Усиление углеволокном: Усиление железобетонных (жб) конструкций. Усиление бетона углеволокном
- Усиление строительных конструкций углеволокном SIKA
- Применение углеволокна в строительстве: армирование и усиление несущих конструкций своими руками
- Содержание
- Что такое углеволокно? Особенности использования материала
- Технические характеристики углеволокна: основные преимущества
- Каким требованиям должна отвечать эффективная технология армирования?
- В каких ситуациях необходимо осуществление внешнего армирования?
- Распространенные конструктивные решения для углеволокна
- Армирование фундамента своими руками: пошаговая инструкция
- Усиление строительных конструкций — углеволокно
- Усиление конструкций углеволокном в Москве и Московской области | Цены на усиление конструкций углеволокном в Москве
- Усиление конструкций углеволокном в Тюмени «ЕвроДом72»
- ГДЕ ПРИМЕНЯЕТСЯ УСИЛЕНИЕ КОНСТРУКЦИЙ УГЛЕВОЛОКНОМ?
- Рост популярности пластиков, армированных углеродным волокном
- Процесс производства углеродного волокна является частично химическим и частично механическим. Вращение: PAN вращается с использованием одного из нескольких процессов вращения.Этот шаг важен, потому что он формирует внутреннюю атомную структуру волокна. Затем волокна промывают и растягивают до необходимого диаметра. Растяжение также помогает выровнять молекулы, чтобы помочь в формировании кристаллов углерода, созданных карбонизацией. Стабилизация: На этом этапе волокна обрабатываются химическими веществами, чтобы изменить их линейное соединение на термостабильную структуру лестничного соединения. Затем нити нагревают на воздухе, чтобы они захватили молекулы кислорода и изменили схему атомных связей. Карбонизация: Волокна затем подвергаются воздействию очень высокой температуры без присутствия кислорода, поэтому волокно не может гореть. Атомы в волокне сильно вибрируют, выталкивая большую часть неуглеродных атомов в предшественнике. Обработка поверхности: После карбонизации поверхность волокон плохо сцепляется с материалами, используемыми при изготовлении композитных материалов. На этом этапе поверхность волокон слегка окисляется погружением в различные газы или жидкости. Проклейка: В этом процессе на волокна наносится покрытие, защищающее их от повреждений во время намотки или ткачества. Несколько продуктов, изготовленных из углеродных волокон, — это удочки, велосипеды, оборудование для гольфа, теннисные ракетки, детали для самолетов, мостов и автомобилей. * Модуль упругости – это сила растяжения, которую может оказывать волокно определенного диаметра без разрыва. Модуль упругости описывается в фунтах на квадратный дюйм или фунтах на квадратный дюйм. Вопросы? Дайте мне знать в разделе комментариев ниже. Ищете дополнительную информацию о пластмассах? Загрузите наше бесплатное руководство! Работа с армирующими материалами из углеродного волокна Меры предосторожности Прежде всего, остерегайтесь осколков! Мы рекомендуем надевать перчатки при работе с углеродным волокном или его резке. Мелкие осколки очень острые и довольно хрупкие. Из-за этого осколки очень трудно удалить, поскольку они часто крошатся и ломаются, когда вы пытаетесь их извлечь. Как и в случае с большинством материалов, пыль, образующаяся при резке или механической обработке углеродного волокна, опасна. Всегда носите пылезащитную маску, чтобы мелкие частицы пыли не попали в легкие и носовые проходы. Защитные очки также необходимы всякий раз, когда вы выполняете операции по резке. Механическая обработка Углеродное волокно — очень твердое, хрупкое вещество, которое затупляет режущие кромки ваших инструментов. Если вам просто нужно укоротить кусок углеродного волокна, мы рекомендуем использовать ножовку, чтобы отрезать его до нужной длины.Мы НЕ рекомендуем использовать электроинструменты для резки углеродного волокна, если в этом нет крайней необходимости. Если вы решили использовать электроинструмент для резки углеродного волокна, используйте абразивные диски или круги. Производители углеродного волокна используют лазеры или гидроабразивные резаки. Склеивание Вы можете использовать цианоакрилаты (суперклей), эпоксидные смолы или клей для дерева. Типичное использование Углеродное волокно в основном используется при изготовлении и ремонте струнных инструментов для усиления грифа.Конструкция и размеры грифа, анкерного стержня (если он есть) и другие аспекты помогут определить, какой кусок углеродного волокна подходит. В показанных примерах вы заметите, что арматурные стержни расположены вдали от анкерного стержня. Это придает шее большую устойчивость и уменьшает скручивание. Ниже приведены некоторые типичные примеры и используемое углеродное волокно: . Пример #1: Это больше относится к ситуации ремонта, но также может быть применено к новой шейке, которая не имеет усиливающего стержня.Снимите накладку грифа с инструмента и прорежьте канал в грифе, чтобы принять арматурный стержень # 4401 (1/8″ x 3/8″ x 18″). В этом или любом из следующих материалов можно использовать любой из рекомендуемых клеев. ситуации Пример № 2 и № 3: Вот две современные конструкции грифа, в которых используется регулируемый анкерный стержень и два усиливающих стержня для обеспечения жесткости и устойчивости. Размеры поперечного сечения грифа определят, какой пример лучше всего подходит для инструмента № 2 или № 3.Пример №3 показывает, как можно усилить 5- или 6-струнный бас. Многие современные тонкие грифы также требуют настройки, как в примере №3.
- Больше, чем просто инъекции
- Скобы и швы
- Произошла ошибка при настройке пользовательского файла cookie
- Новые марки Ultramid® Advanced с армированием углеродным волокном для легких и высокопроизводительных деталей
- Растущая роль пластмасс, армированных углеродным волокном
Усиление строительных конструкций углеволокном SIKA
УСИЛЕНИЕ СТРОИТЕЛЬНЫХ КОНСТРУКЦИЙ С ПРИМЕНЕНИЕМ ЭЛЕМЕНТОВ ВНЕШНЕГО АРМИРОВАНИЯ ИЗ УГЛЕВОЛОКНА
1.Введение. История вопроса.
