Вес керамзитобетон: Вес керамзитобетонного блока 400х200х200 — таблица
- Плотность керамзитобетона (кг м3)
- плюсы и минусы, виды, маркировка, плотность и эксплуатационные качества
- Запущено производство керамзитоблоков | Монолит-ДВ
- Почему нужно выбрать керамзитобетонные блоки?
- плотность теплопроводность состав вес технические требования
- (PDF) Керамзитобетон легкий и опилкобетон на суперсульфатном цементе
- 3,
- 3, гидроталькит (Mg6Al2(CO3)(OH)16·4(h3O), незначительные фазы AFm наряду с присутствием безводного шлака и гипса. Предыдущее исследование было посвящено определению влияния низкоглиноземистых доменный шлак и обезвоженный фосфогипс на свойства SSC [Дворкин 2012]. Для производства легких бетонов на основе цемента применяются различные заполнители [Sonebi et al., 2013]. Серия исследований доказала влияние нескольких основных факторов на прочность легкого бетона: водоцементного отношения , прочности заполнителя, пористости межфазной зоны и внутри затвердевшего цементного теста [Lo 2007]. АВС в производстве строительных материалов
- Большие перспективы производства керамзитобетона в Беларуси
- ТОП-5 крупнейших покупателей бетонных блоков в 🇧🇩 Бангладеш
- Типоразмер керамзитоблоков по ГОСТ
- Керамзитобетон: пропорции для приготовления
- Свойства и характеристики материала
- Керамзитобетон: пропорции и состав раствора
- Преимущества и недостатки стяжки из керамзитобетона
- Наличие технологии производства блоков
- Формование блоков керамзитовых
- Керамзит: состав и пропорции смеси для формовки блоков
- Приготовление раствора
- Формовка блоков и завершающий этап
- Столбчатый фундамент из блоков своими руками. Устройство столбчатого фундамента из блоков 20х20х40
Плотность керамзитобетона (кг м3)
Керамзитобетон – материал легкий и при этом прочный. Плотность его варьирует от 350 кг/м3 до 1800 кг/м3. Строить из керамзитобетонных блоков сможет любой, кто знаком с кирпичной кладкой, но при этом кладка из блоков будет в 2,5 раза легче и быстрее кладки из кирпичей.
Благодаря тому, что керамзитобетонные блоки объемные, кладка ускоряется в 3 раза по сравнению с кирпичной. При этом толщина стен из этого строительного материала меньше, а теплоизоляция при этом лучше, чем в случае строительства из кирпичей. За счет небольшого веса керамзитобетонных блоков, на фундамент оказывается небольшая нагрузка, что позволяет сократить расходы на строительство самого фундамента.
От чего зависит плотность керамзитобетона
Изготавливается керамзитобетон из песка, цемента, керамзита (при этом могут быть использованы различные его фракции: от 5 до 40 мм), смол и гипса. Поэтому его плотность во многом зависит от того, сколько было взято керамзита при его производстве (она будет тем меньше, чем больше будет использовано керамзита). Увеличение расхода цемента при изготовлении керамзитобетонных блоков уменьшает их удельный вес и увеличивает объемный вес. Удельный вес керамзитобетонного блока представляет собой отношение веса блока к занимаемому ним объему, а объемный вес керамзитобетона характеризует его плотность.
Не стоит путать удельный и объемный вес веществ – это разные понятия!
Виды керамзитобетона
Выделяют 3 вида керамзитобетона:
- конструкционный;
- теплоизоляционный;
- конструкционно-теплоизоляционный.
При строительстве несущих стен применяют конструкционный керамзитобетон. Плотность керамзитобетона этого вида составляет 1200-1800 кг/м3. Он довольно морозостойкий (выдерживает до 500 циклов заморозки-разморозки).
Теплоизоляционный керамзитобетон имеет плотность 350-900 кг/м3. Он используется для теплоизоляции и позволяет сохранять зданию тепло зимой и прохладу летом. Конструкционный керамзитобетон имеет плотность 700-1400 кг/м3. Из него строят стены.
Чем меньше объемный вес керамзитобетона, тем выше теплопроводность керамзитобетонных блоков. Чем выше его удельный вес, тем он прочнее. Прочность этого материала является достаточной для малоэтажного строительства. Чтобы кладка не разрушилась от влаги и холода, необходимо защитить ее при помощи стандартных материалов для утепления.
плюсы и минусы, виды, маркировка, плотность и эксплуатационные качества
Дата публикации: 09.02.2019 11:19
Керамзитобетон относится к монолитным стройматериалам, получаемым путем затворения (смешивания в воде) портландцемента, песка средней фракции и наполнителя, в роли которого здесь выступает керамзит с гранулами не менее 5 мм. Примерная пропорция вышеперечисленных компонентов — 1:2:3. В состав керамзитобетона также входят особые воздухововлекающиедобавки типа омыленной древесной смолы СДО. Наиболее привлекательная для потребителей характеристика материала — малый вес керамзитобетона, который для разных марок последнего варьируется от 300 кг/м.куб. до 600 кг/м.куб.
Технология производства керамзитобетона
При производстве керамзитобетонных блоков важно соблюдать последовательность смешивания компонентов. Сначала в бункер закладывают 1 часть портландцемента М400, затем — 2 части сухого речного песка (можно воспользоваться готовым пескобетоном марки М300). После тщательного перемешивания вышеназванных компонентов в смесь с перемешиванием заливают 1 часть воды. Далее в технологическую емкость засыпают 3 весовых части керамзита и снова все перемешивают. Если масса получается недостаточно влажной (слишком сухой керамзит впитал всю воду), ее увлажняют до той степени, когда гранулы покроются цементной глазурью.
В случаях, когда полученный материал планируется использовать для формирования строительных блоков, переливать воду категорически нельзя! При изготовлении керамзитобетона для стяжки или наливного пола воды потребуется больше, а сама смесь должна обрести консистенцию «фасолевого супа». Формовка строительного керамзитобетона в виде блоков ведется в специальных формах кирпичного типа. В результате получают готовые геометрически правильные элементы массой 15-16 кг, пригодные для кладки на стандартный цементно-песчаный раствор. Период схватывания материала — 1-2 суток, а время его полного затвердевания с набором паспортной прочности — 28-30 дней.
Классификация товарного керамзитобетона
Согласно современной классификации, марки керамзитобетона разделяют по прочности (М) и плотности (D). Данные характеристики регулируются как пропорциями базовых компонентов материала, так и качеством таковых. Маркировка по прочности идентична маркировке цемента и выражается пределом прочности готового материала на сжатие либо в кг/см.кв. (по старому ГОСТу), либо в мегапаскалях (по новому стандарту): М100, М150, М300 или В7,5, В12,5, В22,5 соответственно.
Маркировка по плотности керамзитобетона определяет рекомендованное назначение конкретного изделия и представлена такими группами:
- до D700 — теплоизоляционный материал;
- D700-D1400 — керамзитобетон перегородочный;
- D1400-D2000 — стеновые керамзитобетонные блоки;
- облицовочный материал.
Первые две группы керамзитобетона производят с невысоким содержанием песка, в третьей песка и цемента больше. Облицовочные блоки имеют характерную лицевую сторону, обычно имитирующую фактуру природного камня.
Конструктивно керамзитобетонные элементы разделяются на полнотелые и пустотелые. Последние в свою очередь могут в объеме иметь от двух до восьми пустот.
Рабочие качества материала
Эксплуатационные минусы и плюсы керамзитобетона связаны с набором образующих его компонентов и технологической спецификой производства. К преимуществам материала перед кирпичом и бетоном относятся:
- высокая прочность при малом весе;
- низкая теплопроводность;
- минимальное водопоглощение;
- неподверженность появлению в объеме плесени и запотеванию;
- экологическая чистота исходных материалов;
- невысокая стоимость.
Возведение зданий из керамзитобетона проходит быстро и по затратам соизмеримо со строительством сборных деревянных домов. Керамзитобетонные блоки удачно взаимодействуют со всем распространенными отделочными материалами, а конструкции из них могут обходиться без массивных фундаментов, нуждающихся в дополнительном проектировании. Сквозные полости в блоках и наличие в номенклатуре производителей доборных элементов позволяют с минимумом затрат обеспечивать естественную вентиляцию строений.
Определенные минусы керамзитобетона как материала для капитальных сооружений не столь весомы, однако при планировании строительного процесса следует учитывать:
- более низкую относительно кирпича и монолитного бетона прочность;
- образование при кладке многочисленных мостиков холода, требующих дополнительной термоизоляции;
- малопрезентабельный внешний вид, что обязательно требует финишных отделочных работ.
Приобретая керамзитобетонные изделия, следует предварительно убедиться в авторитетности их производителя, ознакомиться с сертификатами качества и отзывами потребителей о конкретной продукции.
Запущено производство керамзитоблоков | Монолит-ДВ
Керамзитобетон представляет собой лёгкий бетон, в котором заполнителем является керамзит — ячеистый материал в виде гранул. Сырьём для производства керамзита служат суглинки и глина — экологически чистые материалы. По тепло- и звукоизоляционным свойствам, влаго- и химической стойкости он не только не уступает обычным и другим лёгким бетонам, но и превосходит их. Блоки из керамзитобетона называют «биоблоками», поскольку в качестве исходного сырья используются только экологически чистые природные компоненты. На основании этого керамзитобетон приобрёл заслуженное распространение, производство и применение которого развивается быстрыми темпами.
Изделия из керамзитобетона используются в качестве несущих конструкций в жилищном, гражданском и промышленном строительстве. Объёмный вес керамзитобетона высоких марок примерно в 2,5 раза меньше, чем тяжёлого бетона. Таким образом, применение керамзитобетона позволяет существенно снизить вес зданий и конструкций достигнув ряда положительных технико-экономических показателей. В климатических условиях России применение однослойных наружных стен из керамзитобетона даёт возможность эффективно использовать его тепло-физические свойства.
Керамзитобетон «дышит», регулируя влажность воздуха в помещении. Строения из керамзитобетонных блоков практически вечны и не требуют ухода. Материал не гниет, не горит и не ржавеет, обладая положительными свойствами дерева и камня одновременно.
Керамзитобетон имеет преимущества и перед кирпичом. Во-первых, удельный вес керамзитобетонных блоков из него в два с половиной раза ниже, чем у кирпичной кладки. Во-вторых, в вибропрессованных керамзитобетонных блоков заметно меньше цемента. В-третьих, один стандартный керамзитобетонный блок заменяет семь кирпичей. И, наконец, в четвертых, квалифицированный каменщик укладывает за смену из блоков объем стены в три раза больший, чем при кирпичной кладке.
И это притом, что по своим экологическим свойствам керамзитобетонные блоки не уступают кирпичу.
Опыт показал: использование керамзитобетонных блоков вместо кирпича на малоэтажном строительстве снижает себестоимость работ на 30-40%.
Керамзитобетон обладает хорошими теплоизоляционными свойствами. Различного рода испытания керамзитового гравия, являющегося заполнителем, проведенные специализированными научно-исследовательскими институтами, показали, что его использование позволяет сокращать потери тепла более чем на 75%!
Качественные керамзитобетонные блоки производят на основе керамзитового гравия мелких фракций — 5-10 мм. Блоки изготавливаются на современных вибропрессах, с последующей тепловой обработкой. Это позволяет достичь высокой прочности и хорошей теплоизоляции. У частных застройщиков блоки пользуются высоким спросом из-за оптимального соотношения цена/качество.
Благодаря хорошим прочностным характеристикам керамзитобетонных блоков, их применяют как в высотном домостроении, так и при строительстве коттеджей, частных домов, хозяйственных построек и гаражей. Опыт использования блоков показал, что для возведения малоэтажных зданий не требуется дополнительных специальных конструкторских решений. Благодаря точно выдержанным размерам керамзитобетонные блоки прекрасно сочетаются со всеми видами мелкоштучных строительных материалов, железобетонных изделий, металлоконструкций, дверных и оконных проёмов. Керамзитобетонные блоки «дышат», регулируя влажность воздуха в помещении. Строения из керамзитобетона практически вечны и не требуют ухода. Керамзитобетон из-за особенностей своей структуры обеспечивает значительное улучшение звукоизоляционных свойств возводимых конструкций по сравнению с обычными бетонами и кирпичом.
В монолитном железобетонном домостроении керамзитобетонные блоки используются при возведении межквартирных, межкомнатных перегородок.
В случае равных физико-механических характеристик с газосиликатом и пенобетоном керамзитобетонные блоки обладают лучшими показателями по паропроводности и гвоздимости.
Почему нужно выбрать керамзитобетонные блоки?
Уникальность свойств керамзитобетонных блоков основывается на специфике их производства. Основным ингредиентом для изготовления керамзитобетонных блоков является экологически чистый керамзит. Вспененная, прошедшая через процедуру обжига глина, из которой делается керамзит, по структуре похож на застывшую пену. Внешняя оболочка, что покрывает каждую глиняную гранулу, дает ей весьма высокую прочность.
Применение керамзитобетонных блоков не ограничивается какими бы то ни было технологическими рамками. Сегодня с их помощью возводятся несущие конструкции и лёгкие перегородки между комнатами, в монолитном домостроении применяют в роли стройматериала для заполнения каркаса.
Пожалуй, единственным на сегодня ограничением для использования керамзитобетонных блоков становится возведение фундамента, который требует повышенной плотности и прочности стройматериала.
Стены из керамзитобетонных блоков отличаются превосходнейшей прочностью. В них идеально прокладывается скрытая электропроводка. без особого труда можно штробить, легко можно забить гвозди.
В последние годы большинство строителей охотно переходят на применение прогрессивных керамзитобетонных блоков, поскольку на практике убедились в их технологичности, практичности, прочности и долговечной износостойкости. Отличающиеся легким весом керамзитобетонные блоки дают возможности выстраивать презентабельные и вместе с тем прочные здания даже на ленточных малозаглубленных, либо столбчатых фундаментах.
