выходе при таком замесе составит около 500 килограмм.
Для изготовления раствора для пеноблоков можно применять различную рецептуру, состав которой будет отличаться. Так, например, для строительства технического одноэтажного помещения можно использовать синтетический пенообразователь, но экономить с его помощью на жилых помещениях опасно для здоровья.
Состав клея для пеноблоков
Строительство домов и других помещений из пеноблоков не обходится без использования специального клея. Причем с помощью такого клея можно не только обеспечить высокое качество межблочных швов, но и придать тепла и уюта дому.
Обычно купить клей для пеноблоков предлагают в виде сухого порошка (по 25 кг в мешке). В состав этого порошка входят следующие элементы:
- цемент,
- добавки-улучшители,
- специальный клеевой состав
Клей для укладки пеноблоков представляет собой сухую массу, разводить которую необходимо, соблюдая пропорции, указанные на упаковке. Целесообразно разводить клеевую смесь непосредственно перед использованием. Лучше для этого применять специальное устройство – дрель с размешивающей насадкой. Для разведения раствора для начала необходимо налить воду, затем при постоянном перемешивании постепенно вводить смесь в воду до достижения однородной массы. Затем раствору необходимо отдохнуть в течение 10 минут для полного растворения всех компонентов. После этого нужно еще раз все перемешать и можно приступать к укладке. Более подробно процесс замеса клея можно рассмотреть на видео.
Таким образом, состав и технология получения растворов достаточно просты и их можно приготовить в домашних условиях.
Блок: 3/3 | Кол-во символов: 2478
Источник: http://penobloki.trubygid.ru/sostav-smesi-dlya-penoblokov
Вяжущие
Вяжущей составной частью выступают известь, портландцемент — главное вещество, используемое строителями для возведения любого объекта. Соответствует ГОСТу 10178-85.
Вернуться к оглавлению
Цемент
Портландцемент твердеет под воздействием воды, воздуха. Представляет собой состав из известняка, глины, которые изначально поддали обжиганию. После спекания смеси происходит обогащение силикатом кальция. Качество клинкера — гранул смеси, влияет на прочность, устойчивость, долговечность сооружения. К нему добавляют гипс, позволяющий контролировать период схватывания стандартного цемента.
Портландцемент делится на 3 вида:
- D0 — отсутствуют добавки;
- D5 — смеси имеют меньше пяти процентов минеральных добавок активного действия;
- D20 — количество добавок варьирует от пяти до двадцати процентов, включая 10 % добавок — минералов гидравлического происхождения.
Марка цемента, используемого для пенобетона, плотностью 500 кг / м3, 400 кг / м3 с нулевым количеством примесей. Иногда используют марку 400 — 500, добавки в который составляют больше 5 %.
Вернуться к оглавлению
Известь
Иногда основным вяжущим компонентом выступает известь. Использование извести зависит от технологии изготовления ячеистого бетона. Основные требование к веществу: равномерный обжиг, общая активность выше 75 %, магния в составе меньше полутора процента. Общая активность извести определяется количеством активных окисей кальция, магния.
Известь могут использовать в виде молотой кипелки, пушонки. В замес добавляют двудонный гипс, замедляющий скорость гашения извести. Также применяют полуводный гипс с поташом.
Вернуться к оглавлению
Блок: 3/13 | Кол-во символов: 1603
Источник: https://kladembeton.ru/raschety/sostav-penobetona.html
Какие соблюдают пропорции при изготовлении пеноблока?
Если быть до конца честным, то каждый производитель имеет свои, универсальные пропорции всех компонентов. Но мы приведем общие рекомендации по составу, которые можно смело брать за основу при изготовлении.
Таблица основных компонентов пенобетонаУровень плотности, кг/м3 400 600 800Портландцемент, кг | 300 | 330 | 400 |
Вода, л | 160 | 180 | 1230 |
Вспениватель, кг | 0,85 | 1,1 | 1,1 |
Песок, кг | нет | 210 | 400 |
Стоит учитывать, что также нужно использовать связующее вещество определенной марки, для получения смеси с оптимальными для изготовления блоков показателями плотности структуры.
Все данные из таблицы определены нормативами ГОСТ.
Зная точные пропорции материала и его состав, можно ориентироваться в качественных показателях пенобетона, который собираетесь купить у производителя. Также не помешает найти отзывы о нем от реальных людей – многие пытаются экономить и используют сырье низкого качества.
Похожие публикации
Блок: 3/3 | Кол-во символов: 1017
Источник: https://KameDom.ru/penobeton/sostav.html
Наполнители
В качестве наполнителей выступают песок, зола, другие вещества (трепел, драгомит и т п). Пенобетон марки 500 делают, исключая наполнители. Применение наполнителей тонкого помола возможно. Пеноблок плотнее отметки 600 кг / м3 изготовляется с использованием песка.
Вернуться к оглавлению
Песок
Чем мельче песок, тем качественнее пенобетон.
Должен отвечать ГОСТу 8736: кварц в составе должен превышать семьдесят пять процентов, домеси — меньше трех процентов. Песчинки должны быть как можно меньше. Их размер влияет на качество пенобетона — менее прочный, неравномерный пеноблок, сделанный из крупнозернистого песка. Используют песок из рек, оврагов — он промытый.
Вернуться к оглавлению
Зола
Может частично или полностью заменить песок в пенобетоне, около тридцати процентов цемента экономится. Во многих регионах используют золу-унос — отходы работы теплоэлектростанций. Повысит прочность пеноблоков на основе золы термовлажностная обработка.
Вернуться к оглавлению
Блок: 4/13 | Кол-во символов: 971
Источник: https://kladembeton.ru/raschety/sostav-penobetona.html
Как отдельные составляющие влияют на прочность продукции?
Разумеется, чем выше марка портландцемента, тем более прочным получится и производимый из него пенобетон. Но не последнюю роль в смеси играет и тонкость помола вяжущего ингредиента. Если был использован цемент более крупного помола, чем указано в ГОСТ 10178, его количество потребуется увеличить на 10%. Отклонение от стандарта приведет к тому, что состав будет затвердевать значительно дольше, а это, в свою очередь, потребует введения дополнительных добавок, ускоряющих твердение.
Составляющие, которые используют для производства пенобетона влияют на его прочность.
С увеличением плотности пенобетона для его изготовления используют песок более высокой зернистости. К примеру, зернистость песка для марок плотностью 400-1200 кг/м3 составляет от 0 до 2 мм, а при плотности 1400-1600 кг/м3 требуется песок зернистостью от 0 до 4 мм. В то же время использование мелкозернистого песка с размером частиц менее 1 мм позволяет увеличить прочность состава при той же плотности. Однако подобная практика применяется довольно редко, так как материал, отвердевая, дает повышенную усадку.
Использование в производстве пенобетона обычной водопроводной воды может привести к снижению качества, если она не соответствует установленному стандарту по кислотности или содержанию минеральных солей. Особой чистоты требует вода, в которой разводится сухой пенообразователь. Температура жидкости должна находиться в диапазоне от 10 до 60°С, хотя многие специалисты считают, что воду теплее 25°С лучше не использовать. Чтобы снизить содержание жидкости в материале и тем самым повысить его прочность, в состав обычно вводят разнообразные пластификаторы. Тем не менее соотношение воды и цемента не должно быть ниже 0,4. В противном случае цемент станет забирать воду из раствора пенообразователя.
Данный компонент обходится несколько дороже синтетических аналогов, но и расходуется более экономно, да и пену образует более стабильную. Иногда недобросовестные производители при выпуске синтетического состава используют пенообразователь, который был изготовлен для пожаротушения. Его применение приводит к значительному снижению характеристик получаемого материала.
Причин, по которым рекомендуется использовать для пенобетона белковый, а не синтетический пенообразователь, существует достаточно много. Основной из них является безопасность для человека ввиду полного отсутствия ядовитых испарений.
Блок: 4/5 | Кол-во символов: 2438
Источник: https://ostroymaterialah. ru/smesi/sostav-penobetona.html
Другие
Известняк тонкого помола добавляют пропорцией 20 до 30 процентов от массы цемента. Он играет роль наполнителя на микроскопическом уровне, позволяющего снизить внутреннюю напряженность во время затвердения. Такая примесь придает составу пенобетона дополнительную морозостойкость, понижает его себестоимость.
Микрокремнезем применяют для придания прочности пенобетону. Добывается в процессе плавки ферросилиция в электрической печке в виде конденсата из шаровидных микрочастиц пыли.
Полипропиленовая фибра защищает пенобетон от пластичных изменений на первом этапе затвердения смеси, предотвращая появление микроскопических трещин. Длина используемой фибры для пенобетона 0,6 — 2 см. Пеноблоки с фиброй отличаются прочностью, морозостойкостью, четкими крепкими гранями.
Вернуться к оглавлению
Блок: 5/13 | Кол-во символов: 794
Источник: https://kladembeton.ru/raschety/sostav-penobetona.html
Что еще добавляют в раствор для улучшения показателей?
Для получения пенобетона особой прочности на многих предприятиях в смесь вводят тонкомолотый известняк. Он не приводит к возникновению трещин, как другие добавки, не утяжеляет изделие, как песок, позволяет сэкономить цемент. Карбонизация раствора повышает устойчивость изделия к механическим нагрузкам. Масса известковой муки может составлять до 20-30% от массы цемента. Такой состав после твердения обеспечивает более высокую морозостойкость, чем смесь компонентов без добавок.
Противоморозные добавки вводятся для того, чтобы предотвратить промерзание раствора при низких температурах. Они делают его более пластичным, увеличивают скорость связывания цемента, обеспечивают ускоренное выделение тепла, образуемого при гидратации, снижают на 7-10% массу воды, необходимой для состава. Чтобы улучшить водонепроницаемость, увеличить устойчивость к повышенной температуре и кислотности, в раствор добавляют микрокремнезем.
Гидрофобизаторы и воздухововлекающая смола предназначены для снижения расслаивания пенобетона при транспортировке, улучшения таких характеристик, как водонепроницаемость, морозостойкость и удобоукладываемость. Добавление 0,5 кг полипропиленовой фибры на 1 м3 смеси значительно снижает количество бракованной продукции при производстве, а также потерь при транспортировке. Фибра повышает устойчивость к ударам и механическим нагрузкам, предупреждает растрескивание. С введением в состав до 1 кг фибры повышается марка конечной продукции.
Блок: 5/5 | Кол-во символов: 1515
Источник: https://ostroymaterialah.ru/smesi/sostav-penobetona.html
Пенообразователь
Для создания пористости материала добавляют пенообразователь, состав которого включает: костный и мездровый клей, канифоль, каустическая сода, паста скрубберная. Состав раствора требует малой пропорции пенообразователя.
Пенообразователь делится на:
- искусственные;
- натуральные — белковые;
- клеекремневые.
Качество немецких и итальянских производителей натуральных образователей пены доказано. Стоимость таких добавок будет выше. В конечном результате пенобетон выровняет себестоимость при меньших затратах на портландцемент.
Вернуться к оглавлению
Блок: 6/13 | Кол-во символов: 556
Источник: https://kladembeton.ru/raschety/sostav-penobetona.html
Вода
Вода должна соответствовать стандартам. Применяют чистую воду без жира, масла, керосина температурой выше 10 градусов, не больше 60. Теплая вода позволяет в холодную пору года повысить скорость гидратации, снизить возможность трещин. Для разведения смеси пенобетона вода должна быть более мягкой, чистой, чтоб образовалось нужное количество пены.
Вернуться к оглавлению
Блок: 7/13 | Кол-во символов: 373
Источник: https://kladembeton.ru/raschety/sostav-penobetona.html
Добавки
Часто используют составы пенобетонов с присадками: антифризовыми, ускорителями твердения, пластификаторами. Необходимость применения добавок определяется технологией, материалами, желаемым результатом.
Вернуться к оглавлению
Блок: 8/13 | Кол-во символов: 231
Источник: https://kladembeton. ru/raschety/sostav-penobetona.html
Ускорители
Ускорители нужны для повышения сохнущих способностей на начальных этапах твердения, особенно при необходимости возведения прочного каркаса. Ускорители:
- электролиты — повышают способность разведения цемента;
- нитрат, нитрит кальция, поташ — повышают плотность;
- гидросульфоалюминат кальция повышает кристаллизацию;
- хлористый кальций позволяет быстро твердеть, имеет низкую стоимость, для нужного эффекта достаточно низкой дозы.
Ускорение должно отвечать требованием:
- не должно быть чересчур быстрым, чтоб качественно выложить раствор;
- низкая стоимость добавок;
- простота в использовании.
Добавление в раствор силикатного стекла должно быть 2,4 % от количества цемента. Имея такую дозировку, он делает смесь более плотной. При большей дозе, вызывает быстрое схватывание в момент замеса, снижает прочность пенобетона.
Вернуться к оглавлению
Блок: 9/13 | Кол-во символов: 835
Источник: https://kladembeton. ru/raschety/sostav-penobetona.html
Пластификаторы
Введения таких добавок позволяет смеси стать более пластичной, гибкой. Они позволяют снизить температуру технического воздействия на конструкцию, помогают лучше переносить раствору морозы, при этом снижают способность сохранять тепло.
Требования, выдвигаемые к пластификаторам:
- совместимость со всеми ингредиентами;
- низкий уровень летучести;
- отсутствие какого-либо аромата;
- химически неактивные вещества;
- не должны растворять полимеры в составе.
Вернуться к оглавлению
Блок: 10/13 | Кол-во символов: 475
Источник: https://kladembeton.ru/raschety/sostav-penobetona.html
Противоморозные добавки
Данные вещества позволяют проводить работы связанные с бетонными растворами в зимнее время. Предотвращают замораживание воды в бетоне, таким образом, он не разрушается морозами сохраняет прочность.
Вернуться к оглавлению
Блок: 11/13 | Кол-во символов: 243
Источник: https://kladembeton. ru/raschety/sostav-penobetona.html
Пропорции для получения 1 м3 пенобетона
Марки D400
Отличается низкими прочностными особенностями, применяется в качестве утеплителя. Имеет пропорции:
- портландцемент — 300 кг;
- песок 120 кг;
- образователи пены — 850 г;
- вода 155 л.
Вернуться к оглавлению
Марки от D600 до D1000
Создают хорошую конструкцию, держат тепло, подходят для строительства домов. Имеет пропорции:
- портландцемент — 325 кг;
- песок — 205 кг;
- пенообразователь — 1,05 кг;
- вода — 182 л.
Вернуться к оглавлению
Марки D800
Пропорции:
- портландцемент — 390 кг;
- песок — 335 кг;
- пенообразователь — 1 кг;
- вода — 225 л.
Вернуться к оглавлению
Блок: 12/13 | Кол-во символов: 578
Источник: https://kladembeton.ru/raschety/sostav-penobetona.html
Вывод
Пенобетон — качественный строительный материал, пользуется большим спросом. Имеет простой состав, обеспечивающий его положительные особенности, экологическую безопасность.
Блок: 13/13 | Кол-во символов: 176
Источник: https://kladembeton.ru/raschety/sostav-penobetona.html
Кол-во блоков: 19 | Общее кол-во символов: 18606
Количество использованных доноров: 4
Информация по каждому донору:
- https://kladembeton.ru/raschety/sostav-penobetona.html: использовано 12 блоков из 13, кол-во символов 7139 (38%)
- http://penobloki.trubygid.ru/sostav-smesi-dlya-penoblokov: использовано 1 блоков из 3, кол-во символов 2478 (13%)
- https://ostroymaterialah.
ru/smesi/sostav-penobetona.html: использовано 4 блоков из 5, кол-во символов 7583 (41%)
- https://KameDom.ru/penobeton/sostav.html: использовано 2 блоков из 3, кол-во символов 1406 (8%)
Расчет состава ячеистых бетонов
Расчет состава ячеистых бетонов основан на следующих положениях:
1. любой единичный объем состоит из объема цемента, наполнителя и объема пор, часть которых заполенена водой, что может быть представлено для объема смеси 1 куб. м. в виде уравнения
(1)
где:
Ц — расход цемента кг\куб. м.
Н — расход наполнителя, кг\куб. м.
В — расход воды, л\куб. м.
Vпор — объем пор за счет применения порообразователя, л
— соответственно истинная плотность цемента и наполнителя кг\л
Расчетная плотность ячеистого бетона
1,15Ц+Н= (2)
Соотношение между цементом и наполнителем Н/Ц=С принимается по таблице 1.
Таблица 1
Соотношение С=Н/Ц для ячеистых бетонов
Бетоны | |
автоклавные | неавтоклавные |
1-1,75 | 0,75-1,25 |
Из уравнения (2) с учетом данных таблицы 1 получим:
1,15Ц+СЦ= (3)
откуда
Ц=/(1,15+С) (4)
Н=СЦ (5)
Из уравнения (1), принимая В=(В/Т)(Ц+Н), где В/Т — водотвердое отношение, принимаемое по таблице 2, получим
(6)
откуда определяется требуемое количество пор за счет применения порообразователя.
Таблица 2
Ориентировочные значения В/Т
Средняя плотность ячеистого бетона | В/Т |
300 | 0,45 |
500 | 0,4 |
700 | 0,35 |
900 | 0,3 |
Примечание: Значения В/Т более точно определяются экспериментальным путем. При этом в качестве основного критерия принимается требуемая текучесть смеси, значения которой представлены в таблице 3
Таблица 3
Требуемая текучесть смеси по Суттарду при литьевом способе формирования
Средняя плотность ячеистого бетона | Диаметр расплыва по Суттарду, см |
300 | 38 |
500 | 30 |
700 | 22 |
900 | 14 |
Далее определяется необходимое количество порообразователя Д:
(7)
где К — коэффициент, учитывающий эффективность использования газообразующей добавки — алюминиевой пудры, принимается равным 0,85
(7)
где К — коэффициент, учитывающий эффективность использования пенообразователя, принимается по опытным данным. Допускается для предварительной оценки состава принимать К=0,8
Состав и пропорции для пенобетона
Пенобетон, как и газобетон, относится к ячеистым бетонам. Кроме того, их сходство заключается в том, что оба эти стройматериала имеют пористую структуру, которая служит хорошим теплоизолятором, но, тем не менее, технология их изготовления существенно отличается друг от друга и, соответственно, каждый из них, за счет этого, приобретает свои персональные свойства.
Пенобетон, в отличии от газобетона, можно сделать своими руками.
Оборудование для производства
В процессе производства газобетона, его твердение должно происходить в автоклавных условиях (в среде, насыщенной паром, и при давлении, которое должно быть выше атмосферного), что требует наличия специального дорогостоящего оборудования. Словом, его целесообразней производить в заводских условиях.
Пенобетон же, создается неавтоклавным (затвердевание происходит в естественных условиях) способом, и по этой причине его возможно изготовить своими руками, что существенно экономит расходы.
Формы для блоков можно приобрести в строительном магазине, а можно сделать и самостоятельно.
Его производство настолько несложное, что, если зная пропорции для пенобетона, данный материал можно сделать даже в домашних условиях. Для этого понадобится приобрести или самостоятельно смастерить такое оборудование, как:
- формы для отливки блоков;
- растворомешалку;
- компрессор, который должен быть рассчитан на переменное напряжение 220 Вт, иметь мощность 0,3 – 0,5 м3 и давление 6 Атм;
- пеногенератор.
Пропорции компонентов
Изготовление пенобетонных блоков включает в себя соблюдение точных пропорций, а также четкой последовательности добавления компонентов в процессе всего производства. Несоблюдение этих правил может отрицательно сказаться на качестве пеноблока. Кроме того, чтобы получить стабильный результат от каждой выпускаемой партии понадобиться приобрести навык, поскольку от температуры и влажности окружающей среды, видов применяемых пенообразователей, способов получения пены, метода добавления пены в смесь, формовки и сушки уже готовых изделий будет зависеть конечный результат. Прежде чем приступать к производству пенобетона, необходимо подготовить такие компоненты, из которых он состоит:
- цемент;
- песок;
- вода;
- пенообразователь.
