Соль в бетон для морозостойкости: что будет если добавить и зачем
- что будет если добавить и зачем
- Для чего добавляют соль в бетон и цементный раствор, сколько её нужно? | Строительный журнал САМаСТРОЙКА
- Зимние добавки к бетонам
- Что будет, если в цемент добавить соль
- Обзор рецептов приготовления добавок в бетон и цементный раствор своими руками
- Цемент/бетон в зимнее время — Стройка и ремонт
- Соли в растворах, воздействие на бетоны
- Влияние гидрофобных обработок на повышение солевой морозостойкости бетона
- (PDF) Влияние типа цемента на устойчивость бетона к замораживанию — оттаиванию и противообледенительной соли
- МОРОЗОСТОЙКИЙ БЕТОН
- Морозостойкость бетона, содержащего летучую золу CFBC
- Устойчивость самоуплотняющегося бетона, содержащего летучую золу, к морозу и солевой стойкости
- Как защитить бетон от солевых повреждений
- Страница не найдена | MIT
что будет если добавить и зачем
Довольно часто при изготовлении различных составов или смесей профессиональные мастера используют компоненты в виде соли, которые должны придать ему дополнительных качеств. При этом постоянно возникают различные споры о том, нужно ли это делать и в каких пропорциях. Поэтому вопрос, зачем добавляют соль в бетон, и какое количество необходимо для достижения нужного результата, очень волнует начинающих специалистов.
Любительское фото последствий в виде пятин от ржавления арматуры и выпадение осадка на поверхности при использовании соли в растворе бетона
Достоинства и недостатки
Для того чтобы разрешить данный спор необходимо рассмотреть все достоинства и недостатки подобного способа и на их основании сделать вывод. При этом на вопрос о том, сколько добавлять соли в бетон стоит отвечать только при положительном результате исследования.
Последствия использования соли в качестве добавки при зимнем монтаже сказываются не только на внешнем виде, но и прочности
Необходимость применения соли
Принято считать, что если добавить соль в бетон, то он получает дополнительные характеристики, которые позволяют не замазать воде на морозе, а значит, можно производить работы зимой при минусовой температуре.
Также некоторые мастера утверждают, что благодаря такой доставке увеличивается скорость застывания, поскольку данное вещество вытягивает влагу.
Стоит помнить, что бетон также подвержен коррозии, а соленая среда только ускоряет этот процесс
- Стоит отметить, что на вопрос о том, сколько добавить соли в бетон точный ответ не может дать ни один специалист. Дело в том, что некоторые строители считают, что это зависит от общего объема раствора, в то же время другие мастера утверждают, что процентное соотношение соизмеряется с температурой на улице.
- Также необходимо сказать и о том, что вопрос, сколько соли добавлять в бетон зимой задают люди, которые затянули ремонт или неправильно распределили время на изготовление того или иного процесса. Профессионалы же если планируют, строительство в холодную погоду используют не добавки, а дополнительные системы обогрева и соответственные температуре смеси.
Внешний вид коррозии бетона
- Очень важно сказать о том, что добавка соли в бетон для придания ему особых качеств является своеобразным мифом.
Дело в том, что пользы от этого нет практически никакой, поскольку по заявлению тех, кто это использует, температура не должна быть меньше 7 градусов.
Совет!
Намного проще приобрести готовый бетон на предприятии, которое делает горячие смеси с высокой температурой застывания.
Однако работать с таким составом нужно очень быстро, чтобы он не схватился.
Существует масса других, более эффективных способов подогрева раствора
Недостатки
Прежде всего, следует отметить, что материал с добавками соли можно пилить обычными кругами. Больше не потребуется резка железобетона алмазными кругами, поскольку застывшее изделие будет менее прочным, что также отразится на сроке его эксплуатации.
Стоит отметить, что соленая среда отрицательно сказывается на арматуре. Поэтому если мы добавляем соль в бетон с включениями металла, то необходимо помнить, что она практически сразу начнет вызывать коррозию и ослабит всю конструкцию с течением времени.
Для некоторых видов бетонных конструкций такое решение может оказаться фатальным
Также такое техническое решение со временем начнет давать и визуальные эффекты. Соль будет выступать на поверхность в виде белого осадка, который очень некрасиво смотрится.
Учитывая всю серьезность данных недостатков, профессионалы не рекомендуют использовать такой метод. При этом вопрос о том, сколько соли надо добавлять в бетон естественно остается без ответа.
Совет!
Использование теплой опалубки или искусственного подогрева бетона намного практичнее, хотя и приводит к дополнительным расходам.
Некоторые добавки от замерзания также значительно улучшают прочность готовой продукции
Другие добавки
Стоит отметить, что навязчивое желание производить работы своими руками и при минусовой температуре порой совершенно не оправдывает расходы. Однако если бюджет невелик, то можно воспользоваться специальными присадками для бетона, которые продаются на рынках строительных материалов.
Эти материалы позволяют работать даже при температуре минус 17, хотя это зависит от марки выбранного средства. При этом прочность раствора нисколько не уменьшается и алмазное бурение отверстий в бетоне снова станет актуальным.
Противоморозные присадки не содержат соли, но являются экологически чистыми
Некоторые мастера считают, что подобные смеси не являются экологически чистыми. Однако их инструкция обычно утверждает обратное, поскольку в состав таких присадок входят только натуральные компоненты.
Среди основных достоинств таких составов является их экономичность. Дело в том, что цена на них и расход очень малы, особенно по сравнению с другими вариантами подогрева.
Данный минерал отрицательно влияет на строения из бетона и все его положительные качества не оправдывают побочных эффектов
Вывод
Ознакомившись с видео в этой статье можно получить дополнительные данные о подобном методе бетонирования. Также принимая за основу статью, которая предложена выше, следует сделать вывод о том, что соль является не самой удачной добавкой для работы в холодное время года.
Для чего добавляют соль в бетон и цементный раствор, сколько её нужно? | Строительный журнал САМаСТРОЙКА
Соль в бетон и раствор: зачем и сколько?
Соль в бетон и раствор: зачем и сколько?
Содержание статьи:
- 1. Зачем добавляют соль в бетон
- 1.1. Сколько нужно добавлять соли в бетон и цементный раствор
Изменить свойства цементного раствора и бетона в лучшую сторону можно разными способами. Очень часто строители добавляют соль в бетон и раствор, которая является эффективной противоморозной добавкой. Соль позволяет работать со строительной смесью при отрицательных температурах воздуха и способна изменить в лучшую сторону её характеристики.
Конечно же, можно использовать специальные добавки на полимерной основе, которые не дадут замерзнуть воде на морозе, которая находится в растворе. Но все это существенно удорожает смесь. Ранее в строительном журнале samastroyka.ru уже рассказывалось про «народные» добавки в бетон и раствор. Упоминалось там и использование соли, но только совсем уж поверхностно. В данной статье будет рассказано, для чего добавляются соль в цементный раствор или бетон, а также её конкретные пропорции использования.
Зачем добавляют соль в бетон
Добавление соли в бетон и цементный раствор даёт возможность вести строительные работы при отрицательных температурах окружающей среды. На застывание цементного раствора нужно примерно несколько дней, а вот при морозе, данный срок существенно сокращается. Из-за этого происходит разрушение строительной смеси изнутри, она становится рыхлой и непрочной.
Соль же добавленная в цементный раствор, не даёт воде замерзнуть некоторое время на морозе, что положительным образом сказывается на качестве раствора. Однако мнения строителей по поводу добавления соли в бетон и растворы на основе цемента, серьезно разделились.
Одни из них считают, что при добавлении соли в бетон, коррозия металлических элементов армирования резко возрастает. Другие же строители, наоборот, добавляют соль в раствор и считают такую добавку самой дешевой из всех противоморозных добавок. Соль позволяет применять растворы на основе цемента при отрицательной температуре воздуха.
Как бы там ни было, каждую добавку в бетон и цементный раствор нужно использовать на свой страх и риск. При этом обязательно следует знать правильные её пропорции по отношению к объему строительной смеси. В противном случае можно сделать только хуже.
Сколько нужно добавлять соли в бетон и цементный раствор
Количество соли в цементный раствор или бетон, всецело зависит от температуры окружающей среды. Добавляют соль в бетон и цементные растворы, только в том случае, если с ними приходится работать при отрицательных температурах, когда требуется не допустить быстрого замерзания воды и их разрушения вследствие этого.
Так, например, при температуре воздуха от 0 до — 5 градусов, процентное содержание соли от общей массы строительной смеси, должно составлять примерно 2%. При температуре от -5 до -15 градусов, соль добавляют в цементный раствор не менее 4% от общей его массы.
Кроме того, учитывая высокие коррозионные процессы при добавлении соли в бетон, можно выделить один главный нюанс: использовать соль в качестве противоморозной добавки можно только для тех конструкций из бетона, в которых отсутствуют металлические элементы армирования. Например, при заливке бетоном отмостки, там, где не применяется армировка. При таком подходе, соль, в качестве противоморозной добавки, окажется самым дешевым вариантом.
Однако, по мнению все тех же самых экспертов, от использования бетона и цементных растворов при отрицательных температурах, лучше и вовсе отказаться. Желательно спланировать бетонные работы, таким образом, чтобы они не приходились на зиму. В любом случае, и прочность, и долговечность эксплуатации строительных конструкций с использованием бетона и цементных смесей, построенных в это время, будет намного ниже.
Читайте также:
Зимние добавки к бетонам
Установлено, что в морозный зимний период прочность раствора или бетона (далее по тексту бетона) при отрицательных температурах зависит в значительной степени от минералогического состава цемента и тонкости его помола, водоцементного отношения и от состояния воды в порах и капиллярах.