Керамзитобетонные блоки преимущества Вес керамзитного блока при его объёмности небольшой, начинается с 10 кг
К основным преимущественным качествам керамзитных блоков можно отнести:
керамзитобетонные блоки размеры :
размер керамзитобетонных блоков идеальны для скоростного монтажа. Каждый керамзитобетонный блок намного крупнее стандартного кирпича, что значительно облегчает и ускоряет процесс строительных работ, позволяет экономично использовать раствор при выполнении кладки. При возведении стен из керамзитобетонных блоков раствора нужно примерно в 2,2 раза меньше, а скорость монтажа бывает раз в 5 выше, масса же метра кладки бывает меньше в 1,5 раза;
керамзитобетонные блокои вес :
вес керамзитобетонного блока полнотелого стандартного размера 390 х 190 х 188 мм. примерно 24 кг., вес щелевого керамзитобетонного блока размером 390 х 190 х 188 мм. от 17 кг., вес перегородочного (толщина 90 мм.) полнотелого керамзитобетонного блока равен примерно 10 кг., а вес щелевой перегородки керамзитобетонного блока составляет 8-9 кг.. Столь малый вес керамзитобетонных блоков создаёт удобство во время транспортировки и при монтаже, что исключает необходимость в обустройстве дорогостоящего массивного фундамента;
керамзитные блоки паропроницаемость :
благодаря ей не образуется конденсационная влага и не наступает преждевременное старение как самих керамзитобетонных блоков, так и материалов отделки,
керамзитобетонные блоки огнеустойчивость:
характеристики керамзитобетонных блоков придают им хорошую сопротивляемость горению, которая обуславливает применение керамзитобетонных блоков как в частном, так и в индустриальном строительстве сооружений любой категории;
керамзитобетонные блоки морозостойкость:
морозостойкость керамзитобетонных блоков составляет 50 циклов последовательной шоковой проморозки и оттаивания, кроме того, стоит отметить сопротивляемость разного рода негативным атмосферным, а вместе с тем химическим воздействиям;
керамзитобетонные блоки теплоизоляционные свойства :
керамзитобетон, постепенно накапливая энергию солнца, тепло отдаёт медленно и равномерно, что защищает от перегрева летом и отлично сохраняет тепло в зимнее время, сделанные из него стены «дышат», поддерживая внутри помещения оптимальную влажность;
экологическая безопасность керамзитобетонного блока:
обоснована использованием исключительно чистого в экологическом плане натурального сырья;
замечательная шумоизоляция блока из керамзитобетона:
показатели изоляции керамзитобетона дают возможность обойтись без монтажа дополнительных систем утепления и защиты от извне поступающих звуков.
Керамзитобетонные блоки, характеристики заметно выигрывают по сравнению с качествами обыкновенного бетона:
При постройке стен из керамзитных блоков вам потребуется раза в два меньше раствора, нежели при строительстве кирпичных стен. Скорость же монтажа стен из керамзитобетонных блоков, наоборот, значительно больше — более чем в 4-ыре раза!
Как уже было замечено, керамзитобетонные блоки обладают замечательными теплоизоляционными свойствами. При применении керамзитобетона тепловые потери можно сократить более чем на семьдесят пять процентов. Доказательством этого служат множественные испытания в научно-исследовательских институтах, которые производились над блочным заполнителем — керамзитовым гранитом. В итоге, характеристики керамзитобетонных блоков в плане теплоизоляции обеспечивают им большую популярность в сравнении с иными строительными материалами, как при строительстве в теплых, так и в холодных условиях климата.
Одной из самых важных характеристик керамзитобетонных блоков стала его воздухопроницаемость, то есть керамзитобетонные блоки могут «дышать», тем самым регулируют в здании влажность воздуха.
Стройобъекты, возведённые из блоков керамзитобетонных, отличаются повышенной долговечностью и не нуждаются в специальном уходе. Керамзитобетонные блоки не склонны к появлению ржавчины, не горят и не гниют.
Качества керамзитобетонных блоков дают им ряд преимуществ и на фоне других видов стройматериалов, к примеру, кирпича:
Удельный вес керамзитных блоков ниже, чем вес кирпичей в два с половиной раза.
Всего за одну смену опытный каменщик может выложить из керамзитных блоков стену, которая в три раза превышает по объему кирпичную кладку.
Обычных размеров керамзитный блок может заменить семь стандартных одинарных кирпичей., и пять полуторных.
Стоимость керамзитобетонных блоков и себестоимость проведения строительных работ в сравнении с использованием стандартного кирпича ниже процентов на 30-40.
Почему при подборе оптимальных блоков из керамзитобетона предпочтение следует отдать компании Экоблок? Наша компания предлагает своим покупателям керамзитобетонные блоки высокого качества, производимые из лучших экологически чистых материалов. В результате характеристики керамзитобетонных блоков (звуко- и теплоизолирующие качества, вес керамзитных блоков, прочность и т.д.) соответствуют высокому качественному уровню, гарантируя долговечность и беспроблемность эксплуатации строений, при возведении которых будет использован данный материал. Кроме того, мы осуществляем не только продажу, но и доставку керамзитобетонных блоков любыми партиями по Волгограду и Волгоградской области.
Чтобы заказать керамзитобетонные блоки, свяжитесь с нами по телефону 8-904-772 46 97, либо отправьте заявку на наш электронный адрес Этот адрес электронной почты защищен от спам-ботов. У вас должен быть включен JavaScript для просмотра. Вы сможете задать все интересующие вас вопросы, получить консультацию по стоимости необходимого вам объёма керамзитобетонных блоков и их доставке, уточнить срок поставки блоков на объект, что, как правило, составляет не более 1 — 2 дней с момента принятия заказа. Мы работаем для вас без праздников и выходных, каждый клиент для нас дорог и может рассчитывать на индивидуальный подход.
плотность теплопроводность состав вес технические требования
Устойчивость, качество и долговечность любого здания полностью зависят от его фундамента – грамотности выбранного материала, а также соблюдения всех норм и технологий его возведения. Для фундамента необходимы прочные, надежные и износостойкие материалы.
Обычно для этих целей использовали бетонные смеси со щебнем, кирпич и железобетонные конструкции, однако в последнее время, а в странах Европы для возведения фундаментов применяют смеси, состоящие из керамзитобетона — щебня с фракциями 5-10, цемента, песка, пластификатора и воды. Их востребованность в современном строительстве связана с великолепным сочетанием низкой цены и отличных эксплуатационных свойств.
Особенности фундамента с использованием керамзитобетона
Керамзитобетонная смесь, которая применяется для возведения фундамента, имеет особый состав, который рассчитан на большую механическую нагрузку и качественную поддержку всего здания. Керамзит в разновидности «щебень» имеет пористую структуру, проявляет высокую стойкость к физическому воздействию.
Полученная смесь для фундамента будет обладать высокими теплоизоляционными свойствами, сохранять свою форму при воздействии перепадов температур. Именно поэтому можно быть уверенными в том, что фундамент останется в сохранности при любых эксплуатационных условиях – не будет промерзать, проседать и вызывать перекос всего строения на протяжении долгих лет.
Керамзитобетон в конструкциях
При возведении сооружений любого типа важную роль играет экологичность, экономичность, а также простота выполнения монтажных работ в возводимом здании. Всеми этими свойствами обладает современный материал — керамзитобетон. Кроме этого, керамзитобетонные дома строятся довольно быстро, не требуют дополнительных затрат на утеплители, транспортировку тяжелых стройматериалов.
Все дома, которые выполнены на основе бетона и керамзита, имеют легкий вес, а значит, их можно возводить в местах, где нет возможности строить массивные сооружения и здания, например, в болотистой местности. Отдельно стоит сказать о том, что при использовании керамзита можно снизить глубину закладки фундамента и, тем самым, сократить финансовые затраты. Применять такой материал целесообразнее при строительстве малоэтажных домов.
Помимо практичности возведение зданий из керамзитобетона будут еще и экономически выгодными. Керамзит, купить который на сегодняшний день можно практически во всех строительных магазинах, имеет доступную цену и отличные практичные свойства, поэтому он обязательно не только оправдает, но даже и превзойдет все ваши ожидания.
Технические требования к керамзитобетону, бетону
Для изготовления керамзитожелезобетонных изделий применяют несколько разновидностей керамзитобетона. Армированные слои, как правило, изготовляют из плотного керамзитобетона с расходом цемента не менее 200 кг/мг3. В этом случае нет необходимости принимать дополнительные меры по защите арматуры: от коррозии. При использовании малопесчаных, крупнопористых и поризованных керамзитобетонов арматура должна предварительно покрываться антикоррозийной обмазкой.
В зависимости от их назначения керамзитобетоны подразделяют на следующие три группы:
- а) конструктивные — для изготовления несущих керамзитожелезобетонных изделий, к которым требования по теплозащите не предъявляются,
- б) конструктивно-теплоизоляционные — для изготовления: элементов наружных ограждений,
- в) теплоизоляционные — для изготовления теплоизоляционных слоев.
Основные требования, предъявляемые к керамзитобетону в зависимости от его назначения, приведены в табл. 1.
К отдельным видам керамзитобетонов специального назначения могут предъявлять дополнительные требования (по водонепроницаемости, коррозионной стойкости и т. д.), которые указываются в проекте отдельно.
Марка керамзитобетона назначается по действующим нормам и техническим условиям. Соответствие фактической прочности бетона в изделиях заданной прочности определяется испытанием на сжатие контрольных бетонных кубов размером 20x20x20 см по ГОСТ 6901—61 «Методы определения удобоукладываемости бетонной смеси и прочности бетона». При испытании кубов другого размера переводные коэффициенты для плотных керамзитобетонов устанавливаются, как и для обычных бетонов, а для среднепористых и крупнопористых бетонов — по «Инструкции по приготовлению и применению крупнопористого бетона».
Табл.1. Основные требования, предъявляемые к керамзитобетону в зависимости от его назначения
При назначении марки керамзитобетона для изготовления железобетонных изделий следует учитывать следующие требования:
- а) работающие на изгиб тонкостенные железобетонные изделия с приведенной толщиной бетона до 100 мм и с обычной ненапряженной арматурой рекомендуется выполнять из керамзитобетона марки не ниже 150, а массивные изделия — марки не ниже 50;
- б) для изделий с предварительно напряженной стержневой арматурой марка керамзитобетона должна быть, как правило, не менее 200, при этом прочность бетона при сжатии к моменту передачи на него предварительного напряжения или при последующем натяжении арматуры должна быть не менее 140 кГ/см2;
- в) в изделиях, армированных горячекатаной арматурой периодического профиля с нормативным сопротивлением до 4000 кГ/см2 и диаметром до 20 мм, натягиваемой до напряжения не более 3500 кГ/см2, допускается применять керамзитобетон марки 150, при этом прочность бетона при его обжатии должна быть не менее 120 кГ/см2;
- г) керамзитобетон марки менее 35 (например, 10, 15, 25) может применяться лишь в многослойных железобетонных конструкциях в сочетании с более прочным бетоном.
Величина отпускной прочности бетона устанавливается техническими условиями на каждый вид изделия в зависимости от назначения его и времени года и не может быть менее 70% проектной прочности. При этом во всех случаях отпускная прочность конструктивно-теплоизоляционного бетона при сжатии должна быть не менее 25 кГ/см2, а конструктивного — 50 кГ/см2.
Требуемый объемный вес керамзитобетона (в сухом состоянии или при заданной влажности) и морозостойкость устанавливается проектом и определяется по ГОСТ «Материалы стеновые и облицовочные. Методы определения объемного веса и удельного веса».
Бетон или раствор для изготовления облицовочных слоев должен удовлетворять требованиям проекта и иметь плотное строение. Прочность фактурного слоя бетона или раствора может быть выше прочности основного керамзитобетона не больше чем в 1,5 раза. Образцы из бетона или раствора для наружных фактурных слоев должны, как правило, выдерживать не менее 25 циклов замораживания и оттаивания (если проектом не предусматривается большее число циклов замораживания и оттаивания) .
(PDF) Керамзитобетон легкий и опилкобетон на суперсульфатном цементе
279
Легкий керамзитобетон и опилкобетон на основе
СУПЕРСУЛЬФИРОВАННЫЙ ЦЕМЕНТ
Дворкин Л.1, Лушникова Н.3, Лушникова Н.1*, ,4
1 Кафедра технологии строительных изделий и материаловедения, Национальный университет
Водоснабжение и экологическая инженерия, ул. Соборная, г. Ровно, 33028, Украина
2 Школа естественной и искусственной среды, здание Дэвида Кейра, Королевский университет Белфаста , Белфаст BT9
5AG, Северная Ирландия (Великобритания)
3 Инженерный факультет Бейрутского арабского университета, П.O. Box: 11 5020 Бейрут, Ливан
4 Факультет науки и техники, Университет Вулверхэмптона, Вулверхэмптон, WV1 1LY, Великобритания
* Автор, ответственный за переписку; e-mail: nvlushnikova@nuwm.edu.ua
Реферат
Рассмотрены особенности свойств двух видов легкого бетона
: керамзитобетона (легкого керамзитобетона — LECA) и опилкобетона. (древесина
стружка), содержащие бетон.Первый основан на LECA производства Западной Украины и
Молдова, для второго применены опилки обычных местных хвойных деревьев. В исследованиях использовался суперсульфатный цемент
, состоящий из доменного гранулированного шлака, фосфорно-гипсового
и портландцемента. Хлористый кальций использовали для уменьшения замедления схватывания, а суперпластификатор
— для снижения водопотребления с целью повышения прочности на сжатие.
Высокая удельная поверхность суперсульфатированного цемента способствует интенсивной гидратации СаО из шлакового
стекла и связыванию его в новообразования.Это увеличивает прочность легкого бетона.
С керамзитом процесс происходит со связыванием свободной извести и гипса с алюминатами из шлака
и заполнителя. Результаты, полученные с керамзитобетоном, варьировались в диапазоне
средней плотности от 960 до 1490 кг/м3 и прочности на сжатие от 7 до 21,5 МПа. Такой бетон
может применяться для конструктивных и теплоизоляционных элементов (блоки стеновые и панели
).Для опилкобетона средние плотности варьировались от 410 до 720 кг/м3 и прочность на сжатие
от 0,34 до 4,7 МПа, что может быть использовано для конструкционных и неконструкционных элементов
. Так как суперсульфатированный цемент имел низкий рабочий рН из-за ограниченного содержания щелочи, это
приводило к положительному влиянию на заполнитель опилок и не приводило к значительному извлечению
дубильных веществ.
Ключевые слова:
Древесная стружка, ЛЕКА (легкий керамзит), керамзит, суперсульфатный цемент
(ССК), легкий бетон
энергоэффективный экологически чистый бесклинкерный цемент
[Juenger 2011, Ding 2014].Его основными компонентами являются
побочные химические и промышленные продукты фосфогипс
(ФГ) и доменный шлак с добавлением сульфата
и щелочного активатора в небольшом относительном количестве.
Обычно соотношение компонентов соответствует
: 70-90 % гранулированного доменного шлака
(GBFS), 10-20 % компонента сульфата кальция и
до 5 % щелочного активатора [Stark 2000 , Hewlett
2004, Юнгер 2011].