Далее, когда материал и оборудование подготовлено, необходимо изучить пропорции компонентов для производства пенобетона, которые определяются в зависимости от требуемой марки ячеистого материала. Так, изменяя соотношение компонентов и его состав, можно производить различные виды пенобетона, которые, в зависимости от этого, используются либо для строительства внешних стен, либо при изготовлении внутренних перегородок, термоизоляции крыш, либо для термо- и звукоизоляции междуэтажных покрытий.
Например, для производства пеноблока марки D400 в количестве 1 куб. м, который имеет низкий класс прочности и из-за этого используется только в качестве теплоизоляционного материала, соотношение компонентов будут иметь такие показатели:
- Цемент – 300 кг.
- Песок – 120 кг.
- Пенообразователь – 0,85 кг.
- Вода – 160 л.
К более прочному и универсальному стройматериалу относятся пеноблоки маркой от D600 до D1000, которые считаются конструкционно-теплоизоляционными видами. Они отлично подходят для строительства небольших домов и коттеджей, а также для возведения зданий в регионах с невысокой сейсмической опасностью. Так, для производства 1 м куб. пенобетона марки D600 понадобится:
- Цемент – 330 кг.
- Песок – 210 кг.
- Пенообразователь – 1,1 кг.
- Вода – 180 л.
В состав 1 м куб. пеноблока марки D800 входят компоненты с такой пропорцией:
- Цемент – 400 кг.
- Песок – 340 кг.
- Пенообразователь – 1,1 кг.
- Вода – 230 л.
Из вышенаписанного можно сделать вывод: чем больше добавляется цемента и песка в нужной пропорции, тем пенобетон приобретает выше марку и, соответственно, его прочность и другие качества улучшаются. Но, опять же, при его производстве учитываются и другие факторы, которые включены в технологию изготовления данного стройматериала и влияют на конечный результат продукции.
Компоненты бетона: для производства пенобетона, газобетона
Компоненты бетона определяют его качество, прочность, марочную и классовую принадлежность, а также массу других параметров и характеристик раствора и затвердевшего материала. Мы расскажем, какое соотношение компонентов бетона считается нормальным, а также покажем, как произвести расчет компонентов для бетона.
Состав бетона и пропорции его ингредиентов напрямую определяют качество и прочность готового материала.
Компонентный состав бетонной смеси
Общие сведения
Однородная на вид масса состоит из нескольких субстанций.
Бетоном принято называть искусственный камень, который производят методом затворения вяжущего вещества водой с введением крупных и мелких заполнителей, а также различных целевых добавок – пластификаторов, гидрофобизаторов, антисептиков и т. д. Существуют также безводные бетоны, такие как асфальтобетон и некоторые другие.
Мы будем говорить о традиционных бетонах, применяемых в гражданском строительстве – смесях на основе цемента в качестве вяжущего вещества, так как помимо цемента в качестве вяжущих используют различные шлаки, полимеры, смолы и т.д.
Цемент – основной компонент бетонного раствора.
Итак, для производства цементобетона используют такие ингредиенты:
- Портландцемент (иногда быстротвердеющий шлакоцемент) – минеральная пыль, которая вступает в реакцию гидратации с водой и твердеет с образованием плотного и твердого камня. Играет роль клея, который связывает все компоненты в одну монолитную структуру;
- Песок – мелкий заполнитель, который способствует экономии цемента и играет роль в создании мелкоструктурного каркаса, предотвращающего деформации и образование микротрещин при твердении и усадочных процессах;
- Щебень – крупный заполнитель, который наряду с песком удешевляет смесь, так как цена заполнителей невысока.
Препятствует разрушениям во время усадки и твердения, создает структурный каркас и повышает модуль упругости материала, а также уменьшает его ползучесть;
- Вода – один из важнейших компонентов смеси, который участвует в процессе гидратации цемента и образовании твердеющего клея, а также является средой, где происходит перемешивание, взаимодействие и равномерное распределение остальных составляющих раствора;
- Добавки – пластификаторы, гидрофобизаторы, антисептики, уплотнители и прочие. Повышают определенные показатели, такие как текучесть, влагостойкость, морозоустойчивость, химическую и биологическую инертность, плотность и т.д.
На фото – цементный камень, получаемый в процессе гидратации цемента.
Важно! Как видим, состав бетонной смеси неоднороден, поэтому качество продукта зависит от многих переменных. Марки бетона и соотношения компонентов, а также их качество и тип связаны прямой зависимостью.
Требования к компонентам
Для производства качественного раствора своими руками следует правильно подбирать его состав.
Теперь поговорим о компонентах подробнее. Одним из основных составляющих, без которого не получится ничего, является цемент. В строительстве, как правило, используют портландцемент марок М300 – М500, однако следует учитывать, что для производства бетона марки М350 потребуется цемент не ниже М500, а из цемента М400 получится бетон марки не выше М250.
Марка показывает предел прочности материала на сжатие, и для индивидуального и гражданского строительства прочности М250 – М350 вполне достаточно, поэтому вы можете смело использовать продукт марки М500 даже для ответственных узлов. Единственное замечание – соотношение компонентов в бетоне для фундамента должно быть подобрано наиболее тщательно, поэтому для бетонирования этой части дома обычно используют раствор товарного качества с завода.
Наиболее подходящая для индивидуального изготовления бетонного раствора марка.
Щебень – еще один важный ингредиент смеси. Считается, что прочность щебня должна примерно вдвое превышать проектную прочность бетона, которую он набирает в течение 28 дней. Это связано с тем, что бетонный камень вызревает несколько лет и набирает дополнительную прочность, которая в результате становится примерно равной прочности щебня, который остается прежним по этому показателю.
Для изготовления традиционного бетона достаточно прочности гравийного щебня, которая составляет примерно 800 – 1000 кгс/кв. см, чего вполне достаточно для получения бетонного материала марки М450. Для производства изделий марки М100 – М300 можно использовать известняковый щебень, но самым прочным и дорогим является гранитный камень, который чаще всего используют для производства специальных, дорожных и высокопрочных разновидностей бетона.
Для жилищного строительства вполне подойдет обычный карьерный гравий.
Важно! Иногда намеренно используют непрочный известняковый щебень, например, когда предстоит шлифовка или резка железобетона алмазными кругами. Также таким способом облегчается алмазное бурение отверстий в бетоне.
Песок можно использовать карьерный или речной, промытый от глинистых и пылевидных примесей. Чаще всего применяют среднюю и мелкую фракцию, а для изготовления пескобетона берут песок крупного размера зерен.
Если говорить о добавках, то стоит сразу отметить, что качественное введение химикатов возможно только в условиях фабричного производства. Компоненты для производства газобетона, например, включают алюминиевые пудры, пасты и эмульсии, дозировка которых должна быть точной.
Введение добавок требует точного соблюдения рецептуры и условий производства.
Аналогично, компоненты для производства пенобетона – пенообразователи – также нуждаются в точном соответствии рецептуре, так как компоненты для пенобетона могут испортить материал и понизить его марку при незначительном отклонении от нормы.
Расчет
Учимся правильно определять соотношение и пропорции ингредиентов.
Как было сказано, соотношение компонентов – важнейший параметр при производстве бетонной смеси. Классическая инструкция предполагает такую пропорцию (цемент/щебень/песок/вода): 1:4:2:0. 5. Числа в пропорции соответствуют массовым долям.
Само собой, такое соотношение весьма условно и примерно, так как на практике мы имеем дело с реальными материалами, которые имеют множество примесей, по-разному поглощают воду, имеют различную исходную влажность. Для более точного определения рецептуры следует пользоваться таблицами и специальными компьютерными программами, однако и они не гарантируют соответствия полученного продукта ожидаемой марке или классу.
Для вычисления количества ингредиентов можно использовать таблицы.
Даже в условиях заводов, где есть лаборатории и специальное оборудование для взвешивания, дозировки, смешивания и подготовки компонентов, приходится делать обязательные испытания полученного камня на прочность, и только после этого можно уверенно говорить о классовой или марочной принадлежности полученного материала.
Для определения марки материал испытывают на предельную прочность.
Существует способ расчета компонентного состава в полевых условиях:
- В десятилитровое ведро насыпаем щебень до верха и встряхиваем емкость, чтобы камень распределился по объему ведра равномерно;
- С помощью литровой банки или иной мерной посуды доливаем воду в ведро с гравием до тех пор, пока она не сравняется с ним по уровню.
Запоминаем количество воды. Так мы определили необходимый объем песка;
- Теперь высыпаем щебень и наполняем ведро сухим песком в том объеме, который мы только что определили. Затем снова доливаем воду мерной банкой (лучше той же) до уровня покрытия песка водой. Количество воды будет равно необходимому объему цемента;
- Чтобы определить оптимальное количество воды, следует взять 50 – 60% объема цемента, который мы нашли экспериментально в предыдущем пункте;
- В конце следует взять расчетный объем бетонировки и разделить его на объем одного ведра – 10 л, а полученное число умножить на вычисленные ранее значения для каждого компонента.
Определить пропорцию поможет обычное ведро.
Важно! Для ответственных работ используйте товарный бетон проверенных производителей, так как сделать качественный продукт в полевых условиях проблематично в силу ряда непреодолимых причин.
Вывод
Качество, тип и соотношение компонентов определяют марку бетонного раствора и прочность будущего изделия. Для определения оптимальных пропорций существуют различные способы, однако добиться в полевых условиях точного соответствия проблематично (см.также статью «Бетон М150 – технические характеристики и особенности применения»).
Видео в этой статье поможет вам в этом убедиться.
Какие компоненты входят в состав пенобетона?
Основным отличием пенобетона от бетона стандартного можно считать пористую структуру, легкость. Состав пенобетона играет большую роль для получения дышащего, водонепроницаемого, легкого материала.
Описание состава
Состав пенобетона должен соответствовать нормативным документам.
Раствор включает: цемент, песок, воду, образователи пены, дополнительные составляющие. Все ингредиенты должны отвечать стандартам. В зависимости от пропорций создают пенобетон разных марок, прочности.
Вернуться к оглавлению
Вяжущие
Вяжущей составной частью выступают известь, портландцемент — главное вещество, используемое строителями для возведения любого объекта. Соответствует ГОСТу 10178-85.
Вернуться к оглавлению
Цемент
Портландцемент твердеет под воздействием воды, воздуха. Представляет собой состав из известняка, глины, которые изначально поддали обжиганию. После спекания смеси происходит обогащение силикатом кальция.Качество клинкера — гранул смеси, влияет на прочность, устойчивость, долговечность сооружения.К нему добавляют гипс, позволяющий контролировать период схватывания стандартного цемента.
Портландцемент делится на 3 вида:
- D0 — отсутствуют добавки;D5 — смеси имеют меньше пяти процентов минеральных добавок активного действия;D20 — количество добавок варьирует от пяти до двадцати процентов, включая 10 % добавок — минералов гидравлического происхождения.
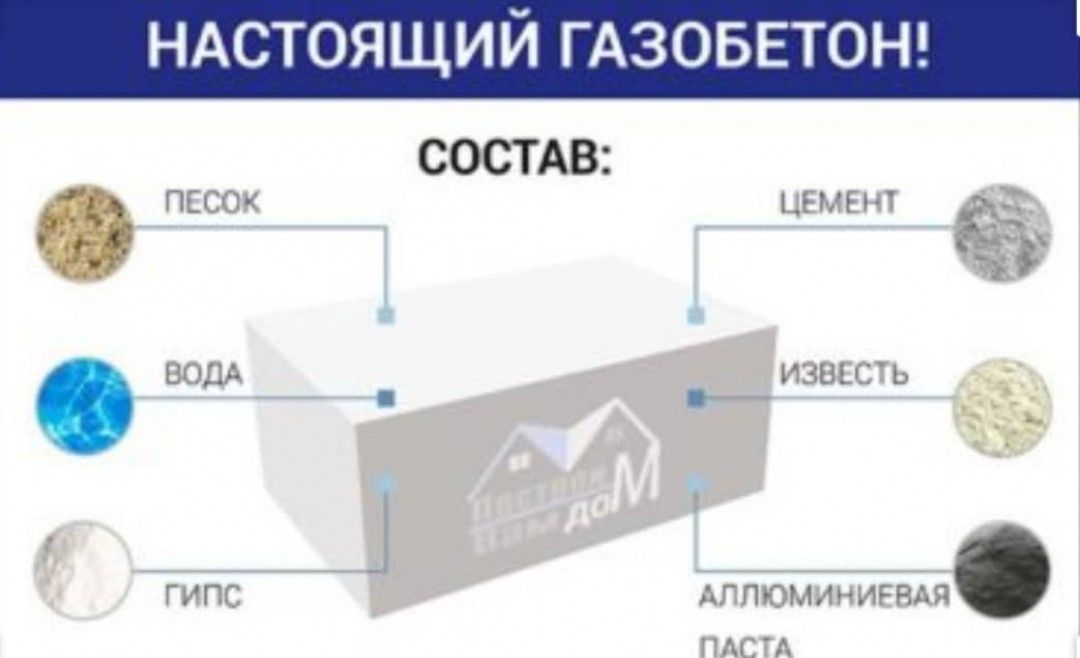
Марка цемента, используемого для пенобетона, плотностью 500 кг / м3, 400 кг / м3 с нулевым количеством примесей. Иногда используют марку 400 — 500, добавки в который составляют больше 5 %.
Вернуться к оглавлению
Известь
Иногда основным вяжущим компонентом выступает известь.
Использование извести зависит от технологии изготовления ячеистого бетона. Основные требование к веществу: равномерный обжиг, общая активность выше 75 %, магния в составе меньше полутора процента. Общая активность извести определяется количеством активных окисей кальция, магния.
Известь могут использовать в виде молотой кипелки, пушонки. В замес добавляют двудонный гипс, замедляющий скорость гашения извести. Также применяют полуводный гипс с поташом.
Вернуться к оглавлению
Наполнители
В качестве наполнителей выступают песок, зола, другие вещества (трепел, драгомит и т п).
Пенобетон марки 500 делают, исключая наполнители. Применение наполнителей тонкого помола возможно. Пеноблок плотнее отметки 600 кг / м3 изготовляется с использованием песка.
Вернуться к оглавлению
Песок
Чем мельче песок, тем качественнее пенобетон.
Должен отвечать ГОСТу 8736: кварц в составе должен превышать семьдесят пять процентов, домеси — меньше трех процентов.
Песчинки должны быть как можно меньше. Их размер влияет на качество пенобетона — менее прочный, неравномерный пеноблок, сделанный из крупнозернистого песка. Используют песок из рек, оврагов — он промытый.
Вернуться к оглавлению
Зола
Может частично или полностью заменить песок в пенобетоне, около тридцати процентов цемента экономится. Во многих регионах используют золу-унос — отходы работы теплоэлектростанций. Повысит прочность пеноблоковна основе золы термовлажностная обработка.
Вернуться к оглавлению
Другие
Известняк тонкого помола добавляют пропорцией 20 до 30 процентов от массы цемента. Он играет роль наполнителя на микроскопическом уровне, позволяющего снизить внутреннюю напряженность во время затвердения. Такая примесь придает составу пенобетона дополнительную морозостойкость, понижает его себестоимость.
Микрокремнезем применяют для придания прочности пенобетону.Добывается в процессе плавки ферросилиция в электрической печке в виде конденсата из шаровидных микрочастиц пыли.
Полипропиленовая фибра защищает пенобетон от пластичных изменений на первом этапе затвердения смеси, предотвращая появление микроскопических трещин. Длина используемой фибры для пенобетона 0,6 — 2 см. Пеноблоки с фиброй отличаются прочностью, морозостойкостью, четкими крепкими гранями.
Вернуться к оглавлению
Пенообразователь
Для создания пористости материала добавляют пенообразователь, состав которого включает: костный и мездровый клей, канифоль, каустическая сода, паста скрубберная. Состав раствора требует малой пропорции пенообразователя.
Пенообразователь делится на:
- искусственные;натуральные — белковые;клеекремневые.
Качество немецких и итальянских производителей натуральных образователей пены доказано. Стоимость таких добавок будет выше. В конечном результате пенобетон выровняет себестоимость при меньших затратах на портландцемент.
Вернуться к оглавлению
Вода
Вода должна соответствовать стандартам.
Применяют чистую воду без жира, масла, керосина температурой выше 10 градусов, не больше 60. Теплая вода позволяет в холодную пору года повысить скорость гидратации, снизить возможность трещин. Для разведения смеси пенобетона вода должна быть более мягкой, чистой, чтоб образовалось нужное количество пены.
Вернуться к оглавлению
Добавки
Часто используют составы пенобетонов с присадками: антифризовыми, ускорителями твердения, пластификаторами. Необходимость применения добавок определяется технологией, материалами, желаемым результатом.
Вернуться к оглавлению
Ускорители
Ускорители нужны для повышения сохнущих способностей на начальных этапах твердения, особенно при необходимости возведения прочного каркаса. Ускорители:
- электролиты — повышают способность разведения цемента;нитрат, нитрит кальция, поташ — повышают плотность;гидросульфоалюминат кальция повышает кристаллизацию;хлористый кальций позволяет быстро твердеть, имеет низкую стоимость, для нужного эффекта достаточно низкой дозы.
Ускорение должно отвечать требованием:
- не должно быть чересчур быстрым, чтоб качественно выложить раствор;низкая стоимость добавок;простота в использовании.
Добавление в раствор силикатного стекла должно быть 2,4 % от количества цемента. Имея такую дозировку, он делает смесь более плотной. При большей дозе, вызывает быстрое схватывание в момент замеса, снижает прочность пенобетона.
Вернуться к оглавлению
Пластификаторы
Введения таких добавок позволяет смеси стать более пластичной, гибкой. Они позволяют снизить температуру технического воздействия на конструкцию, помогают лучше переносить раствору морозы, при этом снижают способность сохранять тепло.
Требования, выдвигаемые к пластификаторам:
- совместимость со всеми ингредиентами;низкий уровень летучести;отсутствие какого-либо аромата;химически неактивные вещества;не должны растворять полимеры в составе.
Вернуться к оглавлению
Противоморозные добавки
Данные вещества позволяют проводить работы связанные с бетонными растворами в зимнее время. Предотвращают замораживание воды в бетоне, таким образом, он не разрушается морозами сохраняет прочность.
Вернуться к оглавлению
Пропорции для получения 1 м3 пенобетона
Марки D400
Отличается низкими прочностными особенностями, применяется в качестве утеплителя. Имеет пропорции:
- портландцемент — 300 кг;песок 120 кг;образователи пены — 850 г;вода 155 л.
Вернуться к оглавлению
Марки от D600 до D1000
Создают хорошую конструкцию, держат тепло, подходят для строительства домов. Имеет пропорции:
- портландцемент — 325 кг;песок — 205 кг;пенообразователь — 1,05 кг;вода — 182 л.
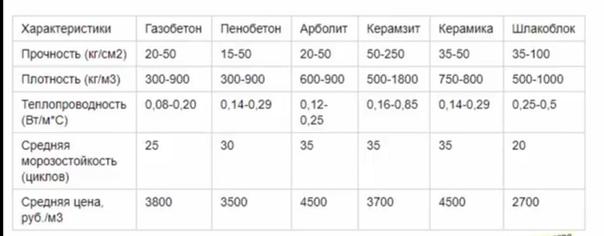
Вернуться к оглавлению
Марки D800
Пропорции:
- портландцемент — 390 кг;песок — 335 кг;пенообразователь — 1 кг;вода — 225 л.