При понижении температуры ниже ноля градусов Цельсия процесс гидратации цемента замедляется, а при охлаждении бетона до температуры —100 градусов Цельсия прочность фактически исчезает, химически несвязанная вода обращается в лед и увеличивается в объеме приблизительно на 9-10%, из-за чего в бетоне возникают напряжения, разрушающие его структуру.
Эффективным приёмом, который позволяет интенсифицировать процесс твердения бетона при низких температурах, служит введение в его состав противоморозных добавок.
При проведении работ в зимнее время по бетонированию монолитных конструкций и стыков сборных железобетонных элементов обычно применяются такие противоморозные добавки, как: азотистокислый натрий (нитрит натрия), углекислый калий (поташ), хлористый натрий, хлористый натрий в сочетании с хлористым кальцием и др.
На интенсивность твердения бетона на морозе влияет, в первую очередь, уровень температуры, вид и количество добавки, вид цемента. Наиболее эффективное замедление твердения с понижением температуры свойственно добавкам хлористых солей. Вместе с тем, явное твердение бетона с добавками хлористых солей и нитрата натрия имеет место в случае, если температура его не опускается ниже -150 градусов Цельсия, а с поташем — ниже -30 градусов Цельсия. При охлаждении бетона ниже приведенных температур твердение бетонной смеси фактически прекращается. Причем, даже повышение дозировок солей не может привести к возобновлению процессов твердения и является опасным с точки зрения живучести бетона и образования высолов.
Минералогический состав цемента также оказывает влияние на твердение бетона с добавками при отрицательных температурах. Меньшее количество нитрита натрия является нормальным для бетонов на быстротвердеющих цементах (БТЦ), смешанных (шлаковых и пуццолановых) и на портландцементах с содержанием трехкальциевого алюмината в клинкере до 7%, меньшее количество поташа является нормальным для бетонов на БТЦ и на портландцементах, клинкер которых в своем составе содержит трехкальциевый алюминат — 7% и более.
При температурах ниже расчетных замедление твердения бетона и структурные нарушения бетона (приводят к уменьшению прочности, плотности, морозостойкости) определяются абсолютным значением температуры. Наиболее значительные нарушения структуры бетона происходят при понижении температуры ниже эвтектической точки замерзания раствора соли.
Наряду с вышеупомянутыми и хорошо известными в качестве противоморозных добавок, используемых в бетоне и железобетоне, предлагаются добавки хлорида кальция, ингибированного нитритом нитратом хлорида кальция (ННХК), а также смеси в сочетании этого продукта с мочевиной (ННХКМ).
По сравнению с примесью хлористых солей натрия (ХН) и кальция (ХК), ННХК и производные на их основе добавки обладают следующим преимуществом: содержащиеся нитрит-ионы нейтрализуют отрицательное влияние хлорид-ионов на арматуру, металлическую опалубку, трубопроводы и оборудование бетоносмесительных узлов и заводов. Преимущество добавки ННХК и производных на ее основе состоит в том, что использование солей кальция не позволяет допустить возможность щелочной коррозии бетона за счет вводимых добавок. Кроме того, добавки ННХК и ННХКМ весьма благоприятно влияют на морозостойкость бетона.
Из спектра предлагаемых противоморозных добавок к бетону преимущественно применяются такие добавки: для температуры до -15 градусов Цельсия нитрит натрия (добавка полифункционального действия — противоморозная, ускоритель твердения, ингибитор коррозии стали), для температуры -30 градусов Цельсия — поташ, нитрит нитрат хлорид кальция.
В 1988-1990 гг. НИИМосстрой совместно с институтом ГосНИИМетанолпроект (г. Северодонецк) разработал новую добавку НИТРОДАП — полупродукт производства нитрит нитратных солей, представляющую собой водный раствор натриевых солей нитрата, нитрита хлорида, карбоната с незначительным количеством примесей в виде полуторных окислов металлов. Применение этой добавки в бетоны показало, что она эффективна при зимнем бетонировании монолитных конструкций до температуры -18 градусов Цельсия. Эта добавка, кроме того, является ускорителем твердения при тепловой обработке изделий применительно к кассетной, конвейерной и вибропрокатной технологиям, повышает активность цементов III группы эффективности.
В результате анализа и обобщения отечественного опыта применения противоморозных добавок в бетоны можно остановить свой выбор на следующих химических добавках:
нитрит натрия (НН) — ГОСТ 19906, ТУ 3810274;
поташ (П) — ГОСТ 1069;
нитрит-нитрат-хлорид кальция (ННХК) — ТУ -6-18-19;
нитродап — ТУ 113-05-8-88.
Заслуживает внимания широко применяемая противоморозная добавка — формиат натрия.
Формиат натрия используется для приготовления и укладки бетонов (монолитные бетонные и железобетонные конструкции, замоноличивания стыков, сборные бетонные и железобетонные конструкции) в зимних условиях при отрицательных температурах до — 15 градусов Цельсия.
Формиат натрия — это кристаллический порошок (хорошо растворимый в воде), снижающий точку замерзания воды затворения для бетонов и цементных растворов. Его отличие — низкий (в 3-4 раза) процент ввода его в качестве добавки в бетоны и растворы, по сравнению с другими добавками (нитрит натрия, поташ). При этом обеспечивается быстрый набор прочности бетона, а также длительная жизнеспособность бетонной смеси.
Добавка не образует токсичных соединений с иными веществами в воздушной и водной средах, взрывобезопасна и негорюча.
Формиат натрия (сухой) рекомендуется вводить в бетонную смесь в количестве 2%-4% от общей массы цемента при температуре наружного воздуха: до -5°C — 2%; до -10°C — 3%; до -15°C — 4%.
Обычно используется раствор 25% концентрации, с плотностью раствора — 1,12 кг/ л. При этом в 1 кг раствора должно содержаться 0,25 кг сухого формиата натрия, а в 1 л раствора — 0,28 кг сухого формиата натрия.
Температура приготавливаемой бетонной смеси, независимо от используемых добавок, не может быть ниже +5°C. Такая температура достигается подогревом одного или нескольких компонентов, например, воды. Температура воды, которая применяется для приготовления бетона, должна быть в пределах от +25 до 40°C.
НИИЖБ Госстроя России рекомендуется к использованию «Формиат натрия сырец» (удовлетворяет требованиям ТУ 6-58-350-89).
Что будет, если в цемент добавить соль
Бетон является универсальным и старым строительным материалом, обладающим неоспоримыми преимуществами. Однако в строительстве издавна используются различные добавки, которые улучшают его качества. К стандартной смеси цемента, щебня, песка и воды добавляют различные материалы для придания бетону необходимых особенностей. Одной из таких добавок принято считать обыкновенную поваренную соль. Попробуем разобраться, зачем некоторые мастера добавляют соль к цементному раствору и есть ли в этом смысл.
Зачем использовать соль в бетонном растворе
Застывание бетона требует определённого времени для того, чтобы конструкция получилась прочной и обладала всеми необходимыми эксплуатационными качествами. Если работы проводятся в холодное время года и среднесуточная температура воздуха опускается ниже нуля, это способствует быстрому замерзанию воды в составе раствора. В результате проводить строительные работы становится затруднительно либо невозможно. С целью снижения температуры замерзания воды, в бетон добавляют хлорид натрия (Na Cl) — обычную поваренную соль. В результате возникающей реакции, солёная вода не превращается в лёд быстро и строительство можно продолжать. Таким образом, поваренная соль считается естественным и дешёвым аналогом специализированным противоморозным добавкам для бетона.
Преимущества добавления соли в цементный раствор
Основными достоинствами «солёного» цемента считаются такие:
- Низкая стоимость по сравнению с профессиональными противоморозными добавками;
- Отсутствие влияния на скорость застывания бетонной смеси.
Недостатки «солёного» цемента
Добавленный в цемент хлорид натрия имеет и ряд минусов, которые являются существенными:
- Солёная вода способствует коррозии и ржавению арматуры;
- Соль может «выходить» на поверхность бетона после его застывания, образуя неприглядные белые разводы;
- Бетон с добавлением соли менее прочен;
- Применять такой метод имеет смысл лишь при небольших заморозках до -5 градусов;
- Na Cl притягивает воду, поэтому конструкции из такого бетона необходимо дополнительно обрабатывать от влаги.
Сколько соли добавлять в бетон
Нет никаких норм соотношения хлорида натрия и основных ингредиентов раствора. Некоторые строители рекомендуют добавлять от 2 до 4% Na Cl, в зависимости от температурного режима на улице. Однако данные параметры никак не регламентируются строительными нормами. Профессиональные строительные бригады используют либо специальные морозостойкие полимеры и присадки либо обогрев строительного объекта.
Итак, использование поваренной соли в бетоне – проверенный годами метод, пользующийся популярностью в первую очередь, благодаря доступности и простоте добавки. Однако существенные недостатки метода говорят о том, что использовать его имеет смысл лишь для небольших участков бетонирования без использования металлической арматуры. Кроме того, современный строительный рынок предлагает большое количество специализированных противоморозных добавок, имеющих более высокие качества и доступных по стоимости.
( Пока оценок нет )
Обзор рецептов приготовления добавок в бетон и цементный раствор своими руками
Базовой характеристикой бетона и цементосодержащих растворов является прочность на сжатие готовых изделий. Процесс схватывания и набора прочности залитого раствора привязан к гидратации цемента. Входящие в его состав минералы реагируют с водой и атмосферной углекислотой, что ведет к созданию прочной кристаллической структуры, которая, в свою очередь, связывает наполнитель: песок, гравий, шлак, щебень, керамзит…. В данной статье мы коснемся основных добавок в бетон и цементный раствор, модифицирующий их свойства и, которые можно сделать своими руками в бытовых условиях квартиры или дачи.