Необходимость в усилении строительных конструкций путем приклейки элементов внешнего армирования из высокопрочного и высокомодульного материала появляется в следующих основных случаях:
— повреждение строительной конструкции, которое привело к снижению её несущей способности, жесткости и трещиностойкости,
— изменение условий эксплуатации, выражающееся ., прежде всего, в изменении величины, характера и расположения нагрузок,
— изменение расчетной схемы конструкции,
— необходимость повысить надежность и долговечность конструкции.
Для обеспечения эффективного усиления технология должна гарантировать выполнение следующих условий:
— возможность монтажа элементов внешнего армирования на конструкции естественной влажности,
— возможность надежной приклейки к любым строительным материалам, которая обеспечивает передачу усилий со строительной конструкции на элемент внешнего армирования,
— механические свойства материалов, применяемых при усилении должны быть стабильны во времени. Это относится как к монтажному клею, так и к элементу армирования,
— модуль упругости и прочность элемента внешнего армирования должны быть представлены достаточно широкой линейкой, для эффективного применения на различных конструкция из разных материалов.
Перечисленным выше требованиям вполне отвечают элементы внешнего армирования из высокопрочных и высокомодульных искусственных волокон, прежде всего углеродных и арамидных. Наибольшее распространение получили углеродные волокна, имеющие наилучшее на сегодняшний день соотношение цена/качество.
Углеродное волокно производится в трех странах: США, Япония и республики бывшего СССР.
Наибольшее распространение в изделиях для усиления получили элементы внешнего армирования из углеволокна японского производства.
Применение углеродного волокна в качестве внешнего армирования строительных конструкций насчитывает примерно 40-летнюю историю. На сегодняшний день имеют тысячи объектов, усиленных по этой технологии. Технология усиления строительных конструкций с применением элементов внешнего армирования из углеволокна тесно связана с технологиями ремонта и восстановления строительных конструкций в целом.
Данная технология является в настоящий момент самым современным и «бережным» методом восстановления и повышения эксплуатационных характеристик строительных конструкций.
2.Усиление железобетонных конструкций.
Железобетонные конструкции имеют в настоящий момент наибольшее распространение в строительстве. Повреждения железобетонных конструкций, как правило, связаны с различными коррозионными повреждениями, перегрузкой отдельных элементов и неправильной эксплуатацией. Часто требуется обеспечить надежную эксплуатацию уникальных, дорогих, исторически значимых конструкций, демонтаж и замена которых значительно дороже ремонта или невозможна вообще. Это, прежде всего, относится к транспортным, гидротехническим сооружениям, памятникам архитектуры. Усиление рядовых конструкций с применением технологии внешнего армирования должно быть обосновано экономически.
Для усиления железобетонных конструкций применяются элементы в виде лент и холстов. Механические характеристики элементов внешнего армирования варьируются в следующих пределах: Е= 70000 – 640000 МПа, R= 1700 – 4800 МПа.
При усилении железобетонных конструкций с применением лент необходимо решить проблему анкеровки ленты на конструкции, что приводит к необходимости устройства закладных деталей – стальных или из углехолста.
Наиболее распространенное решение при усилении железобетонных конструкций с применением углеволокна- расположение элемента внешнего армирования с наиболее растянутого волокна в пролетной зоне изгибаемых конструкций, хотя имеется успешный опыт усиления сжатой зоны. В зоне действия пролетных моментов могут устанавливаться как ленты, так и холсты. В последнее время имеет место тенденция более широкого распространения холстов. Это связано с их более высокими механическими характеристиками и простотой монтажа и обеспечения надежной анкеровки.
Важной областью применения элементов внешнего армирования является усиление приопорных участков в зоне действия поперечных сил. В этих зонах, как правило, устанавливают холсты из углехолста вдоль линии главных растягивающих напряжений. Углехолсты можно наклеивать в несколько слоев и формировать любые сечения, необходимые по расчету.
Применение элементов внешнего армирования для усиления сжатых, внецентренно- сжатых железобетонных элементов типа колонн, пилонов, простенков производится двумя способами. Во-первых, для усиления коротких элементов эффективно устройство бандажей из углехолста, создающих «эффект обоймы» по типу косвенного армирования. Во-вторых, установка углехолста вдоль сжатого элемента является дополнительной рабочей арматурой.
Перспективной областью применения элементов внешнего армирования из углеволокна является предварительно напряженные элементы. Впервые предварительно-напряженные углеродных ленты были применены при усилении автомобильного железобетонного моста на юге Германии в 1982г(Совместный проект концерна «СИКА» проектного бюро «Леонгард, Андрэ и парт. и фирмы «Леоба»). В России впервые предварительно-напряженные углепластиковые ленты были применены при усилении балок пролетного строения авторожного моста через реку Киржач на 104 км трассы Москва-Нижний Новгород в 2003 г. Предварительное напряжение элементов внешнего армирования значительно повышает его эффективность и сферы его применения. Натяжение производится гидродомкратами с использованием специальных захватов и анкерных устройств. При натяжении элементов внешнего армирования из углеволокна с его последующим закреплением на конструкции достигается не только повышение несущей спосбности, но так же достигается повышение жесткости и трещиностойкости усиливаемого элемента.
3. Усиление металлических конструкций.
3.1. Усиление растянутых конструкций.
Усиление растянутых стальных конструкций элементами внешнего армирования из углеволокна целесообразно производить симметрично относительно центра тяжести сечения. При этом применяется углеволокно с модулем упругости равным или минимально отличающимся от модуля упругости материала усиливаемого стального элемента и максимально высокой прочности(например Е=20000-230000 МПа, R=480000 Мпа).
Основываясь на современной линейке материалов из углеволокна, возможен достаточно точный подбор материала для получения наибольшей эффективности усиления.