Вернуться к оглавлению
Вывод
Пенобетон — качественный строительный материал, пользуется большим спросом. Имеет простой состав, обеспечивающий его положительные особенности, экологическую безопасность.
Состав пенобетона
Состав пенобетона интересует людей дела, которые хотят наладить производство и сделать на этом свой бизнес. Из чего делают пеноблоки состав и правила производства мы рассмотрим ниже. Будет предложена инструкция, по которой вы без проблем просчитаете затраты на производство и определите, на сколько будет выгодно производство.
Что входит в состав пенобетона
Химический состав пеноблока довольно прост, надо приобретать качественные материалы и тогда с качеством продукции не будет проблем. Тем более вся работа вполне может быть сделана и своими руками, тогда и себестоимость будет гораздо ниже.
Пенобетон и пеноблоки состав по плотности материала
Внимание: Для производства высококачественного пенобетона нужно с особой осторожностью выбирать необходимые компоненты, верно определять объем, вес, соблюдать требуемые правила влажности изделия, тепловой обработки.
Воспроизводство пенобетона осуществляется в соответствии с установленными нормами и правилами, выбор необходимых составляющих изделия соответствует государственному стандарту № 25485-89 (см. Пеноблок: технические характеристики и другие важные параметры). В соответствии с государственным стандартом № 8736, в состав пеноблоков входит песок, содержащий 75 % кварца.
- Портландемент устанавливается по государственному стандарту № 10178.Пеноблоки химический состав включают в себя канифоль по государственному стандарту № 191113. Если в составе присутствует клей, то его выбор должен быть осуществлен по государственному стандарту № 2067.Стандарт № 3252 используют при поиске и выборе пенообразователя.

Пеноблок химический состав может быть довольно разным, все зависит от добавок. Он может готовиться из различных комбинаций ингредиентов.
Все это способствует производству различных видов материала.
От видовой принадлежности пенобетона зависит их целевое использование. Пенобетонные блоки применяются при кладке звукоизолирующих перегородок (см. Как делается перегородка из пеноблоков), стен зданий.
Не большая цена и прекрасные показатели морозоустойчивости сделали его популярным. Но у него есть и существенный недостаток, жилое помещение надо будет облицевать, а это затраты. Но слой утеплителя можно будет делать и не большой, ведь у блоков высокая теплоемкость.
Формовой пенобетон. В пеногенераторе происходит взбивание пенной основы.
В специальной емкости происходит смещение песка с цементом. При осуществлении данного процесса под влиянием компрессора повышается давление. Масса, по своей консистенции напоминающая сметану, под давлением заливается в подготовленные формы.
Выпуск пенобетонных блоков
Процесс производства блоков из пенобетона предусматривает ряд основных этапов. К ним относят: создание жидкого пенобетонного состава, разлив его по формам, высушивание, распалубка, распиловка, термическая обработка, упаковывание, отправка на склад и дальнейшая реализация.
Выпуск пеноблоков схематически
В зависимости от выбранного способа производства изделий из пенобетона и используемой техники, применяются разнообразные последовательности указанных этапов. Пеноблоки состав смеси будет определяться видом материала, который вы хотите производить. Рассмотрим каждый этап по прядку.
Создание жидкого пенобетонного состава
На сегодняшний день производственный процесс пенобетонного состава может осуществляться двумя способами: баротехнологичный и пеногенераторный. Каждый из методов имеет свои достоинства и недостатки.
Первый метод отличается достаточной простотой и экономичностью. Второй метод более затратный, нежели первый. Однако полученный таким способом материал обладает повышенным качеством.
Формирование пенобетонных блоков
Сегодня действуют два метода осуществления технологического процесса, результатом которых является получение готовых пенобетонных изделий: литьевой и резательный. Состав пенообразователя для пеноблоков вы будете определять в зависимости от используемого оборудования.
Литьевой метод
Литьевой метод выпуска пеноблочных изделий сильно схож с изготовлением железобетонной продукции.
Бетонный состав заливается в форму из металла (см. Формы для пеноблоков: какие лучше использовать), высушивание его производится до того момента, пока он не приобретет необходимую прочность. Далее он извлекается из форм и попадает к конечному потребителю.
Изготовление литьевым методом
При выпуске пенобетона данным способом, применяются формы кассетного типа, имеющие вид металлического поддона с разъемными ограждениями, разделяющими поддон на индивидуальные отсеки. Аналогичная форма для заготовки ледяных кубиков имеется в каждой современной холодильной камере.
Похожая форма применяется на заводах по изготовлению блоков, только большего объема со съемными перегородками. В большинстве случаев их высота составляет 60 сантиметров.
Основными недостатками литьевого способа являются:
Отсутствие четкости размеров готовых изделий. Ширина, высота, длина пенобетонных блоков способны колебаться из-за того, что перегородки кассеты неустойчивы и непроизвольно сдвигаются. Это объясняется тем, что бортики выполнены из тончайшего металла и могут смещаться, что сказывается на неточных размерах готовой продукции.
Но имеют свое существование и формы, отличающиеся особым качеством с толстыми, не деформирующимися стенками. Но у подобных форм есть один важный недостаток – высокая цена. Поэтому мелкие компании в целях экономии закупают дешевые аналоги с тонкими перегородками, что заметно сказывается на качестве готовой продукции;Присутствие неровностей на поверхности блока. Они появляются сверху залитой в форму пенобетонной смеси.
Явным примером может послужить тот же ледяной кубик, поверхность которого сверху не отличается гладкостью. Аналогичным образом на готовом блоке образуются неровности. Многие наверняка смогут вспомнить верхнюю поверхность плит перекрытий, все части которой гладкие, кроме одной – верхней.
Неровность пенобетонных блоков, произведенных по описанной технологии, всегда можно заметить на одном из фронтонов;Обязательное применение специальных кассетных бортов, расточенных под определенный размер блоков. Для производства нескольких видов пеноблоков, отличающихся по размеру, компания должна иметь в своем арсенале несколько типов бортов с различными размерами;Распалубка кассет немного повреждает уголки и верхнюю часть готовых пенобетонных изделий. Это объясняется тем, что пенобетон приклеивается к стенкам формы, ввиду недостаточной прочности на момент проведения данной процедуры.
Небольшая порча блоков происходит из-за недостаточного смазывания формы перед заливанием состава, ввиду экономии. Производитель старается сэкономить всеми доступными способами, нередко жертвуя качеством выпускаемых изделий. Для смазки кассет предприятия часто применяют отработанные масла.
К достоинствам рассмотренной технологии выпуска пеноблочных элементов относят относительную экономию денежных средств компании. Она проявляется в экономии на дорогом оборудовании, хотя для покупателя это не имеет никакого значения.
Резательный метод
Данный метод выпуска пеноблочных изделий предполагает два этапа: отлив пенобетонной массы в большую емкость и ее распалубка с дальнейшим разрезанием на блоки установленного размера. Данный процесс осуществляется с использованием дорогостоящего специализированного оборудования.
Изготовление резательным методом
Разные виды оборудования способны выдавать различные размеры готовых блоков. При этом применяются разнообразные типы режущих конструкций. К примеру, множество видом струн, пилящих механизмов.
Резательный способ выпуска пеноблочных элементов имеет ряд достоинств, к числу которых можно отнести следующее:
- Точность размеров, соответствующая государственному стандарту № 21520-89 гладкость поверхности изготавливаемых пенобетонных блоков.

Эта тонкость крайне необходима для снижения затрат времени и финансов при последующем монтаже стен:
- В результате того, что при данном методе производства пеноблоков не используются смазочные материалы, готовая пенобетонная продукция отличается хорошим сцеплением с другими поверхностями, а также приятным видом. Он особой роли не играет, чего нельзя сказать об адгезии, являющейся важным критерием осуществления качественных работ по шпатлевке, штукатурке стен;Способность производить блоки необходимых размеров. Современные технологии позволяют нарезать пеноблоки в соответствии с индивидуальными запросами каждого потребителя;Посредством обрезания пенобетона с каждой стороны, пропадают ненавистные неровности и шероховатости на поверхности блоков.
Технологический процесс, осуществляемый рассматриваемым методом, имеет и слабые стороны.
Процесс нарезки пенобетона специализированными режущими инструментами должен происходить в соответствии с четкими правилами и требованиями.
При осуществлении резки струнным оборудованием, нужно с наибольшей точностью выбирать нужный момент, когда пенобетон уже подсох, но еще не приобрел излишнюю прочность.При осуществлении нарезки блоков в неподходящее время, режущая струна не будет следовать по указанной траектории, что негативным образом отразится на правильности блочных размеров.При выполнении нарезки блоков с помощью пил, пенобетон наоборот должен затвердеть как можно сильнее. Данное условие необходимо из-за того, что при осуществлении процесса резки блоки неоднократно переворачивают. При низкой степени прочности, бетон способен трескаться и крошиться.
Приведенные недостатки доставляют огромные неудобства производителям пеноблоков, чего не сказать о покупателях.
Высушивание изделий из пенобетона и уровень прочности
При осуществлении производственного процесса блоков литьевым методом применяются два вида высушивания блочных элементов:
Естественная сушка пеноблоков
- Первый способявляется самым простым и подразумевает естественное высыхание пенобетона, помещенного в емкость, в течение десяти часов с его дальнейшей нарезкой.

Внимание: Стоит отметить, что аналогичный вариант высушивания применяется при изготовлении конструкций из железобетона. Резательный способ изготовления блоков предполагает естественный процесс высыхания понобетонной смеси с последующей его распалубкой.
Конечный состав пеноблоков вы определите в зависимости от требуемых характеристик. На видео в этой статье и фото вы сможете узнать дополнительную и нужную информацию. Так что сделать пеноблоки самостоятельно вполне возможно и конечная цена будет не высокой.
- Дата: 09-03-2015Просмотров: 228Комментариев: Рейтинг: 35
В сравнении с бетоном классическим, пенобетон имеет более низкий вес. Его легкость обусловливается пористой структурой, причем большинство воздушных пор в ней закрыто.
Это выгодно отличает изделие от газобетона, имеющего большое количество пор сквозных. Правильно подобранный состав и тщательное соблюдение технологии производства позволяют получить дышащий строительный материал, имеющий в то же время высокие гидроизоляционные характеристики. Благодаря насыщенности пузырьками воздуха он ощутимо снижает нагрузку на фундамент и уменьшает вес строения в целом.
Пенобетон уже много лет благодаря своим качествам и достаточно низкой стоимости является самым популярным материалом для строительства зданий.
Основные компоненты и стандарты, определяющие их свойства
Свойства материала определяет ГОСТ 25485-89, в соответствии с которым производится классификация.
В нем указаны основные требования к составу пенобетона и технические характеристики различных его марок. Кроме того, каждый из ингредиентов также должен соответствовать определенному стандарту. Вот список основных компонентов, из которых создается материал:
- цемент;песок;вода;пенообразователь;разнообразные необязательные добавки.
Рецепт семеси для пенобетона.
Вяжущим ингредиентом, участвующим в создании пенобетона, является портландцемент марок М500 Д20, М400 Д0, М400 Д20 (ГОСТ 10178). В качестве заполнителя используют песок, который должен содержать не менее 75% кварца (ГОСТ 8736). В песке допускается присутствие не более 3% примесей, содержащих ил и глину.
Свойства воды определяет ГОСТ 23732. Пенообразователи могут быть как синтетическими, так и белковыми. Натуральные пенообразователи являются экологически чистыми, а изделия, в состав которых они входят — особо прочными.
Характеристики отдельных компонентов пенообразователя определяются следующими стандартами:
- сосновая канифоль — ГОСТ 191113;костный клей — ГОСТ 2067;мездровый клей — ГОСТ 3252;едкий натр (технический) — ГОСТ 2263;скрубберная паста — ТУ 38-107101.
Что касается необязательных добавок, то они у каждого производителя свои. К примеру, на некоторых заводах в пенобетон добавляют фиброволокно.
Благодаря этому почти на четверть повышается прочность материала. Грани его блоков имеют четкий контур и практически не подвержены разрушению. В состав материала может входить и мелкодисперсная зола, образующаяся после сгорания твердого топлива.
Самые крупные ее частицы не превышают 0,14 мм. Такая добавка позволяет увеличить прочность перегородок между отдельными порами материала и сэкономить до 30% цемента. К прочим добавкам относятся ускорители твердения, пластификаторы, биологически разлагаемые смазочные материалы для форм, красители.
Вернуться к оглавлению
Пенобетон имеет пористую структуру, за счет которой он имеет легкий вес.
К основным видам пенобетона относятся: теплоизоляционный, конструкционно-теплоизоляционный, конструкционный. Каждому из видов соответствует несколько марок, характеризуемых средней плотностью.
Данный показатель зависит от количественного соотношения отдельных ингредиентов, входящих в состав конечного продукта. Смеси невысокой плотности, как правило, песка не содержат. В частности, для приготовления 1 м3 материала плотностью М400 используется 300 кг цемента, 160 л воды и 0,85 кг пенообразователя.
Прочность пенобетона увеличивается по мере роста его плотности. Чем тяжелее материал, тем большую нагрузку он способен выдержать. Для создания изделий М600 необходимо взять 330 кг цемента, 210 кг песка, 180 л воды и 1,1 кг пенообразователя.
В состав материала М800 входит 400 кг цемента, 340 кг песка, 230 л воды и 1,1 кг пенообразователя. Добавление в смесь золы позволяет уменьшить коэффициент теплопроводности изделия. Чем выше марка продукции, тем ощутимее эффект от этой добавки.
Из вышеизложенного следует, что при одном и том же количестве пенообразователя увеличение количества цемента и песка приводит к возрастанию плотности материала. При этом увеличивается и его прочность.
В отличие от классического бетона, при производстве пенобетона не используются такие заполнители, как щебень и гравий. Однако на некоторых заводах в его состав вводят легкие заполнители: полистирол или частицы керамзита. Они при той же плотности позволяют увеличить как прочность, так и теплоизоляционные характеристики материала.
Вернуться к оглавлению
Разумеется, чем выше марка портландцемента, тем более прочным получится и производимый из него пенобетон.
Но не последнюю роль в смеси играет и тонкость помола вяжущего ингредиента. Если был использован цемент более крупного помола, чем указано в ГОСТ 10178, его количество потребуется увеличить на 10%. Отклонение от стандарта приведет к тому, что состав будет затвердевать значительно дольше, а это, в свою очередь, потребует введения дополнительных добавок, ускоряющих твердение.
Составляющие, которые используют для производства пенобетона влияют на его прочность.
С увеличением плотности пенобетонадля его изготовления используют песок более высокой зернистости.
К примеру, зернистость песка для марок плотностью 400-1200 кг/м3 составляет от 0 до 2 мм, а при плотности 1400-1600 кг/м3 требуется песок зернистостью от 0 до 4 мм. В то же время использование мелкозернистого песка с размером частиц менее 1 мм позволяет увеличить прочность состава при той же плотности. Однако подобная практика применяется довольно редко, так как материал, отвердевая, дает повышенную усадку.
Использование в производстве пенобетона обычной водопроводной воды может привести к снижению качества, если она не соответствует установленному стандарту по кислотности или содержанию минеральных солей. Особой чистоты требует вода, в которой разводится сухой пенообразователь. Температура жидкости должна находиться в диапазоне от 10 до 60°С, хотя многие специалисты считают, что воду теплее 25°С лучше не использовать.
Чтобы снизить содержание жидкости в материале и тем самым повысить его прочность, в состав обычно вводят разнообразные пластификаторы. Тем не менее соотношение воды и цемента не должно быть ниже 0,4. В противном случае цемент станет забирать воду из раствора пенообразователя.
Данный компонент обходится несколько дороже синтетических аналогов, но и расходуется более экономно, да и пену образует более стабильную. Иногда недобросовестные производители при выпуске синтетического состава используют пенообразователь, который был изготовлен для пожаротушения. Его применение приводит к значительному снижению характеристик получаемого материала.
Причин, по которым рекомендуется использовать для пенобетона белковый, а не синтетический пенообразователь, существует достаточно много. Основной из них является безопасность для человека ввиду полного отсутствия ядовитых испарений.
Вернуться к оглавлению
Для получения пенобетона особой прочности на многих предприятиях в смесь вводят тонкомолотый известняк. Он не приводит к возникновению трещин, как другие добавки, не утяжеляет изделие, как песок, позволяет сэкономить цемент.
Карбонизация раствора повышает устойчивость изделия к механическим нагрузкам. Масса известковой муки может составлять до 20-30% от массы цемента. Такой состав после твердения обеспечивает более высокую морозостойкость, чем смесь компонентов без добавок.
Противоморозные добавки вводятся для того, чтобы предотвратить промерзание раствора при низких температурах. Они делают его более пластичным, увеличивают скорость связывания цемента, обеспечивают ускоренное выделение тепла, образуемого при гидратации, снижают на 7-10% массу воды, необходимой для состава. Чтобы улучшить водонепроницаемость, увеличить устойчивость к повышенной температуре и кислотности, в раствор добавляют микрокремнезем.
Гидрофобизаторы и воздухововлекающая смола предназначены для снижения расслаивания пенобетона при транспортировке, улучшения таких характеристик, как водонепроницаемость, морозостойкость и удобоукладываемость.
Добавление 0,5 кг полипропиленовой фибры на 1 м3 смеси значительно снижает количество бракованной продукции при производстве, а также потерь при транспортировке. Фибра повышает устойчивость к ударам и механическим нагрузкам, предупреждает растрескивание. С введением в состав до 1 кг фибры повышается марка конечной продукции.
Источники:
- kladembeton.ru
- kladka-info.ru
- ostroymaterialah.ru
его изготовка в домашних условиях, пропорции на на 1 м3
Задавшись идеей создания собственного дома, владелец участка использует любую возможность удешевить процесс строительства. Лучшим способом этому послужит самостоятельная работа, в том числе при получении материалов для возведения объекта. Действительно, зная состав пеноблока, изготовка нужного количества единиц, труда не представляет. А ячеистый бетон, сегодня популярен, как никогда.
Компоненты и пропорции
Все участвующие материалы при изготовлении в фабричных условиях проходят строгий контроль и стандартизацию. Нельзя допустить отхождения от нормы и в самодельном производстве. Итак, составы пенобетонных смесей содержат:
- Портландцемент. ГОСТ 10178. Его основа – силикатный кальций содержанием не менее 80 %.
- Песок. ГОСТ 8736. С наличием кварца не менее 75 % и допустимым количеством примесей не более 3 %.
- Пенообразователь. В его состав входят многие элементы – канифоль, едкий натр, клеи.
- Вода техническая. ГОСТ 23732.
- Отвердитель – кальций хлористый. Используется как скорейшее достижение результата в промышленных условиях.
Пропорции для производства различного назначения пеноблоков – от возведения фундамента, до кровли, отличаются, и продукт имеет отличную друг от друга рецептуру.
Для изготовления пенобетона плотностью до 1800 кг/м3, потребуется:
- кварцевый песок 1330 кг;
- цемент 420 кг;
- вода 185 л;
- концентрированный пенообразователь 0.44 кг;
На выходе, получится пластичная масса весом в 1935 кг.
Для менее тяжелого продукта, параметром 440 кг/м³, песок не требуется вовсе. Остальной же состав выглядит так:
- цемент 350 кг;
- вода 110 170 л;
- пеноконцентрат 1.5 кг.
Окончательный вес будущего материала перед заливкой в формы равен почти половине тонны в сыром виде.