Согласно опубликованным результатам [Midgley 1971, Stark
2000, Hewlett 2004, Matschei, 2005], гидратированный SSC
состоит преимущественно из кристаллов эттрингита и игольчатых или пластинчатых низкоосновных гидросиликатов кальция
3,
3, гидроталькит (Mg6Al2(CO3)(OH)16·4(h3O), незначительные фазы AFm наряду с присутствием безводного шлака и
гипса.
Предыдущее исследование было посвящено определению влияния низкоглиноземистых доменный шлак
и обезвоженный фосфогипс на свойства
SSC [Дворкин 2012].
Для производства легких бетонов на основе цемента
применяются различные заполнители [Sonebi et al., 2013].
Серия исследований доказала влияние нескольких основных факторов
на прочность легкого бетона: водоцементного отношения
, прочности заполнителя, пористости межфазной зоны
и внутри затвердевшего цементного теста [Lo 2007].
АВС в производстве строительных материалов
Весьма перспективно использование АВС в производстве различных строительных материалов, таких как наномодифицированный бетон, мелкодисперсный цемент, особопрочный силикатный кирпич и др.
Устройство вихревого слоя, или АВС-100, прошло испытания на различных промышленных объектах. Практика показывает, что АВС эффективно заменяет такие устройства, как шаровые, вибрационные, молотковые мельницы, различные измельчители и диспергаторы. Установки АВС используются в качестве реакторов, смесителей и т.п.
Применение в производстве керамзита
Керамзит.
В процессе производства керамзита глину гомогенизируют и измельчают в смесителях, вальцовых мельницах и т.п.Однако эти устройства не обеспечивают качественного измельчения, отсюда низкая прочность керамзита. Из-за отсутствия измельчения и гомогенизации даже 3% углеродистых включений в хорошо вспененной низкоплавкой глине делают ее непригодной, образующийся керамзит теряет прочность или распадается при хранении из-за гидратации СаО.
Наше решение проблемы — Vortex Layer Deivce.
Перепесчаная глина с содержанием свободного SiO2 до 10-30% также малопригодна для производства керамзита. Все эти проблемы во многом решаются за счет обработки сырья в вихревом слое.Измельчение и гомогенизация шихты для производства керамзита общего и специального назначения в АВС привели к значительному снижению объемной массы и увеличению прочности (см. Таблицу ниже)
Таблица 1
Результаты измельчения и гомогенизации шихты в АВС для производства керамзита
Опыт № Продолжительность обработки сырья и АВС Механические свойства керамзита Обработка шихты в АВС Шихта смешанная без АВС Объемная масса, γ, г/см3 Прочность на сдвиг σs*10-5, Па Отношение прочности к весу Объемный вес, γ, г/см3 Прочность на сдвиг τс*10-5, Па Отношение прочности к весу 1 Глина с 26 % свободного SiO2 (30-секундная обработка шликера) 0,24 2,25 10,3 0,38 1,60 5,1 2 То же с содержанием свободного SiO2 41 % (30-секундная обработка бланка) 0,34 2,45 7,8 0,84 3,24 4,1 3 Монотермит (7-минутная сухая обработка) 0,85 29,4 36 1,6 9,81 6,5 4 Глина 50%, угольный пепел 50% (7 минут сухой обработки) 0,57 10,7 18 0,58 1,32 8,4 5 То же с опудриванием сырья каолином (7-минутная сухая обработка) 0,74 27,9 32,0
Переработка глинистого шлама из глины, содержащей до 40 % двуокиси кремния, привела к двукратному уменьшению массы керамзита с одновременным увеличением прочности (удельная прочность керамзита, обработанного АВС, почти в два раза выше, чем у обычной шихты).
Резкое улучшение свойств керамзита – это, очевидно, активация кварцевого песка за счет образования активных центров – свободных радикалов, образующихся при разрыве силоксановой связи Si–O аналогично диспергированию SiO2 в дезинтеграторах при высоких оборотах ротора.
Активация SiO2 заставляет диоксид кремния активно участвовать в образовании силикатов и стекла. После обжига керамзита в гранулах отсутствуют крупные частицы SiO2 (точки напряжений). Присутствие SiO2 в стекле повышает прочность и термостойкость.
Сухая обработка сырья в вихревом слое достаточно эффективна. Так, в результате монотермитной обработки был получен легкий огнеупорный наполнитель с вдвое меньшим удельным весом и в три раза большей прочностью по сравнению с контрольными образцами (опыт 3, табл. 1). Это было достигнуто сухой обработкой многокомпонентной шихты с содержанием в вихревом слое до 50 % огарков тепловых установок (опыты 4 и 5).
На примерах показано, что применение АВС весьма перспективно для получения керамзита из перепескоструенного материала с высоким содержанием углерода, для получения керамзита повышенной прочности и термостойкости, высококачественных наполнителей из шихты с отходом до 50%, таких как угольная зола.
Производство пенобетона
Пенобетон получают путем схватывания смеси вяжущего, воды и кремнеземистого заполнителя, вспененной пенообразователем. Наиболее часто используемым пенообразователем является алюминиевая пудра, выделяющая водород при реакции водного раствора гидроксида натрия.
Известно, что качество пенобетона повышается с уменьшением размера пор и повышением однородности. Для этого алюминиевый порошок должен быть равномерно распределен в смеси.Кроме того, структура пенобетона определяется таким фактором, как наличие в смеси активного СаО.
Обычно приготовление пенообразователя заключается лишь в удалении парафиновой пленки с частиц алюминия путем смешивания их с водой и поверхностно-активными веществами и последующего перемешивания суспензии с полученной смесью. Из-за низкой эффективности перемешивающих устройств парафиновую пленку очень трудно удалить. Кроме того, частицы алюминия коагулируют, что приводит к концентрированному газовыделению в смеси, кавернам и трещинам.
Из-за недостаточного газовыделения при производстве газосиликата смесь необходимо сочетать с известью до 25 %. Необходимость дополнительной извести диктуется также требованием получения за счет гидратации достаточной прочности бетона для сохранения его пенообразования. Использование АВС при приготовлении алюминиевых суспензий в производстве газосиликата позволяет полностью исключить коагуляцию частиц алюминия, повышая их активность, газовыделение и гомогенность. Некоторые сравнительные данные по физико-химическим свойствам газосиликата, полученного из алюминиевой суспензии, приготовленной различными способами, приведены в таблице 2.
Таблица 2
Физико-механические свойства газосиликата, полученного с использованием алюминиевой суспензии, полученной различными способами
Опыт № Условия приготовления суспензии Производительность АВС-100, л/час Механические свойства газосиликата АВС обработка Обработка миксера Удельный вес, γ, г/см3 Прочность на сдвиг σs*10-5, Па Отношение прочности к весу Удельный вес, γ, г/см3 Прочность на сдвиг τс*10-5, Па Отношение прочности к весу 1 Алюминиевая пудра — 100% от расчетного количества 120 385 377
414
18,7 10,3
11,8
2,56 1,47
1,41
396 419
438
15,2 79,5
10,8
2,03
0,92
1,14
2 То же – 90% расчетной суммы 950 386 427
375
14,5 15,2
12,3
1,85 1,70
1,80
437 —
—
14,1 —
—
1,51
—
—
Из таблицы видно, что при использовании алюминиевой суспензии, обработанной АВС, был получен газосиликат с прочностью на 10-30% выше и отношением прочности к массе на 20-60% выше, чем у контрольного образца (таблица 2, эксперимент1).
Использование АВС позволило снизить расход пенообразователя на 10%, расход извести на 2%, не утяжеляя продукт. Наоборот, удельный вес уменьшился, а отношение прочности к весу увеличилось. По-видимому, качество пенобетона можно повысить путем обработки известково-песчаной или цементно-песчаной смеси в вихревом слое для активации SiO2 по аналогии с процессом при производстве керамзита.
Производство силексного кирпича
Силекс-кирпич
Сырьем для производства силикатного кирпича являются кварцевый песок (92-95% сухой смеси) и известь (5-8%).Прочность кирпича напрямую связана с активацией SiO2 и равномерным распределением компонентов. Это делает АВС очень перспективным для обработки сухой смеси для активации компонентов. Для этого через вихревой слой установки АВС-100 просеивали известково-песчаную смесь. Интересно, что такая кратковременная обработка (частицы смеси проходили через вихревой слой за доли секунды) не приводила к измельчению песка и извести.
О степени активации можно судить по изменению механических свойств кирпича, изготовленного из этой смеси.
Условия обработки АВС Прочность на сжатие
σs*10-5, Па Без обработки 91,2 Однократное просеивание через слой 239,5 Два просеивания 324,5 Три просеивания 328,1
Как видно из данных, кратковременная обработка смеси увеличивает прочность силексного кирпича в 3 раза.5 раз.
По-видимому, подобная обработка песчано-известковых, известково-зольных и известково-кремнеземных смесей приведет к столь же значительному улучшению механических свойств широко применяемых в строительстве силикатных бетонов.
Большие перспективы производства керамзитобетона в Беларуси
Новолукомль, 18 сентября.
/Корр. БЕЛТА/. Целесообразно создание в Беларуси новых предприятий по выпуску керамзитобетонных блоков. Об этом корреспонденту БЕЛТА сообщил директор Новолукомльского керамзитобетонного завода «Керамзит Новолукомль» Михаил Лазарашвили.
Руководитель сказал: «В прошлом году мы ввели в эксплуатацию ультрасовременный цех по производству керамзитобетонных блоков. Выработка на одного работника в этом отделе составляет 400 000 долларов. Мы показали, что можем и должны делать керамзит. Создание таких предприятий по всей Беларуси — следующий шаг, который необходимо сделать».
По его словам, новые мощности по производству керамзитобетонных блоков могут быть созданы на базе действующих предприятий промышленности строительных материалов, которые знают бетон наизнанку и имеют соответствующие лаборатории.«Наши специалисты могут проконсультировать их в покупке необходимого оборудования и организации производственного процесса. Кроме того, мы готовы предоставить керамзит для таких производств», — заверил Михаил Лазарашвили.
На вопрос, чем лучше создавать новые производства в регионах и доставлять туда керамзит, чем поставлять предприятиям готовые блоки, директор отметил, что с точки зрения логистики выгоднее перевозить исходные материалы.«Поскольку стоимость перевозки зависит от веса в тоннах, керамзит выгоднее перевозить, потому что он очень легкий», — заявил Михаил Лазарашвили.
Новолукомльский керамзитобетонный завод «Керамзит Новолукомль» также следит за внешними рынками. «До недавнего времени ни одно предприятие в бывшем СССР не производило керамзитобетонные блоки. Не так давно в Санкт-Петербурге открылся завод. Они используют наш керамзит», — отметил он. По словам Михаила Лазарашвили, экспорт керамзита, используемого для производства керамзитобетонных блоков, ежегодно увеличивается на 30-50%.
Новолукомльский завод керамзитобетонного щебня «Керамзит Новолукомль» — один из крупнейших производителей керамзита в Европе. Предприятие входит в систему предприятий Министерства архитектуры и строительства Республики Беларусь.
Предприятие неоднократно удостаивалось наград за лучший строительный продукт года.
ТОП-5 крупнейших покупателей бетонных блоков в 🇧🇩 Бангладеш
Показать все
Трейдинг
Производство
Товар бетонный блок оптом
Торгово-скупочная компания
Вы хотите найти новых клиентов, покупающих бетонные блоки оптом
Тома Констракшн и Ко.ООО
Бетонные блоки и плательщики
N.n Международный
Машина для производства бетонных блоков с гидравлическим приводом e:cee-1060 с тарельчатым смесителем: грузоподъемность 50 0 кг с мотор-редуктором 10 л.с., 1440 об/мин (API)
Бдпл Срипур Нестле Бангладеш Лтд.
Осветительный разрядник со стандартными аксессуарами: бетонный блок с пластиковой опорой (8,5 кг) № по каталогу Dehn 102060 (API)
Акий Группа
Бетонные блоки и брусчатка
Производство кирпича в Бангладеш Владелец
120 кг добавки для бетонных блоков
Елена Еременко
менеджер по логистике в ЕС, Азию
логистика, сертификат
электронная почта: [email protected]
Крупнейшие производители и экспортеры бетонных блоков
Компания (размер) Продукт Страна 1.
🇰🇷 Samjung Carryworld Co., Ltd. (10) СТАЛЬНОЙ ПОДДОН ДЛЯ МАШИНЫ ДЛЯ ИЗГОТОВЛЕНИЯ БЕТОННЫХ БЛОКОВ СТАЛЬНОЙ ПОДДОН ДЛЯ МАШИНЫ ДЛЯ ИЗГОТОВЛЕНИЯ БЕТОННЫХ БЛОКОВ Южная Корея 2. 🇮🇹 Refrattari Generali Srl (6) БЕТОННЫЕ БЛОКИ TERMIX Италия 3. 🇨🇳 Linyi Baoma Steel Sales Co., Ltd. (6) МАШИНА ДЛЯ ПРОИЗВОДСТВА БЕТОННЫХ БЛОКОВ BM БЕТОНЕМЕСИТЕЛЬ JD Китай 4. 🇮🇹 Penta Automazioni Industriali Srl (4) УСТАНОВКА ДЛЯ РАСКОЛКИ И ДРОБЛЕНИЯ БЛОКОВ ДЛЯ ПЕРЕРАБОТКИ БЕТОННЫХ ИЗДЕЛИЙ РАСКОЛКА И ДРОБЛКА P Италия 5.🇲🇽 Aircrete Mexico Sapi De Cv (4) BLOCK DE CONCRETO CELULAR AUTO CLAVEADO DE X X MM АВТОРАСТЯЖЕННЫЙ ЯЧЕБЕТОННЫЙ БЛОК X X MM CO Мексика
БЕТОННЫЙ БЛОК оптовая цена в Бангладеш
9016 / кг
90-100 кг
Продукт Product бетонный блок цена за кг, MT вес $ 58.
4 / кг $ 58.4 / кг 10-100 кг Нерегулирующие соединения для фасадных поверхностей 3 доллара.5 за Kg 100 — 1.000 кг Нерегульники Соединения для фасадных поверхностей $ 1.2 / кг 1,000 — 10.000 кг Сухие смеси $ 222 за MT выше 10MT Лигносульфонат технический порошок ТУ 2455-028-00279580-2014. В качестве сырья для 2,1 $/кг 10-100 кг Технологическая добавка «Полипласт Лигно» (ТУ 2455-082-58042865- 2015) Смесь натриевых солей лигносульфокислот (с введением редуцирующих и минеральных веществ) $7.2 в кг 100 — 1.000 кг Добавка технологическая «Полипласт Лигно» (ТУ 2455-082-58042865-2015) представляет собой смесь натриевых солей лигносульфокислот (с введением редуцирующих и минеральных веществ) 9017 $3 0 1.