Установка элементов внешнего армирования происходит в следующем порядке:
— очистка поверхности от загрязнений (возможна пескоструйная обработка),
— нанесение адгезионного слоя – монтажного эпоксидного клея,
— монтаж элементов внешнего армирования ( холста или ленты),
— эащитная или огнезащитная покраска.
3.2. Усиление внецентренно сжатых конструкций.
Усиление внецентренно сжатых стальных элементов производится путем установки элементов внешнего армирования из углеволокна симметрично относительно центра тяжести сечения. Возможно несимметричное расположение элементов внешнего армирования, например при восстановления сечения при ремонте коррозионных повреждений.
Лдя усиления внецентренно сжатых стальных элементов целесообразно применять элементы внешнего армирования из углеволокна с максимально высоким модулем упругости (до 640000 Мпа).
3.3. Повышение устойчивости пластинок.
Повышение устойчивости стальных пластинок, например высоких стенок балок из плоскости изгиба в зоне действия поперечной силы производится путем наклейки элементов внешнего армирования (холстов) симметрично относительно центра тяжести сечения.
- 4. Усиление деревянных конструкций.
Усиление деревянных конструкций производится путем установки элементов внешнего армирования из углеволокна. При этом применяется углеволокно с модулем упругости не менее 300000 Мпа.
Установка элементов внешнего армирования производится двумя основными способами:
— путем приклейки к поверхности,
— путем вклейки на монтажный клей в предварительно подготовленные пропилы.
Второй способ применяется в случае, если необходимо сохранить первоначальный вид балок и сделать незаметным само усиление. Пропилы предпочтительно делать вертикальными для минимального нарушения целостности сечения.
Наиболее широко используют элементы внешнего армирования из углеволокна при усилении деревянных балок, как сплошный, так и клееных в зоне действия пролетных моментов.
Элементы усиления в виде углехолстов устанавливают на участки, где действуют главные растягивающие напряжения и имеется опасность раскалывания вдоль волокон. Эффективно повышение жесткости гибких фанерных стенок путем приклейки углехолста в зоне действия поперечной силы.
К основным преимуществам элементов внешнего армирования из углеволокна относят простоту и скорость их монтажа и незаметность на конструкции.
5. Усиление каменных конструкций.
Основная сфера применения элементов внешнего армирования из углеволокна при усилении каменных конструкций-внецентенно-сжатые элементы, т.е. столбы, пилоны и простенки. При усилении этих элементов специалисты сталкиваются с проблемой включения в работу стальных обойм, монтируемых на конструкцию, в соответсвии с традиционной концепцией усиления. Для обеспечения совместной работы стальной обоймы и усиливаемого столба как правило пытаются создать в обойме начальные усилия путем нагрева хомутов и применения расширяющихся растворов. Технически это осуществимо, но достаточно трудоемко и нетехнологично.
Обоймы из углеволокна (углехоста) являются эффективной альтернативой стальным обоймам, поскольку их включение в работу усиливаемого элемента обеспечивается просто во время монтажа холста на усиливаемый элемент через клеевой слой.
Натурные испытания кирпичных столбов, проведенные в лаборатории каменных конструкций ЦНИИСК в 2004г по инициативе и под руководством руководителя сектора к.т.н. Грановского А.В., показали 1,5-2,0 кратное увеличение несущей способности кирпичных столбов, усиленных банадажами из углехоста.
Применение элементов внешнего армирования из углеволокна позволяет в широких пределах регулировать усилия в каменной конструкции, минимально нарушая её целостность. Это в полной мере касается конструкций рекоструируемых и реставрируемых зданий.
Отдельный вопрос-это усиление каменных стен, поврежденных в результате просадок фундаментов или имеющих отверстия в виде технологических, дверных, оконных проемов.
Традиционным решением при усилении подобных элементов является установка стальных скоб, стальных профилей через анкерное крепление на стене в отдельных точках с последующей зачеканкой расширяющимися растворами. Применение элементов внешнего армирования из углеволокна для усиления перечисленных конструкций позволяет избежать установки точечных анкеров, вовлечь больший объем материала в работу отдельного элемента, реализовать имеющиеся резервы конструкции, при этом бережно отнестись к неповрежденным участкам.
Применение углеволокна в строительстве: армирование и усиление несущих конструкций своими руками
Современное строительство, как и любая другая отрасль, не обходится без внедрения инновационных технологий, и уже сегодня материалы, ранее используемые только в наукоемких производствах, таких как ракетостроение, широко применяются в строительной сфере, формируя архитектуру будущего. Одной из наиболее важных задач современного строительства является предотвращение проблем, связанных с прочностью зданий и сооружений, которая находится под влиянием динамических нагрузок, перепадов температур и других агрессивных климатических факторов. В результате этого на бетонных стенах построек появляются трещины, отслаивается защитный слой, что приводит к снижению эксплуатационных характеристик зданий. В связи с этим, неотъемлемым этапом строительства стало армирование несущих конструкций, призванное предотвратить их преждевременное разрушение. Если раньше популярным материалом, используемым в этих целях, долгое время был стеклохолст, то сегодня его постепенно вытесняет новый востребованный материал – углеволокно, о характеристиках и особенностях использования которого поговорим далее.
Содержание
- Что такое углеволокно? Особенности использования материала
- Технические характеристики углеволокна: основные преимущества
- Каким требованиям должна отвечать эффективная технология армирования?
- В каких ситуациях необходимо осуществление внешнего армирования?