Цементный раствор и бетон своими руками, что это и зачем — вводная
По сути это это наиболее простой вариант бетона: смесь цементного раствора с песком крупных фракций. Применяется в основном в качестве подложек к фундаментам или как наполнитель металлических форм (сваи). Воды на раствор требуется совсем немного — только для удобного размешивания и гидратации цемента. Допускается замешевание смеси непосредственно в заливочной форме или опалубке.
Для получения более прочного цемента — необходимо добавлять наполнитель. Любопытно, что если наполнителем выступают пористые материалы (например керамзит, шлак, перлит,…) — бетон получает улучшенные теплоизоляционные свойства. Обычно используют щебень с фракцией от 2-3 мм до 30-35 мм. Важно!: щебень, как и любой другой наполнитель, должен быть чистым! Так же рекомендуется использовать заполнители разных размеров с неглаткими поверхностями, т.е. добытые дроблением горных пород.
В рецептах ниже будем считать, что 1 мешок цемента составляет 50кг. если явно не указано иное.
Итак, как самостоятельно приготовить бетон:
- Готовим форму или опалубку.
- Выбираем заполнитель с разными размерами, например смешанные крупный гравий или щебень со средним. Т.к. в домашних условиях обычно отсутствует оборудование для качественной утрамбовки бетона — именно разный размер камня позволит обеспечить плотное прилегание элементов заполнителя друг к другу, что не позволяет образовываться крупным пустотам.
- Смешиваем песок с цементом в корыте, ведре или бетономешалке.
- Заливаем воду, которая должна быть максимальновозможно чистой и без посторонних щелочных или кислотных включений.
- Понемногу начинаем добавлять цемент и заполнитель постоянно перемешивая.
- Тщательно перемешав!!!, выливаем готовый раствор в форму или опалубку и, по возможности, утрамбовываем его подручными средствами.
Пропорции в технологии приготовления бетона не даны, т.к. для разных целей требуется и разный его состав. Фундаменты под дом или крупные строения требуют включения крупных заполнителей и цементный раствор нужен достаточно текучим и в количестве, достаточном для их сцепления/закрепления. Наиболее распространены пропорции бетонного раствора 1:3:6, где соответственно цемент, песок и заполнитель + к этому 0,5-1 воды. Покомпонентный с пропорциями состав бетона изложен в ГОСТ 7473-94 и СНиП 5.01.23-83.
Пластификаторы своими руками
История знает много рецептов и методик по улучшению характеристик бетона. Например уже в 19 веке для увеличения пластичности и адгезии в раствор добавляли белок от куриного яйца, в 20-м веке, после появления гашеной извести (пушонки), переключились на нее. Сейчас в домашних условиях иногда добавляют стиральный порошок или другие моющие средства.
Приготовление в домашних условиях пластификатора для бетона и цементного раствора своими руками
Рецепт 1: добавляем жидкое мыло или шампунь
Вводится при затворении смеси. Требуется 200-250 мл на 50 кг цемента (далее мешок).
- Замешиваем воду с 200-250 мл. жидкого мыла и выливаем в ведро/корыто для приготовления раствора.
- Начинаем добавлять цемент (1 мешок) и наполнитель.
- Качественно перемешиваем раствор и заполняем им наши формы или опалубку.
Имейте в виду, что если не сократить кол-во воды на 200-250 мл. (т.е. на количество добавленного нами жидкого мыла) – время застывания бетона увеличится на 3 часа.
Рецепт 2: добавляем стиральный порошок
Предварительно растворяется в воде. Вводится при затворении смеси. Требуется 100-150 г. на мешок цемента.
- Растворяем 100-150 г. стирального порошка в теплой воде
- Замешиваем воду с раствором порошка и выливаем в ведро/корыто для приготовления раствора.
- Начинаем добавлять цемент (1 мешок).
- Качественно перемешиваем раствор и заполняем им наши формы или опалубку.
Комментарий к Рецептам 1 и 2:
Стоит учесть, что мыльный раствор заливается первым и мешать надо очень аккуратно – это позволит избежать появления пены, которая при взаимодействии мелкими частицами цемента нивелирует его свойства – т.е. испортит цементосодержащий раствор.
Какие недостатки и проблемы можно получить от применения такого мыльного пластификатора:
- Мыльные растворы вымывают соли на поверхность, что приводит к появлению высолов (соляных разводов).
- Поверхность готового бетона не покрывается специальной водоотталкивающей пленкой
- Жидкое мыло не позволяет образовываться микропузырькам внутри бетонного раствора, что затрудняет миграцию воды по раствору. В следствие этого бетонная конструкция быстро намокает и в слабопроветриваемых помещениях или без антисептической обработки может покрываться плесенью и грибком.
Рецепт 2: добавляем гашеную известь-пушенку
Данная технология, возможно с небольшими отступлениями, широко применялась при строительстве кирпичных домов в советское время. Гашеная известь придает раствору повышенную клейкость и эластичность, добавляет сцепляющих возможностей, а также придает бетону бактерицидные свойства и предотвращает появление на поверхности плесени и грибка.
Как и мыльный раствор, гашеную известь добавляют первой в количестве не более 15-20% от массы цемента.
Рецепт 2: добавляем клей ПВА
Технология широко применяется в дачном строительстве и ремонтных работах в гаражах и квартирах. Клей ПВА, добавленный в цементный раствор, улучшает его подвижность, повышает итоговую прочность и водостойкость бетона.
Вводится при затворении смеси. Требуется 200 г. на ведро раствора.
Противоморозные добавки
Позволяют заливать опалубку и заливочные формы с очень низкими теплоизолирующими свойствами при минусовых температурах не допуская, при этом!, замерзания воды в растворе. Регламентируется согласно ГОСТ 1006(0-4)-95.
Марка морозостойкости идентифицируется буквой «F» и числом от 25 до 1000 (больше показатель -> выше морозостойкость). Марки F25-100 допускаются к применению при строительстве жилых домов. Марки выше F100 — при возведении гидротехнических сооружений.
Противоморозные добавки своими руками в бетон и цементосодержащий раствор в домашних условиях
В нашей стране в качестве противоморозной добавки часто используют соли (хлориды). Хлористая соль сильно опускает температуру замерзания жидкостей в растворе и, как следствие, уменьшает время его схватывания дополнительно сокращая расход цемента. Т.е. по сути есть 2 проверенных и доступных варианта: соль хлорид натрия (по сути это техническая соль) и хлорид кальция (на данный момент недорогая и эффективная противоморозная добавка).
К недостаткам применения соли можно отнести невозможность ее применения при работе с армированными металлом (арматурой, металлической фиброй) бетона, т. к. соли способствуют коррозии. Выходом из ситуации может стать добавление в раствор ингибиторов коррозии (например Нитрит-нитрат кальция добавляется в от же количестве, что и соль).
Вводится вместе с водой затворения в процессе размешивания раствора.
Ускорители твердения
Применяются как компенсатор замедленного схватывания и при потребностях в ускоренном схватывании раствора при бетонировании — т.е. когда требуется быстрый переход к следующим этапам работ.
Ускорители твердения, схватывания, застывания и гидратации цементосодержащей смеси (бетона) своими руками в бытовых условиях
Если не брать строительную химию, способствующую ускорению схватывания бетона, то реально работающих народных средств не так уж и много. Наиболее распространенный в промышленности способ ускорить твердение бетона — это его тепловая обработка насыщенным паром. При наличии специальной камеры применение данной технологии наиболее удобно.
Если нет спец. оборудования, то используют электропрогрев самого бетона или опалубки.
Электропрогрев бетона проводами
Технология достаточно проста и применяется в основном при температуре ниже -5C. Способ позволяет ускорить гидратацию цемента в бытовых условиях и основывается на применении ПНСВ (Провод Нагревательный Стальной Виниловая оболочка) и понижающего трансформатора, в качестве которого можно задействовать сварочный аппарат.
Перед заливкой внутри каркаса из арматуры, укладывают петли из ПНСВ, которые будут нагреваться понижающим трансформатором. Кабель надо укладывать аккуратно, закрепив к каркасу и не перетерев, при этом, изоляцию. При поврежденной изоляции возникнет КЗ через землю и петля целиком выйдет из строя.
Достоинством является доступность и, относительная, дешевизна способа. Недостатками — неудобства прокладки кабеля (укладки петель).
Электропрогрев бетона электродами
Технология прогрева опалубки электродами аналогичен по сути методу с ПНСВ. Отличие лишь в том, что в этом способе нагревательный элемент это арматура и/или катанка (8-10 мм). Технология удобна при возведении вертикальных бетоноконструкций с применением вертикальной опалубки.
Электроды для удобства втыкают сразу после этапа заливки бетона на расстоянии 0,6-1 м между прутками. Интервалы выбираются в зависимости от температуры по принципу: чем ниже, тем меньше расстояние. Особенностью такого подхода является то, что нагрев идет не электродов, а жидкости между ними по принципу кипятильника из двух лезвий. Так, например, для прогрева столба хватит всего одного прутка арматуры, который будет фазой, а роль земли возьмет на себя металлический каркас.
Недостатком прогрева электродами является высокая энергозатратность, т.к. только один электрод потребляет 45-50А.
Электропрогрев опалубки бетона
Само название метода говорит за себя — монтаж нагревательных элементов происходит прямо в щиты опалубки.
Достоинством технологии электропрогрева опалубки являются:
- возможность простой замены в греющих элементов практически в любой момент,
- опалубка может быть практически не ограниченной высоты
- возможность применять способ до -25С
К недостаткам можно отнести высокую стоимость при работе с малыми и нестандартными конструкциями.