000 — 10.000 кг Аэрированные бетонные блоки $ 0,1 на кг 100 — 1.000 кг Настенный газовый блок — это строительный газобетонный блок из сотового бетона, нерешенных $ 0.1 / кг 1.000 — 10.000 кг Силикатный строительный кирпич $ 9.7 / кг 10-100 кг цементные строительные блоки и кирпича $ 0.5 за Kg 100 — 1.000 кг Однослойный бетонный кирпич с известковым наполнителем, неармированный Удельная плотность продукта от 1 0,1 $ / кг 1.000 — 10.000 кг Встроенные кухонные мойки в комплекте со сливными частями 0 $ 8.2 / кг 10-100 кг Искусственные каменные кухонные раковины $ 6 на KG 100 — 1.000 кг бетонные продукты $ 1.
8 / кг 1.000 — 10.000 кг
бетонный блок Склад
- Склад в Дакке
- Бетонный блок в Читтагонге
- Склад Кхулна
- Раджшахи Бангладеш
- Склад Комилла Бангладеш
Просмотрите эту статью:
Лицо: Марина Анисон 11 января 2022 г.
Образование: Technische Universität Berlin
© Copyright 2016 — 2022 «Экспорт из России».Все права защищены.
Сайт не является публичной офертой. Вся информация на сайте носит ознакомительный характер. Все тексты, изображения и товарные знаки на этом веб-сайте являются интеллектуальной собственностью их соответствующих владельцев. Мы не являемся дистрибьютором бренда или компаний, представленных на сайте, Политика конфиденциальности
Типоразмер керамзитоблоков по ГОСТ
Керамзитобетон — современный строительный материал, относящийся к легким бетонам. Выпускает блоки и другие элементы, которые используются для возведения внутренних и наружных стен домов и инженерных сооружений различного назначения.
Применяется также для заполнения монолитных каркасов в качестве теплоизоляционного материала.
Состав и производство
Керамзитовые блоки получают путем смешения керамзита, портландцемента, песка и воды методом полусухого вибропрессования. Иногда при необходимости добавляют разрешенные пластификаторы. В зависимости от места применения состав может меняться: для повышения теплоизоляционных свойств может уменьшаться количество песка и цемента, при этом увеличивается объем керамзита, уменьшая вес изделий и вес готового объекта.При этом повышаются показатели тепло- и звукоизоляции.
Керамзит — специально обработанная обожженная глина, имеющая вид пористых овальных камешков. В зависимости от способа производства они могут иметь угловатую форму, такой материал называют керамзитовым гравием. Для производства блоков используется наполнитель фракцией 5-10 мм.
Так как глина натуральный дешевый материал, дом из таких блоков будет экологически безопасным, а общая стоимость материалов будет ниже, чем при покупке более традиционных и распространенных строительных камней (гипсобетон, пенобетон).
Классификация
Так как состав, размер керамзитоблоков и характеристики могут быть различными, они делятся на несколько групп на несколько групп:
1. По назначению:
- Конструктивные. Самые тяжелые и прочные блоки. Применяются для возведения самостоятельных несущих элементов зданий, мостов, путепроводов. Удельный вес таких блоков от 1400 до 1800 кг/м 3.
- Конструкционная и тепловая изоляция участвует в возведении стен, преимущественно однослойных стен.Удельный вес блоков от 600 до 1400 кг/м 3.
- Теплоизоляция применяется в качестве утеплителя различных конструкций. Самые легкие элементы с наименьшим содержанием цемента и песка. Удельный вес 350-600 кг/м 3 .
2. По области применения:
- Стен. Для внутренней и внешней прокладки разные степени ответственности.
- Перегородки для разделения межкомнатного и в некоторых случаях межквартирного пространства.
3.
По форме. Все блоки-параллелепипеды различаются только степенью заполнения:
4. По порядку кладки:
Стандарты
По свойствам и техническим показателям керамзитобетонные блоки должны соответствовать требованиям, установленным в ГОСТ 6133-99 «Бетонные стеновые камни». В документе перечислены различные параметры контроля качества, марки, сырье для их производства, правила транспортировки и хранения. ГОСТ
указывает конкретные размеры газоблока, пеноблока, керамзитоблока:
Также в документе указываются допустимые отклонения от основных размеров:
Общие параметры
Размеры керамзитоблока ГОСТ четко определены, для наглядности, Мы упрощаем и переведу их в обычную форму, и мы получаем следующую таблицу:
7079
390х190х188
288x288x138
288x138x138
290х190х188
190h290h288
90х190х188
размер, мм
стены
Разметка
590х90х188
390h90h288
190h90h288
в соответствии с этими значениями, вы всегда можете рассчитать количество материалов, необходимых для строительства.
Эти цифры относятся к блокам из всех видов бетона.
Типоразмер керамзитоблока может быть изменен по индивидуальным пожеланиям на этапе производства для конкретной партии или всей линейки продукции. Затем продавец должен указать, что товар изготовлен согласно спецификации и имеет персональные, отличные от принятых размеры.
В стандарте прописан не только размер керамзитовых блоков, но и основная форма камней — параллелепипед.Элемент может иметь плоские торцы, а также свайно-пазовые соединения.
Форма камней (многогранники, полукруги и т.п.) может быть изменена для возведения архитектурных элементов сооружений.
Технические характеристики
Обратите внимание, что размер блоков керамзита не влияет на характеристики.
1. С точки зрения прочности, глиняные блоки различаются в зависимости от области применения:
9
100-500
Назначение
Индикатор, кг / см 2
Теплоизоляция
5-35
Структурные и теплоизоляция
35-100
Конструктор
2.
Массовая вес:
Назначение
350-600
350-600
Структурная и теплоизоляция
600-1400
Конструктивные
1400-1800
3. Теплопроводность керамзитобетонных блоков в диапазоне 3.14-0,66 Вт/(м*К). Показатель зависит от количества песка и цемента в составе камня – чем их меньше, тем выше способность блока удерживать тепло. Полые элементы имеют самый высокий показатель, конструкция из них будет самой теплой.
4. Морозостойкость зависит от тяжести блока – чем больше вес, тем большее количество циклов выдерживает материал.
Структурные и теплоизоляция
Назначение
15-50
150160
150
Конструктивный
500
5.
Водопоглощение для стандартного керамзитоблока – до 10%. Показатель можно уменьшить, добавляя в состав специальные пластифицирующие добавки и улучшители.
6. Паропроницаемость увеличивается с пористостью — 0,3-0,9 мг/(м*ч*Па). Соответственно, легкие изоляционные блоки прекрасно пропускают влагу.
7. Звукоизоляция зависит от степени пористости блока. При толщине перегородки 90 мм обеспечивается защита до 50 дБ.
8. Огнеупорность.Керамзитобетон способен выдержать 180 минут. при температуре выдержки 1050 0 С.
9. Усадка соответствует величине 0,3-0,5 мм/м.
10. Допустимый строительный номер 12.
Применение
Блоки из керамзитобетона универсальны – их используют для возведения различных частей зданий и инженерных сооружений. Для фундамента выпускаются массивные элементы, выдерживающие значительные нагрузки, корпус дополнительно армируется.Для стен есть как самостоятельные, так и утепляющие блоки. Отличие заключается в конструкции и составе: элементы несущих и несущих конструкций имеют больший вес и плотность, а теплоизоляционные более пористые и легкие.
Перегородки из керамзитобетона хорошо изолируют звук в помещениях. Такие подойдут в дома и помещения различного назначения. Размер барьерного керамзитоблока позволяет быстро собрать стену с минимальными трудозатратами.
Преимущества перед другими материалами
+ Выпускаемые керамзитоблоки, размеры которых стандартизированы, удобны в укладке: их пористая структура позволяет раствору проникать в тело камня, обеспечивая тем самым надежную перевязку кладки.
+ Стены, возводимые из пустотелых блоков, легко армируются: в сквозные отверстия вставляется усиливающая конструкцию арматура, образуя каркас. Особенно это актуально для многоэтажного строительства.
+ Размер керамзитоблоков позволяет сэкономить на количестве раствора для кладки, а также снижает трудозатраты на возведение конструкций.
+ Легкие элементы не требуют прочного фундамента для основания.
+ Возможность сэкономить без использования дополнительного утепления.
+ «Дышащие» стены позволяют поддерживать в помещении оптимальный микроклимат без образования конденсата.
+ Керамзитобетонная поверхность может быть отделана различными строительными материалами, а ее структура обеспечит надежное сцепление слоев.
+ Прочные камни выдерживают различные подвесные предметы (шкафы, полки, технику).
+ Минимальная усадка почти не отображается на отделке и целостности конструкций.
недостатки
- По сравнению с тяжелым бетоном керамзит менее прочен, поэтому его применение для фундаментов возможно только при малоэтажном строительстве и тщательном расчете.
- При строительстве высотных зданий требуются блоки повышенной плотности, что увеличивает нагрузку на фундамент и требует более мощной конструкции, что может увеличить стоимость проекта.
- Бывает, что размеры керамзитоблока неидеальны из-за его структуры, необходимо особенно тщательно производить упаковку. Но если отклонения в пределах, допускаемых ГОСТом, проблем нет.
Особенности применения и выбора
Если при выборе стройматериала для дома вы остановились на керамзитобетоне, необходимо учитывать некоторые нюансы:
- Чтобы не создавать дополнительное утепление, его необходимо устроить стену толщиной не менее 40 мм.
Тогда жить в доме будет комфортно, а микроклимат всегда оптимален. - Кладка должна производиться путем тщательного измерения толщины швов. Не должно быть никаких выступов или выступов.
- Для дома из керамзитоблоков подойдет ленточный фундамент, если нет цокольного помещения. После того, как он осядет, можно приступать к строительству стен.
Размер керамзитоблока стандарт определяет четко, а потому, если проект у вас рассчитан на такие параметры, будьте внимательны при покупке материала: производитель обязательно указывает размеры по ГОСТу или ТУ.Они могут быть разными.
р>
Керамзитобетон: пропорции для приготовления
Керамзит
имеет широкое распространение в строительстве благодаря надежности формируемых из него конструкций. Строительные формы и конструкции могут простоять десятки лет, не теряя физических и эстетических характеристик. Состав цементного раствора и керамзита относится к легкой группе бетонов. В состав керамзитобетона входит крупный заполнитель из керамзита, мелкозернистый песок и цемент в качестве вяжущего компонента.
Кроме цемента для скрепления можно использовать гипс. Рассмотрим подробно, что представляет собой керамзитобетон, пропорции для смесей разной плотности, область применения и характеристики строительного материала.
Свойства и характеристики материала
Визуально керамзитобетон имеет пористую структуру, размер пор зависит от режима обжига основного заполнителя. Различают три степени пористости бетона: крупнопористый, пористый и плотный. На эксплуатационные характеристики конструкций и конструкций значительное влияние оказывает однородность бетонной структуры.
Нормативная прочность керамзитобетона определяется долей керамзитобетона мелкой и крупной фракций. Применение керамзитобетона в качестве основного элемента строительных опалубок требует дополнительного армирования, для повышения прочности конструкций монтаж железобетонных элементов сопровождается креплением арматуры. Основная роль керамзитобетона заключается в формировании защитного теплоизоляционного слоя в многослойных конструкциях.
Прочность и физические характеристики керамзитобетона зависят от соотношения компонентов.Следует учитывать, что пропорции керамзитобетона для пола и пропорции смеси для строительных блоков разные.
Керамзитобетон: пропорции и состав раствора
В качестве перекрытий при возведении зданийДавно используются железобетонные плиты, на сегодняшний день эта технология не актуальна. Железобетонные перекрытия имеют существенный недостаток – низкую теплоизоляцию. Материал, способный успешно выдерживать нагрузки и при этом обеспечивать комфортные условия пребывания в помещении, – керамзитобетон, который используется в виде стяжки.
При укладке стяжки нужно обратить внимание на тип поверхности, от которого зависит ее состав. Оптимальные пропорции керамзитобетона для стяжки: при высоте 30 мм на 1 м2 требуется 40 кг смеси песчаника М300 и 35 кг керамзитобетона.
Клейдитовый бетон: пропорции для стяжки, в зависимости от расчетного значения плотности на 1 м3
плотность расширенного Claydite цемент Sand вода кг / м3 кг кг кг кг кг L 0
700 720 900 — 250 — 140 1500 700 — 0,8 430 420 — — — 700 900 7000
— 0,72 400 640 — 6 1600 600 — 0,68 430 680 — 1700 700 — 60 19 30 130 830 — — 1700 600 — — 0,56 410 880 — —
Для приготовления бетонной смеси в контейнере SuitableThe загружается с керамзит, а затем заливают водой (небольшим количеством).
После растворения пористой структуры гранул в емкость загружают вяжущие компоненты – цемент и пескобетон. Все перемешивается строительным миксером до густой консистенции. Замешивание раствора прекращается после того, как керамзит приобретет цвет цемента.
Преимущества и недостатки стяжки из керамзитобетона
Часто керамзитобетонную стяжку применяют при необходимости повышения уровня пола в помещении. Образованная поверхность обладает высокой прочностью, устойчива к влаге, не пропускает воздух.Преимущества стяжки из керамзитобетона:
- стоимость зависит от площади и толщины покрытия;
- доступная технология монтажа и длительный срок службы;
- возможность корректировки плоскости, устранение качания и неровностей;
- абсолютная совместимость со всеми типами напольных покрытий;
- высокая степень влагостойкости и огнестойкости, звукоизоляция;
- устойчивость к биологическому и химическому воздействию;
- в таком процессе, как приготовление керамзитобетона, пропорции регулируют плотность;
- экологическая чистота.

Стяжка из керамзитобетона имеет недостатки:
- укладка сопровождается значительным подъемом уровня пола;
- После высыхания требуется шлифовка поверхности.
Наличие технологии производства блоков
При возведении небольших жилых или хозяйственных построек на даче или в саду хозяева часто отдают предпочтение строительным блокам из керамзита. Они также используются для строительства домов, возводимых в районах с низкой несущей способностью грунта.Причина выбора – высокие характеристики материала и доступная технология производства блоков. Их можно изготовить самостоятельно на приусадебном участке без использования технологического оборудования.