- Распространенные конструктивные решения для углеволокна
- Армирование фундамента своими руками: пошаговая инструкция
Что такое углеволокно? Особенности использования материала
Углеродное волокно – линейно-упругий композитно-полимерный материал искусственного происхождения, структурным элементом которого являются тонкие углеродные нити диаметром от 3 до 15 микрон, состоящие из атомов углерода. Последние, в свою очередь, объединены в кристаллы микроскопических размеров, которые, благодаря выравниванию, расположены параллельно друг другу. Выравнивание способствует повышению прочности волокна на растяжение. По своим техническим характеристикам, в частности твердости, углеволокно в несколько раз превосходит металл, вследствие чего широко используется в оборонной промышленности, аэрокосмическом производстве и строительной сфере. Несмотря на то, что уникальные характеристики углеволокна позволяют считать данный материал инновационным, он не является изобретением нашего столетия и давно используется в авиа- и ракетостроении, а с конца прошлого столетия и в строительстве. Впервые в этой сфере он появился в 1980 году, когда в Калифорнии все здания и сооружения стали возводиться с использованием углеродного волокна, что позволило укрепить постройки, расположенные на сейсмически активной территории. Взяв это свойство на вооружение, отечественные строители нашли применение данному материалу в процессе проведения ремонтных мероприятий в жилых домах, и с тех пор его популярность только растет.
Важно! Следует помнить, что углеволокно, аналогично бетону, является лишь материалом, а не конечным готовым изделием. Оно является основой для изготовления большого количества материалов, используемых в строительстве для армирования своими руками. К ним относятся углеродные сетки, ламели и ленты.
Технические характеристики углеволокна: основные преимущества
Углеродное волокно состоит из полиакрилнитрита, прошедшего предварительную обработку высокими температурами (до 3-5 тысяч градусов). В силу технических особенностей, углеволокно используется для внешнего армирования, в процессе которого его пропитывают связующим веществом (двухкомпонентная эпоксидная смола) и аналогично обоям наклеивают на поверхность конструкции, нуждающейся в укреплении. Целесообразность применения именно этого связующего вещества доказана по нескольким направлениям:
- Во-первых, эпоксидная смола обладает высокой адгезией к железобетону;
- Во-вторых, после вступления в химическую реакцию со смолой углеволокно превращается в жесткий пластик, приобретая прочность, в 6-7 раз превосходящую прочность стали.
На сегодняшний день углеволокно характеризуется наибольшей популярностью среди других композитных материалов. Несмотря на то, что оно на 30 % легче алюминия и на 75 % легче железа, его прочность на разрыв в четыре раза превосходит наилучшие марки стали. Изготовленное на основе углерода, углеволокно имеет низкий удельный вес и при нагревании незначительно расширяется, при этом оно не подвержено воздействию агрессивных химических веществ. С учетом вышеперечисленных характеристик, углеволокно можно считать универсальным материалом, адаптированным для использования в различных климатических зонах.
Длительный эксплуатационный срок материала объясняется сочетанием следующих его преимуществ:
- Высокие гидроизоляционные характеристики, обусловленные глянцевой поверхностью углепластика, за счет которой материал не вступает в реакцию с водой;
- Высокая адгезия к различным поверхностям;
- Исключительная устойчивость к коррозионным процессам;
- Легкость – свойство, благодаря которому система армирования не создает дополнительных нагрузок на постройку.
Несмотря на то, что углеволокно весит намного меньше, чем сталь, оно обладает высокими прочностными характеристиками;
- Используя углеволокно, вы получаете возможность наносить армирующий материал в несколько слоев;
- В процессе выполнения ремонтных работ можно не прекращать эксплуатацию усиливаемого здания;
- Применение углеволокна для армирования фундамента своими руками способствует сокращению временных и трудовых затрат при проведении работ;
- Углеволокно по праву считается универсальным материалом, который можно использовать для армирования конструкций любой сложности и конфигурации, в том числе на закругленных и угловых поверхностях, на ребристых плитах перекрытий, балочных элементах рамных конструкций, а также тавровых балок мостовых пролетов, которые характеризуются малой шириной ребра;
- Углеволокно – экологически чистый и токсически безопасный материал для армирования;
- Кроме того, данный материал отличается огнеупорностью и ударопрочностью.
Каким требованиям должна отвечать эффективная технология армирования?
Для обеспечения эффективного усиления конструкции технология армирования должна гарантировать выполнение ряда условий:
- Естественная влажность конструкций не должна быть препятствием для монтажа армирующих элементов;
- Элементы армирования должны надежно приклеиваться к любым строительным материалам, благодаря чему будет осуществляться эффективная передача усилий с усиливаемой конструкции на армирующие элементы;
- Все материалы, используемые в процессе армирования, в том числе и монтажный клей, должны характеризоваться свойствами, стабильными во времени, что позволит повысить эффективность армирования;
- В связи с тем, что армированию подлежат конструкции из различных материалов, модуль упругости и прочность армирующих элементов должны быть представлены достаточно широкой линейкой.
Всем требованиям, перечисленным выше, отвечают элементы внешнего армирования, представленные волокнами искусственного происхождения, в частности арамидными и углеродными, при этом последние, продемонстрировав наилучшее соотношение цена/качество, получили наибольшее распространение.
В каких ситуациях необходимо осуществление внешнего армирования?
На сегодняшний день углеволокно используется для армирования конструкций из различных материалов:
- Железобетонных построек — к ним относятся мосты, гидротехнические сооружения и памятники архитектуры, которые нуждаются в защите от коррозии, усилении сжатых элементов и их защите от перегрузок. С этой функцией в полной мере справляется углеволокно;
- Металлических конструкций, которые обладают близким к углеволокну модулем упругости и прочности;
- Каменных конструкций, в частности каменных столбов, стен кирпичных домов и пилонов.
Необходимость в усилении построек посредством внешнего армирования возникает в следующих ситуациях:
- В случае повреждения конструкции, ставшего причиной снижения ее несущей способности, жесткости и устойчивости к трещинам;
- Если произошло изменение условий эксплуатации постройки, которое выражается в изменении величины и характера нагрузок;
- В процессе проектирования и строительства конструкций с целью повышения их сейсмостойкости и увеличения межремонтных промежутков;
- В случае длительного воздействия на конструкцию механических факторов или агрессивных природных сред, приведшего к разрушению бетона или коррозии арматуры, возникает необходимость устранения неутешительных последствий и усиления конструкции.