Варианты рецептов производства пеноблоков могут разниться и по составу пенообразователей. Используя дешевые синтетические, можно получить хорошее качество изделия для подсобных одноэтажных помещений. На жилом объекте экономить в натуральном сырье нельзя – от этого зависит прочность конструкции.
Важно приобрести все нужные агрегаты автоматического процесса, если производство планируется вести в домашних условиях и позаботиться о темном сухом помещении для сушки и хранения единиц стройматериала.
Сравнительные характеристики пеноблока и газобетона
Оба представляют собой ячеистые образования в результате добавления присадок. Состав пенобетона, в отличие от газобетона содержит пенообразователи. В то время как второй вариант создается с помощью алюминиевой пудры, которая выделяет водород. От разницы в составе, технические характеристики обоих материалов существенно отличаются:
- Прочность и нагрузка. Пенобетон выдерживает не более 9 кг/см², а газовый блок до 35 при одинаковой плотности – 500 кг/м³.
- Уровень энергосбережения. Стена из материала с добавлением алюминия почти в 1.5 раза тоньше, нежели с присадками пенообразователя. На этом примере станет ясно, каким образом однородность ячеек влияет на сохранение тепла – пенобетон одинаковыми «пузырьками» похвастать не может. Отчего возникает риск промерзания в разных местах объекта.
- Микроклимат дома из газоблоков лучше, так как поры сквозные. Однако менее подвержен сырости и не потребует отделки сразу же после строительства, здание из пенобетона – ячейки в нем имеют твердые перегородки, это, естественно, влаге препятствует.
- Внешний вид. Сказать, что оба материала красивы нельзя – цвет от белого, до темно-серого, шероховатая структура, швы, требующие профессионализма. Поэтому такие дома все-таки подлежат отделке – сайдинг, блок хаус. К тому же если производство велось вне зоны промышленных предприятий, то геометрию с погрешностями так или иначе, придется закрывать. Сравнить материалы в таком ключе можно, когда для отделки используется штукатурка – на газовый блок она ляжет ровнее, именно из-за его однородной пористости.
Что касается цены. Разница существенна, если принимать в расчет высококачественный газобетон и автоклавный раствор с добавлением пены почти на треть стоимости. Но из-за популярности и спроса на второй вариант, вполне возможно, приобрести достойный продукт, мало уступающий блоку, в составе которого есть алюминиевая пудра.
Расчет расхода материалов на пробный замес исходного состава ячеистого бетона
Расход составляющих компонентов ячеистобетонной смеси и воды на пробный замес определяют по следующим формулам:
вяжущее
известь
цемент
кремнеземнистый компонент
вода
где ρс – заданная плотность ячеистого бетона в сухом состоянии, кг/л;
Кс – коэффициент увеличения массы ячеистого бетона за счет связанной воды, Кс = 1,1;
V – объем замеса, л, равный объему форм, изготовляемых из одного замеса, умноженному на коэффициент избытка смеси, равный для пенобетона – 1,05, для газобетона – 1,1…1,15;
C – соотношение кремнеземистого компонента и вяжущего; п – массовая доля извести в вяжущем (исходную долю извести в смешанном вяжущем принимают по табл. 10).
Количество газообразователя или пены теоретически должно быть таким, чтобы выделенный объем газа или введенный объем пены соответствовал получению пористости, рассчитываемой по формуле
В действительности порообразователь не полностью используется на создание пористости в растворе. Поэтому обычно расход его принимают больше, чем теоретически необходимый.
Расчет газообразователя или водного раствора пенообразователя Рп на замес производят по формуле
где Пг – пористость, которая должна создаваться порообразователем в ячеистом бетоне для получения заданной плотности;
Кп – выход пор (количество газа или объем пены, получаемые из 1 кг порообразователя), л/кг;
Кп = 1390 л/кг при использовании алюминиевой пудры;
Кп = 18…20 л/кг при использовании пенообразователя;
α – коэффициент использования порообразователя, равный 0,85. Пористость Пг рассчитывают по формуле
где ρс – заданная плотность ячеистого бетона в сухом состоянии, кг/м³;
Wс – удельный объем сухой смеси, л/кг; принимается по табл. 13 в зависимости от вида кремнеземистого компонента, вида вяжущего вещества и их массового соотношения в смеси.
Алюминиевую пудру вводят в раствор в виде водно-алюминиевой суспензии. Для ее приготовления на 1 мас. ч. алюминиевой пудры расходуется 0,05 мас. ч. сухого ПАВ (мылонафта, С-3 и др.) и 30 мас. ч. воды.
Эту воду учитывают в общем количестве воды затворения. Выход пор при использовании алюминиевой пудры устанавли- вают расчетным путем, пользуясь, например, уравнением реакции газовыделения
Из уравнения следует, что при реакции 54 г алюминия с известью выделяется 6 г водорода. Поскольку одна грамм-молекула газа занимает при нормальных условиях объем 22,4 л, то, следовательно, 1 г алюминия выделяет при нормальных условиях (3·22,4/54 = 1,244) л водорода.
Пример подбора состава ячеистого бетона.
Требуется получить автоклавный газобетон средней плотности 500 кг/м3 по литьевой технологии с применением смешанного цементно-известкового вяжущего с возможно большей прочностью.
Объем одного замеса – 10 л.
Исходные материалы: портландцемент ПЦ500-Д0, молотая известь-кипелка активностью 70 %, быстрогасящаяся, кремнеземистый компонент – зола-унос (ρ = 2,06 г/см³), ПАВ – мылонафт, замедлитель скорости гидратации извести-кипелки – молотый гипсовый камень.
1. Пользуясь соответствующими формулами, подсчитывают расход материалов на один замес с учетом следующих исходных величин:
n = 0,45 (по табл. 11), C = 1,5 (по табл. 12), Кс = 1,1.
По табл. 13 определяют, что расплыв растворной смеси (исходная текучесть) должен быть 30 см при литьевой технологии изготовления ячеистого бетона.
Опытным путем устанавливают, что такая текучесть растворной смеси имеет место при В/Т = 0,44. По табл. 15 находят, что при применении данных материалов удельный объем сухой смеси W= 0,48 л/кг.
Коэффициент выхода пор Кп = 1390 л/кг,
коэффициент использования газообразователя α = 0,85.
Установив эти величины, производят расчет расхода материалов на один замес:
Вяжущее
Рвяж = 0,5·10 / 1,1(1 + 1,5) = 1,8 кг;
известь
Ри = 1,8· 0,45 = 0,81 кг;
цемент
Рц = 1,8 – 0,81 = 0,99 кг;
кремнеземистый компонент
Рк = 1,8·1,5 = 2,7 кг;
молотый гипсовый камень
Рг = 0,81·0,03 = 0,024 кг;
вода
В = (1,8 + 2,7) 0,44 = 1,98 л.
Пористость, которую необходимо создать при помощи порообразователя для получения средней плотности,
Пг = 1 — 0,5(0,48 + 0,64) /1,1 = 0,49 (49 %).
Зная пористость, определяют расход: алюминиевой пудры
Рп = 0,49 10/1,390,85 =4,15 г;
мылонафта для приготовления водно-алюминиевой суспензии
Рм = 4,15·0,05 = 0,21 г.
Хотя в настоящее время современное технологическое оборудование в состоянии обеспечить необходимую точность дозирования компонентов, однако это не всегда гарантирует стабильность получения ячеистобетонной смеси и ячеистого бетона с требуемыми характеристиками. Для каждого вида изделий разрабатываются свои алгоритмы подбора и коррекции состава ячеистобетонной смеси, которые должны обеспечить стабилизацию прочностных свойств, подвижности смеси, степень ее поризации и оптимизацию состава.
На современном уровне развития технологии ячеистых бетонов, а также аппаратных средств контроля качества материалов и управления технологическим процессом следует ограничиться только коррекцией состава бетона, которую можно производить двумя принципиально разными методами. Первый состоит в полном расчете состава ячеистого бетона по характеристикам материалов, проводимом как бы «на чистом месте». Второй метод состоит в коррекции заданного лабораторией номинального (базового) состава. В ряде случаев при таком подходе достаточно, не меняя заданного базового состава, скорректировать только фактические расходы материалов для «возврата» к номинальному составу. При этом учитываются факторы наиболее значимые для качества продукции.
Задача 1
Рассчитать автоклавный газобетон средней плотности 600 кг/м3 по вибрационной технологии с применением цементного вяжущего с возможно большей прочностью.
Объем одного замеса – 10 л.
Задача 2
Рассчитать автоклавный газобетон средней плотности 300 кг/м3 по литьевой технологии с применением смешанного вяжущего с возможно большей прочностью.
Объем одного замеса – 10 л.
Задача 3
Рассчитать неавтоклавный газобетон средней плотности 400 кг/м3 по литьевой технологии с применением цементного вяжущего с возможно большей прочностью.
Объем одного замеса – 10 л.
Задача 4
Рассчитать неавтоклавный газобетон средней плотности 700 кг/м3 по литьевой технологии с применением смешанного вяжущего с возможно большей прочностью.
Объем одного замеса – 10 л.
Контрольные вопросы
1. Какие основные пути получения пористой структуры бетона вы знаете?
2. Какие бетоны называют ячеистыми?
3. Каковы преимущества ячеистых бетонов перед другими?
4. Как различают ячеистые бетоны по условиям твердения?
5. Каков порядок подбора состава ячеистого бетона?
6. Какие исходные данные необходимы для подбора состава ячеистого бетона?
ПРАКТИЧЕСКОЕ ЗАНЯТИЕ №4
(PDF) Исследование расчета пропорций смеси цементного пенобетона
4
1234567890 ‘’ «»
AEMCME 2018 IOP Publishing
IOP Conf. Серия: Материаловедение и инженерия 439 (2018) 042053 doi: 10.1088 / 1757-899X / 439/4/042053
7 3 1 3 2 1.80
8 3 2 1 3 2.35
9 3 3 2 1 2.21
∑𝐾 6,50 6,85 6,85 6,91
∑𝐾 6,50 6,72 6,72 5,63
∑𝐾 6,36 5,79 5,92 6.82
𝑘 2,17 2,28 2,28 2,30
𝑘 2,17 2,24 2,24 1,88
𝑘 2,12 1,93 1,97 2,27
Диапазон R 0,05 0,35 0,31 0,42
Примечания: ① ∑𝐾 (𝑖 = 1,2,3) — произвольный коэффициент, сумма соответствующей прочности на сжатие
, когда горизонтальное число равно i;
② 𝑘 (𝑖 = 1,2,3) выражается как ∑𝐾3
⁄;
③ Диапазон R = 𝑘
−𝑘
.
4. Заключение
⑴ Наблюдая за приведенными выше результатами испытаний, результаты показывают, что порядок влияния на прочность на сжатие
пенобетона на основе цемента составляет D> B> C> A, в котором водоцементное соотношение является Самый важный фактор, влияющий на прочность на сжатие,
, а затем количество пенообразователя, суперпластификатор
, и степень влияния этих трех факторов аналогична, количество пены
стабилизатор
является наименее затронутым. 3, а степень водопоглощения снизилась до 23%.
Благодарности
Эта работа была поддержана Департаментом науки и технологий провинции Цинхай, Китай (грант №
2015-ZJ-722 и 2016-ZJ-766) и платформой S&T Foundation провинции Цинхай (грант №
2018-ZJ-T01).
Ссылки
[1] Li, GD, Bi, WL, Sun, XT, Li, Q., Chen, Y., Guan, Y. (2017) Получение и свойства
физически пенобетона [J] . Вестник силиката, 36 (02): 733-737.
[2] Li, Y.Q., Zhu, L.D., Li, J.L., Hu, S.K., Duan, C., Wang, X.F. (2011) Расчет пропорции смеси
пенобетона [J]. Журнал Технологического института Сюйчжоу (ЕСТЕСТВЕННЫЕ НАУКИ
ИЗДАНИЕ), 26 (02): 1-5 + 90.
[3] Министерство жилищного строительства и городского и сельского развития Китайской Народной Республики. (2014)
Технические условия на применение пенобетона [S]. China Construction Industry
Press, Пекин.
[4] Сюй, Т.Т. (2014) Исследование применения монолитного пенобетона в условиях сильного холода [D].
Цинхайский университет.
[5] Li, J.H., Wu, K.H., Cai, X. (2017) Исследование конструкции смеси из переработанного пенобетона из заполнителя для строительных отходов
[J]. Новые строительные материалы, 44 (02): 114-116.
[6] Министерство жилищного строительства и городского и сельского развития Китайской Народной Республики. (2011) Пена
Материальный дизайн и оценка характеристик пенобетона для цифрового производства
Реферат
Трехмерная (3D) печать пенобетоном, который известен своими отличными физико-механическими свойствами, еще не исследовался целенаправленно .В данной статье представлен методический подход к проектированию смесей из пенобетонов для 3D-печати и систематическое исследование возможностей применения этого типа материала в цифровом строительстве. Три различных пенобетонных состава с соотношением воды к вяжущему между 0,33–0,36 и плотностью от 1100 до 1580 кг / м 3 в свежем состоянии были произведены методом предварительного вспенивания с использованием пенообразователя на белковой основе. На основе испытаний в свежем состоянии, включая 3D-печать как таковую, был определен оптимальный состав и охарактеризована его прочность на сжатие и изгиб.Пенобетон, пригодный для печати, показал низкую теплопроводность и относительно высокую прочность на сжатие, превышающую 10 МПа; Таким образом, он соответствовал требованиям к строительным материалам, используемым для несущих стеновых элементов в многоэтажных домах. Таким образом, он подходит для приложений 3D-печати, одновременно выполняя как несущие, так и изолирующие функции.
Ключевые слова: цифровое изготовление , 3D-печать, пенобетон, дизайн смеси, испытание материалов
1. Введение
Пенобетон (FC) — это легкий цементный материал с ячеистой структурой, получаемый путем введения воздушных пустот в строительный раствор или цемент вставить.Он может иметь плотность от 200 до 1900 кг / м 3 . Пенобетон плотностью менее 400 кг / м 3 используется в первую очередь как наполнитель или изоляционный материал [1,2,3]. Из-за технической и инженерной незнания большинства практиков и предполагаемых трудностей в достижении достаточно высокой прочности в последние несколько десятилетий пенобетон в значительной степени игнорировался для использования в конструкционных приложениях. В большинстве случаев пенобетон использовался для заполнения пустот, выполнял функцию теплоизоляции и действовал как акустический глушитель.Достижения в области химических и механических технологий вспенивания, добавок в бетон и других добавок значительно улучшили стабильность и механические свойства пенобетона. В настоящее время потенциал этого материала для структурного применения хорошо известен, и многочисленные исследовательские проекты были сосредоточены на улучшении свойств пенобетона, особенно в отношении его механических характеристик несущей способности [2,4,5].
Группы, работающие с предвидением в области цифрового производства, определили будущую потребность в устойчивых строительных материалах, которые являются экономически эффективными и экологически чистыми [6].Ожидается, что после завершения предварительных исследований и описания фундаментальных принципов цифрового производства из цементирующих материалов следующим шагом станет переосмысление технологии, включая сокращение материальных затрат и воздействия на окружающую среду. Пенобетон имеет небольшой удельный вес, что снижает собственные нагрузки и, таким образом, позволяет уменьшить размеры фундамента и количество арматуры. Кроме того, низкая теплопроводность пенобетона позволяет сократить использование дополнительных изоляционных материалов, которые в основном основаны на нефтехимических полимерах с высоким содержанием CO 2 и очень ограниченной возможностью вторичной переработки.В отличие от таких материалов, пенобетон состоит из минеральных компонентов с незначительным содержанием химических примесей [7]. Кроме того, поскольку применение дополнительных изоляционных панелей может больше не потребоваться, можно ожидать значительного сокращения энергопотребления и времени на транспортировку и монтаж, а также снижение шума на строительной площадке. Подводя итог, пенобетон признан универсальным строительным материалом, экологически чистым и технически эффективным.
Концепция 3D-печати бетона на месте (CONPrint3D), разработанная в Техническом университете Дрездена, способствует реализации преимуществ аддитивных технологий в строительной отрасли [8]. В отличие от концепций, продвигающих печать интегрированной опалубки, CONPrint3D подчеркивает сокращение второстепенных шагов, таких как заполнение печатных форм [9,10]. Эта технология позволяет печатать стены большой толщины, заменяя кладку.Применение пенобетона в рамках концепции CONPrint3D является многообещающим и потенциально позволяет изготавливать несущие стены и конструктивные элементы с такими свойствами, как превосходная теплоизоляция, звукопоглощение и огнестойкость [11,12]. Авторы ожидают, что применение различных материалов на основе цемента в 3D-печати бетона упростит формулирование новых строительных стандартов и перейдет к полной автоматизации строительных процессов. Изменяя плотность и толщину стен из пенобетона, напечатанных на 3D-принтере, можно полностью или частично отказаться от дополнительных систем изоляции.Еще одним аспектом, облегчающим применение пенобетона в качестве материала, выполняющего как изоляционные, так и структурные функции, является легкость его переработки и утилизации.
В литературе есть пример, описывающий автоматизированное нанесение пенобетона на вертикальные поверхности методом экструзии [13]. Авторы поместили пенобетон на голые стены существующих зданий, чтобы получить изоляцию фасада, которую можно перерабатывать, а также свободный дизайн и форму.Использованный материал обладал видимой стабильностью формы, прочностные характеристики не изучались.
Faliano et al. В [14,15] описаны пенобетоны с плотностью в сухом состоянии от 400 до 800 кг / м 3 и прочностью на сжатие от 1,5 до 9 МПа, которые, кроме того, сохраняют стабильность размеров после экструзии. Отношение воды к цементу (в / ц) было установлено на 0,3 во всех смесях. Ни наполнители, ни заполнители не использовались. Предварительно сформированная пена была приготовлена с пенообразователем на белковой основе.Исследование дает широкий спектр результатов, связанных с влиянием условий отверждения на прочность на растяжение и сжатие. Однако описанная экспериментальная процедура не представляла типичных процедур 3D-печати с помощью роботизированных печатающих головок. Материал был скорее заполнен стальной опалубкой и вручную вытеснен с опалубки на ранней стадии гидратации. Техника осаждения, использованная Faliano et al. имитирует автоматическую экструзию и обеспечивает первое заполнение поведения материала с точки зрения стабильности формы и развития прочности в сыром виде.
Не существует стандартного способа измерения свойств сборки. Как правило, возможность сборки оценивается путем печати определенного количества слоев с определенной скоростью [16,17,18,19]. На данный момент трудно оценить возможную конструктивность пенобетона, разработанного Faliano et al. [11,12], поскольку время покоя пенобетона и его реологические характеристики в свежем состоянии не уточняются. В исследовании подчеркивается использование агентов, повышающих вязкость (VEA), и указывается на необходимость дополнительных исследований поведения экструдированного пенобетона в свежем состоянии.Авторы предполагали возможность применения экструдированных пенобетонных смесей плотностью до 200 кг / м 3 3 . Как конструкционные, так и неструктурные области применения экструдируемых элементов из пенобетона были признаны эффективными и экологически безопасными. Одним из предложенных вариантов применения было формирование многослойных изоляционных панелей на месте.
В общем, бетон, который подходит для цифрового строительства, должен быть хорошо экструдируемым и демонстрировать адекватную строительную способность.Кроме того, напечатанные слои должны иметь хорошие межслойные связи [9,16,20,21]. Наконец, материал должен обладать соответствующими механическими свойствами, например прочностью на сжатие [9,21,22,23]. Обычный пенобетон отличается хорошей технологичностью и текучестью, что является многообещающим с точки зрения технологических параметров экструзии и прокачиваемости, необходимых для 3D-печати. Обычно пенобетон перекачивается к месту укладки и, как правило, не требует уплотнения; пенобетон можно успешно перекачивать на значительные расстояния и высоты [1].Таким образом, с этой точки зрения он подходит для технологий 3D-печати на основе экструзии. Однако необходимо учитывать потенциальное влияние перекачки на характеристики пены, поскольку они могут повлиять на стабильность смеси и привести к изменению ее плотности.