Замедлители твердения
В основном применяются при транспортировке бетонных и цементосодержащих растворов, а в бытовых условиях необходимость в них крайне мала, т.к. даже в рамках дачи всегда можно сделать ровно то количество бетонного раствора, которое необходимо.
Микроармирующие добавки — фибра
Применяется как альтернатива армирующей сетке или как дополняющий элемент, способствует борьбе с образованием микротрещин в бетоне. Заводы выпускают металлическую, полипропиленовую, базальтовую, полиэфирную фибру и стекловолокно. Современные технологии позволяют выпускать микроармирующие добавки, способные полностью выдавить традиционные методы армирования из ряда строительных и производственных отраслей. Например уже редко где встретишь армированные бордюры, колодезные кольца и т.д.
В домашних условиях изготовить качественное фиброволокно из полипропилена или базальта крайне сложно, а точнее даже невозможно, но металлическое волокно сделать вполне реально.
Фибра и фиброволокно своими руками в домашних условиях
Еще в стародавние времена роль микроармирующего элемента выполняли подручные материалы и мы до сих пор можем встретить избы-мазанки при изготовлении стен, которых использовалась солома или сено. Сейчас практикуется нарезка проволоки нужной длины, но надо понимать, что характеристики сильно зависят от формы.
Цемент/бетон в зимнее время — Стройка и ремонт
Господа!
Работать с цементом можно при любой отрицательной температуре
Ограничении вовсе не в цементе а в морозоусточивости работника.
Для начала немного теории.
Есть такое понятие как ВОДО-ЦЕМЕНТНОЕ СООТНОШЕНИЕ
Суть этого дела такова: в рекцию с цементом известного объема может вступить вполне конкретное количество воды ни больше и не меньше.
Причем той воде которая вступила в реакцию глубоко безразлично сколько градусов за бортом, реакция завершиться при любой погоде…. это просто вопрос времени.
Вся трудность состоит в том, что идеально выдержать эту пропорцию можно только в лаборатории….
Но идеально нам и не надо нам свободной воды было минимальное количество.
Собственно методика расчета этого отношения описана в любой книжке посвященной бетонам.
Вообще этот расчет не сложен потому как искомое значение В/Ц берется из таблицы в зависимости от марки цемента и требуемой марки раствора.
Но для правильного выбора количества добавляемой воды надо знать влажность заполнителя (песок щебень и тп)
Ну а теперь практика:
Доля успешного замеса нам потребуется:
А)Подготовка
1) берем некую емкость например ведро взвешиваем пустое, взвешиваем полное цемента (сухого)
Теперь мы знаем сколько кг цемента влезает в наше ведро (нам это понадобиться)
2) Рассчитываем водо-цементное отношение
3) Выбираем пропорцию цемент заполнитель и рассчитываем сколько воды нам понадобиться для затворения смеси
Б)Эксперимент
1) Гарцуем смесь (смешиваем заполнитель и вяжущее без воды но соблюдая пропорцию)
2) Затворяем смесь ГОРЯЧЕЙ ВОДОЙ!!! (разумеется с соблюдением отношения рассчитанного выше)
я в свое время делал смесь с В/Ц 1/3 крылечко мы отливали к новому году ударно.
Тут не стоит пугаться смесь будет очень густая и неудобная для работы.
А может и удобная тут смотря для чего 😉
3)Но мне было неудобно я добавлял «латекс» это очень хороший пластификатор для бетона можно добавлять ПВА это почти тоже самое.
Пластичность это хорошо но мне надо было быстро
поэтому чтобы раствор быстро вставал
4)я добавлял «Жидкое стекло» тут два в одном во первых ускоритель схватывания (на химию процесса оно не влияет но схватыват раствор быстрее)
Во вторых введение жидкого стекла снижает точку замерзания свободной воды не вступившей в реакцию с цементом.
Пропорции модификаторов я вам не скажу потому как и то и другое я лил на глаз 9лет назад.
Но вводить модификаторы в раствор надо именно в описанном мной порядке. у латекса есть любопытное свойство после введения в раствор и размешивания раствору надо дать постоять недолго после повторного размешивания раствор будет более пластичным чем после первого.
Собственно для этого и нужен эксперимент и возможно не один.
Как было верно отмечено выше при реакции цемент вода выделяется некое количество тепла.
Поэтому с учетом того что мы затворяли раствор ГОРЯЧЕЙ водой весьма целесообразно утеплите результат ваших трудов
хотябы закрыв плёнкой, а лучше пленкой а затем минеральной ватой
Изменено пользователем Sulde
Соли в растворах, воздействие на бетоны
Ко второму виду относятся процессы, связанные с химическим взаимодействием между цементным камнем и агрессивными агентами, которое приводит к образованию либо легко растворимых продуктов, выносимых из бетона во внешнюю среду в результате диффузии или фильтрации, либо атмосферных веществ, не обладающих вяжущими свойствами и не способных препятствовать дальнейшему развитию коррозии. Процессы, обнесенные ко второму виду, имеют место в тех случаях, когда на бетон воздействуют растворы кислот и некоторых кислых солей, В этих средах разрушение бетона происходит во много раз интенсивнее, чем при коррозии выщелачивания.
[c.120]
НИХ структурных напряжений, которые могут привести к разрушению материала. Очевидно, что в условиях циклического воздействия коррозионно опасными могут быть не только жидкости, способные к активному химическому взаимодействию, но и растворы веществ, химически инертных по отношению к цементному камню. Установлено, что при действии таких растворов коррозионное, разрушение бетона начинается, когда его поровое пространство заполняется кристаллами соли на 85. .. 95 %. При известной концентрации агрессивного раствора число циклов насыщения-высушивания (/i), необходимое для достижения критической концентрации твердого вещества в норовом пространстве бетона, может быть выражено моделью
[c. 134]
Полученные теоретическим путем в работе [59] расчетные формулы описывают 10 разновидностей коррозионных процессов в зависимости от вида разрушения (с буфером и без буфера), интенсивности конвективного обмена, а также наличия или отсутствия агрессивного вещества в растворе. Для 3-го вида коррозии бетона (по В. М. Москвину [62]) под действием кристаллизующихся в его порах солей в настоящее время решений не имеется. Полученные решения для 1-го и 2-го вида охватывают лишь постоянное взаимодействие жидкой среды с бетоном. Практически же для большинства промышленных зданий характерно периодическое воздействие на наземные строительные конструкции жидких агрессивных сред (например, увлажнение и высушивание, образование зон капиллярного подсоса и испарения), при котором коррозия 2-го вида может сопровождаться коррозией 3-го вида с разной степенью влияния на разрушение бетона, а также может получить опережающее развитие (стать контролирующим) процесс коррозии арматуры.
[c. 10]
Наиболее интенсивно происходит разрушение бетона под воздействием кислых реагентов. В этом случае, так же как и при воздействии солей, разрушение цементного камня вызывается главным образом понижением щелочности жидкой фазы. При этом скелет цементного камня, состоящий из гидроокиси кальция, силикатов и алюминатов, разрушается. Некоторые соли, образующиеся в результате этих реакций (углекислые, фтористые, силикаты), могут в начальный период уплотнять бетон, другие, особенно соли серной и соляной кислот, образуют рыхлые и нестойкие соединения на поверхности бетона. Содержа-шиеся в окружающей среде газы могут образовывать растворы кислот, которые также вызывают коррозию бетона. [c.5]
При проектировании зданий и сооружений необходимо учитывать затраты на строительство контрольных смотровых скважин для систематической регистрации изменений в химическом составе грунтовых вод. Приведенный выше краткий перечень отдельных положений проектирования зданий и сооружений с сильноагрессивными средами показывает, что защита от коррозии не может рассматриваться изолированно, лишь как проблема обеспечения химической стойкости и долговечности строительных элементов. Кислоты, щелочи, растворы солей оказывают коррозионное воздействие не только на бетон, сталь, кирпич, асбестоцемент, но еще большую опасность они представляют для грунтов и грунтовых вод, так как заранее предусмотреть все последствия нарушения геохимического равновесия в природе не всегда удается.
[c.163]
Кремнийорганические жидкости ГКЖ-Ю и ГКЖ-11— этилсиликонат и метилсиликонат натрия относятся к типу воздухововлекающих добавок. Улучшают структуру затвердевшего бетона адсорбируясь на цементных частицах гидрофобйзируют стенки пор и капилляров. Поставляются в виде водно-спиртовых растворов с содержанием основного вещества около 30 %. Вводятся в бетонную смесь в количестве 0,05. .. 0,2 % от массы цемента. Повышаю морозостойкость бетона в 2. .. 3 раза, водонепроницаемость — на две марки, трещиностойкость, стойкость к воздействию растворов минеральных солей, в том числе сульфатов, а также значительно понижают скорость капиллярного подсоса воды бетоном.