Формование блоков керамзитовых
Блоки керамзитовые бывают двух видов: пустотелые и полнотелые. Независимо от формы блоков, фундамент – керамзитобетонный. Блоки, форма которых не имеет пустот, используются для кладки фундаментов и облицовки наружных стен.Пустотелые блоки широко используются в качестве звукоизоляционного и теплоизоляционного ограждающего слоя внутренних стен здания.
За счет использования пористых блоков, несущих характеристики фундамента и стен здания. Однако главное преимущество применения керамзитобетона в строительстве определяется экономичностью возводимых конструкций. За счет пористости структуры достигается снижение затрат на сырье и малый вес элементов конструкции.
Керамзит: состав и пропорции смеси для формовки блоков
Керамзитовые блоки в своем составе содержат керамзит, цемент, мелкий песок и другие добавки. Другими словами, смесь содержит вяжущие вещества и керамзит. В качестве добавок, повышающих физические свойства строительных блоков, для повышения устойчивости к низким температурам может использоваться омыленная древесная смола (СДС). Для повышения степени связывания добавляют порошок лигносульфоната технического (ЛСТП).
Приготовление раствора
Вяжущей основой смеси для формирования фактурного слоя является шлакоцемент (ШПЦ) или цемент марки М400 (портландцемент). Следует учитывать, что марка цемента не может быть меньше М400.
Далее добавляют керамзит и мелкий песок.
Производим керамзитобетон своими руками,Соотношение смешивания: 1 (цемент), 8 (керамзитовый гравий) и 3 (песок). Этот состав придаст оптимальные характеристики будущему строительному материалу.Для производства керамзитобетона пропорции на 1м3 должны быть следующими: 230-250 литров воды. Для придания пластичности бетону можно воспользоваться народным методом: в процессе смешивания компонентов добавить чайную ложку моющего средства.
Смешивание всех компонентов необходимо производить в бетономешалке, последовательность действий следующая: сыпучие компоненты загружаются и перемешиваются в барабане, затем постепенно добавляется вода до получения однородной массы, напоминающей по консистенции глину.
Формовка блоков и завершающий этап
Устанавливается место для лепки блоковПоддон, на который ставится опалубка.Во время сушки блоков недопустимо прямое воздействие влаги и прямых солнечных лучей, для этого устанавливается навес.
Перед заливкой раствора внутренние стенки форм смазывают машинным маслом, а основание посыпают песком. Существуют стандартные размеры блоков из керамзитобетона: 190×190×140 и 390×190×140 мм. Следует придерживаться стандартных размеров, но для небольшой дачной постройки размеры можно изменить по своему усмотрению.
После завершения всех подготовительных этапов формы заполняются раствором. Смесь уплотняют для устранения пустот до появления цементного молочка. Поверхности блоков выравниваются мастерком. Формы разбираются через 24 часа с момента укладки раствора, сами блоки до полного застывания не сдвигаются.
Период высыхания длится до 25-28 дней в зависимости от климатических факторов. Процесс сушки не должен искусственно стимулироваться и проходить в короткие сроки, быстрая потеря влаги может вызвать растрескивание и потерю прочности блоков.
Блоки из керамзитобетона, изготовленные в домашних условиях, при соблюдении всех вышеперечисленных правил не уступают блокам, изготовленным в условиях промышленно-технологического участка.
р>
Столбчатый фундамент из блоков своими руками. Устройство столбчатого фундамента из блоков 20х20х40
Выбор разновидности фундамента будет зависеть не только от особенностей будущего здания, но и от характеристик грунта, которые следует знать до начала строительства.Для экономичных и других строений с незначительным весом наиболее выгодными и подходящими считаются столбчатые фундаменты.
Создавать их можно из самых разных материалов, причем технология может отличаться, но общая черта в том, что основание будет состоять из опор, заглубленных до необходимого уровня. Столбы можно выкладывать из блоков, которые отливают из железобетона. Иногда опоры делают из металлических труб.
Важно помнить
Столбчатый фундамент из блоков 20х20х40 см не предусматривает наличие подвала.Если для будущего владельца важен этот критерий, то стоит обратить внимание и на другие виды оснований. В качестве наиболее подходящей глубины фундамента выступает 1 м, если условия строительства требуют более внушительной глубины, имеет смысл рассмотреть возможность устройства фундамента из асбестоцементных труб, залитых бетоном.
Ведь укладка блоков ФБС на глубину более 1 м – очень трудоемкий процесс. Более внушительная глубина может быть продиктована некоторыми условиями строительства по типу массива дома или типу грунта.
Когда следует отказаться от столбчатого фундамента из блоков ФБС
В некоторых ситуациях необходимо отказаться от столбчатого фундамента, где будут использоваться блоки ФБС. Такие ограничения выражаются при строительстве массивных зданий, стены которых выполнены из тяжелых материалов, таких как железобетонные стеновые блоки или кирпич. Не используйте такой фундамент на тех грунтах, которые имеют менее внушительную несущую способность, среди них:
- просадочные;
- глинистый;
- водонасыщенный.
Подвижные грунты также не подходят для такого основания, т. к. они обладают низким сопротивлением нагрузкам горизонтального смещения. Если на территории есть естественные перепады высот более 1 м, то требуется заранее выровнять землю.
Область применения
Сборный фундамент из блоков своими руками возводится частными мастерами.
Эти основания имеют ограничения по эксплуатации и потенциалу. Их можно возводить на слабощебнистых грунтах или грунтах, не склонных к пучению.После возведения фундамента можно построить панельный дом, как правило, одноэтажный.
Если вы затеяли строительство в регионе, где имеются крупные обломочные, плотные скальные или песчаные грунты, то несущей способности фундамента из ФБС будет достаточно для возведения полноценного дома из пенобетона, бруса или каркаса. Отлично подходят для такого строительства валунные, гравийные и галечные грунты.
Выбор блоков
Перед изготовлением столбчатого фундамента из блоков необходимо подобрать материал.Для этой цели подходят изделия с маркировкой ФБС, технология изготовления которых должна регламентироваться ГОСТами 13579-58. Ознакомившись с нормами, можно понять, что для производственного процесса используют бетон марки М-100 и выше, а также сетку, размер которой достаточно широкий.
Если перед вами стоит вопрос, как правильно сделать столбчатый фундамент из блоков, то вам следует узнать, что железобетонные конструкции бывают достаточно крупногабаритными.
Их укладывают краном, ведь вес может достигать 2 тонн. Такие блоки армируются арматурным каркасом из горячекатаной арматуры марки А3. Диаметр стержней будет зависеть от размера блоков и варьируется от 9 до 15 мм. Если речь идет о крупногабаритных блоках, то их можно использовать для ленточных и плитных оснований, на которые впоследствии будут устанавливаться массивные кирпичные конструкции.
Крупногабаритные блоки в частном мелкосерийном строительстве используются довольно редко, так как их вес не позволяет выполнять ручную кладку, для этого приходится арендовать строительный кран, что нивелирует преимущества основания и дешевизны.Для ручной кладки лучше использовать ПБС, основу которого составляет керамзитобетон. Такие изделия отличаются незначительным весом, а также термостабильными характеристиками. Довольно часто устройство столбчатого фундамента из блоков 20х20х40 см осуществляется по той причине, что эти изделия самые ходовые, а их вес составляет 32 кг.
Технические характеристики блоков ФБС размерами 20х20х40 см
ФБС отлично подходят для создания столбчатых фундаментов, имеют номинальную прочность 150 кг/см 2 .
Морозостойкость достаточно высокая и составляет 15 циклов, а способность впитывать влагу достигает 15% от общего объема. Теплопроводность изделий составляет 1,16 Вт/мК. Если вы думаете о том, как построить столбчатый фундамент из блоков 20х20х40 см, вам следует учитывать преимущества использования таких изделий, они заключаются в высокой скорости работы, а также возможности использования специального клеевого состава или цементно-песчаный раствор.
При этом все работы можно выполнить самостоятельно, не прибегая к помощи строительной техники.Однако у этих изделий есть и недостатки, они выражаются в низкой гидрофобности, так как керамзитобетонные блоки имеют пористую структуру, вследствие чего впитывают влагу из почвы, как губка. В долгосрочной перспективе это может привести к разрушению блока.
Особенности столбчатого фундамента из блоков
Столбчатый фундамент из блоков подходит для зданий на основе деревянного каркаса. При этом не приходится укладывать бетон, что иногда играет решающую роль.
Профнастил также не требуется, поэтому не нужно привозить на участок большое количество щебня, это касается и других строительных материалов. Подготовить нужно будет только бетонные блоки, рекомендуемый размер которых 20х20х40 см. Эта технология позволяет сэкономить на строительстве и актуальна в тех случаях, когда нет возможности подвести электричество к площадке для бетономешалки.
Консультация специалиста
Если необходимо построить сауну, гараж или хозяйственную постройку, а проект ограничен как в плане реализации, так и в финансовых возможностях, лучшим решением будет столбчатый фундамент.Он подойдет для любой другой малогабаритной постройки, к тому же строительство будет завершено в кратчайшие сроки. Можно использовать не только блоки, но и кирпичи, деревянные столбы и асбестоцементные трубы. Такие основания обладают высокой несущей способностью и долговечностью. Возможно использование ФБС, которые представлены на рынке железобетонными или керамзитобетонными изделиями заводского производства.
Они изготавливаются методом вибропрессования и отлично подходят для этой цели.
Подготовительные работы
Если вы решили возводить столбчатый фундамент из блоков, то сначала нужно подготовить площадку, для этого ее выравнивают, очищают от мусора и снимают верхний слой грунта. Его толщина может достигать предела от 25 до 30 см, все будет зависеть от уклона участка.
Как только место будет готово, можно переходить к разметке, для этого в углах будущей конструкции устанавливаются колышки, измеряются диагонали, это позволит убедиться в точности установки углов.Колышки должны располагаться в местах пересечения стен, соединение кольев осуществляется по линии прохода стен с помощью шпагата.
Земляной
Столбовой фундамент из блоков требует колодцев для установки столбов. Для этого лучше использовать ручную дрель, выходя на нужный уровень. Расширить яму можно лопатой. При использовании бетонных блоков вышеуказанных размеров размеры скважины должны быть следующими: 50 х 50 см.
Глубина будет зависеть от климата, в котором ведется строительство.
Важно учитывать глубину промерзания грунта. Если в вашем регионе 50 см, то необходимо углубить скважину на 90 см. После того, как колодцы сформированы по всем углам, необходимо выкопать колодцы в местах пересечения стен. Затем следует расположить канавки под будущие стены, расстояние между ямами должно быть 2 м. Если вы решили возводить столбчатый фундамент из блоков, то на следующем этапе можно переходить к формированию столбов.
Работы на опорах
На дно каждой ямы насыпается щебень, который будет служить дренажным слоем. Это особенно важно при сезонных перепадах температур. Как только подготовка завершена, из раствора можно сделать подушку, на которую устанавливаются первые блоки. Следующие два нужно уложить сверху, расположив их перпендикулярно. Чем меньше вы сделаете шов между камнями, тем надежнее будет основание.
Столбы должны быть подняты так, чтобы над поверхностью земли они возвышались на 30 см и более.

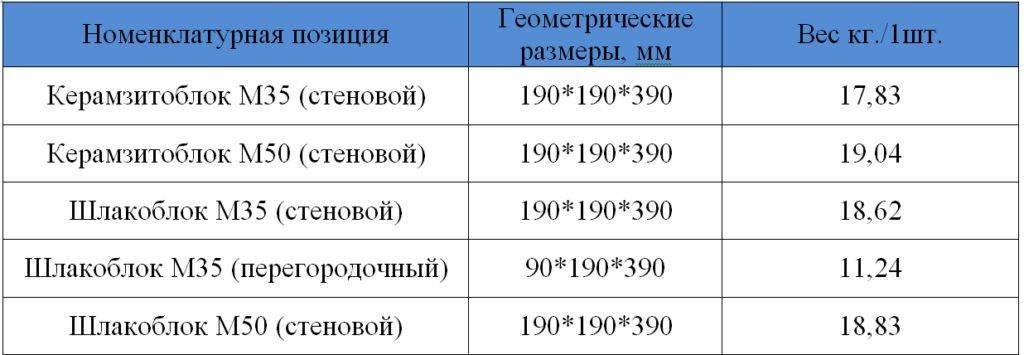



377
414
10,3
11,8
1,47
1,41
419
438
79,5
10,8
2,03
0,92
1,14
427
375
15,2
12,3
1,70
1,80
—
—
—
—
1,51
—
—


σs*10-5, Па
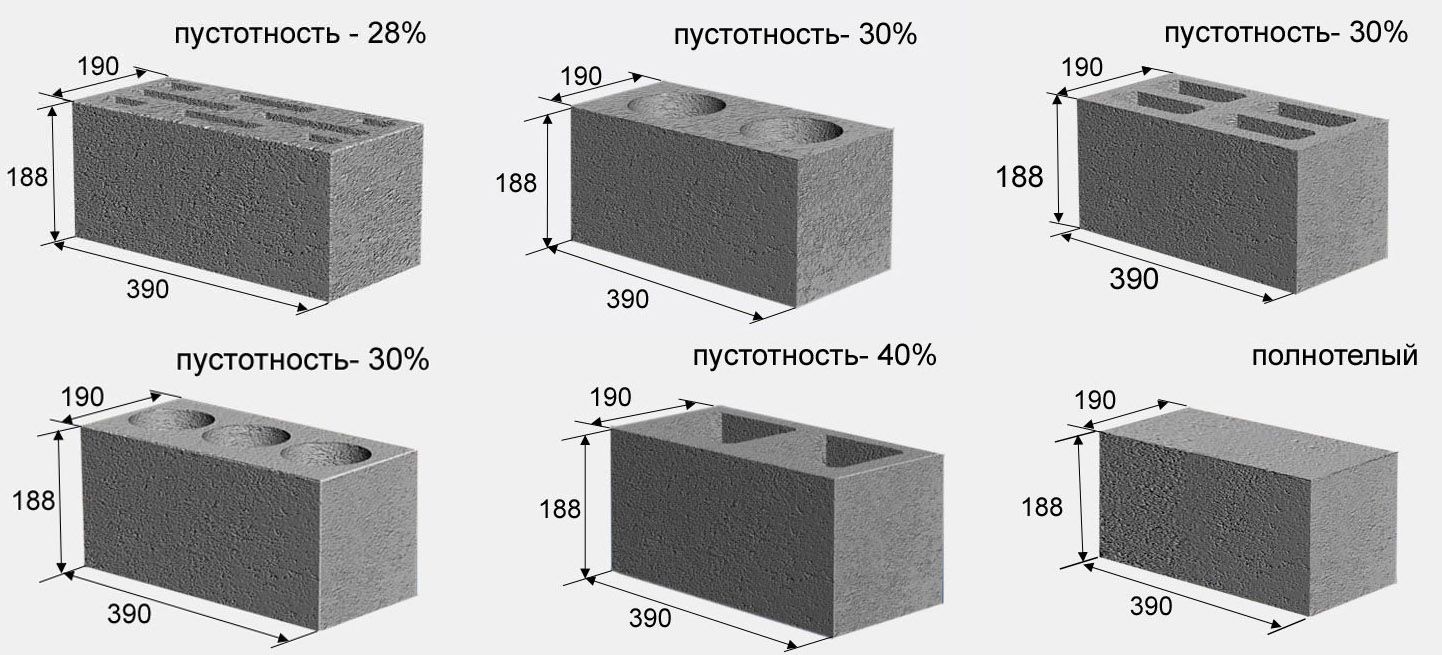


Трейдинг
Производство
Тома Констракшн и Ко.ООО
Бетонные блоки и плательщики
N.n Международный
Машина для производства бетонных блоков с гидравлическим приводом e:cee-1060 с тарельчатым смесителем: грузоподъемность 50 0 кг с мотор-редуктором 10 л.с., 1440 об/мин (API)
Бдпл Срипур Нестле Бангладеш Лтд.