Другой важной особенностью материала для печати является его способность к наращиванию, которая складывается из стабильности формы напечатанных слоев под их собственным весом и способности удерживать следующие слои с минимальной деформацией [20].Другими словами, строительная способность пенобетона может быть описана как сочетание самостойкости и достаточной жесткости с ранним схватыванием. Что касается самостойкости, пенобетон обычно воспринимается как сыпучий, самоуплотняющийся материал. Признано, что при более низких плотностях текучесть снижается из-за уменьшения собственного веса и адгезии между твердыми частицами и пузырьками воздуха [24]. Однако предыдущие исследования пенобетона показали, что снижение текучести по сравнению с обычными применениями, такими как заполнение пустот, часто рассматривается как признак низкого качества или несоответствующего дизайна смеси [4].Имея в виду 3D-печать в качестве технологии нанесения, должно быть возможно получение перекачиваемого и самостабильного пенобетона, но на сегодняшний день этот подход не был тщательно исследован, поэтому необходимы дальнейшие исследования.
В исследованиях, связанных с 3D-печатью с использованием бетона с нормальным весом, быстрое схватывание обычно достигается за счет использования ускоряющих добавок или выбора цементов с более коротким временем схватывания, то есть быстротвердеющих сульфоалюминатных или алюминатных цементов [6,25]. Такими же подходами можно добиться быстрого схватывания пенобетона.Однако, как сообщается в [26], использование ускоряющих схватывание материалов в пенобетоне не всегда дает такой же эффект, как в бетоне с нормальным весом. Более того, они могут вызвать нестабильность и повлиять на качество пенобетона. В некоторых исследованиях использовались различные типы цемента, характеризующиеся быстрым схватыванием [27,28]. Быстротвердеющий портландцемент часто используется для снижения рисков нестабильности и сегрегации, а также для обеспечения того, чтобы пенобетон на очень ранней стадии развил прочную однородную микроструктуру.Также было замечено, что добавление алюминатного цемента, сокращая время схватывания, может снизить прочность пенобетона на сжатие [29]. Кроме того, упомянутые специальные вяжущие материалы относительно дороги, что ограничивает область их применения.
Еще одним важным аспектом печатных элементов является их межслойное склеивание. Он сильно влияет на механические свойства, долговечность и работоспособность 3D-печатных конструкций; см., например, [30,31,32]. Качество межслойной связи зависит от множества факторов, связанных со свойствами свежего бетона и техникой печати, т.е.е., временной интервал между слоями, форма и размер волокна и т. д. Не было найдено литературы, которая могла бы помочь оценить поведение пенобетона с этой точки зрения. Что касается проницаемости пенобетона и его устойчивости к агрессивным средам, было доказано, что его ячеистая пористая структура не обязательно делает его менее устойчивым к проникновению влаги по сравнению с обычным плотным бетоном, поскольку воздушные пустоты не связаны между собой и действуют как буфер, предотвращающий капиллярное всасывание и другие транспортные процессы.
Как правило, существует два механизма введения больших объемов воздушных пустот в смесь: (1) использование газообразующих химикатов, таких как алюминиевый порошок, и (2) использование пенообразователей. Добавление газообразующих агентов приводит к образованию пузырьков в результате химических реакций с щелочными продуктами гидратации, например гидроксидом кальция [33]. Этот метод используется для производства газобетона, который еще называют газобетоном. Как сообщили Холт и Райвио [31], пенобетон, полученный с добавлением алюминиевой пудры, имеет ряд существенных недостатков, таких как относительно высокая стоимость, а также более низкая прочность, более высокое содержание влаги и более выраженная усадка по сравнению с традиционным бетоном.Свойства газобетона можно значительно улучшить путем отверждения паром под высоким давлением в автоклаве. Однако такое отверждение было бы контрпродуктивным, поскольку основным преимуществом технологии 3D-печати бетона является сокращение промежуточных этапов, таких как сложное литье и отверждение.
При альтернативном подходе пенобетон может быть получен либо путем добавления пенообразователя к цементному тесту с последующим интенсивным перемешиванием, которое называется методом смешанного вспенивания, либо путем смешивания отдельно полученной пены с цементным тестом, что известно как метод предварительного вспенивания [1,4].В отличие от добавления газообразующих химикатов, использование пенообразователей при производстве пенобетона имеет более высокий потенциал для применения в 3D-печати. В основном это объясняется относительной легкостью корректировки свежих и затвердевших свойств путем варьирования сырья и химических добавок [1,2,7,24,26,34].
Смешанный метод вспенивания широко применяется в строительной индустрии для производства пенобетона. Однако этот метод ограничен использованием синтетических пенообразователей и сильно зависит от используемого смесительного устройства.Напротив, метод предварительного вспенивания позволяет определять плотность материала путем точного добавления необходимого количества пены к основной смеси. Поскольку соотношение пены и основного материала может быть больше 1: 1, пена становится основным фактором влияния [35]. Стабильность воздушных пустот во время перекачивания и перемешивания с цементной матрицей важна для обеспечения требуемых характеристик пенобетона в свежем и затвердевшем состояниях. Для пенобетона с синтетическими пенообразователями легче обращаться, они менее восприимчивы к экстремальным температурам и могут храниться дольше.Синтетические пенообразователи можно использовать как в технологиях предварительного вспенивания, так и в технологиях смешанного вспенивания. Более того, они, как правило, менее дороги и требуют значительно меньше энергии для производства высококачественной пены [35]. Тем не менее, синтетические поверхностно-активные вещества не могут соответствовать характеристикам агентов на основе белков из-за их большего размера пузырьков и менее изолированных ячеек, что приводит к более низкой прочности бетона [35,36]. Пены, полученные с использованием пенообразователей на белковой основе, характеризуются меньшим размером пузырьков воздуха, более высокой стабильностью, т.е.е. меньший дренаж воды и более прочная изолированная пузырьковая структура по сравнению с пенами, полученными с помощью синтетических пенообразователей [1,2]. Также сообщалось, что пенобетон, полученный с использованием поверхностно-активных веществ на белковой основе, имеет отношение прочности к плотности от 50% до 100% выше по сравнению с пенобетоном, полученным с использованием синтетического пенообразователя [35,36].
Основываясь на соображениях, упомянутых в отношении характеристик двух существующих поверхностно-активных веществ, это исследование фокусируется на технологии предварительного вспенивания с использованием пенообразователя на белковой основе.показана структура экспериментальной части представленного исследования. Настоящее исследование посвящено получению пригодного для печати пенобетона, который является стабильным и дает адекватные реологические и механические свойства, подходящие для 3D-печати. Составляющие материалы были выбраны специально для достижения достаточной когезии и стабильности формы сразу после нанесения материала печатающей головкой, а также адекватных долгосрочных механических свойств для структурных применений. Было подготовлено четыре рецепта.Желаемая плотность свежих смесей была указана в пределах 1100–1600 кг / м 3 . Наконец, изоляционные свойства пенобетона для печати сравнивались с изоляционными свойствами обычного бетона для печати (справочный материал описан в [37]).
Обзор экспериментальной программы.
2. Материалы и методы
2.1. Методология проектирования смесей и экспериментальная программа
Схема подхода к проектированию смесей, разработанная в рамках исследовательского проекта CONPrint3D-Ultralight, представлена в.Этот подход также может быть применен к смешанному методу вспенивания. Тогда определение характеристик пены не требуется. Составление смеси пенобетона с использованием метода предварительного вспенивания делится на два этапа, а именно: определение состава матрицы на основе цемента и определение количества пены, которое необходимо добавить для достижения желаемой плотности. В частности, общий подход к дизайну смеси можно разделить на четыре этапа, как показано на. Итерационная оптимизация используется для получения удовлетворительных композиций пенобетона, пригодных для печати.
Подход к составлению смеси для пенобетона, пригодного для печати.
Во-первых, ограничения, такие как диапазон водоцементного отношения (в / ц) и содержание цемента, должны быть установлены в соответствии с предполагаемым применением. На основании информации из литературы можно определить подходящие пропорции и материалы. Производство и характеристики пены приведены ниже. Целью этого этапа является получение достаточно стабильной пены, способной выдержать процесс перемешивания. Параллельно с этим с помощью итеративного тестирования определяются водопотребность и вяжущий состав матрицы на основе цемента, включая дозировку суперпластификатора (SP).Обрабатываемость оценивалась путем измерения значений диаметра разбросанного потока в соответствии с европейским стандартом DIN EN 1015-3: 1998 и, таким образом, с использованием так называемого конуса Хэгермана и 15 ходов [38]. На первом этапе цель этой процедуры — получить матрицу на основе цемента с минимальным количеством воды, но этого достаточно для пластификации матрицы с рекомендованной дозировкой SP. В то же время матрица на основе цемента должна быть достаточно текучей, чтобы обеспечить хорошее включение пены в смесь.Чрезмерно жесткая матрица на основе цемента приводит к разрушению или разрушению пены, тогда как чрезмерно жидкая матрица расслаивается. В этом исследовании первая оценка добавления воды была сделана в соответствии с процедурой, описанной Окамурой и Одзавой [39]. В результате первого шага получается стабильная пена и соответственно жидкая матрица на основе цемента.
Третий этап направлен на проверку реологических свойств свежего пенобетона, которые должны соответствовать требованиям процесса 3D-печати по пригодности для печати, экструдируемости и сборке [39,40,41,42].Связующий состав можно регулировать для достижения требуемых свойств, включая использование дополнительных химических добавок и дальнейшую оптимизацию пены.
Последний шаг определяет испытания свойств пенобетона в затвердевшем состоянии, таких как его прочность на сжатие и изгиб, теплопроводность и / или долговечность. На этом этапе отношение воды к связующему (вес / вес) может быть уменьшено; в качестве альтернативы может быть введено усиление в виде диспергированных нановолокон или микроволокон [1,3,43].Представленный подход был использован в данном исследовании для разработки пенобетонов с различной плотностью путем изменения их состава и режимов перемешивания. Реологические свойства в свежем состоянии и механические свойства в затвердевшем состоянии — по схеме, приведенной в — были испытаны, и их результаты представлены в разделе 3.
2.2. Определение потребности в воде
Важно указать подходящее содержание воды в пенобетоне. Стандартной процедуры не существует, особенно когда должны быть выполнены требования по пригодности для печати, прокачиваемости и наращиванию.В настоящей работе водопотребность цементной матрицы определялась методом Окамуры и Одзавы [39]. Состав испытанных порошков приведен в.
Таблица 1
Композиции связующего, испытанные в соответствии с процедурой Окамуры.
: 100
Связующее | Тип цемента | Состав по объему [зола-унос: цемент] | Отношение золы-уноса к цементу [по массе] |
---|---|---|---|
A-0 | CEM II | 0.00 | |
A-1 | CEM II | 40:60 | 0,47 |
2.3. Сырье
Использовали композитный портландцемент типа II CEM II / A-M (S-LL) 52,5 R (OPTERRA Zement GmbH, Werk Karsdorf, Германия). В качестве вторичного вяжущего материала была выбрана летучая зола каменного угля Steament H-4 (STEAG Power Minerals GmbH, Динслакен, Германия). Химический состав и измеренный гранулометрический состав представлены соответственно в и.Хотя химический состав был взят из таблиц данных поставщиков материалов, распределение частиц по размерам было оценено с помощью лазерной дифракции (LS 13320, Beckman Coulter, Крефельд, Германия). Летучая зола соответствует стандарту DIN EN 450 [44] и может использоваться в качестве добавки к бетону в соответствии с DIN EN 206-1 [45]. Таким образом, он был принят как полученный в данном исследовании и не охарактеризован далее. Второстепенные составляющие показаны, тогда как значения для основных составляющих SiO 2 и Al 2 O 3 не приводятся.Внедрение летучей золы в состав бетона, с одной стороны, позволило снизить водопотребность сухих компонентов при сохранении заданного реологического поведения; с другой стороны, это улучшило устойчивость смесей. SP на основе поликарбоксилатного эфира (PCE) (MasterGlenium SKY 593, BASF Construction Solutions GmbH, Тростберг, Германия) использовали в матрице на основе цемента для регулирования удобоукладываемости при пониженном содержании воды. Содержание воды в СП составляло 77% по массе.Плотность СП составила 1050 кг / м 3 3 . Для производства пены использовали пенообразователь на белковой основе (Oxal PLB6, MC-Bauchemie GmbH & Co. KG, Боттроп, Германия).
Гранулометрический состав твердых компонентов.
Таблица 2
Химический состав цемента и летучей золы (LOI = потери при возгорании, n.d. = не определено).
2.22
Материал | Плотность [г / см 3 ] | Химический состав [% по массе] | ||||||||||||||||||||||||
---|---|---|---|---|---|---|---|---|---|---|---|---|---|---|---|---|---|---|---|---|---|---|---|---|---|---|
Остаток | SiO 2 | Al 2 O 2 O 3 | CaO | MgO | SO 3 | K 2 O | Na 2 O | LOI | CO | |||||||||||||||||
CEM II / AM (S-LL) 52.5 R | 3,12 | 0,74 | 20,63 | 5,35 | 2,82 | 60,94 | 2,14 | 3,52 | 1,05 | 0,22 | 3,47 | nd | н.о. | н.о. | н.о. | 3,6 | н.о. | 0,6 | н.о. | 2,9 | 1,8 | н.о. | <0.01 |
2.4. Процедура смешивания
На предварительной стадии было приготовлено три литра матричной пасты на основе цемента для оценки потребности в воде с использованием тарельчатого смесителя (Hobart NCM20, The Hobart Manufacturing Company Ltd, Лондон, Великобритания, вместимость 5 л). описывает процедуру смешивания.
Таблица 3
Процедура смешивания связующей пасты для определения водопотребности порошков.
Время [мин: с] | Скорость [об / мин] | Действие |
---|---|---|
0:00 | 0 | Добавьте воды к твердым частицам |
0: 00–1: | 2500 | Перемешивание на низкой скорости |
1: 00–1: 30 | 5000 | Перемешивание на высокой скорости |
1: 30–3: 00 | 0 | Отдых, больше этого времени , очистите стены |
3: 00–4: 00 | 5000 | Смешивание на высокой скорости |
Пенобетон производился с помощью конического многороторного коллоидного смесителя (KNIELE KKM30, Kniele GmbH, Bad Бухау, Германия).Для каждого эксперимента было приготовлено 30 л пенобетона по методике согласно. После смешивания связующей матрицы пошагово добавляли отдельно полученную пену: 40%; затем еще 40% и, наконец, оставшиеся 20% от общего объема пены.
Таблица 4
Порядок перемешивания пенобетона.
Время [мин: с] | Скорость [об / мин] | Действие |
---|---|---|
0:00 | 0 | Добавьте воды к твердым частицам в смесительном баке |
0:00 –2: 00 | 3000 | Перемешивание на высокой скорости |
2: 00–2: 30 | 0 | Проверьте смесь на однородность |
2: 30–4: 30 | 3000 | Смешивание на высокой скорости |
4: 30–5: 00 | 0 | Добавление 40% всего объема пены |
5: 00–7: 00 | 1500 | Смешивание матрицы и пены вместе на низкой скорости |
7: 00–8: 00 | 0 | Добавление еще 40% от всего объема пены |
8: 00–10: 00 | 1500 | Смешивание матрицы и пена вместе на низкой скорости |
10: 00–11: 00 | 0 901 98 | Добавление оставшихся 20% от общего объема пены |
11: 00–13: 00 | 1500 | Смешивание матрицы и пены вместе на медленной скорости |
2.5. Процесс 3D-печати
Эксперименты по экструзии и осаждению проводились с использованием двух устройств: (а) автономный винтовой насос (PCP1) DURAPACT DP 326S (DURAPACT Gesellschaft für Faserbetontechnologie mbH, Хаан, Германия) и (б) 3D-бетон. испытательное устройство для печати (3DPTD, устройство для 3D-печати по индивидуальному заказу, разработанное TU Dresden, Дрезден, Германия), оснащенное PCP2; видеть . Использовалась труба диаметром 25 мм, а выход из сопла устанавливался вручную для нанесения бетонных слоев.В b выходное отверстие сопла расположено автономно с помощью предварительно запрограммированного сценария Lua, который является языком программирования. При использовании PCP1 скорость откачки была установлена на уровне 10 л / мин, а выходное отверстие сопла имело круглое поперечное сечение диаметром 20 мм. Эксперименты по печати с помощью специально разработанного 3DPTD были выполнены с двумя различными прямоугольными геометриями сопла 10 мм на 50 мм и 20 мм на 30 мм, чтобы исследовать влияние этого параметра на печатные характеристики пенобетона. Скорость печати 40 мм / с была выбрана на основании предварительных исследований экструдируемости.Были изготовлены образцы с прямыми стенками длиной 700 мм с интервалом времени послойного напыления 30 с. Чтобы оценить способность к наращиванию состава смеси, было нанесено максимальное количество слоев, один поверх другого, до тех пор, пока не произошло саморазрушение. Кроме того, стены, состоящие всего из трех слоев, были напечатаны и в конечном итоге использовались при подготовке образцов для механических испытаний.
( a ) Автономный винтовой насос (PCP), DUROPACT DP 326S и ( b ) устройство для тестирования 3D-печати бетона (3DPTD).
2.6. Подготовка образца
Каждая напечатанная стена была перенесена в климатическую камеру в возрасте 24 часов и отверждена при постоянной температуре 20 ° C, относительной влажности 65% и при отсутствии ветра в течение 27 дней. Эта процедура специально не соответствует стандарту DIN EN 12390-2 [46], который предписывает совсем другие условия отверждения, а именно влажное отверждение. Поскольку в 3D-печати бетона не используется опалубка, а практические варианты отверждения очень ограничены из-за особенностей процесса печати, авторы решили использовать стандартный лабораторный климат на протяжении всей экспериментальной программы, включая подготовку бетона, 3D-печать, отверждение и т. Д. и тестирование.Такие климатические условия лучше всего представляют перспективную экспозицию крупногабаритных печатных элементов конструкций в практике строительства. В возрасте шести дней стены распилили, чтобы изготовить образцы для механических испытаний. Пиление происходило без добавления воды, чтобы избежать впитывания; затем образцы были возвращены в климатическую камеру. Кубики с длиной кромки 40 мм были подготовлены для испытаний на прочность на сжатие, тогда как размеры образцов для испытаний на изгиб варьировались в диапазоне от 30 до 33 мм в ширину и от 50 до 56 мм в высоту, что соответствует размеру трех отпечатанных слои.Неровные боковые поверхности слоев не шлифовали. Длина балочных образцов 160 мм. Погрузочная площадка была равномерно закалена быстротвердеющим гипсом.
2.7. Механические испытания
показывает установки для испытаний на изгиб и сжатие. Испытания на изгиб проводились под контролем поперечного смещения со скоростью смещения 0,5 мм / мин. Для измерения прочности на сжатие загрузочные плиты испытательной установки были 40 мм на 40 мм в соответствии с поперечным сечением кубов.Для каждого материала было испытано не менее трех образцов.
Измерение механических свойств напечатанных образцов: ( a ) испытание на трехточечный изгиб (Zwick 1445, ZwickRoell GmbH & Co. KG, Ульм, Германия), ( b ) испытание на одноосное сжатие (EU20, VEB Werkstoffprüfmaschinen, Лейпциг, Германия).