- Проанализировав определенный набор технико-экономических показателей, можно прийти к выводу, что усиление углеволокном чаще всего уместно по отношению к железобетонным конструкциям, однако применимо и к металлическим, и бетонным, и даже деревянным зданиям и сооружениям.
Распространенные конструктивные решения для углеволокна
Если вы отдали предпочтение углеволокну и системам внешнего армирования с его использованием, помните, что проектируя системы усиления, необходимо руководствоваться Сводом правил СП 164.1325800.2014 «Усиление железобетонных конструкций композитными материалами. Правила проектирования».
Отказавшись от армирования перекрытий руками специалистов и производя их усиление самостоятельно, учтите, что оно осуществляется посредством наклеивания углеволокна в зонах наибольшей нагрузки – обычно они приходятся на центральную часть пролета и соприкасаются с нижней гранью конструкции. Благодаря этому приему значительно повышается несущая способность конструкции по изгибающим моментам. Чтобы решить эту задачу, специалисты рекомендуют использовать любой из доступных видов углеродных материалов – ламели, ленты или сетки.
Важно! В процессе усиления балок зачастую возникает необходимость в усилении приопорных зон, что позволит повысить несущую способность конструкции при воздействии поперечных сил. С этой целью наклеивают U-образные хомуты, изготовленные из углеродных сеток или лент.
Важно! Что касается особенностей использования материалов из углеволокна, необходимо отметить, что, благодаря схожести способов монтажа и адгезивных составов, углеродные ленты и ламели, как правило, монтируются вместе, тогда как использование углеродных сеток, в силу монтажа материала «мокрым» способом, исключает применение лент и ламелей.
В рамках обсуждения технологии армирования бетона своими руками, отдельно необходимо поговорить об усилении колонн, которое осуществляется посредством их оклейки углеродными сетками или лентами, которые монтируются в поперечном направлении. Благодаря этому удается достигнуть эффекта «бондажирования», что позволяет предотвратить поперечные деформации бетона.
Армирование фундамента своими руками: пошаговая инструкция
Если вы ищите ответ на вопрос: «Как сделать армирование фундамента своими руками?», ознакомьтесь с нашими рекомендациями, представленными ниже, и вы узнаете, как произвести армирование плиты фундамента своими руками.
Подготовка поверхности: рекомендации специалистов
Прежде чем приступить к монтажу системы внешнего армирования с использованием углеволокна, необходимо произвести разметку конструкции, отчертив зоны, в которых будут располагаться элементы усиления. Произведя размеры, очистите поверхность от остатков отделочных материалов, цементного молочка с помощью углошлифовальной машинки с алмазной чашкой или водо-пескоструйной установки до тех пор, пока не обнажится крупный заполнитель бетона. Старайтесь производить эти манипуляции качественно, так как от характеристик подготовленного основания напрямую зависит эффективность системы усиления. В связи с этим, в процессе подготовки основания, обратите внимание на следующие параметры:
- Целостность и прочность материала, из которого изготовлена конструкция, подлежащая усилению;
- Ровность поверхности, на которую будет монтироваться углеволокно;
- Температура и влажность поверхности, на которую будет наклеиваться углеродный материал;
- Отсутствие пыли и других загрязнений;
- Кроме того, существует еще целый ряд контролируемых параметров, которые можно найти в технологических картах на выполнение того или иного вида работ.
Подготовка армирующих материалов
Углеволокно продается смотанным в рулоны, упакованные в полиэтиленовую пленку. В процессе подготовки рабочей поверхности важно следить за тем, чтобы на армирующий материал не попала пыль, в большом количестве образуемая в процессе шлифования бетона, так как это приведет к тому, что материал не пропитается связующим веществом и станет причиной производственного брака.
Чтобы предотвратить это, перед раскроем материала застелите рабочую поверхность полиэтиленом и только после этого осуществляйте замеры. Для обрезки углеродных сеток и лент можно использовать канцелярский нож или ножницы по металлу, ламелей – углошлифовальной машинкой, оснащенной отрезным кругом по металлу.
В качестве адгезивов рекомендуют использовать двухкомпонентные составы, в связи с чем, неотъемлемым этапом их подготовки будет смешивание двух компонентов в определенной пропорции. Чтобы случайно не нарушить их соотношение, в процессе их дозирования необходимо использовать мерную посуду или весы. Существует важное правило подготовки смеси – компоненты смешивают, постепенно добавляя друг к другу и перемешивая полученную массу дрелью, оснащенной специальной насадкой.
Важно! Ошибки, допущенные в процессе подготовки смеси, могут привести к закипанию адгезива.
Важно! На современном строительном рынке можно найти адгезивы, поставляемые в комплекте – т.
е. в двух ведрах, в которых уже дозирован необходимый объем компонентов. Таким образом, работая с уже дозированными смесями, достаточно содержимое одного ведра смешать с содержимым другого (для удобства работы одно из ведер поставляется большего объема и остается полупустым).
Для углеродных сеток используют полимерцементный адгезив, который поставляется в мешках и перед работой разводятся водой в соответствии с инструкцией.
Как произвести монтаж углеволоконных материалов?
Технология монтажа армирующей системы существенно отличается в зависимости от типа используемого материала.
Монтаж углеродной ленты может осуществляться «сухим» или «мокрым» способом. И в том, и в другом случае на поверхность усиливаемого основания наносят слой адгезива, однако «мокрый» способ подразумевает пропитывание углеродной ленты адгезивом с последующим прикатыванием ее валиком к основанию, тогда как «сухой» способ предполагает крепление ленты к основанию и только после прикатывания валиком ее пропитывают адгезивной смесью. Таким образом, последовательность этапов монтажа меняется местами. Для осуществления пропитки углеродной ленты адгезивным составом на ее поверхность наносят слой адгезива и, прикатывая валиком, добиваются того, чтобы верхний слой связующего вещества попал вглубь углеволокна, а нижний – вышел наружу.