[c.149]
Сульфат железа — уплотняющая добавка. При введении в бетонную смесь вступает в обменную реакцию с гидроокисью кальция с образованием труднораствори -мой гидроокиси железа высокой дисперсности и двувод -кого гипса, которые активно участвуют в структурообра-зовании цементного камня на ранних стадиях твердения. Поставляется в виде кристаллического порошка. Вводится в бетонную смесь в количестве 1. .. 3 % от массы цемента. Повышает непроницаемость бетона на две марки, проч ность — на 10. .. 15 %, стойкость к воздействию водных растворов минеральных солей, в том числе сульфатов. Наибольший эффект достигается при работе с цементами пониженной активности. [c.150]
Суперпластификатор С-3 — синтетический продукт на основе сульфированной нафталино-формальдегид-ной смолы относится к типу пластифицирующих уплотняющих добавок. За счет адсорбции на цементных частицах способствует их активному диспергированию и облегчает смачивание, что приводит к значительному повышению подвижности бетонной смеси. Поставляется в виде водного раствора 33. .. 38 %-ной концентрации. Вводится в бетонную смесь в количестве 0,2. .. 1,2 % от массы цемента в пересчете на сухое вещество. Повышает водонепроницаемость бетона на две-три марки, прочность—на 30 40 %, стойкость к воздействию нефтепродуктов, а также растворов минеральных солей в условиях капил-
[c.150]
Бетонные строительные конструкции во влажной почве подвержены действию водных растворов различных минеральных и органических солей. Степень коррозионного воздействия этих солей на бетоны зависит от их концентрации, pH, от химического состава вяжущего и койпонентов бетона. Кислые соли являются агрессивными по отношению затвердевшему цементному камню в бетоне, всегда содержащему значительные количества извести. Их действие на бетон рассматривается в IV части. [c.164]
Толщина цементнобетонного слоя выбирается в зависимости от нагрузки и составляет, как правило, 40—100 мм. Полы, облицованные кИ слотоупорным бетоном на основе жидкого стекла, применяются для защиты от действия минеральных кислот (за исключением плавиковой) и растворов их солей, имеющих кислую реакцию, а также большинства растворителей. Кислотоупорный бетон нестоек в щелочах и растворах солей, имеющих щелочную реакцию. Длительное воздействие на кислотоупорный бетон воды приводит к значительному снижению его механической прочности и ухудшению защитных свойств. В связи с высокой проницаемостью кислотоупорных бетонов, обусловленной их повышенной пористостью, при устройстве таких полов особое анимание должно быть уделено созданию надежного непроницаемого подслоя.
[c.285]
Сульфитно-дрожжевая бражка СДБ — продукт переработки кальциевых солей лигносульфоновых кислот относится к типу пластифицирующих добавок. Адсорбируясь на поверхности цементных зерен, устраняет слипание между ними, повышает подвижность бетонной смеси, способствует вовлечению в бетонную смесь воздуха. Поставляется в виде жидких и твердых концентратов. Вводится в бетонную смесь в количестве 0,15. .. 0,3 % от массы цемента в пересчете на сухое вещество. Позволяеи повышать прочность бетона на 5. .. 10 %, морозостойкость — в 1,5. .. 2 раза, водонепроницаемость — на одну марку, а также трещиностойкость и стойкость к воздействию растворов минеральных солей. Наибольший эффект достигается при введении в бетоны на быстротвердеющих и высокоалюминатных портландцементах.
[c.148]
Покрытия на основе хлоркаучука отличаются высокой химической стойкостью. Их применяют для наружной защиты аппаратуры, емкостей и т. д., стальных и бетонных конструкций, эксплуатирующихся в цехах химических предприятий. Они выдерживают воздействие газов (хлора, сероводорода, паров нитрующей смеси, аммиака, двуокиси серы, фтористого и хлористого водорода, двуокиси углерода), кислот (соляной, серной, фосфорной), щелочной и моющих средств, солей, спиртов, хлорной воды, паров циклогексанона и бензола. На основе хлоркаучука вырабатывается химически стойкая змаль КЧ-749, представляющая собой раствор хлоркаучука в ксилоле с добавлением пластификаторов и пигментов. Она предназначена для защиты поверхностей, эксплуатирующихся в кислых и щелочных средах при 60°. Эмаль выпускается белого и серого цвета с вязкостью 30—60 секунд по вискозиметру по ВЗ-4. Наносится на подготовленную поверхность по -слою грунта КЧ-075 (также на основе хлоркаучука). Покрытие высыхает за 2—3 часа, им,еет красивый внешний вид. Однако воздействие сильно агрессивных сред может быть лишь периодическим.
[c.234]
В последние годы все более уве-личгшается применение для защиты от коррозии различного водоподго-товительного оборудования лако-1 расочиых материалов на основе эпоксидных смол. Эти материалы выгодно отличаются от других материалов, выпускаемых промышленностью хорошей стойкостью к воздействию воды, растворов кислот, щелочей и нейтральных солей при повышенных температурах (150—200°С) очень высокой адгезией к черным и цветным металлам, пластмассам, бетону, стеклу практическим отсутствием усадки ири затвердевании гибкостью в тонких слоях и т. д. Покрытия хорошего качества из материалов на основе эпоксидных смол могут быть получены как при повышенной температуре, так и при сушке в обычных условиях. Для перевода термопластичных и растворимых смол в неплавкое и нерастворимое состояние в эпоксидные лакокрасочные материалы перед употреблением добавляются специальные вещества— отвердители. Некоторые марки этих материалов содержат, помимо эпоксидной смолы и растворителя, также пигменты и наполнители.
[c.47]
Агрессивное воздействие кислых газов на железобетонные конструкц1П1 зданий н сооружений проявляется в повреждении бетона и стальной арматуры. Проникая в поры бетона, кислые газы растворяются в жидкой фазе, образуют кислоты и, вступая в химические реакции с гидратом окиси кальция, силикатами, алюминатами н другими соединениями цементного камня, нейтрализуют его с образованием соответствующих кальциевых солей, геля кремнекислоты, гидратов алюминия и железа. Следствием этого является постепенное перерождение цементного камня. Основные минералы разрушаются, понижается щелочность жидкой фазы, прочностные и деформатпвные свойства бетона ухудшаются, утрачивается способность поддерживать стальную арматуру в пассивном состоянии. [c.51]
В принципе отклонения от результатов такого расчета могут быть вызваны связыванием хлорид-ионов в гидрохлоралюминаты, а также изменениями влажности среды и бетона. Влияние этих факторов отчасти учитывается в исходных данных, поскольку эти факторы действуют с начала эксплуатации конструкции. Однако редкие случайные повышения влажности могут существенно изменить скорость проникания хлоридов в бетон. В случае появления конденсата раствор солей будет проникать в глубь бетона за счет капиллярного всасывания, т. е. значительно интенсивнее, чем по диффузионному механизму. Поэтому в сложных случаях нестационарных режимов воздействия среды на конструкцию необходимы специальные исследования.
[c.179]
Влияние гидрофобных обработок на повышение солевой морозостойкости бетона
. 2020 26 ноября; 13 (23): 5361.
DOI: 10.3390 / ma13235361.
Принадлежности
Расширять
Принадлежности
- 1 Ключевая лаборатория по изучению воздействия на окружающую среду и структурной безопасности в машиностроении Цзянсу, Китайский горно-технологический университет, Сюйчжоу 221116, Китай.
- 2 Школа архитектуры, Северо-Китайский университет водных ресурсов и электроэнергии, Чжэнчжоу 450045, Китай.
Бесплатная статья PMC
Элемент в буфере обмена
Гуо Ли и др.
Материалы (Базель).
.
Бесплатная статья PMC
Показать детали
Показать варианты
Показать варианты
Формат
АннотацияPubMedPMID
. 2020 26 ноября; 13 (23): 5361.
DOI: 10.3390 / ma13235361.
Принадлежности
- 1 Ключевая лаборатория по изучению воздействия на окружающую среду и структурной безопасности в машиностроении Цзянсу, Китайский горно-технологический университет, Сюйчжоу 221116, Китай.
- 2 Школа архитектуры, Северо-Китайский университет водных ресурсов и электроэнергии, Чжэнчжоу 450045, Китай.
Элемент в буфере обмена
Полнотекстовые ссылки
Опции CiteDisplay
Показать варианты
Формат
АннотацияPubMedPMID
Абстрактный
Гидрофобная обработка — важный метод улучшения водонепроницаемых свойств бетона. Для оценки эффективности гидрофобных обработок по повышению стойкости бетона к солевой морозостойкости были выбраны два типичных коммерческих обычных водоотталкивающих агента — силан и кремнийорганическая эмульсия, и были изготовлены образцы бетона с тремя соотношениями вода / цемент. После нанесения репеллентов на бетонные поверхности, образцы были подвергнуты ускоренным циклам замораживания-оттаивания солевым раствором (5% MgCl 2 ). Потери массы и относительный динамический модуль упругости (RDME) бетона периодически проверялись.Углы смачивания и коэффициент водопоглощения бетона с гидрофобной обработкой и без нее также были протестированы. Результаты показали, что репелленты могут значительно повысить гидрофобность бетона и значительно снизить его водопоглощение. Различные репелленты по-разному улучшали гидрофобность бетона. Между тем, репелленты могут в определенной степени улучшить стойкость бетона к солевому отложению и потерям RDME, а бетон с высокой гидрофобностью показал относительно высокую солевой морозостойкость.
Однако обычные водоотталкивающие агенты не могут обеспечить такое же улучшение устойчивости бетона к солевой морозостойкости, как гидрофобность бетона по отношению к воде. При циклах замораживания и оттаивания солевого раствора гидрофобный слой, образованный репеллентами на поверхностном бетоне, постепенно разрушался. В результате морозостойкость бетона после гидрофобных обработок была окончательно потеряна.
Ключевые слова:
конкретный; угол контакта; цикл замораживания-оттаивания; гидрофобная обработка; солевые накипи.
Заявление о конфликте интересов
Авторы заявляют об отсутствии конфликта интересов.
Цифры
Рисунок 1
Образцы призматического бетона с нанесением…
Рисунок 1
Образцы призматического бетона с нанесенным репеллентом BS4004.
фигура 1
Образцы призматического бетона с нанесенным репеллентом BS4004.
Рисунок 2
Схема водопоглощения…
Рисунок 2
Схема эксперимента по водопоглощению для одной стороны бетона.
фигура 2
Схема эксперимента по водопоглощению для одной стороны бетона.
Рисунок 3
Капли воды на поверхности…
Рисунок 3
Капли воды на поверхности бетона, обработанной различными репеллентами: (…
Рисунок 3
Капли воды на поверхности бетона, обработанной различными репеллентами: ( a ) необработанный, ( b ) BS4004 и ( c ) C3033.