Осветительный разрядник со стандартными аксессуарами: бетонный блок с пластиковой опорой (8,5 кг) № по каталогу Dehn 102060 (API)
Акий Группа
Бетонные блоки и брусчатка
Производство кирпича в Бангладеш Владелец
120 кг добавки для бетонных блоков
менеджер по логистике в ЕС, Азию
электронная почта: [email protected]

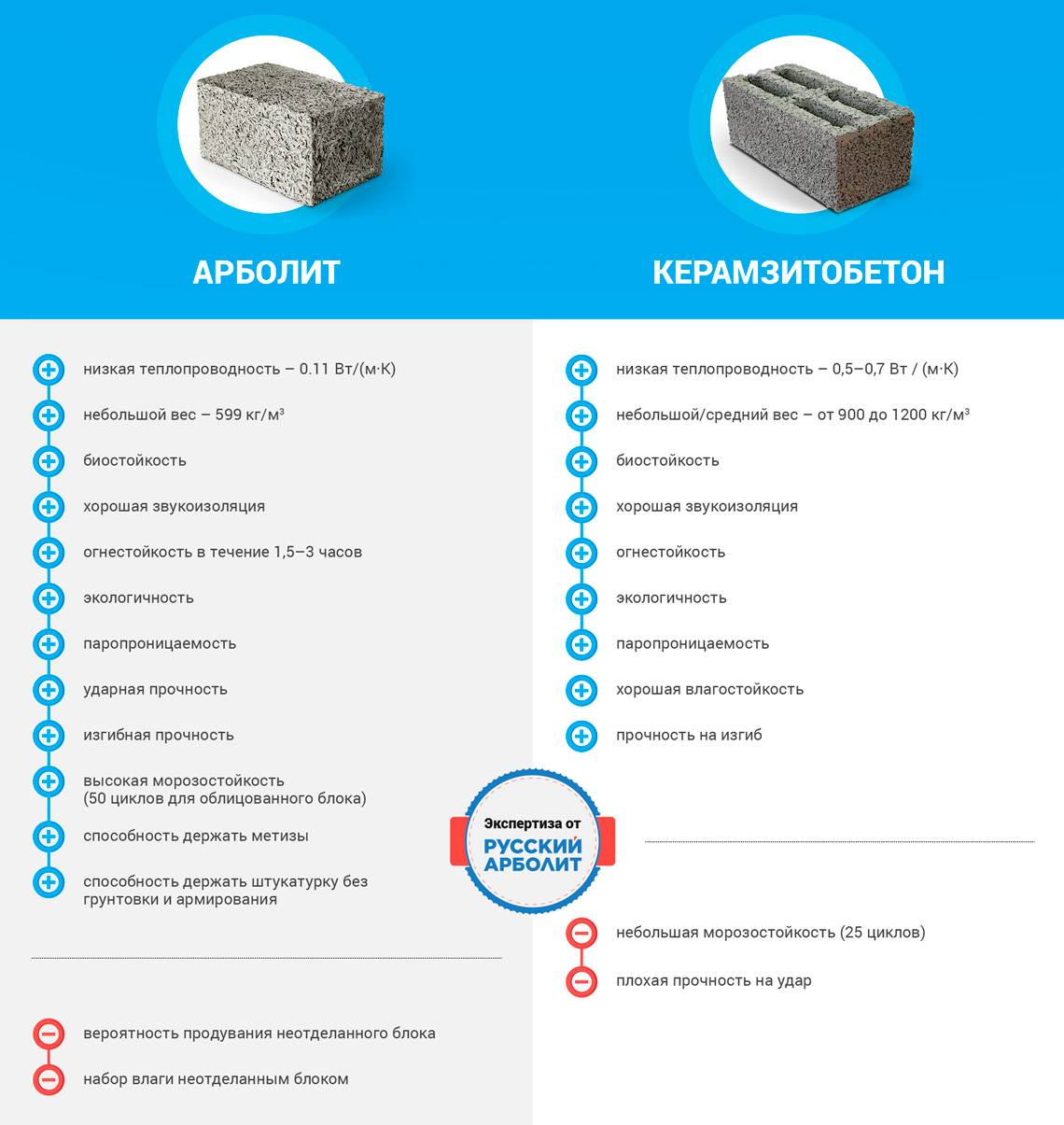

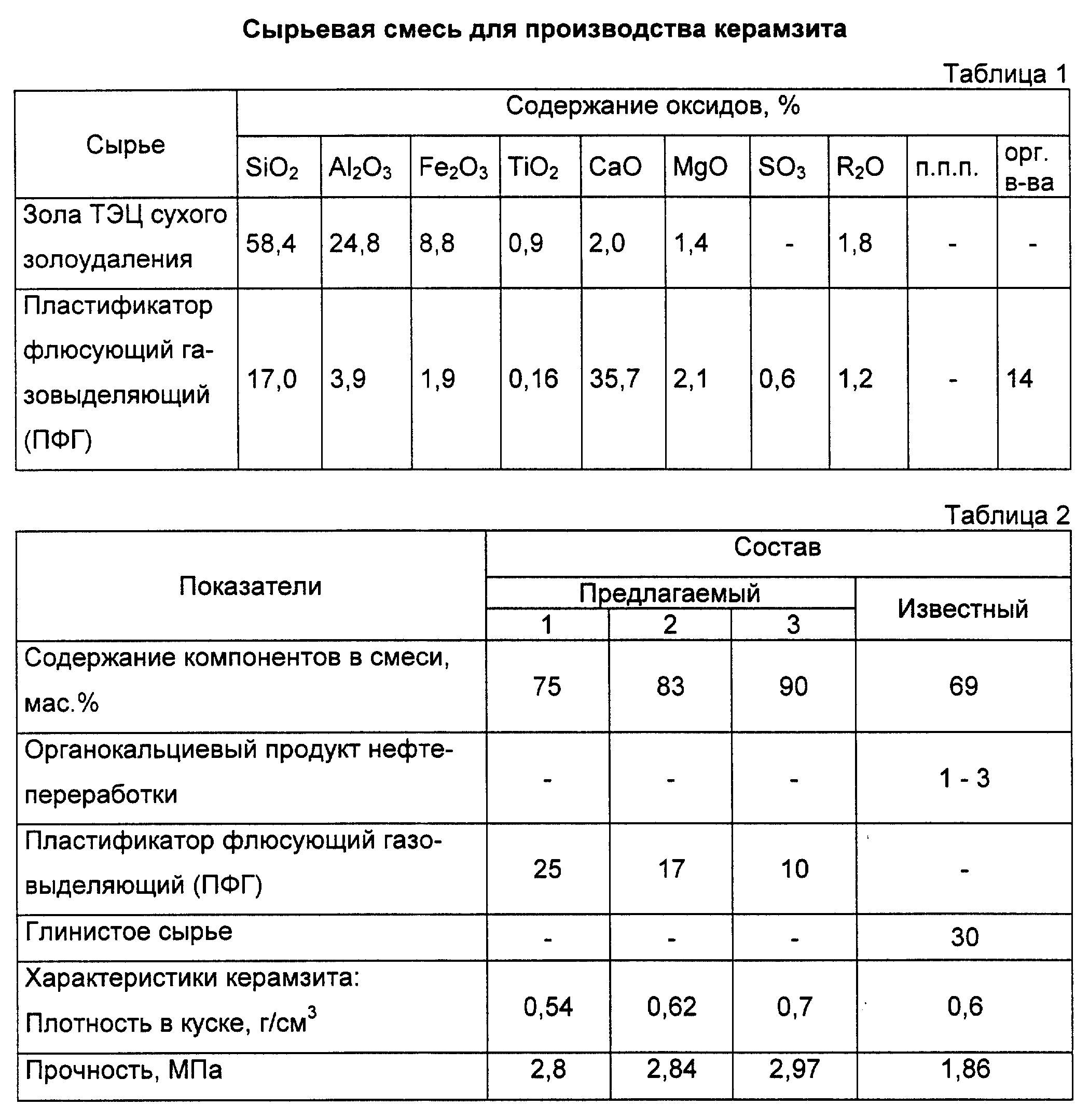
Образование: Technische Universität Berlin
Сайт не является публичной офертой. Вся информация на сайте носит ознакомительный