Углеродные ленты можно наклеивать в несколько слоев, однако при их наклеивании на поверхность потолка не рекомендуется наносить более двух слоев, что предотвратит «сползание» материала под тяжестью собственного веса.
Важно! Помните, что после того, как произойдет полимеризация адгезива, его поверхность станет идеально гладкой и ровной, что сделает его отделку практически невозможной. В связи с этим, не дожидаясь затвердевания связующего вещества, еще на «свежую» поверхность наносят слой крупного песка.
В процессе монтажа углеродных ламелей слой связующего вещества наносят не только на усиливаемую конструкцию, но и на монтируемый элемент армирования. В завершение работ ламель прикатывают валиком или шпателем.
Монтируя углеродную сетку, в процессе армирования ленточного фундамента своими руками ее крепят на увлажненную бетонную поверхность. После нанесения первого слоя полимерцементного адгезива ручным или механизированным способом, не дожидаясь его высыхания раскатывают углеродную сетку, слегка вдавливая ее в нанесенный состав. Для удобства работы специалисты рекомендуют использовать шпатель. Затем необходимо дождаться первичного схватывания состава, время наступления которого зависит от характеристик выбранного состава и температуры окружающей среды. Чтобы убедиться в том, что состав начинает затвердевать, надавите на его поверхность пальцем – он должен продавливаться с большими усилиями. После этого наносят заключительный слой полимерцемента.
Важно! Адгезивы на основе эпоксидных смол подвержены возгоранию и разрушению под действием ультрафиолетовых лучей, в связи с чем, их необходимо проверить на класс огнестойкости и защитить от ультрафиолета.
Усиление строительных конструкций — углеволокно
Как известно, лучшее – враг хорошего. На смену проверенным решениям приходят новые, как минимум не менее качественные и уж точно более надежные и удобные. Типовые решения усиления металлическими элементами различного профиля сменяются углеволоконными. Откуда оно пришло, это углеволокно? Сначала оно было только в космических технологиях, потом в пришло в авиастроение. Поинтересуйтесь, из чего делаются самые нагруженные элементы в современных авиалайнерах – крепление хвоста, крыльев и закрылки?
Углеволокно?
Да, да именно из углеволокна. А малые самолеты класса Сессна? Они из родственной технологии – стекловолокна. По мере расширения применения падала стоимость этих материалов и постепенно они стали проникать в промышленность и строительство. В далеком 1969 году в США был построен полностью (!) углеволоконный мост. Пусть он был совсем малого пролета, но это факт!
Сейчас уже никого не удивить удочками, теннисными ракетками, велосипедами, ветряками, лыжами из стекло- или углепластика. Где вес в совокупности с прочностью и термостойкостью имеет значение – тут все остальные материалы пасуют. Углеволокно и только углеволокно. Но технология рвалась вперед, в новые области. И тут в поле зрения попала проблема разрушения железобетона. Ведь защитный слой бетона не вечен, а враг прочной стали – влага – вездесущ. И постепенно идет коррозия и арматура не выполняет свои функции.
А трещины, аварийные ситуации? Как заменить или восстановить один из элементов, взаимосвязанных в единое целое в сооружении. Подвести еще металл? Неплохая идея, кроме опять же ее подверженности коррозии, дополнительного веса и следственно нагрузки на несущие конструкции и практически невозможностью включить дополнительный металл в работу. И тут углеволокно опять незаменимо. От усилений колонн обоймами до усиления ребристых плит и балконов. И углеволокно купить стало просто – в Минске в наличии на складе. Причем различных поставщиков.
Углеволокно!
Прочность на разрыв в 10 раз выше,чем у стали, вес пренебрежимо мал, толщина настолько мизерна, что никак не влияет на размеры сечений усиливаемой конструкции и внутренних размеров зданий, что важно в административных и жилых зданиях, ведь это все деньги, не правда ли? Прочность адгезивов, которые передают нагрузку на углеволокно, не вызывает сомнений и позволяет намертво прикрепить материал к усиливаемой конструкции и включить в работу при увеличении нагрузки или преднапряжении.
Казалось бы, как полосочка материала толщиной около 1 мм (!) и весом 230 г/м2 может существенно увеличивать прочность конструкции, например в обойме колонны или под плитой перекрытия? Но опыты десятков европейских институтов и лабораторий доказали, что это не фантастика, а реальность. В Беларуси идет применении углеволокна с 1999 года.
Самыми частыми были усиления колонн обоймой из углеволокна (ТЦ по ул. Сурганова – 2 объекта, ул. Московской, ул.Притыцкого), усиления перекрытий – просто много объектов, все не перечислить; усиление ребристых плит. Хотя считается, что уклеволокно купить и применить дорого – мы усиляли ригеля в птичниках – это оказалось дешевле и быстрее. Не было только усиления балконов, хотя сделать это технически возможно.
Качественные решения сегодня – спокойный сон завтра
За это время десятки объектов получили вторую жизнь, будучи вылеченными без “хирургического вмешательства” – никаких раздалбываний пустот в пустотных плитах, никаких металлических кастетов на колоннах – вместо них изящные невидимые потом бандажи из “эластичных бинтов”, никаких подведенных “костылей“ под плиты покрытия в виде двутавров, никаких окольцовок зданий массивными швеллерами – лишь изящные темно серые повязки из углеволокна, и конечно же, без остановок производств, движения поездов, отселения жильцов и самое главное – без головной боли как потом это обслуживать – заботиться об антикоррозии, степени натяжения, усталости и отваливающейся штукатурки.
Усиление конструкций углеволокном в Москве и Московской области | Цены на усиление конструкций углеволокном в Москве
Компания «БАУЭР» предлагает комплексные решения по увеличению долговечности конструкции, продлевающее срок эксплуатации зданий и сооружений. В числе прочих, наша компания предлагает услугу «усиление углеволокном конструкций зданий и сооружений».