Рисунок 4
Развитие водопоглощения…
Рисунок 4
Развитие водопоглощения бетона с поверхностной обработкой с различным соотношением в / к: (…
Рисунок 4
Развитие водопоглощения бетона с поверхностной обработкой при различных соотношениях в / ц: ( a ) в / ц = 0. 6, ( b ) w / c = 0,5 и ( c ) w / c = 0,4.
Рисунок 5
Типичный вид бетона…
Рисунок 5
Типичный вид образцов бетона после различных циклов замораживания / оттаивания: ( a )…
Рисунок 5.
Типичный внешний вид образцов бетона после различных циклов замораживания / оттаивания: ( a ) необработанный (0 цикл), ( b ) необработанный (50 циклов), ( c ) необработанный (100 циклов), ( d ) BS4004 (0 циклов), ( e ) BS4004 (50 циклов), ( f ) BS4004 (100 циклов), ( г ) C3033 (0 циклов), ( ч ) C3033 (50 циклов ) и ( i ) C3033 (100 циклов).
Рисунок 6
Типовые образцы бетона после соли…
Рисунок 6
Типовые образцы бетона после опытов с солевым морозом: ( a ) необработанные (275 циклов),…
Рисунок 6
Типичные образцы бетона после экспериментов с солевым морозом: ( a ) необработанные (275 циклов), ( b ) C3033 (275 циклов) и ( c ) BS4004 (300 циклов).
Рисунок 7
Коэффициенты потери массы бетона…
Рисунок 7
Коэффициенты потери массы бетона, подвергнутого гидрофобной обработке с циклами замораживания-оттаивания: (…
Рисунок 7
Коэффициенты потери массы бетона, подвергнутого гидрофобной обработке с циклами замораживания-оттаивания: ( a ) w / c = 0. 6, ( b ) w / c = 0,5 и ( c ) w / c = 0,4.
Рисунок 8
Относительный динамический модуль упругости…
Рисунок 8
Относительный динамический модуль упругости (RDME) бетона, подвергнутого гидрофобной обработке…
Рисунок 8
Относительный динамический модуль упругости (RDME) бетона, подвергнутого гидрофобной обработке с циклами замораживания-оттаивания: ( a ) w / c = 0.6, ( b ) w / c = 0,5 и ( c ) w / c = 0,4.
Рисунок 9
Схема капиллярной воды…
Рисунок 9
Схема капиллярного водопоглощения бетона после гидрофобной обработки: ( а…
Рисунок 9
Схема капиллярного водопоглощения бетона после гидрофобной обработки: ( a ) необработанный бетон, ( b ) бетон с гидрофобной обработкой и ( c ) бетон после солевого мороза.
Все фигурки (9)
Похожие статьи
Метод испытаний для защиты от обледенения высокопрочного бетона.
Strand MJ, Фрид К.
Strand MJ, et al.
МетодыX. 2018 9 октября; 5: 1299-1310. DOI: 10.1016 / j.mex.2018.10.007. eCollection 2018.
МетодыX. 2018.PMID: 30370225
Бесплатная статья PMC.Экспериментальное исследование циклов замораживания и оттаивания бетона с компенсацией усадки с двойными расширяющими добавками.
Го Дж, Го Т, Чжан С., Лу Ю.
Гуо Дж и др.
Материалы (Базель). 2020 15 апреля; 13 (8): 1850. DOI: 10.3390 / ma13081850.
Материалы (Базель). 2020.PMID: 32326462
Бесплатная статья PMC.Морозостойкость и пористая структура бетона, содержащего резиновые заполнители и нано-SiO 2 .
Фанг Дж., Чжао Л., Ши Дж.
Фанг Дж. И др.
Материалы (Базель). 2 марта 2021 г .; 14 (5): 1170. DOI: 10.3390 / ma14051170.
Материалы (Базель). 2021 г.PMID: 33801516
Бесплатная статья PMC.Отходы ильменитовых грязей как добавка для морозостойкости устойчивого бетона.
Хилински Ф., Кучиньски К.
Chyliński F, et al.
Материалы (Базель). 2020 Июнь 28; 13 (13): 2904. DOI: 10.3390 / ma13132904.
Материалы (Базель). 2020.PMID: 32605247
Бесплатная статья PMC.Структура и реакционная способность воды на поверхности биоматериала.
Фоглер Э.А.
Фоглер Э.А.
Adv Colloid Interface Sci. 1998 Февраль; 74: 69-117. DOI: 10.1016 / с0001-8686 (97) 00040-7.
Adv Colloid Interface Sci. 1998 г.PMID: 9561719
Рассмотрение.
Рекомендации
Перенчо В.Ф. Прочность бетона, обработанного силанами. Concr. Int. 1988. 10: 34–40.
Бузубаа Н., Билодо А., Фурнье Б., Хутон Р.Д., Ганье Р.Р.Д., Джолин М. Устойчивость бетона к образованию отложений солевого налета с добавлением дополнительных цементирующих материалов: данные лабораторных и полевых испытаний. Может. J. Civ. Англ. 2008; 35: 1261–1275. DOI: 10.1139 / L08-067.
—
DOI
Чжан Ю.
Q., Yu H.F., Sun W., Wang J.C., Cao W.T., Zhou P. Исследование и изучение прочности моста при солевых отложениях. J. Build. Матер. 2012; 15: 665–669.
Ю. Х. Ф., Сунь В., Ян Л. Х., Ван К. Исследование долговечности при замораживании-оттаивании воздухововлекающего бетона, подверженного воздействию соленых озер. J. Wuhan Univ. Technol. 2004; 26: 15–18.
Пенттала В.Поверхностное и внутреннее разрушение бетона из-за солевых и незасоленных нагрузок замерзания-оттаивания. Джем. Concr. Res. 2006; 36: 921–928. DOI: 10.1016 / j.cemconres.2005.10.007.
—
DOI
Показать все 45 ссылок
(PDF) Влияние типа цемента на устойчивость бетона к замораживанию — оттаиванию и противообледенительной соли
1050 Гинтаутас Скрипкиунас и др. / Procedure Engineering 57 (2013) 1045 — 1051
данными исследований трудно объяснить большое увеличение скорости ультразвуковых импульсов композиций 2 и 4 после 14 циклов замораживания-оттаивания
.
Тип изменения кривых деформации, представленный на рис. 3, остается одинаковым на протяжении всего времени испытания (28
циклов замораживания-оттаивания).
После 7 циклов замораживания-оттаивания образцы деформируются отрицательно, т.е. усаживаются. После 14 циклов деформации
имеют тенденцию к увеличению и остаются отрицательными.После 21 цикла деформации увеличиваются и деформации в образцах составов
6 и 8 становятся положительными.
У всех 8 составов деформации становятся положительными только после 28 циклов замораживания-оттаивания.
Такое изменение деформации может быть связано с тем, что остаточные деформации измеряются в центре образца
(50 мм от поверхности образца), на который не влияет замораживание и оттаивание в результате хорошей теплоизоляции образца
. Более сильные деформации во второй половине испытания указывают на то, что разрушение происходит в середине образца
. Результаты испытаний показывают, что наибольшие деформации бетона произошли на испытательной поверхности, которая была покрыта раствором NaCl
, что ускорило разрушение конструкции бетона.
4. Выводы
1. Бетон, содержащий шлаковый цемент CEM III / B 32,5 N-LH без замедлителя гидратации, имеет самую высокую
стойкость к замерзанию-оттаиванию и образованию отложений против обледенения.Потеря массы в образце из этого бетона составила 0,1 кг / м
2
после 28
циклов замораживания-оттаивания. Бетон, содержащий портландцемент CEM I 42.5 R с содержанием замедлителя схватывания 1,80%, имеет самую низкую стойкость к замерзанию-оттаиванию и образованию солей против обледенения
с потерей массы 5,5 кг / м
2
.
2. Когда замедлитель гидратации добавляется в количестве 0,3% по массе цемента, потеря массы увеличивается до 2,6 раз, а скорость ультразвукового импульса
падает до 25%. Когда замедлитель гидратации добавляется в количестве 0,5% по массе цемента, потеря массы увеличивается до
в 5 раз, а скорость ультразвуковых импульсов падает до 34,0%. Было обнаружено, что замедлитель гидратации цемента оказывает отрицательное влияние на сопротивление бетона
замораживанию-оттаиванию и противообледенительной соли.
3. Циклическое замораживание и оттаивание оказывает существенное влияние только на поверхностный слой. Влияние солевого раствора и циклического замораживания-оттаивания
было менее значительным в более глубоких слоях, где измерялись остаточные деформации.
Благодарности
Авторы выражают благодарность AB Akmenės Cementas за предоставленный цемент для испытаний и финансовую поддержку исследования.
Ссылки
[1] Кумар, Р., Бхаттачарджи, Б., 2003. Пористость, распределение пор по размерам и прочность бетона на месте, Исследование цемента и бетона 33, стр. 155–164.
[2] Нагроцкене Д., Скрипкиунас Г. , Гирскас Г., 2011. Прогнозирование морозостойкости бетона с разной концентрацией крупного заполнителя по пористости.
Параметры
, Материаловедение 17 (2), стр.203–207.
[3] Озбай, Э., Карахан, О., Лачеми, М., Хоссейн, К.М.А., Атис, CD, 2013. Двойная эффективность замораживания-оттаивания и сульфатной атаки на большие объемы
КЭП, содержащих шлак, Композиты: Часть B 45, стр. 1384–1390.
[4] Балтренас, П., Казлаускене, А., 2009. Устойчивое экологическое развитие, снижающее негативное воздействие солей для содержания дорог, Балтийский журнал по
Устойчивое развитие 15, стр. 178–188.