характер. Все тексты, изображения и товарные знаки на этом веб-сайте являются интеллектуальной собственностью их соответствующих владельцев. Мы не являемся дистрибьютором бренда или компаний, представленных на сайте, Политика конфиденциальности



размер, мм
стены
Разметка
590х90х188
390h90h288
190h90h288
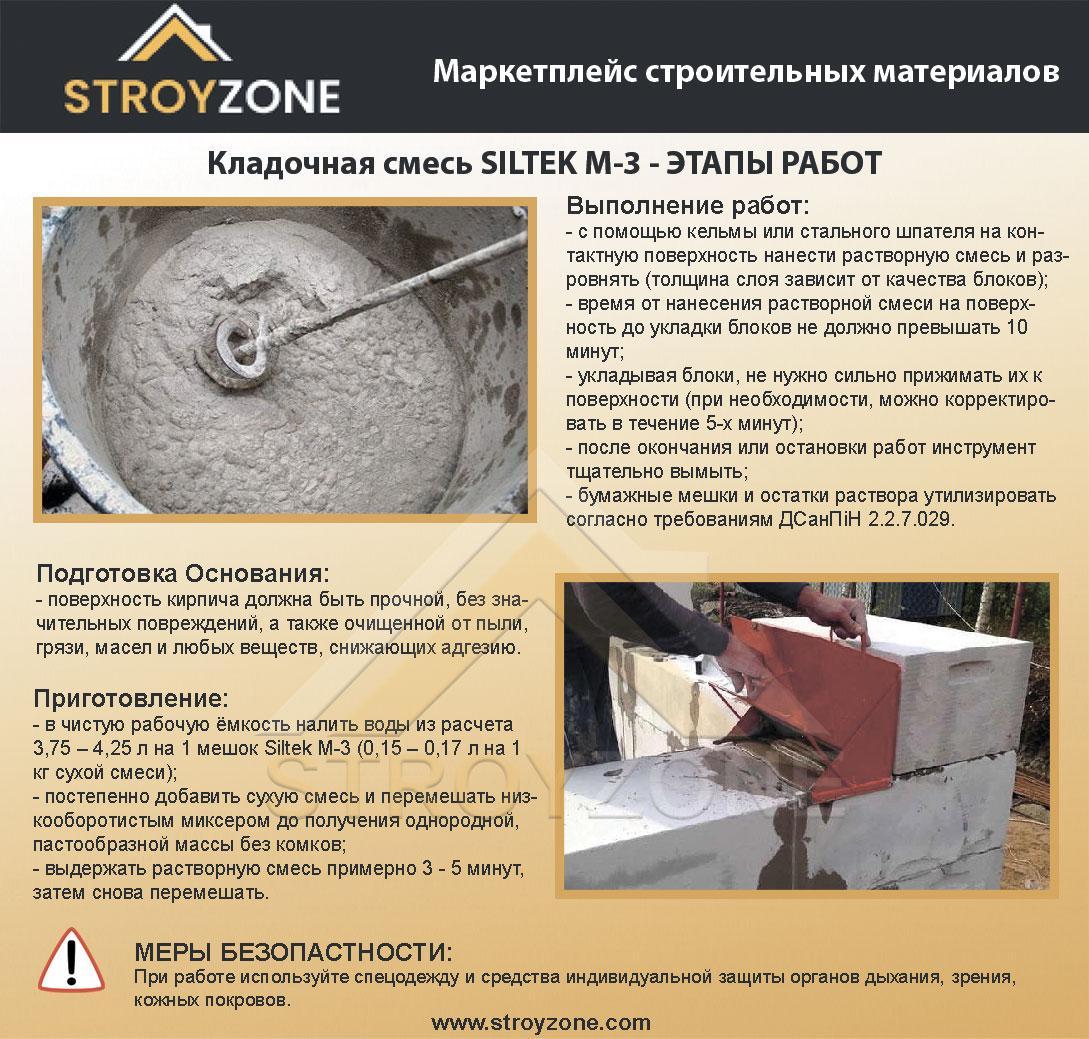
Назначение
Индикатор, кг / см 2
Теплоизоляция
5-35
Структурные и теплоизоляция
35-100
Конструктор

Назначение
350-600
350-600
Структурная и теплоизоляция
600-1400
Конструктивные