Современные высокие технологии позволяют использовать композитные материалы для усиления конструкций в случае необходимости увеличения расчетных нагрузок и увеличения несущей способности конструкций сооружения. Одно из самых современных направлений в этой области — усиление углеволокном.
Усиление углеволокном укрепляет:
С помощью углеволокна, как материала для усиления зданий, производят укрепления следующих типов конструкций:
- Железобетонных.
- Металлических.
- Деревянных.
- Каменных.
Специалисты нашей компании проведут полный комплекс высокотехнологичных работ по усилению углеволокном при реконструкции здания, что является наиболее эффективным способом увеличения несущей способности здания или сооружения по сравнению с более традиционными методами строительной сферы. Для осуществления работ в рамках услуги «усиление углеволокном» необходимы дополнительные знания, опыт и специальное техническое оснащение. Всем этим располагает компания «БАУЭР».
Для уточнения стоимости работ по усилению конструкций углеколокном, обратитесь по нашему телефону +7 (495) 128-92-56 или закажите звонок нашего менеджера.
Что такое углеволокно?
Углеволокно (углеродное волокно) – это материал, который состоит из нитей диаметром 3-15 микрон, образованными преимущественно атомами углерода, которые в свою очередь образовывают кристаллы, выровненные параллельно друг другу. Благодаря чему, такое волокно приобретает огромную прочность на растяжение. Помимо этого, углеродное волокно инертно к химическим соединениям, что позволяет производить усиление конструкций углеволокном в различных средах.
Углеволокно, как материал, имеет и ряд других достоинств. Например, коррозийная стойкость, низкий вес, низкий коэффициент температурного расширения и высокое расчетное сопротивление. Все это влияет на серьезное увеличение сроков службы и эксплуатации зданий и сооружений, прошедших процедуру по усилению углеволокном.
Особое место применение углеволокна нашло в сфере реконструкции промышленных и производственных зданий. Усиление конструкций углеволокном применяется в рамках работ, связанных с реконструкцией зданий или сооружений, которые приходят в негодность или перестраиваются в связи с повышенными требованиями к техническим и технологическим характеристикам.
«БАУЭР» — это проверенная временем инжиниринговая компания, которая имеет опыт работы не только в сфере строительства зданий, но и в их проектировании. Наши опыт и знания помогут вам произвести усиление конструкций углеволокном на высшем уровне. Достижение значительного экономического эффекта, строго определенные сроки и высокое качество работ – это то, что гарантируют специалисты нашей компании.
С НАМИ ВЫГОДНО! |
Усиление конструкций углеволокном в Тюмени «ЕвроДом72»
Необходимость усиления элементов здания возникает не только из-за естественного износа конструкции, но и из-за эксплуатации. Иногда в усилении конструкций требуется и новые строения. Наиболее подходящий способ усиления выбирается по результатам предварительного обследования.
Усиление углеволокном — инновационный и эффективный метод, который часто применяется в современном строительстве. Углеродное волокно — очень перспективный материал. Приклеивается к элементам, требующим армирования тонкими слоями. Толщина материала не превышает пяти миллиметров. Удельный вес тоже очень маленький. Это делает его использование совершенно незаметным, не меняет внутренних габаритов помещения. По этой же причине армирование конструкций углеродным волокном может применяться при нежелательном увеличении массы конструкции.
При необходимости армированные углеродным волокном производится, чтобы увеличить несущую способность здания на долгое время.
Если в результате расчетов или технического осмотра были выявлены повреждения несущих конструкций, арматуры, вызванные поломкой или коррозией, то необходимо усилить конструкции углеродным волокном. Эта мера также необходима при нарушении соединения арматурного каркаса с объектом (анкером) или открытых трещин.
В чем суть метода?
Техника включает в себя приклеивание прочной тонкой углеродной ткани к поврежденному элементу. В результате армирующий материал сам принимает на себя часть нагрузки. Это увеличивает несущую способность всей конструкции
Для обеспечения хорошего контакта углеродного волокна к поверхности используются специальные клеи, эпоксидные смолы или составы, содержащие минеральный вяжущий компонент.
В результате усиления с применением углеродного волокна мы:
- Укрепляем или реставрируем каменные, металлические, деревянные, бетонные конструкций или элементы здания;
- Перераспределяем давление и снимаем нагрузку к несущим стенам, аркам и фундаментам;
- Повышаем сейсмостойкость здания или комплекса сооружений за счет установки плит из углеродного волокна для защиты фундамента и некоторых элементов конструкции;
Звоните нам для получения подробной технической консультации. Мы знаем все тонкости усиления строительных конструкций.
Качественные сервис
Долгосрочная гарантия
Квалифицированные
специалисты
Евродом г. Тюмень
- Утепление частных и промышленных объектов ППУ напылением
- Монтаж дренажных систем для дома и участка
- Гидроизоляция жилых и нежилых помещений
- Усиление конструкций углеволокном
- Восстановление конструкций
- Заливка и ремонт отмосток
ГДЕ ПРИМЕНЯЕТСЯ УСИЛЕНИЕ КОНСТРУКЦИЙ УГЛЕВОЛОКНОМ?
Для повышения общей прочности и надежности сооружения строительный процесс не проходит без усиления конструкций. Данная процедура позволяет повысить сроки эксплуатации как отдельных частей строения, так и всей постройки.
С этой целью применяется сравнительно новая технология — усиление углеволокном.
Сегодня именно использование углеволокна является наиболее экономичным, но при этом результативным способом укрепить конструкцию. Но получение ожидаемого результата возможно лишь при условии, что материал соответствует ряду требований:
· по своей структуре материал должен состоять из параллельно расположенных волокон;
· углеволокно должно соответствовать определенным стандартам качества;
· качественный материал должен изготавливаться с соблюдением всей технологии.