[5] Кауфманн, Дж., Студер, В., 1998. «Сравнение механизмов солевого разрушения морозом в полевых и лабораторных условиях», Тр. 2-й Международной конференции
по бетону в суровых условиях (CONSEC 1998), 21–24 июня, Тромсё, Норвегия. С. 262–271.
[6] Валенца II, Дж. Дж., Шерер, Г. У., 2006. Механизм образования солей, Журнал Американского керамического общества 89, стр. 1161–1179.
[7] Валенца II, Дж. Дж., Шерер, Г. У., 2007. Обзор солевых отложений I: феноменология, исследования цемента и бетона 37, стр.1007–1021.
[8] Шерер Г. В., 1999. Кристаллизация в порах, Исследование цемента и бетона 29, стр. 1347–1358.
[9] Шерер, Г. В., Валенца II, Дж. Дж., 2005. Механизмы повреждения от замерзания, Материаловедение бетона (VII), стр. 209–246.
[10] Скрипкиунас, Г., Гирскас, Г., Нагроцкене, Д., 2012. «Устойчивость к замораживанию-оттаиванию и противообледенительной соли затвердевшего цементного теста, модифицированного синтетическим цеолитом
», Proc. Международного конгресса по прочности бетона (ICDC 2012), 18–21 июня 2012 г., Тронхейм, Норвегия, стр.1–13.
[11] Вектарис, Б., 2012. Ускорение испытания на долговечность портландцементного раствора, Химическая технология 1 (59), стр. 19–24 (на литовском языке).
[12] Скрипкиунас, Г., Нагроцкене, Д., Гирскас, Г., Янавичюс, Э., 2012. Устойчивость модифицированного затвердевшего цементного теста к морозу и солям для борьбы с обледенением,
Балтийский журнал дорог и мостов Инженерное дело 7 (4), стр. 269–276.
[13] Клозе, Н., 2002. Klimarelevante Umweltvorsorge der Zementindustrie und deren Umsetzung im Naugeschechen.Beton-Informationen, стр. 3–7.
[14] Giergiczny, Z., Glinicki, MA, Sokolowski, M., Zielinski, M., 2009. Система воздушных пустот и морозно-солевой отложения бетона, содержащего шлакобетонный цемент
, Строительство и строительные материалы 23 С. 2451–2456.
[15] Сахмаран, М., Ли, В. К., 2007. Устойчивость к образованию отложений против обледенения механически нагруженных цементных композитов, Журнал цемента и
Concrete Research 37, стр. 1035–1046.
[16] Ахани Р.М., Ноккен, М.Р., 2012. Устойчивость к образованию солей — эффект отверждения и предварительного насыщения, Строительные и строительные материалы 26, стр. 558–
564.
[17] Дежа, Дж., 2003. Замораживание и антиобледенительная солеустойчивость доменных шлакобетонов, Цементно-бетонные композиты 25, стр. 357–361.
МОРОЗОСТОЙКИЙ БЕТОН
В статье исследуются две основные проблемы морозостойкости бетона: внутреннее растрескивание из-за циклов замораживания и оттаивания и образование накипи на поверхности, как правило, из-за замерзания в присутствии антиобледенительных солей. Хотя есть еще части проблемы, которые не совсем понятны и требуют дальнейшего изучения, особенно в отношении различий между лабораторными испытаниями и полевыми испытаниями, способ сделать бетон устойчивым к циклам замерзания и оттаивания очень хорошо известен. Полевой опыт, а также лабораторные данные убедительно показали, что внутренних трещин из-за мороза в бетонах с надлежащим воздухововлекающими добавками практически не существует. Образование накипи из-за замерзания в присутствии антиобледенительных солей является гораздо более сложной проблемой, чем внутреннее растрескивание по многим причинам, но, вероятно, главным образом потому, что оно связано с микроструктурой самого поверхностного слоя или «корки» бетона.Надлежащим образом воздухововлекающие и должным образом выдержанные, хорошо спроектированные полевые бетоны из портландцемента, как правило, довольно устойчивы к образованию отложений противообледенительных солей, но они все же иногда возникают неожиданно уже через несколько лет.
Также необходимо особенно исследовать способность широко используемых тестов на образование отложений антиобледенителя для прогнозирования характеристик бетона при нормальных условиях воздействия поля. Кроме того, необходимы исследования, чтобы лучше понять процесс образования больших воздушных пустот в воздухововлекающем бетоне.
- Наличие:
- Корпоративных авторов:
Эльзевир
The Boulevard, Langford Lane
Kidlington, Оксфорд
Великобритания
OX5 1 ГБ - Авторов:
- Голубь, M
- Marchand, J
- PLEAU, R
- Дата публикации: 1996
Язык
Информация для СМИ
Предмет / указатель терминов
Информация для подачи
- Регистрационный номер: 00729206
- Тип записи:
Публикация - Агентство-источник: Лаборатория транспортных исследований
- Файлы: ITRD
Дата создания:
12 декабря 1996 г., 00:00
Морозостойкость бетона, содержащего летучую золу CFBC
Basu P (1999) Сжигание угля в котлах с циркулирующим псевдоожиженным слоем: обзор. Chem Eng Sci 54: 5547–5557. DOI: 10.1016 / S0009-2509 (99) 00285-7
Артикул
Google Scholar
Новак В. (2003) Технология чистого угольного псевдоожиженного слоя в Польше. Appl Energy 74: 405–413. DOI: 10.1016 / S0306-2619 (02) 00195-2
Артикул
Google Scholar
EN 450-1: 2005 Летучая зола для бетона. Определение, спецификации и критерии соответствия
ASTM C 618-03 Угольная зола и необработанный или кальцинированный природный пуццолан для использования в бетоне
Brandstetr J, Havlica J, Odler I (1997) Свойства и использование твердого остатка от сжигания угля в псевдоожиженном слое. В: Chandra S (ed) Отходы, используемые в производстве бетона. Noyes Publications Press, Вествуд, Нью-Джерси, США, стр. 1–47
Google Scholar
Себок Т., Симоник Дж., Кулисек К. (2001) Прочность на сжатие образцов, содержащих летучую золу с высоким содержанием сульфата кальция и оксида кальция. Cement Concr Res 31: 1101–1107. DOI: 10.1016 / S0008-8846 (01) 00506-3
Артикул
Google Scholar
Глиницкий М.А., Кобылецкий Р., Новак В., Масланка Дж. (2004) Применение механически активированной золы от сжигания угля в псевдоожиженном слое в Польше, 8-я международная конференция CANMET / ACI по летучей золе, кремнеземному дыму, шлакам и природным пуццоланам в бетоне.В материалах технических документов, организованных Консультативным комитетом США, EPRI, Пало-Альто, Калифорния (CD-ROM)
Глиницкий М.А., Нововейски Г. (2008) Долговременная прочность бетона с добавлением летучей золы из псевдоожиженного слоя сжигание каменного угля. Материалы 5-й конференции DNI BETONU 2008. Польская цементная ассоциация, Висла, Польша (на польском языке)
Глиницкий М.А., Зелински М. (2008) Система воздушных пустот в бетоне, содержащем летучую золу, образующуюся при сжигании циркулирующего псевдоожиженного слоя.Mater Struct 41: 681–687. DOI: 10.1617 / s11527-007-9273-6
Артикул
Google Scholar
Старк Д.К., Косматка С.Х., Фарни Ю.А., Теннис П.Д. (2001) Характеристики бетонных образцов в испытательном стенде PCA на открытом воздухе. RD124, Portland Cement Association, Skokie, Illinois, USA
Valenza JJII, Scherer GW (2006) Механизм образования солей. J Am Ceram Soc 89 (4): 1161–1179. DOI: 10.1111 / j.1551-2916.2006.00913.x
Артикул
Google Scholar
Pigeon M, Marchand J, Pleau R (1996) Морозостойкий бетон. Construct Build Mater 10 (5): 339–348. DOI: 10.1016 / 0950-0618 (95) 00067-4
Артикул
Google Scholar
Игараши С., Бентур А., Миндесс С. (1996) Определение микроструктуры и прочности цементного теста с помощью испытаний на микротвердость.Adv Cement Res 30: 87–92
Google Scholar
Чжу В., Бартос П.Дж.М. (2000) Применение микровыступов с измерением глубины для изучения межфазной переходной зоны в железобетоне. Cement Concr Res 30: 1299–1304. DOI: 10.1016 / S0008-8846 (00) 00322-7
Артикул
Google Scholar
Глиницкий М.А., Зелински М. (2004) Метод глубинного вдавливания для оценки эффективности вторичных вяжущих материалов.Cement Concr Res 34: 721–724. DOI: 10.1016 / j.cemconres.2003.10.014
Артикул
Google Scholar
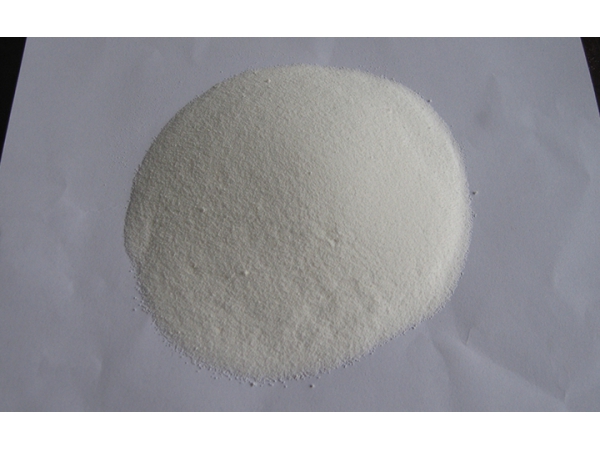
Kasperkiewicz J (2006) О возможности идентификации структуры с помощью микроиндентирования и акустической эмиссии. В: Bartos PJM (ред.) Нанотехнологии в строительстве. RILEM Proceedings pro045, pp 151–159
Tremblay M-H, Lory F, Marchand J, Scherer GW, Valenza JJ (2007) Способность модели скола клея учитывать разрушение бетона от отложений соли De-Icer.В: Beaudoin JJ, Makar JM, Raki L (eds) Paper W4-07.3 в ходе работы 12-го заседания ICCC. Национальный исследовательский совет Канады, Монреаль, Канада
CEN / TS 12390-9 (2006) Испытание затвердевшего бетона — Часть 9: сопротивление замораживанию-оттаиванию — образование накипи. Европейский комитет по стандартизации, Брюссель
SS 137244 (1995) Испытания бетона — затвердевший бетон — образование накипи при замерзании
Trtik P, Bartos PJM (1999) Микромеханические свойства вяжущих композитов.Mater Struct 32: 388–393. DOI: 10.1007 / BF02479632
Артикул
Google Scholar

Игараши С., Бентур А., Миндесс С. (1996) Испытания на микротвердость вяжущих материалов. Adv Cement Base Mater 4: 48–57
Google Scholar
Зелински М. (2007) Влияние летучей золы в псевдоожиженном слое на выбранные свойства раствора и бетона.DROGI i MOSTY No. 2: 59–85 (на польском языке)
Neuwald A, Krishnan A, Weiss J, Olek J, Nantung TE (2003) Отверждение бетона и его связь с измеренным образованием накипи в бетоне, содержащем летучую золу . Совет по транспортным исследованиям. Доступно по адресу: http://cobweb.ecn.purdue.edu/~concrete/weiss/publications/r_conference/RC-019.pdf. Процитировано 5 ноября 2007 г.