2,8. Измерения теплопроводности
Образцы размером 70 × 70 × 20 мм 3 были вырезаны из стен, напечатанных таким же образом, как и для механических испытаний.Изоляционные свойства оптимального состава смеси были измерены с помощью анализатора теплопередачи ISOMET 2104 (Applied Precision Ltd, Братислава, Словакия). В этом приборе применяется метод динамического измерения, который позволяет сократить период измерения теплопроводности до 10–16 минут.
2.9. Сканирующая электронная микроскопия и световая микроскопия
Сканирующая электронная микроскопия (SEM) использовалась для визуализации микроструктуры пенобетона. Установка для сканирующего электронного микроскопа Quanta 250 FEG (Thermo Fisher Scientific, Уолтем, Массачусетс, США) работала в так называемом «режиме низкого вакуума», при котором непроводящие образцы отображались в том виде, в котором они были получены без напыления.
Пористая структура пенобетона состоит из пор геля, капиллярных пор, а также захваченных и захваченных воздушных пустот [3]. Гелевые и капиллярные поры не оценивались, потому что эти свойства матрицы на основе цемента не считались существенными в данном исследовании. Между тем, оценивались только захваченные и захваченные воздушные пустоты диаметром более 0,01 мм. Размеры воздушных пустот в пенобетоне изучали с помощью цифрового микроскопа VHX 6000 (Keyence Deutschland GmbH, Ной-Изенбург, Германия) с инструментом анализа изображений высокого разрешения.Метод SEM не позволяет захватить большую площадь, а требует длительных последовательностей изображений и сшивания изображений. Напротив, цифровой световой микроскоп позволил гораздо проще генерировать обзорные изображения богатой порами микроструктуры с наиболее подходящей степенью разрешения. Образцы измерений теплопроводности использовались в дальнейшем для измерения пористости. Их обрабатывали в три этапа: (1) шлифовка наблюдаемой поверхности наждачной бумагой разной степени тяжести, (2) окрашивание выглаженной поверхности черным фломастером и 3) заполнение протянутых пор порошком контрастного цвета ( белый BaSO 4 ).Эта часть подготовки образца соответствует стандарту DIN EN 480-11: 2005 [47]. Для оценки рассматривалась площадь 1905,0 мм². После того, как поры были заполнены и контраст между порами и остальной поверхностью был заархивирован, было создано двоичное изображение, состоящее из двух (случайных) цветов. показывает типичную последовательность обработки изображений.
Типичное исходное изображение и последовательность обработанных изображений пенобетона: ( a ) полированный образец, ( b ) цветное изображение, ( c ) двоичное изображение, обработанное для вычислительных измерений параметров воздушной полости.
Расчет состава и состава пенобетона с легкими хвостовиками
[1]
Х.Г. Цинь, В.Л. Сан, Дж. Ли и др. Приготовление и свойства пенобетона с неорганическими легкими хвостами.Научный журнал материаловедения. 3 (2013) 103-107.
[2]
Э.К. К. Намбьяр, К. Рамамурти. Модели, связывающие состав смеси с плотностью и прочностью пенобетона с использованием методологии поверхности отклика, J. Cement & Concrete Composites. 28 (2006) 752–760.
DOI: 10.1016 / j.cemconcomp.2006.06.001
[3]
Технические условия на применение легкого пенобетона.GTJ32 / TJ 104-2010, Нанкин; (2010).
[4]
W.X. Ван. Исследование корреляции плотности в сухом состоянии и прочности пенобетона на сжатие, J.Китай Бетон. 6 (2010) 50-53.
[5]
Y.Q. Ли, Л. Чжу, Дж.Л. Ли и др. Исследование состава смеси пенобетона, J. Journal of Xuzhou Institute of Technology (Natural Sciences Edition). 26 (2011) 1-5.
[6]
П.Э. Реган, А. Арасте. Пенобетон на легком заполнителе, J. Struct Eng. 68 (1990) 167–173.
[7]
Пенобетонный блок.JC / T 1062-2007, Пекин; (2008).
[8]
R.C. Доблесть. Ячеистый бетон часть 2. Физические свойства.ACI J 1954, 50: 817–836.
[9]
М. Визажи, Э. Кирсели.Свойства пенобетона под влиянием параметров воздушной полости, J. Concrete / Beton. 2002 (101): 8–14.
[10]
Д.Олдридж, Т. Анселл. Пенобетон: производство и конструкция оборудования, свойства, области применения и потенциал. В кн .: Материалы однодневного семинара по пенобетону: свойства, применение и новейшие технологические разработки. Университет Лафборо; (2001).
[11]
ЧАС.Вейглер, С. Карл. Конструкционный бетон на легком заполнителе пониженной плотности — пенобетон на легком заполнителе J. Lightweight Concr. 2 (1980) 101–104.
DOI: 10.1016 / 0262-5075 (80)
-9
[12]
Z.Х. Пан, Л. Ченг, Д. X. Ли и др. Исследование технологии приготовления нового пенобетона с высокими эксплуатационными характеристиками, J. New Building Materials. 5 (2002) 1-5.
[13]
С.Карл, Дж. Д. Ворнер. Пенобетон-смешивание и удобоукладываемость. В: Бартос П.Я.М., редактор. Особая удобоукладываемость и перемешивание. Лондон: E&FN Spon; 1993, с.217–224.
[14]
Э.К.К. Намбияр, К. Рамамурти. Влияние типа наполнителя на свойства пенобетона, J. Cement & Concrete Composites. 28 (2006) 475–480.
DOI: 10.1016 / j.cemconcomp.2005.12.001
Производство пенобетона
Производство пенобетона
Производство пенобетона
Производство пенобетона в малых масштабах — довольно простой процесс, который
не использовать дорогостоящую или тяжелую технику и в большинстве случаев использует оборудование, которое
уже доступен для обычного производства бетона / раствора.
В зависимости от необходимого объема бетона (обычно не более 20 куб.
метров / сутки) понадобится только одна;
Оборудование
1. Обычный миксер для бетона и раствора или специальные миксеры для
пенобетон.
2. Пенообразователь
3. Опалубка (при производстве сборных элементов)
Материалы
1.Песок мелкий
2. Цемент
3. Вода
4. Стабильная пена
Простая смесь
Первым шагом, конечно же, является определение плотности во влажном состоянии и количества пенобетона.
требовать.
- Допустимый объем пенобетона = 0,5 м3
- Требуемая влажность пенобетона = 1000 кг / м3
Требуемое сырье;
цемент = 200 кг
песок = 200 кг (с учетом сухого песка)
вода = 100 кг (включая воду в пену)
, то от целевого объема пенобетона (0.5м3) рассчитать содержание воздуха
и конечный объем пены в смеси.
- Содержание пены в смеси = 0,25 м3 (250 литров)
Если выход пены из Portafoam = 1,5 литра / сек, то необходимо перекачивать генератор для
250 / 1,5 = 2,77 мин. Практический способ — прокачать 166 секунд и добавить остальное.
пены с помощью мерной емкости.
Процедуры смешивания
Теперь, когда вы определили количество материалов, необходимых для изготовления пены.
бетон, сначала добавьте их в сухом виде, начиная с песка и цемента.Смешайте сухие компоненты в течение
несколько минут, постепенно добавляя воду и тщательно перемешивая. Затем добавьте пену в
влажной суспензии и убедитесь, что пена полностью смешана с раствором.
По окончании перемешивания проверьте, что влажная плотность пенобетона
близко к тому, что требуется. Плотность пенобетона в сухом состоянии (высушенная в печи) обычно составляет
меньше, чем его влажная плотность, в зависимости от соотношения в / ц, плотности, а также от сотовой
структура получена.Поэтому не забывайте устанавливать значение плотности во влажном состоянии намного выше.
чем то, что нам на самом деле требуется (сухой).
- Специальная подготовка и демонстрация Portafoam и
производство вспененного
бетон для производства блоков / панелей (например, конструкция смеси, свойства сырья, смешивание
процедуры, контроль качества, блочные формы, вспомогательное оборудование и т. д.) могут быть
при условии. Мы также предоставим документацию вместе с этим обучением, а также обсудим
проекты и опыт производства пенобетонных блоков.
ПРЕИМУЩЕСТВА ПЕНОПРОФОННЫХ БЛОКОВ
НАЗАД
НА ГЛАВНУЮ СТРАНИЦУ
Для дальнейших запросов обращайтесь
sarahn5663@gmail.com или dr.norizal@drn.com.my
Базовый RGB
% PDF-1.4
%
1 0 объект
>
эндобдж
2 0 obj
>
/Шрифт
>
/ ProcSet [/ PDF / Text / ImageC]
/ XObject
>
/ ExtGState
>
>>
/ Тип / Страница
/ Содержание [38 0 R 39 0 R 40 0 R 41 0 R 42 0 R 43 0 R 44 0 R 45 0 R]
/ Родитель 1 0 R
/ Большой палец 46 0 R
/ MediaBox [0 0 595.276 793.701]
/ CropBox [0 0 595.276 793.701]
>>
эндобдж
5 0 obj
>
эндобдж
6 0 obj
>
эндобдж
7 0 объект
>
эндобдж
8 0 объект
>
эндобдж
9 0 объект
>
эндобдж
10 0 obj
>
эндобдж
11 0 объект
>
эндобдж
12 0 объект
>
эндобдж
13 0 объект
>
эндобдж
14 0 объект
>
эндобдж
15 0 объект
>
эндобдж
16 0 объект
>
эндобдж
17 0 объект
>
эндобдж
18 0 объект
>
эндобдж
19 0 объект
>
эндобдж
20 0 объект
>
эндобдж
21 0 объект
>
эндобдж
22 0 объект
>
эндобдж
23 0 объект
>
>>
эндобдж
24 0 объект
>
>>
эндобдж
25 0 объект
>
>>
эндобдж
26 0 объект
>
эндобдж
47 0 объект
>
поток
приложение / постскриптум
Adobe Illustrator CS32008-03-10T21: 25: 07 + 05: 302008-04-10T16: 18: 19 + 05: 302008-04-10T16: 18: 19 + 05: 30
AQBIAAAAAQAB / + 4ADkFkb2JlAGTAAAAAAf / bAIQABgQEBAUEBgUFBgkGBQYJCwgGBggLDAoKCwoK
DBAMDAwMDAwQDA4PEA8ODBMTFBQTExwbGxscHx8fHx8fHx8fHwEHBwcNDA0YEBAYGhURFRofHx8f
Hx8fHx8fHx8fHx8fHx8fHx8fHx8fHx8fHx8fHx8fHx8fHx8fHx8fHx8fHx8f / 8AAEQgBAADMAwER
AAIRAQMRAf / EAaIAAAAHAQEBAQEAAAAAAAAAAAQFAwIGAQAHCAkKCwEAAgIDAQEBAQEAAAAAAAAA
AQACAwQFBgcICQoLEAACAQMDAgQCBgcDBAIGAnMBAgMRBAAFIRIxQVEGE2EicYEUMpGhBxWxQiPB
UtHhMxZi8CRygvElQzRTkqKyY3PCNUQnk6OzNhdUZHTD0uIIJoMJChgZhJRFRqS0VtNVKBry4 / PE
1OT0ZXWFlaW1xdXl9WZ2hpamtsbW5vY3R1dnd4eXp7fh2 + f3OEhYaHiImKi4yNjo + Ck5SVlpeYmZ
qbnJ2en5KjpKWmp6ipqqusra6voRAAICAQIDBQUEBQYECAMDbQEAAhEDBCESMUEFURNhIgZxgZEy
obHwFMHR4SNCFVJicvEzJDRDghaSUyWiY7LCB3PSNeJEgxdUkwgJChgZJjZFGidkdFU38qOzwygp
0 + PzhJSktMTU5PRldYWVpbXF1eX1RlZmdoaWprbG1ub2R1dnd4eXp7fh2 + f3OEhYaHiImKi4yNjo
+ DlJWWl5iZmpucnZ6fkqOkpaanqKmqq6ytrq + v / aAAwDAQACEQMRAD8A9EeXfLvl9vL + mM2mWhJt
ICSYI6k + mv8Ak4qmP + HPL3 / VrtP + REX / ADTirv8ADnl7 / q12n / IiL / mnFXf4c8vf9Wu0 / wCREX / N
OKu / w55e / wCrXaf8iIv + acVd / hzy9 / 1a7T / kRF / zTirv8OeXv + rXaf8AIiL / AJpxV3 + HPL3 / AFa7
T / kRF / zTirv8OeXv + rXaf8iIv + acVd / hzy9 / 1a7T / kRF / wA04q7 / AA55e / 6tdp / yIi / 5pxV3 + HPL
3 / VrtP8AkRF / zTirv8OeXv8Aq12n / IiL / mnFXf4c8vf9Wu0 / 5ERf804q7 / Dnl7 / q12n / ACIi / wCa
cVd / hzy9 / wBWu0 / 5ERf804q7 / Dnl7 / q12n / IiL / mnFXf4c8vf9Wu0 / 5ERf8ANOKu / wAOeXv + rXaf
8iIv + acVd / hzy9 / 1a7T / AJERf804q7 / Dnl7 / AKtdp / yIi / 5pxV3 + HPL3 / VrtP + REX / NOKu / w55e /
6tdp / wAiIv8AmnFXf4c8vf8AVrtP + REX / NOKu / w55e / 6tdp / yIi / 5pxVj36G0f8Axd9V + o2 / 1anq
eh6ScOfpU5caUrTvirIfLn / KPaX / AMwkH / JpcVX3V3DbUa4uvSDsQikA9D8jkgLYE1zKAXzLpLGg
vnr4ekf + acl4Z7mPix71WDXdLnlWKPUKyOaKnEAk / SuJgR0UZAeqZwMzIeR5EMy16dCRkC2BUwJd
irsVdirsVdirsVdirsVdirsVdirsVdirsVdirsVdirsVdirGv + m3 / wCef / MvFU18uf8AKPaX / wAw
kH / JpcVSnznbtPa2scbFZXmKximxJNaFh8Q + jLsRouPnFgMKMU6sxU1bmvwlTy2PFt1J3qKU98yL
cWim / l / Q59QuBd200a + hLG0gdWViFYnZeo6U3yE51sW3Hj4jYZ / b / Yb / AF3 / AOJHMUuYFXAl2Kux
V2KuxV2KuxV2KuxV2KuxV2KuxV2KuxV2KuxV2KuxV2Ksa / 6bf / nn / wAy8VTXy5 / yj2l / 8wkH / Jpc
VWau / pRxzR2ouryMyG1DFQFeh + I8iv00ycWufussV1GXzJqGlRWs + mpFqMcolDRSxopkUk1AD8qd
aitcvjwg3ezjSM5RojdR0S782WGqSONEi9DUGjNxILqOkcgYhyq1qVIIPjU4ZiBHPl5MccskZfTs
fNn1t9hv9d / + JHMUucFXAl2KuxV2KuxV2KuxV2KuxV2KuxV2KuxV2KuxV2KuxV2KuxV2Ksa / 6bf /
AJ5 / 8y8VTXy5 / wAo9pf / ADCQf8mlxVWuLKK4KmaJXMZbgakEB + v3jCDTExtR / Q9j6pmNsjSncuxJ
JNa1 + de + HiKOAdzjo1iWVjbISreou52c78h748ZXgHcjYUZFIbqWZtvck5EsgvxS7FXYq7FXYq7F
XYq7FXYq7FXYq7FXYq7FXYq7FXYq7FXYq7FWNf8ATb / 88 / 8AmXirFNC / O7yZFomnxNHe8o7aFWpB
tVYwD + 1lPjxdkOyspF + n5o7 / AJXn5K / 33ff9I / 8Azdj48U / yTm / o / NdF + dvlGaVYoLbUZpX2WOO1
LsfoDHHx4oPZWUCyY / NfdfnP5XtJjDd2ep28ygM0ctoykKehNW6HxxOcDvRHsvJIWDE / FS / 5Xn5K
/ wB933 / SP / zdj48WX8k5v6Pzd / yvPyV / vu + / 6R / + bsfHiv8AJOb + j83f8rz8lf77vv8ApH / 5ux8e