1400-1800
Назначение
15-50
150160
150
Конструктивный
500

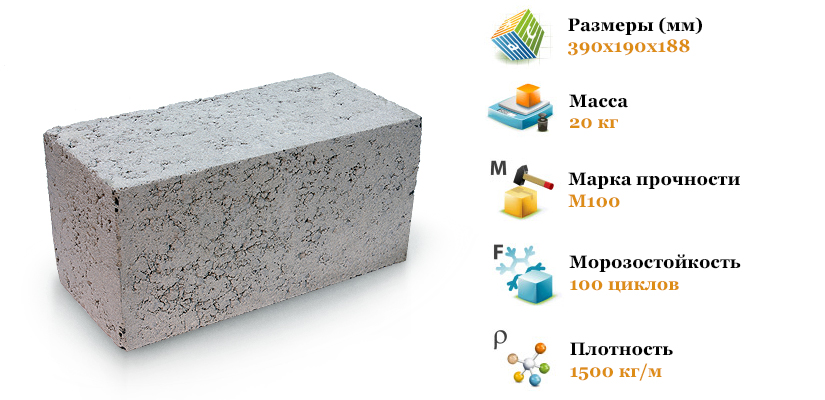
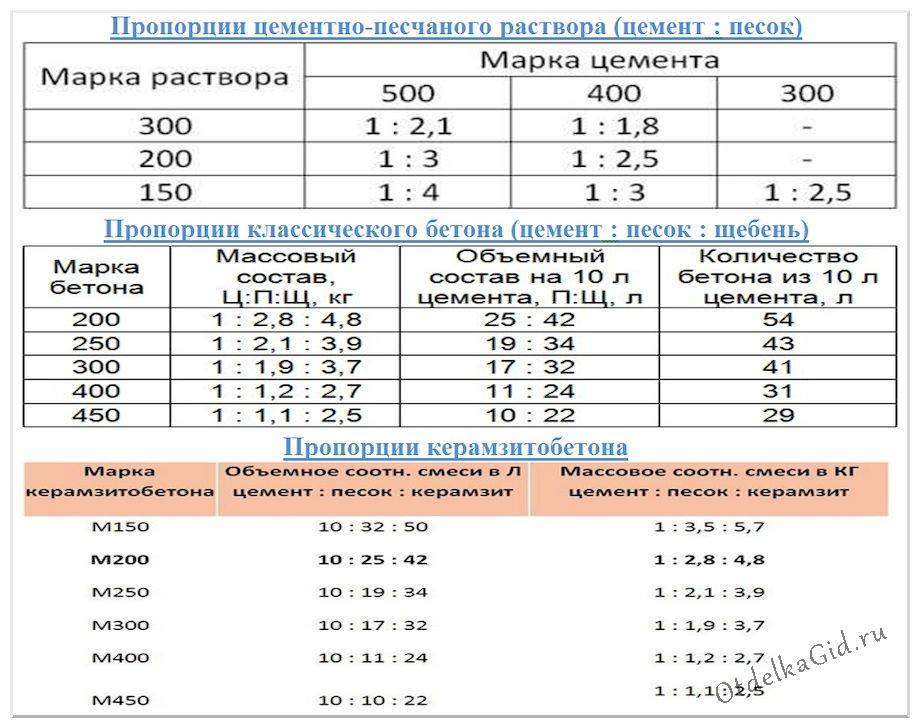

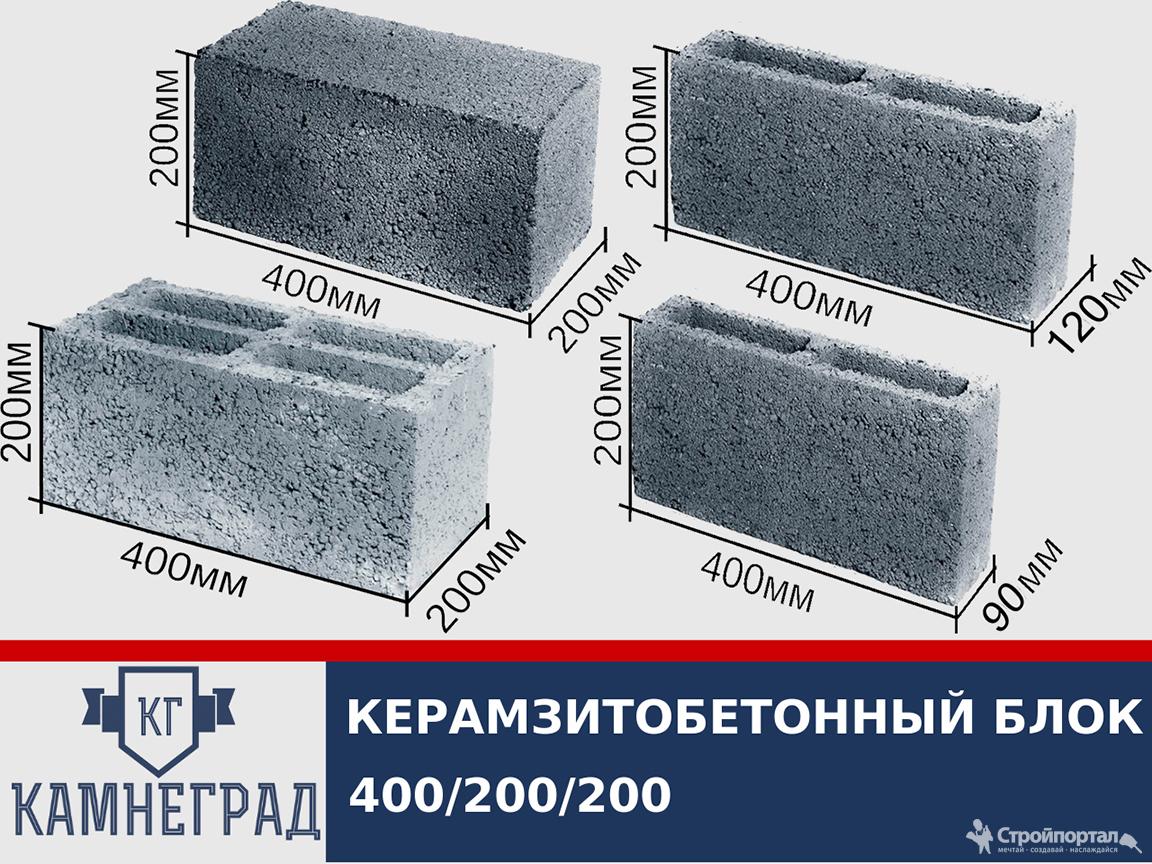

0
0


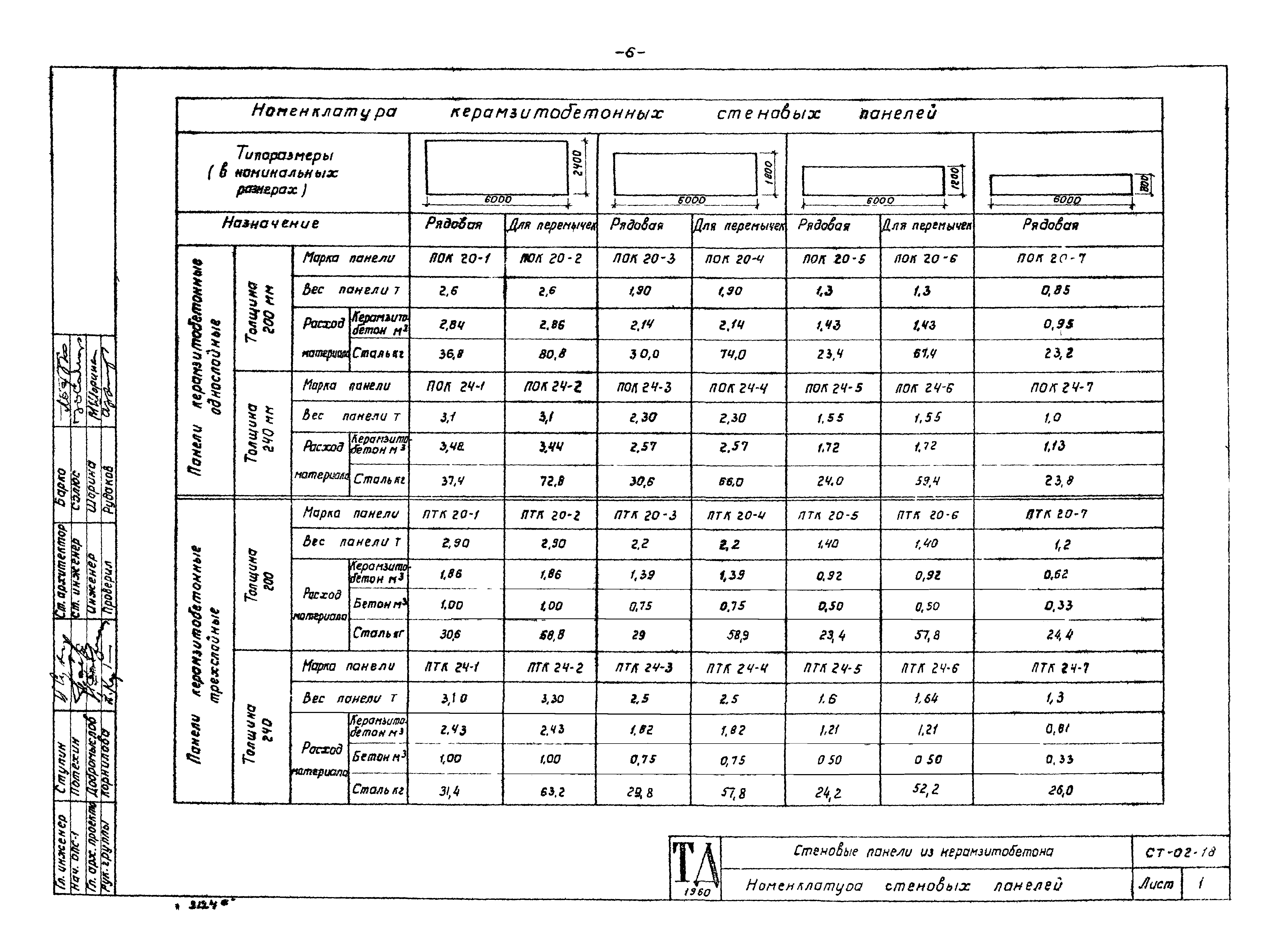
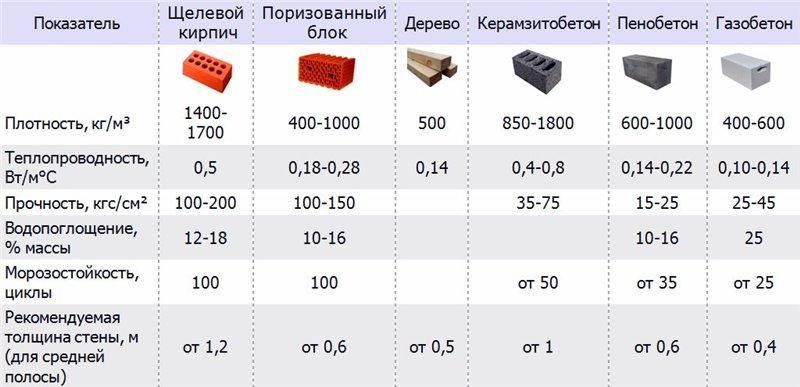
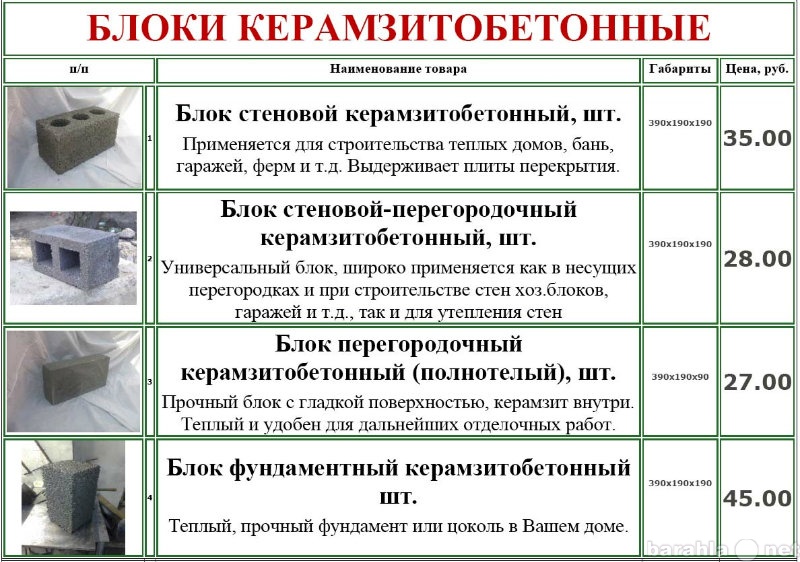

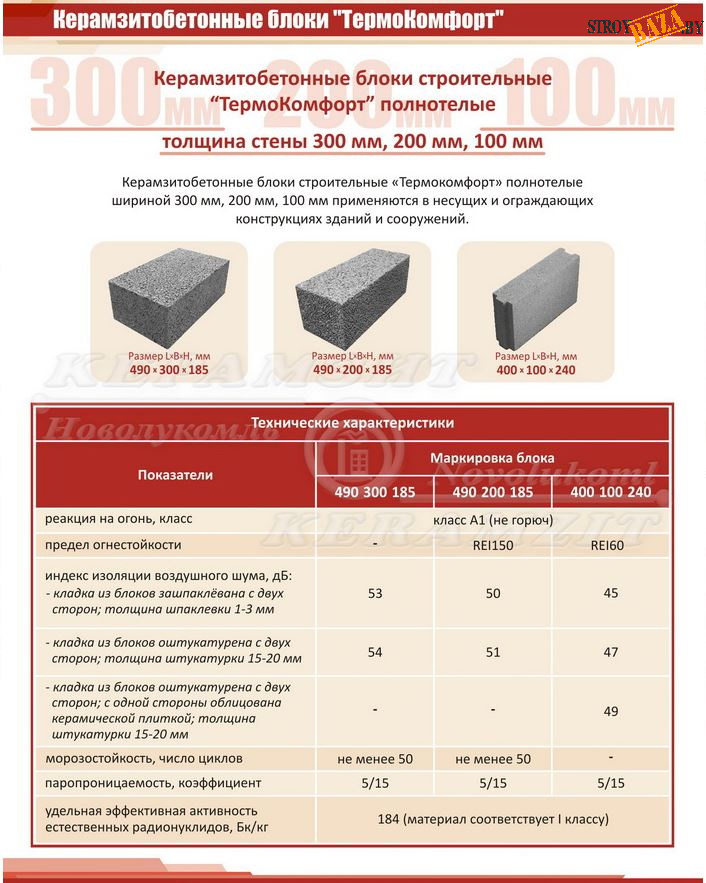
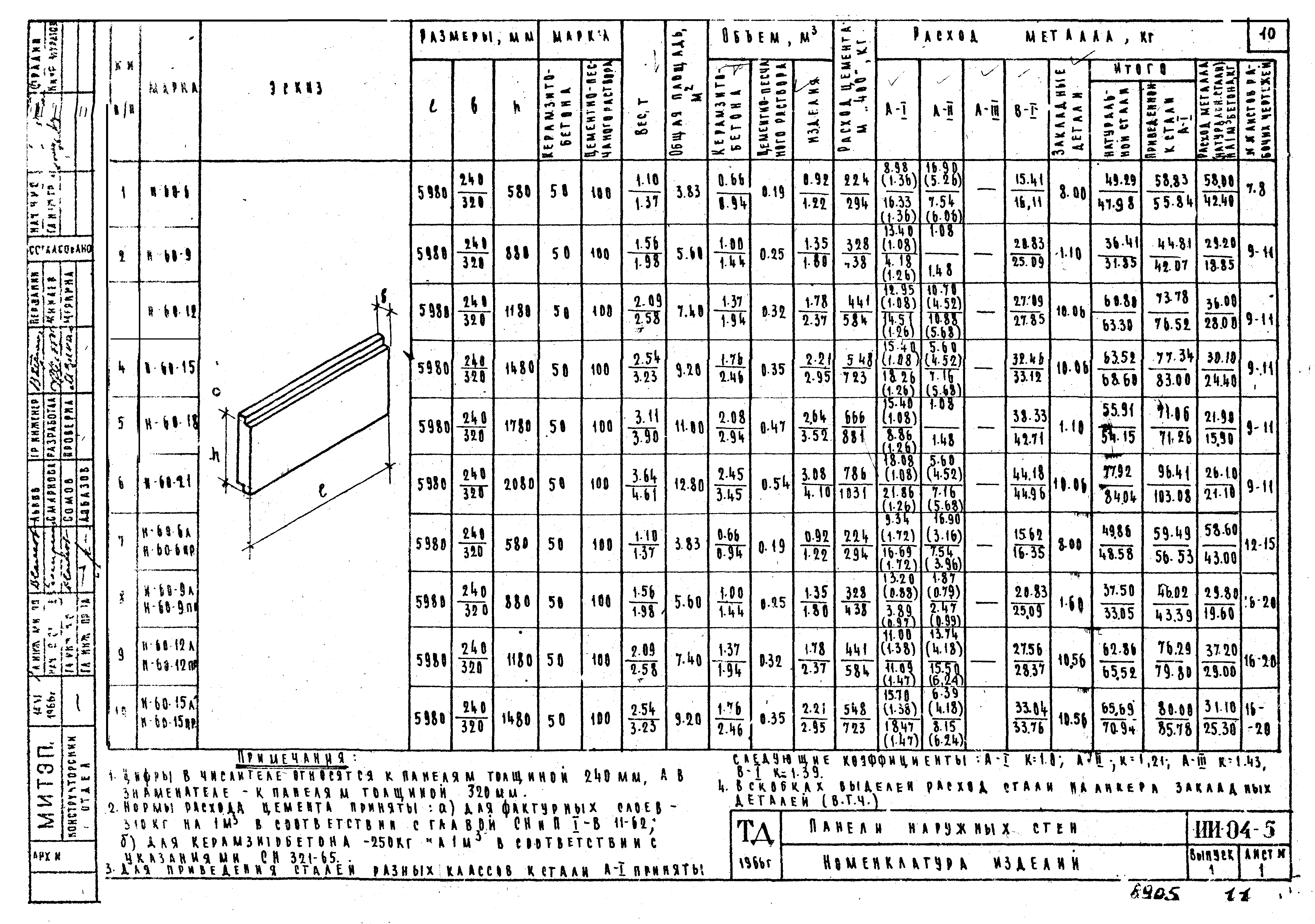
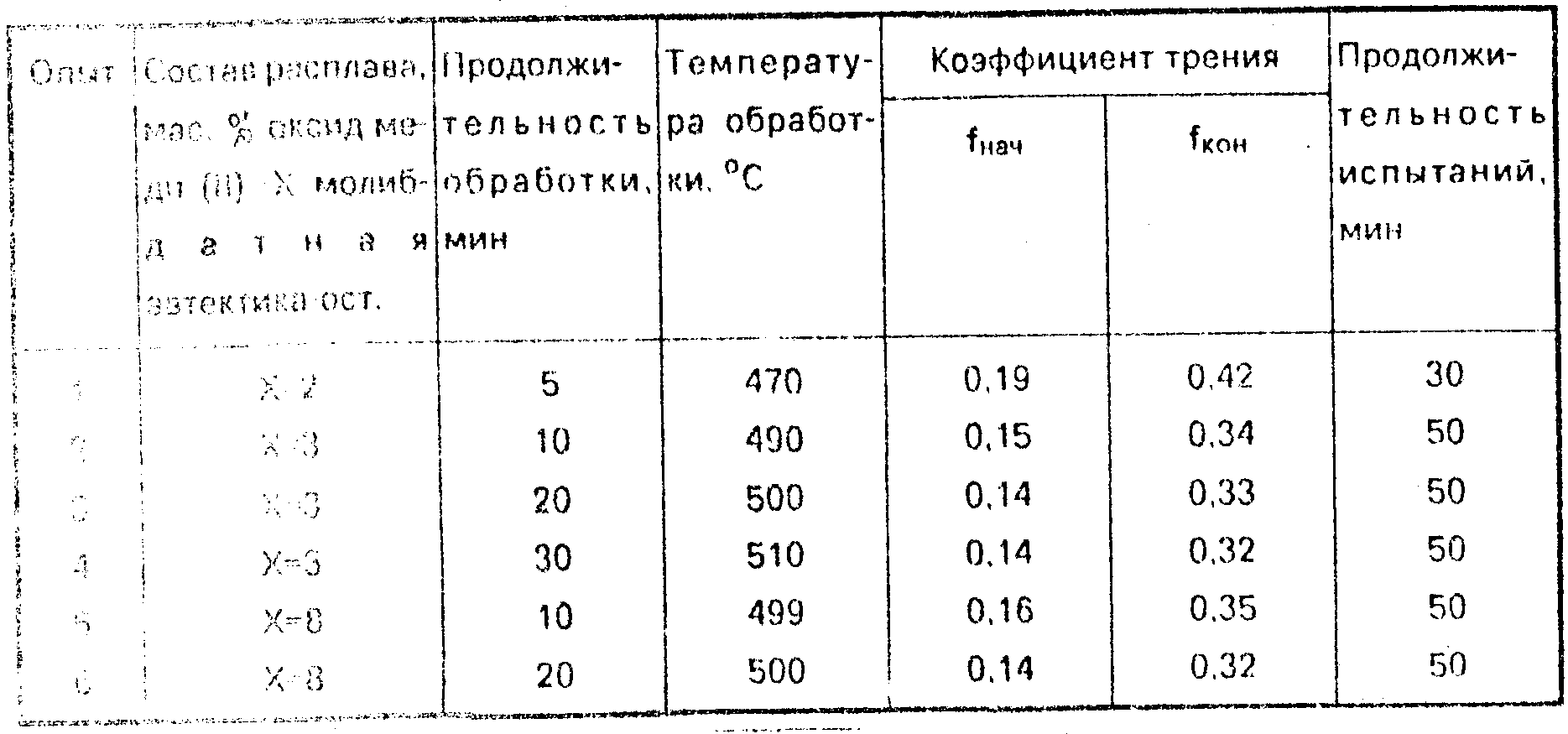
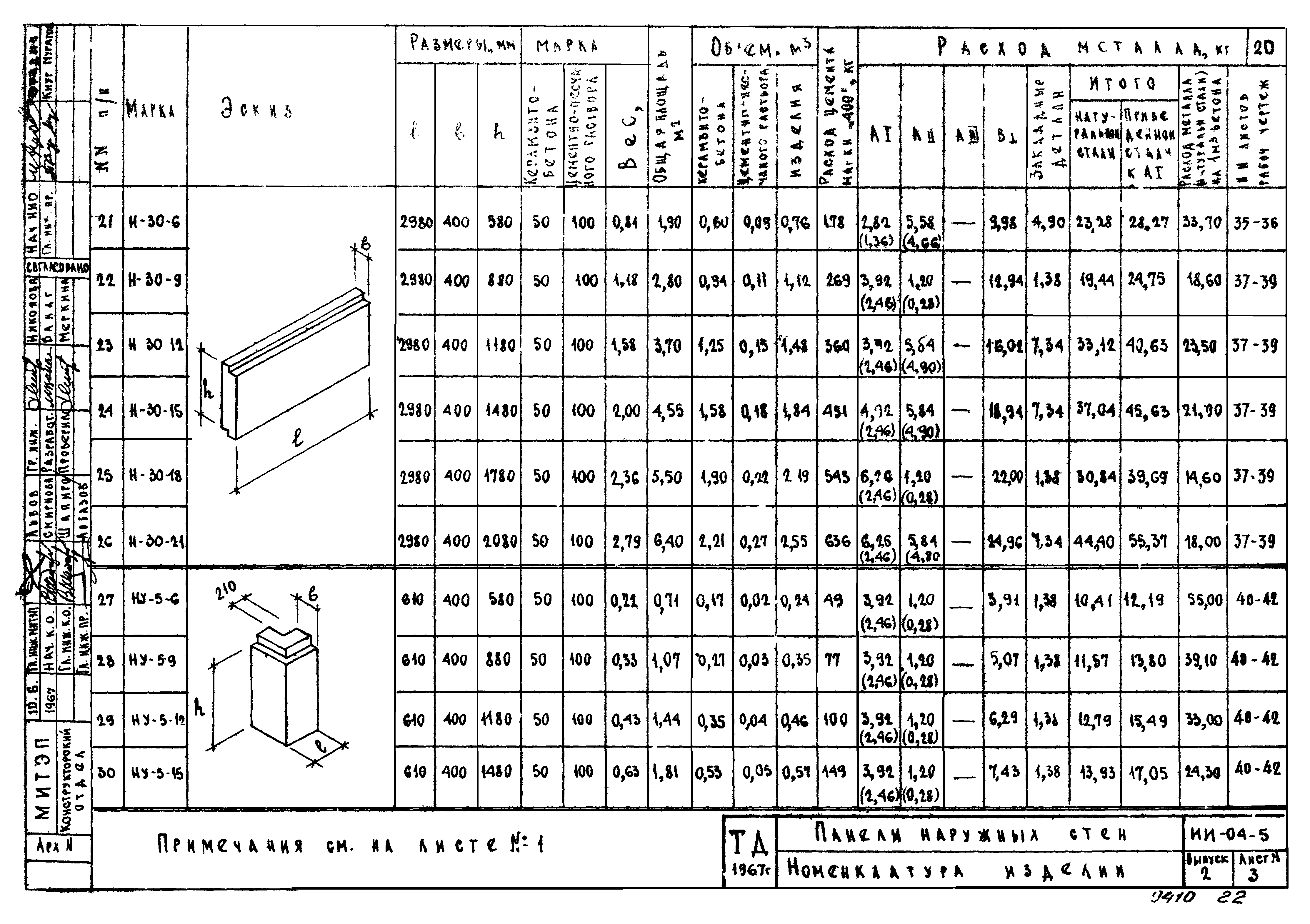
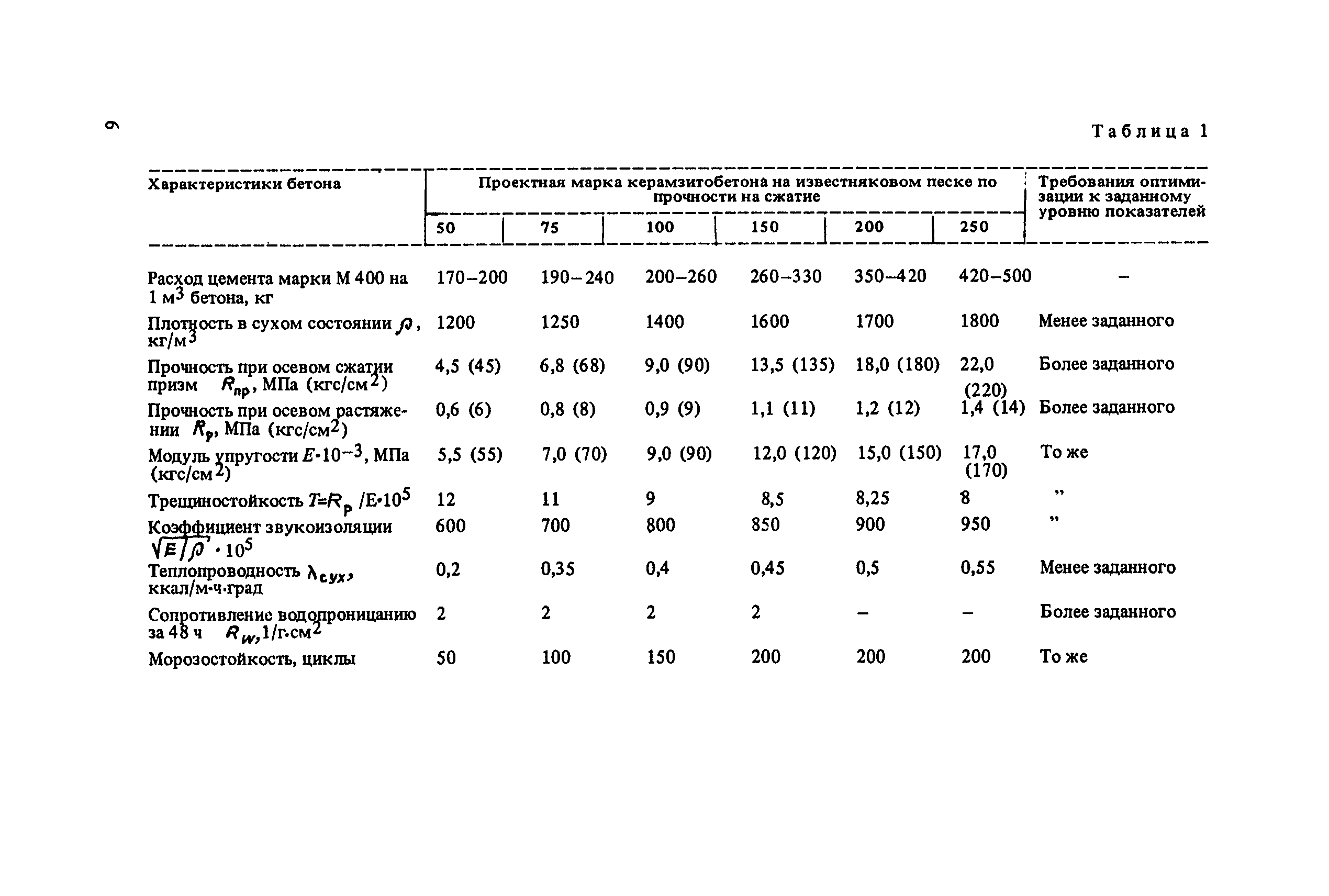