Элсен Дж. И др. (1995) Определение соотношения вода / цемент затвердевшего цементного теста и образцов бетона на шлифах с использованием методов автоматического анализа изображений.Cement Concr Res 25 (4): 827–834. DOI: 10.1016 / 0008-8846 (95) 00073-L
Артикул
Google Scholar
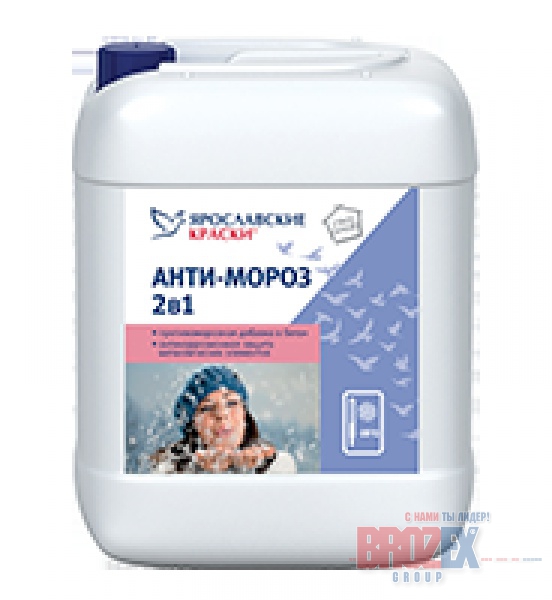
Brown PW, Shi D, Skalny J (1991) Взаимосвязь пористости / проницаемости. В: Skalny J, Mindess S (ред.) Материаловедение бетона II. Американское керамическое общество, Вестервилль, стр. 83–109
Билодо А., Малхотра В.М. (1992) Бетон, включающий большие объемы летучей золы ASTM класса F: механические свойства и устойчивость к образованию отложений солей и хлорид-ионов. проникновение.В: Малхотра В.М. (ред.) Летучая зола, микрокремнезем и природные пуццоланы в бетоне, материалы четвертой международной конференции. Специальная публикация ACI SP-132, Американский институт бетона, Детройт, стр. 319–349
Устойчивость самоуплотняющегося бетона, содержащего летучую золу, к морозу и солевой стойкости
Номер проекта 215
Самоуплотняющийся бетон (SCC) демонстрирует свойство, заключающееся в том, что до завершения выравнивания он течет без сегрегации, полностью заполняет все полости и удаляет воздух без каких-либо уплотняющих работ.
В отношении SCC до настоящего времени было проведено множество исследований, но устойчивость к воздействию замерзающей и антиобледенительной соли не исследована в достаточной степени. В настоящее время по заказу VGB Powertech Институт исследования строительных материалов (ibac) Ахенского университета работает над исследовательским проектом, касающимся устойчивости вибробетона, содержащего летучую золу, к воздействию морозильной и антиобледенительной соли (проект № 203). В этом проекте вибробетон, изготовленный в соответствии с классами воздействия XF2 и XF4 (DIN EN 206-1 07.01 и DIN 1045-2 07.01).
Что касается устойчивости к воздействию солей при замораживании и борьбе с обледенением, то в настоящее время нет технического опыта, касающегося SCC, который, в зависимости от смеси (порошкообразный, комбинированный и вязкостный), имел содержание порошка более 600 кг. / м³ и, следовательно, содержание золы уноса до 350 кг / м³. Поскольку недавно были получены первые технические разрешения на SCC, содержащие летучую золу, возникают вопросы относительно долговечности этих бетонов.Таким образом, в дополнение к текущему проекту «Влияние летучей золы на устойчивость бетона к замерзанию и противообледенительной соли», стойкость значительных SCC с высоким содержанием летучей золы к воздействию морозильной и противообледенительной соли должна составлять быть исследованным.
В отличие от вибробетона, следующие элементы недостаточно исследованы для SCC с высоким содержанием золы:
- Взаимодействие суперпластификаторов на основе поликарбоксилат-эфира нового поколения с воздухововлекающими добавками в смесях, содержащих летучую золу.
- Обеспечение достаточной стабильности воздушных пустот и содержания воздушных пор в SCC с высоким содержанием летучей золы. Замедляется образование микропор в бетонах высокой консистенции.
- Влияние условий хранения и чувствительности к отверждению SCC с большим количеством летучей золы.
- Долговременное поведение SCC с высоким содержанием летучей золы в отношении устойчивости к воздействию морозильной и антиобледенительной соли.
Таким образом, результаты этого исследовательского проекта способствуют получению подтвержденных знаний, и летучая зола SCC не может быть исключена из технических разрешений для классов воздействия XF2 и XF4.Кроме того, результаты могут быть учтены в рекомендациях «Самоуплотняющийся бетон» согласно DIN EN 206-1 07. 01 и DIN 1045-2 07.01 Немецкой комиссии по конструкционному бетону (DAfStb).
Помимо применения SCC в производстве сборных элементов, SCC с высоким содержанием летучей золы особенно подходит для строительства туннелей из-за сложности процесса их производства. Особый интерес в этом случае представляет устойчивость к воздействию солей и морозов.
Как защитить бетон от солевых повреждений
Что такое Saltguard WB?
PROSOCO’s Saltguard WB — это репеллент на водной основе, соответствующий требованиям ЛОС, который обеспечивает отличную защиту бетона и кирпичной кладки от повреждения солью.Он действует, проникая глубже, чем обычные репелленты на основе воды или растворителей, что делает его идеальным для защиты бетона от повреждения солью.
Кроме того, в прибрежных районах Saltguard WB защищает бетон от солевых повреждений, вызванных высокими уровнями хлорида натрия в воздухе. Этот тип водоотталкивающего средства действует как экран от хлоридов, проникая в основание и химически связываясь с ним, защищая от повреждения водой и солью.
Как пользоваться Saltguard WB?
Препарат
Следует избегать прямого контакта спрея.Также следует защитить другие поверхности от брызг. Несмотря на минимальный запах, вам необходимо обеспечить надлежащую вентиляцию перед использованием Saltguard WB.
Перед нанесением необходимо тщательно очистить всю поверхность с использованием соответствующих продуктов PROSOCO. Герметики, отвердители, масло, смазку и ржавчину следует полностью удалить, поскольку такие загрязнения могут повлиять на проникновение и склеивание Saltguard WB.
Для достижения наилучших результатов нанесите Saltguard WB на явно сухие поверхности.Влажные поверхности уменьшают проникновение, так как служат барьером между продуктом и бетонной поверхностью. Избыточная влажность также может снизить эффект от лечения.
Заявление
Перед нанесением необходимо убедиться, что поверхность должным образом подготовлена. Перед нанесением следует провести патч-тест для каждого типа поверхности, чтобы убедиться в пригодности. После высыхания исследуемую область следует осмотреть, и процесс будет продолжен только в том случае, если результаты будут положительными и без пятен.Нанесение следует производить в затененном месте, а контейнеры следует хранить вдали от прямых солнечных лучей.
Рекомендуется наносить репеллент в большом объеме и при низком давлении (<50 фунтов на кв. Дюйм) с помощью веерного наконечника. Кисти или валики также можно использовать для мелкомасштабного нанесения. Важно ровное и равномерное пропитывание поверхности спреем, а любые лужи или лужи следует немедленно вымыть щеткой.
Страница не найдена | MIT
Перейти к содержанию ↓
- Образование
- Исследовать
- Инновации
- Прием + помощь
- Студенческая жизнь
- Новости
- Выпускников
- О Массачусетском технологическом институте
- Подробнее ↓
- Прием + помощь
- Студенческая жизнь
- Новости
- Выпускников
- О Массачусетском технологическом институте
Меню ↓
Поиск
Меню
Ой, похоже, мы не смогли найти то, что вы искали!
Попробуйте поискать что-нибудь еще!
Что вы ищете?
Увидеть больше результатов
Предложения или отзывы?
.