K / yTm / o / N3 / K8 / JX ++ 77 / pH / AObsfHiv8k5v6Pzd / wArz8lf77vv + kf / AJux8eK / yTm / o / N3 / K8 /
JX ++ 77 / kR / zdj48V / knN / R + bv + V5 + Sv9933 / AEj / APN2PjxX + Sc39H5q1v8AnL5ZuY5Zbay1OeKA
AzvFaM4QHpyIbEZh5sT2ZkGxMRfmoD89PJRFRHff8iP + bsfHiy / knN / R + ab + V / zM8ueZNTOm6cly
twImnJmi4LxQqp3qd / jGShlEjQadRoMmKPFKqZZljhOxV2KuxV2KuxV2KuxV2KuxV2Ksa / 6bf / nn
/ wAy8VfMGmf8c20 / 4wx / 8RGa483s4fSESSAKnoMDJ6V + jZvJf5e22vWhKa / rhjge4aha3glR5aQj
s1EWpNd8vrhjfUuq4xnzmB + ih3nzSQ67Pd + QLi0uZ2vdWudQihjaQ + pcG3C81jB + 0V9Ukj3Y5Hiu
Pm5HggZwQKiI / C / 7EL / yrrzcWtkW1jZrlzCAJkPpyhC / pzf77fiOh77YPCkz / O4t9 + Xl9zrr8uvN
9st80lmCumosl2UcNQOC1Ep9shRVgOmJxyWOtxGt / q5JbrHlrXNGt7S41O1NtFeqXgLEVoOoYD7L
d6HIyiRzbcWeEyRE3SYf8q981i3WeS2iirwLQyTIsqLK3FHkQ7qpY0qcl4cmr87iur + xF / 8AKqvP
h2j6uLKMy + mZSBMhAWtBU + LUNBj4UmH8oYau / sTn8s / Ih20X + p61YLPZwxvHZ28rCj3Ebsj8hUEc
WTiK5PFjvctGv1nDUYGj19zzmRHhZ45KCSMlZO45Lsfxyh3gN8nsGiR2 + h + VvKWqyXp0zT4VnuNT
ttxLeTSoAkQjpWT9o0zJjsAXR5ScmTJEDilsB / RDyjVJln1C5uUt2tYp5ZJIoWUrxVmJAofnmOeb
ucYqIF3TNvyQ / wCU2f8A5gZv + TkWW4PqcDtX + 5 / zh + l73mY847FXYq7FXYq7FXYq7FXYq7FXYqxr
/ pt / + ef / ADLxV8waZ / xzbT / jDH / xEZrjzezh9IREgJjYDqQQMDMPW / zLuo9W / L / y / e6efWtVdFlE
fxBH9Ejiwh3SpBG + ZOU3EU6TQx4M8xLn + 1L / AMn / AC9CnmRbzUouF4ttJNY2k0ZEnAMqi4UMK0Y8
lUjwPjkcMd923tLOTjqPK9z + hM / L2sRXfmDT9F0 / S7iLTL3Up73UtTu4 + LXN3Erzmg6DjIi9TUUA
yUZb0BtbTmxEQM5SHEIgADoOSpL5yvEtfPuvLM31aFobDSVr8HqRhwzRjpyPME08MPH9RQNKCcUK
3NkrH0eee98kaRqjerZ2SCe / lumr691OrSCMep / etUcmG + 2Dh4iCkZQBllHmeVdAPuQFzLZaprOr
abp + n3t7e6xfQwa1qt1Fxjht451YW6L8RCEKQOVOtcB3JA6tsQYQjKRiBGJMQOprmzeLUY7jz3qX
A8rfy5p6IIkqay3FW + yOrARcR / blt + r3OvMKwx75y + 7 + 1jEllqsH5YXqrH6eqa5eTNdMDQRoZW5G
V + iBESjcuh3yujweZcsTidQP5sAPu6ML / Kuzs73z3psN4iSQ8ZpBDKoZWdIiVBVtiV + 19GVYhcnP
7QkY4SR5M60zSNc8w6NrWkatJdW2paRqf1qxv3EomWFmLj6u / wBr7AKLwPtlwiZAg9C67JkhinGc
aMZRoj9bzfznqmo6nrst3eJPAkn + 8dtcFg0cKfuwfTbdOfDkdtzU5RMkl2ulxxhChXnXeyP8kP8A
lNn / AOYGb / k5Fk8h2OL2r / c / 5w / S97zMecdirsVdirsVdirsVdirsVdirsVY1 / 02 / wDzz / 5l4q + Y
NM / 45tp / xhj / AOIjNceb2cPpCJwMmVeRv8XD6 / JompLpljbxmXULm5P + iL0pyDJKOZ7UWuWY + LoX
D1fhbCceInlXN1xa + Z41m84Qa3HfG3dUbVYJH5eq54 + iEljjNQtGK8ePEjEg / VaiWM / ujGr6fp5p
ZP5u8zz6muqy6nMdQjRo4rgcBwR / tKi8eC8u + 1cjxm7tuGmxiPDwjhQTanqLac2mtcOdPeQzva7c
DKernblX6cFmqbOCPFxV6u9Uvdd1q + a1a8vppmsVC2ZLUMQXoV4032 + 11xMiWMMUI3Q580dd + efN
93cwXM + qy + vasXgZFjQK5UoX4qoVm4sRVgckckj1a46TFEECI3UbLzZ5lsbu7vLTUZYru / FLycBC
0lK0JquxFTQimATI6sp6fHIAEbDkp / 4g1 + TShoYvZW02SQt9UFPjkkfkamnNuTtWhPXHiNUnwYCX
HXq71EjVdG1If3thqVqwI24SxtTwPscG4LL0zj3xKayfmF53kvIbx9YmM8CssRAjCAPTlWMLwavE
bkZLxJd7SNFhArhFFJ9R1G + 1K9lvr + Zri8nIMsz0q3EBR0AGwFBkSSdy3wgIioigGb / kh / ymz / 8A
MDN / yciy3B9Tr + 1f7n / OH6XveZjzjsVdirsVdirsVdirsVdirsVdirGv + m3 / AOef / MvFXzBpn / HN
tP8AjDH / AMRGa483s4fSEQ7cVLeAJ + 7AzD1XzvpUHl / 8q9I0y3qr3txFNeN3kYxNI9aeD8aewzIy
DhgA6bSZDk1MpHoNmJ + Wm1DW9NTyXYx0kvb4Xstyx + BI44wjFgN9qD9WVxsjhDm5 + HHLxj0jSbJ5
L8rSw6nLFJqDDQ9Qj0 ++ UegTP6kiw + pBsAgEj1oxPwjxyXAN + ezQdVkBiDw + uNjnt13ZC35O + Whr
Tab9evFaS1M9sSYmPJGo7SUjAC / GoUdT8W + 2T8EXTjfynk4OKhz / AB1YdoXkq2k0bU / MOuTyW + i6
cXRPq4X1riRDxonOqgV23B3yqMNiTyc7LqjxxxwFzl39E / j / ACv0RfMWo6JPc3XqQ2i31pMGhVFR
hx4TEqxqHB3UAEZZ4QunGOvn4YmAOdHn9ijD + XXlW80221ex1eVtKt4ZpdYlf0zIDHQIIowBw5kP
9snpg8MEWDsyOtyRkYmPqJHCu8n + T / Ll3r + hXaNerb6hB + kbC1lETOv1d + LfWHUKOLHiy8VxhAWE
anU5IwkPTcTwn49yB1PTNh2uXWfObvevoUUoR0pFHcz3UkiwiOCvJAilhu1cBANy6NuOc8fDi9PH
9gHPdJ / PPlaHy7q6WsErS208KTxCWnqqHrVX40FRTrTIZIcJbtJqDljZ52xzIOU9A / JD / lNn / wCY
Gb / k5Fl2D6nW9q / 3P + cP0ve8zHnHYq7FXYq7FXYq7FXYq7FXYq7FWNf9Nv8A88 / + ZeKvmDTP + Oba
f8YY / wDiIzXHm9nD6QiGUMpU9CKYGT03zJrNr5s8gaQlvcwLrOnyKl3ZzTxQOVWMo0ieqycgTxO3
jl8pcUR3upwYjhzSsHhPI0T9zf5bXmieW9fjtr68sjcXVpJLLfpKjxRSM68bYzA8Nlj5Gh6tTHER
E7rrozywsA0Dyr7aTXyZqPlvSdISy1bULQ6hrOotdXRE8TrEIW9ZGmcMVWvoqByPVsnAgDfqWnVQ
yTlcQeGMa5fDb5taX5otrzX / ADtdjUrWCSSOC00ie4mRE4D1VZ42Y7qKhjx / jgE7Mt1yacxhiHCe
plQ9yV6pLo95 + V8eiaJfwySW17Iz211cQwzSRGeRuZ9VkHFuYb5YDRhQbsYnHUccwdx0B7gg7bUL
Kz8qebbka2L7VblorOzmnl / 0uWBGRHKK7NLw + N6e2 + Rugd92coGWTGOGojc7bX9yH8j6lFa + TPMt
pbGyGqTSQvFb33o8LiILQqFmKo / Gh3PT6ccZ9JZ6uBOWBPFw + V7fJPfy + 1OODUNZvdY1ezOrLZxR
WQeeFIIgylvShZSIgq / Dy9PYh4yWM7mzu4 + tx3GIhE8N77G / j1 + a6LXNLT8todO8tXVpHdW10EWH
UHt1l4rL / vRxuKLWtH5U27b4eIcFBBxSOoMsgNEdL7uWzzjX5bmTVp / rGonVpUIVr8szh6DcIW34
qdhTbwyiXPvdphAERQ4fJLsi2s0 / KTWNJ0nzY13ql5DY2xtJYxPcSLEnNnjIXk5AqQp2zI0sDKdA
Xs6rtjJGGG5GhxD9L2X / AJWN5A / 6mPTf + kuH / mrNh + XyfzT8nl / zeL + dH5h4 / KxvIH / Ux6b / ANJc
P / NWP5fJ / NPyX83i / nR + Yd / ysbyB / wBTHpv / AElw / wDNWP5fJ / NPyX83i / nR + Yd / ysbyB / 1Mem / 9
JcP / ADVj + XyfzT8l / N4v50fmHf8AKxvIH / Ux6b / 0lw / 81Y / l8n80 / JfzeL + dH5h4 / KxvIH / Ux6b /
ANJcP / NWP5fJ / NPyX83i / nR + Yd / ysbyB / wBTHpv / AElw / wDNWP5fJ / NPyX83i / nR + Yd / ysbyB / 1M
em / 9JcP / ADVj + XyfzT8l / N4v50fmHf8AKxvIH / Ux6b / 0lw / 81Y / l8n80 / JfzeL + dH5hOtP1Gw1Kz
jvdPuY7uzmr6VxC4kjbiSp4spINCCMqlExNHYt0JiQsGwiMDJjX / AE2 // PP / AJl4qxfQfyW8lS6H
p0rrc8pLaFmpO3UxgnKfAi7EdqZgOnyVtR / JnyZb6fdXEa3PqQwySJWdiKqpIr92GOniSiXa2YAn
b5PmQeY9QI3Ef / An + ubz + RsH9L5vN / 6LNX / Q / wBL + 1v / ABHqHhH / AMCf64 / yNg / pfNf9Fmr / AKH +
l / a7 / EeoeEf / AAJ / rj / I2D + l81 / 0Wav + h / pf2u / xHqHhH / wJ / rj / ACNg / pfNf9Fmr / of6X9rv8R6
h5R / 8Cf64 / yNg / pfNf8ARZq / 6H + l / aiBqfmE2RvxZubBSA156EnoAk0AMv2Ou3XB / JOnurN + 9s / 0
T62uKo1 / V / ah / wDEeodxH / wJ / rh / kbB / S + bX / os1f9D5ftd / iPUPCP8A4E / 1x / kbB / S + a / 6LNX / Q
/ wBL + 13 + I9Q8I / 8AgT / XH + RsH9L5r / os1f8AQ / 0v7Xf4j1Dwj / 4E / wBcf5Gwf0vmv + izV / 0P9L + 1
3 + I9Q8I / + BP9cf5Gwf0vmv8Aos1f9D / S / tULzV7u7hEUoUKGDfCKGoBHj75kabs / HhlxRu3C1 / bm
fVY + DJw8N3sPx3oHM50ypLb3EPD1oni9VBJFzVl5o3R1qByU9iNsAILIxI5qeFi7FXYq7FXYq7FX
Yq + u / wAjP / JV6F / q3H / UVLnO67 ++ Pw + 56vsz + 4j8f90Wd5iOexr / AKbf / nn / AMy8VTXy5 / yj2l / 8
wkH / ACaXFVTWv + ONf / 8AMPL / AMQOShzDGf0l8KjoM6t4h3KHYq7FWbflH5Dg85 + a / qN6XXTLSL6x
emM8WYcgEjDb05mtfYZi6vOccLHMufoNKMs9 + QTiH80NS1r8w7Jb6VF8qvdCz / Q7fBY / VGb0gZYi
eDFQQ9W6Ee2VHSiOM19dc + ts / wA6Z5Rf0XVdK9ySX / lvzF5y8z67qekW8ctqb94o5nligidmYiKK
JpGUO5VfsrlscscUIg9zXPDPNOUo8r8vgh5Pyt8 + TWN3fLpZS2sTIt2ZJYleNoa8w0fLnXbbbftk
jqsdgXzYfkstE1y93625fyp / MCLV7XSH0eQX97E88EfOMr6cYqxdwxRCOlGPXANXjom9gp0WUSEe
Hc + 5DaX + XfnLVLa + uLHTjKmmyNBep6kYkSVDQp6fLmT4bUOSlqYRqzzYw0uSV0L4eah2ryV5q0TU
LPT9T06SG81Dj9RiBWT1WchQiFCw5cjTjTjXDDPCQJB2CMmmyQIBG5Vtc8g + a9DtkuNRs1SN51tCIZ
op3S4dSywyJEzsrsBsDjDUQkdinJpZwG46105oi6 / LDz1b / V1n0zgbqRYFHrQfBK68ljm + P90zLu
OdMiNVjPVkdFlFbfd + PmzOXyx568y + a / KvlrzBokENvoEFrHepbyLy / R / NY2aZ / UO7LERRMxhlxw
hKcT9V / NzPBy5Jxxzj9AHy + bH / N / 5eay3n7UtJ0bSEsbWNDc2sLTxLElmhEZneR5CEVn / mNfbLcO
oj4YMjf62jUaQ + KYxFdefTl3pSv5b + dDqdzpz6d6M1nGs91NNLFHbpE / 2JDcMwjKtQ0ofHwy38zC
gb5tH5TJxEVy / HPl9qR6lpt7pl / NYX0RhurduMiVDDcVBVhVWVgaqw2Iy2MhIWGmcDE0eaFyTB2K
uxV2Kvrv8jP / ACVehf6tx / 1FS5zuu / vj8Puer7M / uI / H / dFneYjnsa / 6bf8A55 / 8y8VTXy5 / yj2l
/ wDMJB / yaXFVTWv + ONf / APMPL / xA5KHMMZ / SXwqOgzq3iHYodirsVez / APOMur2NtrusaZNKsd5q
EMT2at + 36PPmoPiAwNM1nacCYg9A7rseYEiCdz + 15Tp2g3d1c3dvPysI7CKWTULmaJytuI1NBIAA
QzvRFHUsRmfLIABW98nWY8JJ32A5 / j7HtfmvQre91H8ptC0ZfUtI0e7DJ9kwx / V3eQ / 8Dv8APNXi
yUMspc / 7XdZcXF4Qjy / sP6GRedtch8u + WvO3mbTZle51q7js7CaOhrNDbx2bAf6kkUn0jKcMOOUI
noP2t2fJwQnMH6jQ + VH5brtV1R0 / NPy15ftyf0d5X06fUdRiQE1Y2zwRDiN2I57AYxj + 6lI85Gvt
TOf76MRygL + z + z5sEQ67ofkP8xtfvIjb3ut3sUIRWDvGjltm4E8WCz0I7ZlemWTHEcoj8fc4Q4o4
skusiB8z + 1l3k1tL0Tyv5c0TUAo8waNpN9q8dqwq8Ql5uDt0bjJ065j5rlOUh9JIDlYTGEIiX1RE
pfO2M / lFYa0PIN5rFrbJealrWqxTafFLIsYn + r1llbm2w2VzX2y / Vyj4gB2Ai0aSExjJq5GQrzrn
+ lN / NMul + bpNIm8sXhj07WtdjtPMeklFUSXdoqySSF6fEyJGoYoxVgB4ZXiBx3xDeMdi2ag + Jw8J
2lIAx + 37u7yXafpOry / mv5v80z2xKadY3KaTBUNK / pKYEKxD4lDtG / Co + LtjKUfBjC + Z3RGMvGnO
vpBofYPuKRQaP5b0X8mbSPzLJMPrWuV1eLTeE0k9zGJGFq8leIFU + JhXcUHXLTOUsx4f5u1 / e18E
IYPVf1b17jsya2856ff2uoWvn3RF0vy3qs9vpWnQM3qyI8cSyRQyxR1lVisgdXVfhPWnXKDhMSDj
NyG7fDOJAjJGonb3bXv1eJ / mItxH531m1numvPqNw1pDO55N6MHwRIx7siUVveubTTV4YNVbpNWC
MhF3X6NmOZe4zsVdirsVfXf5Gf8Akq9C / wBW4 / 6ipc53Xf3x + h4PV9mf3Efj / uizvMRz2Nf9Nv8A
88 / + ZeKpr5c / 5R7S / wDmEg / 5NLiqprX / ABxr / wD5h5f + IHJQ5hjP6S + FR0GdW8Q7FDsVdiqrbXNx
a3EdzbSvBcQsHimjJV1YdCpHTAQCKLKMiDYZD5g / Mjzr5gsPqGq6k01mxVpYUSOISFDVTJwC86Hf
fKcemxwNgbt + XV5JipHb8dynYfmD5z0 / SBpFnqksNiqtHEoC + pGj / bSOQjmit3AOMtPAy4iN1jq8
gjwgmkC3mfX30iz0ZrxzpdhN9ZtLU04pMXaTn0qTzcnfJ + FHiMq3LA558Ijew5Iu188ebY / MjeYI
9TdNauF9CW + bj / dsAlGFKUUb9NuuROCHDw16WUdTk4 + K / V3vQdc8zt5Z8iaHB5c80Wl7rNtczXGs
ekxmaeS6 + IkrIpEiqa1Le2YWPFx5DxRIj0djlzeHiiITBlZv4 / f8Xm0vm3zHL5j / AMSSXrtrfNXN
3QVPFQgUqBx48Bx40pTM4YY8PDXpdYc8zPjv1Iq9 / MDzjeajZ6hJqckdxp5rYrCFiihrseEaAIKj
Y7b4I6eABFc2ctVklIEncclt95781XuqWWpy3vp3mmkvZNAiRJG5NWcIgC8n / aNN8Y6eABFbFEtT
MyEr3C6H8wPOUOqalqkWqSpf6uhiv5hT40IIAUdE4g / Bx + z2xOngQBWwUarICTZuXP8Ah58lnl7z
z5r8u209ro + oNbW9weckRVZFD / 78UOG4v / lDHJghM3ILi1M8YqJq1TR / zB836Qk6WWoEi5nN3KZ0
SdvrDAKZlMgYq5AAqME9PCXMJx6vJDkfx8Uiurq4u7qa6uZGmubiRpZ5W3Z5JGLOzHxLGuXAACg0
SkZGzzUsLF2KuxV2Kvrv8jP / ACVehf6tx / 1FS5zuu / vj8Puer7M / uI / H / dFneYjnsa / 6bf8A55 / 8
y8VTXy5 / yj2l / wDMJB / yaXFUTf27XNjc2ykK00Txqx6AupFfxwxNG0SFinzyP + cXfMVP + O7af8iZ
P + as3H8px7nRfyMf5zf / AEK75i / 6vtp / yJk / 5qx / lSPcj + Rj / Od / 0K75i / 6vtp / yJk / 5qx / lSPcv
8jH + c7 / oV3zF / wBX20 / 5Eyf81Y / ypHuX + Rj / ADnf9Cu + Yv8Aq + 2n / ImT / mrH + VI9y / yMf5zv + hXf
MX / V9tP + RMn / ADVj / Kke5f5GP853 / QrvmL / q + 2n / ACJk / wCasf5Uj3L / ACMf5zv + hXfMX / V9tP8A
kTJ / zVj / ACpHuX + Rj / Od / wBCu + Yv + r7af8iZP + asf5Uj3L / Ix / nNf9CueYf + r5af8iZP + asf5Uj3
J / keX85v / oV3zF / 1fbT / AJEyf81Y / wAqR7kfyMf5zFvMf5O6noWv6fo0 + pQzzajx9OZI2VV5ME3B
Ne + Vy7YiCBwlzMHs1PJAzEwOFlP / AEK75i / 6vtp / yJk / 5qyz + VI9zh / yMf5zv + hXfMX / AFfbT / kT
J / zVj / Kke5f5GP8AOd / 0K75i / wCr7af8iZP + asf5Uj3L / Ix / nO / 6Fd8xf9X20 / 5Eyf8ANWP8qR7l
/ kY / znf9Cu + Yv + r7af8AImT / AJqx / lSPcv8AIx / nO / 6Fd8xf9X20 / wCRMn / NWP8AKke5f5GP853 /
AEK75i / 6vtp / yJk / 5qx / lSPcv8jH + c7 / AKFd8xf9X20 / 5Eyf81Y / ypHuX + Rj / Od / 0K75i / 6vtp / y
Jk / 5qx / lSPcv8jH + c9q / L3yxceV / J + naDcTpczWQkDzxgqrepM8goDU7B6ZrNRl8SZl3u30uDwsY
h4X99siylyGNf9Nv / wA8 / wDmXiqa + XP + Ue0v / mEg / wCTS4qmGKuxV2KuxV2KuxV2KuxV2KuxV2Ku
xV47 + an / AJMnyz84 / wDk8Mxsv1h4nZ / 9xP8AHR7FmS6N2KuxV2KuxV2KuxV2KuxV2KuxVjX / AE2 /
/ PP / AJl4qmvlz / lHtL / 5hIP + TS4qmGKuxV2KuxV2KuxV2KuxV2KuxV2KuxV47 + an / kyfLPzj / wCT
wzGy / WHedn / 3E / x0exZkujdirsVdirsVdirsVdirsVdirsVY1 / 02 / wDzz / 5l4qmvlz / lHtL / AOYS
D / k0uKphirsVdirsVdirsVdirsVdirsVdirsVeO / mp / 5Mnyz84 / + TwzGy / WHedn / ANxP8dHsWZLo
3Yq7FUquPMljBPNC6ycomCAhTRiV5bHpt0yYxktZygFBL51sSQDBJ8bBY + m9e5qdvnkvCLDxwqW3
m + ynRyIJlKAEhl4j4n4DdqDuDicRCRmBcnm62eRQtrMUkXnGStCwqa7Hp9nvj4RXxh4KsvmmzW2g
mSKR / rDskaEBD8BFWPIjbfAMZtJyik5yttdirsVY1 / 02 / wDzz / 5l4qmvlz / lHtL / AOYSD / k0uKph
irsVdirsVdirsVdirsVdirsVdirsVeO / mp / 5Mnyz84 / + TwzGy / WHedn / ANxP8dHsWZLo1k7yJDI8
cZlkVSyRKQCxAqFBYgCvTc4QgsNPnTU7nW / 0XBZlbyCOC4vdMikhe9gSUsGM / JhbemKD + 5md / wDJ
zI8ECN38en6 / mHGOeRlwgfr / AFfIk + StYXmshG1671aeTRLRJ5JbM6dJbTSMGNPgkrKI41HwjjVj
U1ptgkI / SB6veiMpfWZekXtw1 + 1N4 / NugPHCxu41aaKKcLyVgqTCqFnQtH8Q3Hxb9srOKXc3DPA9
VsXnTyrJJFGmqQepPy9JC3EngAW2NKbMOvjicM + 5A1GMmrCy488eWooGlF2JGEfqpEoId1 / yAwWu
wr8t + mEYZdynUQA5qi + btEE01vPN9WubdvTuIZRRkeiGm1QwpKvxLVffB4UuajPGyOo / H6Vv + NPK
5iaVNQjkRAzN6YdyFRQxNFBNKMCD3rtj4Mu5fzEKu0z0 + / tdQsoL60cyW1wgkhcqyEqeh5sFYfSM
hKJBotkJiQBHIojAyY1 / 02 // ADz / AOZeKpr5c / 5R7S / + YSD / AJNLiqYYq7FXYq7FXYq7FXYq7FXY
q7FXYq7FXjv5qf8AkyfLPzj / AOTwzGy / WHedn / 3E / wAdHsWZLo3YqkfmXTdIupdOnv7ySy + pXaXa
ejIYfXeJHVY5SN3T4 + XHxGW45EXQuw1ZYxNWa3RM2p6VfxNZwaiIppgVjkt3X1VI7pyDio9wciIk
b0kyEtgWOnQPKUUE8MmpTfU72hvo2eMRTy1LtIx9McWYtuqEL / kjLvEnfLcOP4MAKvY8 / NRk8s + R
ZLeNLq + aWMKsZZjHEGAZWXl6UcS1 + AEGm43w + LO9gg4cZFE3 + PJdcaR5Wu4547zWbmUiMWzTSi3V
xQfA6SegprR9qfCfA74BOQ5D8fNTjgQbke7p + ph3OleVopXvfrMk0qtMl1cyt / fvcxqXZiFUH92o
48KKF6ZGU5HZsjjgN7 / banovl7y9AFsNP1GfgIjBLbqsCc4goVY5CsKtWNem / Pc1JwzySO5CMeGI
2B + 79XRkum2IsLC3sllknW3RY1ll4lyqig5cFRa09splKzbkQjwgDuRORZMa / wCm3 / 55 / wDMvFU1
8uf8o9pf / MJB / wAmlxVMMVdirsVdirsVdirsVdirsVdirsVdirx381P / ACZPln5x / wDJ4ZjZfrDv
Оз / 7if46PYsyXRuxVSuLS1uOHrxLL6bc4 + YB4t4iuEEhBAPNDw6JpEEiyQ2cUci14uqgMK7GhHzw
mZPViMcR0aOh6QdjaRkE1oRUVO5NPE9zjxnvXw49zb6JpLkFrWMkUptT7IoOngNvljxleCPc1 + hN
J4sv1WOjkM23dem / tjxlfDj3Lv0PpfBk + rJwY8ilNq0pWny2 + WPEU8A7lSDTrG3IaGFUYEkMBvUi
hJPicBkSoiAiMDJ2Ksa / 6bf / AJ5 / 8y8VTXy5 / wAo9pf / ADCQf8mlxVMMVdirsVdirsVdirsVdirs
VdirsVdirx381P8AyZPln5x / 8nhmNl + sO87P / uJ / jo9izJdG7FXYq7FXYq7FXYq7FXYq7FXYqxr /
AKbf / nn / AMy8VTXy5 / yj2l / 8wkH / ACaXFUwxV2KuxV2KuxV2KuxV2KuxV2KuxV2KvHfzU / 8AJk + W
fnH / AMnhmNl + sO87P / uJ / jo9izJdG7FXYq7FXYq7FXYq7FXYq7FXYqxr / pt / + ef / ADLxVNfLn / KP
aX / zCQf8mlxVMMVdirsVdirsVdirsVdirsVdirsVdirx381P / Jk + WfnH / wAnhmNl + sO87P8A7if4
6PYsyXRuxV2KuxV2KuxV2KuxV2KuxV2Ksa / 6bf8A55 / 8y8VTXy5 / yj2l / wDMJB / yaXFUezBVLHoo
JP0Yqx3 / AB1pH8sn3L / XL / y8mj8xF3 + OtI / lk + 5f64 / l5L + Yi7 / HWkfyyfcv9cfy8l / MRd / jrSP5
ZPuX + uP5eS / mIu / x1pH8sn3L / XH8vJfzEXf460j + WT7l / rj + Xkv5iLv8daR / LJ9y / wBcfy8l / MRd
/ jrSP5ZPuX + uP5eS / mIu / wAdaR / LJ9y / 1x / LyX8xF3 + OtI / lk + 5f64 / l5L + Yi7 / HWkfyyfcv9cfy
8l / MReYfmLrdpfee9AvIQwig4FwaV2lB23zC1GMxyRDv + zcglp8h / HJ6gfPOkA04yfcv9czfy8nQ
fmItf460j + WT7l / rj + Xkv5iLv8daR / LJ9y / 1x / LyX8xF3 + OtI / lk + 5f64 / l5L + Yi7 / HWkfyyfcv9
cfy8l / MRd / jrSP5ZPuX + uP5eS / mIu / x1pH8sn3L / AFx / LyX8xF3 + OtI / lk + 5f64 / l5L + Yi7 / AB1p
H8sn3L / XH8vJfzEXf460j + WT7l / rj + Xkv5iLv8daR / LJ9y / 1x / LyX8xFJv8AE1h / iP8ASPF / Q / uq
bV5elXxyPhG6ZeKKtlnlz / lHtL / 5hIP + TS5U2pgQCKHocVSW9vPKtjcfV7w28E1FYI6gEhuVCNv8
g5YBM8mqUoA0aXG58r8A4 + rsm / xKAQKMF3p7sMfUtwaN35SHWWzHfqnTGp + a8UPJuW68qxSRxyPa
q0qiSOvGhUmgavgT0xHH5qTAdyw3 / lAUPrWnFhUNVOPWnXDU / NeKHkqzTeWIHZJmto3TZlbiCDSu
AcR70kwHct + s + VarVrYBlDqx4hSGrSh + jh2 + aLh5LRe + UjMIPVtPVNKJ8Nfi + z99Man5rxQutnG9
8pCgMtoCQCASlaE0G2NT814oeS43PlQdZLQb06pj6 / Nbh5NNeeUloGktAT0HwfPGp + a8UPJ5f + Za
WZ / MDywbZUNvMIyOAHFgZR4dcw85PGLd / wBm1 + XnX42ewfozTv8Almj / AOBGZXGe90fAO536L07 /
AJZov + BGPGe9eAdzv0Xp3 / LNF / wIx4z3rwDud + i9O / 5Zov8AgRjxnvXgHc79F6d / yzRf8CMeM968
A7nfovTv + WaL / gRjxnvXgHc79F6d / wAs0X / AjHjPevAO536L07 / lmi / 4EY8Z714B3O / Renf8s0X /
AAIx4z3rwDud + i9O / wCWaL / gRjxnvXgHc79F6d / yzRf8CMeM968A7mO / UrP / ABj6Pop6XDlw4jjX
0utMHEU8ITvy5 / yj2l / 8wkH / ACaXAlMMVQt1pWm3UolubaOWQDiHYVNPCv05ISIYmAPMKNp5f0W0
iEVtaRxxrSiip6VG9Tv1wmZPMojjiOQWN5Y8vMAG063IVeC1jXZa1p9 + PiS70eDDuC6Ty7oUn27G
FvgWPdAfgQ1VfkvbHxJd6nFHuWDyt5cEXpDTbf0wQwT01pUCgP3Y + JLvXwYdwVX0HRpJDI9nE8jG
rMygkkinfBxnvT4ce5zeX9EdQjWUTIpqFKggEinTHjPevhx7ljeWfL7EFrCEsDyDFBUMBStfGmHx
Jd6PCj3Njy3oIkMv1CD1CKF + ArStaV + ePiS718KPc7 / DuhUI + oQ0IoRwHTwx8SXenwo9zT + WtBdH
RrCErICr / CKkEUO / Xpj4ku9HhR7nln5mwQwfmF5WghQRwxiNY0XYACYbDMPMbmHf9nCtPMD8bPZc
yXSOxV2KuxV2KuxV2KuxV2KuxV2Ksa / 6bf8A55 / 8y8VTXy5 / yj2l / wDMJB / yaXFUwxV2KuxV2Kux
V2KuxV2KuxV2KuxV2KvHfzU / 8mT5Z + cf / J4ZjZfrDvOz / wC4n + Oj2LMl0bsVdirsVdirsVdirsVd
irsVdirGv + m3 / wCef / MvFU18uf8AKPaX / wAwkH / JpcVTDFXYq7FXYq7FXYq7FXYq7FXYq7FXYq8d
/ NT / AMmT5Z + cf / J4ZjZfrDvOz / 7if46PYsyXRuxV2KuxV2KuxV2KuxV2KuxV2Ksa / wCm3 / 55 / wDM
vFU18uf8o9pf / MJB / wAmlxVMMVdirsVdirsVdirsVdirsVdirsVdirx381P / ACZPln5x / wDJ4ZjZ
frDvOz / 7if46PYsyXRuxV2KuxV2KuxV2KuxV2KuxV2Ksa / 6bf / nn / wAy8VQvl / 8AMDyGmg6aj + ZN
LV1tYAym9twQRGoIIL4qj / 8AlYfkD / qZtK / 6Trb / AJrxV3 / Kw / IH / UzaV / 0nW3 / NeKu / 5WH5A / 6m
bSv + k62 / 5rxV3 / кВт / IH / AFM2lf8ASdbf814q7 / lYfkD / AKmbSv8ApOtv + a8Vd / ysPyB / 1M2lf9J1
t / zXirv + Vh + QP + pm0r / pOtv + a8Vd / wArD8gf9TNpX / Sdbf8ANeKu / wCVh + QP + pm0r / pOtv8AmvFX
f8rD8gf9TNpX / Sdbf814q7 / lYfkD / qZtK / 6Trb / mvFXf8rD8gf8AUzaV / wBJ1t / zXiryr8yfNPli
8 / MDy9dWmr2VxbQFPWniuInjSkoPxMrEDbxzHyxJkHcaHLGOCYJAJ / U9V / 5WH5A / 6mbSv + k62 / 5r
zIdO7 / lYfkD / AKmbSv8ApOtv + a8Vd / ysPyB / 1M2lf9J1t / zXirv + Vh + QP + pm0r / pOtv + a8Vd / wAr
D8gf9TNpX / Sdbf8ANeKu / wCVh + QP + pm0r / pOtv8AmvFXf8rD8gf9TNpX / Sdbf814q7 / lYfkD / qZt
K / 6Trb / mvFXf8rD8gf8AUzaV / wBJ1t / zXirv + Vh + QP8AqZtK / wCk62 / 5rxV3 / Kw / IH / UzaV / 0nW3
/ NeKpJ / i / wApf4m / Sf6bsP0dX0Prv1qH0PV9Hl6fqcuHOm / GtcVf / 9k =
uuid: 5BB4C6A5B3EEDC11BF4C8DD3CF145AD1uuid: B024F078EB06DD11AFF1D96B18AF51BAuuid: 5AB4C6A5B3EEDC11BF4C8DD3CF14514AD1DBF4C8DD3CF14514EmbD1DBACC08CF2CF02C08C08C08C08C08CF0CF08C08C08C02CF02CF08C08C0C8tifuuid: 5B710D25DE06DD119766CEDEDC127FA5uuid: 8e0bba25-fdea-40b9-afdc-3e0e790bae74
Базовый RGB 209,999994297,000002 Миллиметры1 Ложь Ложь
конечный поток
эндобдж
27 0 объект
>
эндобдж
48 0 объект
>
поток
hn0 {ibc $ t = le # Wqv # Z} B
lPi * U4e [2 ~ l.߀6, ga`S + [9, it
Экспериментальные исследования соединителей сдвига в пенобетоне с заделкой канала C
Аллахьяри, Х., Никбин, И.М., Рахими, С., и Хейдарпур, А. (2018 г.) ). Новый подход к определению прочности соединителя ребер Perfobond на сдвиг в железобетонных композитных конструкциях с использованием нейронной сети. Инженерные сооружения, 157, 235–249.
Артикул
Google Scholar
Чен, В., Е, Дж., Бай, Ю., и Чжао, X. Л. (2012). Натурные пожарные эксперименты на несущих стенах из холодногнутой стали, облицованных различными панелями. Журнал исследований конструкционной стали, 79 (2012), 242–254.
Артикул
Google Scholar
Дави, Дж. Л., Лю, Ю., и Ли, Дж. Ю. (2010). Прочность и поведение холодногнутых стальных офсетных ферм. Журнал исследований конструкционной стали, 66 (2010), 556–565.
Артикул
Google Scholar
Флорес-Джонсон, Э. А., и Ли, К. М. (2012). Конструктивное поведение композитных сэндвич-панелей с гладкими и армированными волокнами вспененными и гофрированными поверхностями. Композитные конструкции, 94 (5), 1555–1563.
Артикул
Google Scholar
Gosowski, B., Kubica, E., & Rykaluk, K. (2014). Анализ поперечно закрепленных холодногнутых прогонов С-образной формы по теории Власова. Архив гражданского строительства и машиностроения, 15 (2014), 456–468.
Google Scholar
Хилал, А., Том, Н. Х., и Доусон, А. Р. (2015). Использование добавок для улучшения свойств готового пенобетона. Международный журнал инженерии и технологий, 7 (4), 286–293.
Артикул
Google Scholar
Хо, Дж., Ван Х., Чжу З., Лю Ю. и Чжун К. (2018). Экспериментальное исследование поведения при ударе шпилек между бетонной плитой и стальной балкой. Журнал. Строительное проектирование, 144 (2), 04017203.
Статья
Google Scholar
Ибрагим, В., Джамалуддин, Н., Ирван, Дж. М., Рамадхансьях, П. Дж., И Сурая Хани, А. (2014). Прочность на сжатие и изгиб пенобетона, содержащего полиолефиновые волокна. Advanced Materials Research, 911, 489–493.
Артикул
Google Scholar
Икпонмвоса, Э., Фаладе, Ф., Фапохунда, К., Акинний, Т., и Олори, К. (2014). Влияние концентрации пены на конструктивные характеристики стальных балок из газобетона. Pacific Journal of Science and Technology, 15 (1), 32–46.
Google Scholar
Лайм, Л., Родригес, Дж. П. К., и да Силва, Л. С. (2013). Экспериментальный и численный анализ структурных свойств холодногнутых стальных балок. Тонкостенные конструкции, 72 (2013), 1–13.
Артикул
Google Scholar
Ляо, Ф., Ву, Х., Ван, Р., и Чжоу, Т. (2017). Испытание на сжатие и анализ многолучевых сборных колонн из холодногнутой стали. Журнал исследований конструкционной стали, 128 (2017), 405–415.
Артикул
Google Scholar
Лим, С., Тан, К., Чжао, X., & Лин, Т. (2014). Прочность и вязкость легкого пенобетона с разной фракцией песка. Журнал гражданского строительства KSCE . https://doi.org/10.1007/s12205-014-0097-y.
Google Scholar
Лю Д., Ван Ф., Фу Ф. и Ван Х. (2017). Экспериментальные исследования механизма разрушения пенобетона с заделкой С-образным каналом. Компьютеры и бетон, 20 (3), 263–273.
Артикул
Google Scholar
Ма, В., Бекке, Дж., Хаджирасулиха, И., и Йе, Дж. (2015). Оптимизация поперечного сечения холодногнутых стальных швеллеров по Еврокоду 3. Engineering Structures, 101 (2015), 641–651.
Артикул
Google Scholar
Моэн, К. Д., & Шафер, Б.W. (2008). Эксперименты на стальных холодногнутых колоннах с отверстиями. Тонкостенные конструкции, 46 (10), 1164–1182.
Артикул
Google Scholar
Моэн, К. Д., & Шафер, Б. В. (2009). Упругая деформация холодногнутых стальных колонн и балок с отверстиями. Engineering Structures, 31 (12), 2812–2824.
Артикул
Google Scholar
Moen, C.Д., Шудлих А. и фон дер Хейден А. (2013). Эксперименты с холодногнутыми стальными балками C-образного сечения с отверстиями в стенке без жесткости. Journal of Structural Engineering, 139 (5), 695–704.
Артикул
Google Scholar
Мохамад, Н., Халил, А. И., Абдул Самад, А. А., и Гох, В. И. (2014). Конструктивное поведение сборных легких пенобетонных сэндвич-панелей с соединителями фермы двойного сдвига при изгибной нагрузке. ISRN Гражданское строительство . https://doi.org/10.1155/2014/317941.
Google Scholar
Майдин, М.А.О., и Ван, Ю.С. (2011). Высокотемпературные термические свойства легкого пенобетона. J. Строительство и строительные материалы, 25, 705–716.
Артикул
Google Scholar
Парнелл, Р., Дэвис, Б. В., и Сюй, Л.(2010). Вибрационные характеристики легких стальных холодногнутых полов. Journal of Structural Engineering, 136 (2010), 645–653.
Артикул
Google Scholar
Рамезани, М., Вилчес, Дж., И Нейтцерт, Т. (2013). Характеристики выдергивания стальной оцинкованной полосы в пенобетоне. International Journal of Advanced Structural Engineering, 5 (1), 24.
Статья
Google Scholar
Смит, Ф.Х. и Моэн К. Д. (2014). Решения по продольному изгибу конечных полос для тонкостенных металлических колонн с перфорацией. Тонкостенные конструкции, 79, 187–201.
Артикул
Google Scholar
Тан, К. С., Ли, Ю. Л., Мохаммад, С., Лим, С. К., и Ли, Ю. Х. (2015). Взаимодействие холодногнутой стали и легкого пенобетона с различным содержанием цемента. Malaysian Journal of Civil Engineering, 27 (1), 115–127.
Google Scholar
Такрел, М. Х. (2014). Экспериментальное исследование пенобетона. Международный журнал исследований и разработок в области гражданского строительства, строительства, окружающей среды и инфраструктуры, 4 (1), 145–158.
Google Scholar
Тран, Т., и Ли, Л. (2006). Глобальная оптимизация стальных гнутых профилей швеллеров. Тонкостенные конструкции, 44 (2006), 399–406.
Артикул
Google Scholar
Ву, Д. П., и Ли, К. Ю. (2012). Исследование устойчивости при осевом давлении открытой холодногнутой тонкостенной стали с дощатыми пластинами. Журнал Уханьского технологического университета, 11, 104–108.
Google Scholar
Юэ Л. и Бинг К. (2015). Новый тип сверхлегкого пенобетона на фосфатно-магниевом цементе. Журнал материалов в гражданском строительстве . https://doi.org/10.1061/(ASCE)MT;1943-5533.0001044,04014112.
Google Scholar
Проектирование пенобетонной смеси
ПРОЕКТИРОВАНИЕ БЕТОННОЙ СМЕСИ
|
| ПЕНОБЕТОН KIS www.kisinnovate.com адрес электронной почты: teamkisinnovate@gmail. |