усиление композитными материалами применяется в работе с конструкциями из дерева, бетона, металла, железобетона. Выделяют следующие области применения усиления углеволокном:
· в проектировании оно обеспечивает повышение несущей способности конструкции и ее прочность;
· повышает уровень сейсмостойкости здания;
· позволяет увеличить межремонтные промежутки времени;
· в реконструкционных работах используется в качестве армирующего материала для несущих конструкций;
· позволяет устранить последствия коррозий, крошения и другого нарушения целостности кладки из бетона либо камня.
Проводить усиление строительной конструкции необходимо в следующих случаях:
· в ходе перепланировки и изменения функций конструкции;
· при необходимости увеличения количества этажей в здании;
· когда отельные элементы и материалы со временем износились в ходе эксплуатации и под воздействие факторов окружающей среды;
· при повреждении конструкции;
· необходимость усиления строения после аварий.
Усиление конструкции строения данным способом имеет ряд преимуществ, главным из которых можно выделить увеличение несущей способности конструкции в 4 раза, чего не удается достичь при использовании других методов. Кроме того, к достоинствам относится:
· так как вес используемого материала сравнительно небольшой, в работе можно обойтись без специального оборудования и техники;
· углеволокно не поддается влиянию факторов окружающей среды, поэтому сроки его эксплуатации достигают 75 лет;
· применение данного материала не увеличивает нагрузку на саму конструкцию, так как данный усилитель имеет небольшой вес;
· волокно создает водонепроницаемый слой, тем самым защищая арматуру от коррозий, а бетон от влаги;
· простота работы с материалом сокращает сроки необходимые на выполнение укрепительных работ;
· финансовая экономия;
· сведение трудозатрат к минимуму.
Начало работ по усилению здания заключается в выявлении слабых элементов конструкции. Далее выполняется разметка и подготовка конструкции к усилению. Зоны, которые будут покрываться материалом, очищаются и шлифуются. Только на подготовленную поверхность монтируется материал.
Рост популярности пластиков, армированных углеродным волокном
Углеродные волокна в пластиковых материалах
Использование углеродных волокон в пластиковых материалах имеет долгую историю. Еще в 1879 году Томас Эдисон экспериментировал с углеродными волокнами, изготовленными из хлопковых нитей и бамбуковых щепок. Фактически, первая лампа накаливания, нагреваемая электричеством, содержала углеродные волокна.
В 1960-х годах доктор Акио Синдо из Агентства промышленных наук и технологий Японии разработал углеродное волокно на основе полиакрилонитрила (ПАН).Полученное волокно содержало 55% углерода.
Процесс конверсии на основе ПАН быстро стал основным методом производства углеродного волокна. Сегодня девяносто процентов углеродных волокон изготавливаются из полиакрилонитрила (C 3 H 3 N) n или ПАН, синтетической полукристаллической органической полимерной смолы. Остальные 10% изготавливаются из искусственного шелка или нефтяного пека. Волокна из ПАН очень прочные и легкие. Эти волокна связаны термореактивными или термопластичными полимерами, такими как полиэстер, виниловый эфир или нейлон, для получения пластика, армированного углеродным волокном, или углеродного FRP.
Добавление углеродного волокна к полимеру дает много преимуществ
Прочность на растяжение и модуль изгиба увеличиваются, как и температура теплового прогиба или HDT. Кроме того, добавление армирования углеродным волокном уменьшает усадку и коробление.
Каждое углеродное волокно представляет собой длинную тонкую прядь, состоящую из тысяч углеродных нитей. Одиночное волокно имеет диаметр около 5-10 мкм и состоит в основном из углерода. Микроскопические кристаллы углерода связаны друг с другом в структуру, которая более или менее выровнена параллельно длинной оси волокна.Именно такое расположение кристаллов делает волокна такими прочными.
Классификация по модулю растяжения
Углеродные волокна классифицируются по модулю растяжения * волокна. Модуль упругости может варьироваться от 34,8 млн фунтов на квадратный дюйм до 72,5-145,0 млн фунтов на квадратный дюйм. Сталь имеет модуль растяжения 29 миллионов фунтов на квадратный дюйм, поэтому самое прочное углеродное волокно в пять раз прочнее стали.
Низкомодульные волокна
имеют модуль упругости при растяжении ниже 34,8 миллионов фунтов на квадратный дюйм (240 миллионов кПа).Волокна также классифицируются в порядке возрастания модуля упругости на «стандартный модуль», «промежуточный модуль», «высокий модуль» и «сверхвысокий модуль». Углеродные волокна с классификацией сверхвысокого модуля имеют модуль упругости 72,5-145,0 миллионов фунтов на квадратный дюйм (500 миллионов-1,0 миллиардов кПа).
Прядение, стабилизация, карбонизация, обработка поверхности и калибровка
Процесс производства углеродного волокна является частично химическим и частично механическим.
- Вращение: PAN вращается с использованием одного из нескольких процессов вращения.Этот шаг важен, потому что он формирует внутреннюю атомную структуру волокна. Затем волокна промывают и растягивают до необходимого диаметра. Растяжение также помогает выровнять молекулы, чтобы помочь в формировании кристаллов углерода, созданных карбонизацией.
- Стабилизация: На этом этапе волокна обрабатываются химическими веществами, чтобы изменить их линейное соединение на термостабильную структуру лестничного соединения. Затем нити нагревают на воздухе, чтобы они захватили молекулы кислорода и изменили схему атомных связей.
- Карбонизация: Волокна затем подвергаются воздействию очень высокой температуры без присутствия кислорода, поэтому волокно не может гореть.
Атомы в волокне сильно вибрируют, выталкивая большую часть неуглеродных атомов в предшественнике. - Обработка поверхности: После карбонизации поверхность волокон плохо сцепляется с материалами, используемыми при изготовлении композитных материалов. На этом этапе поверхность волокон слегка окисляется погружением в различные газы или жидкости.
- Проклейка: В этом процессе на волокна наносится покрытие, защищающее их от повреждений во время намотки или ткачества.
Несколько продуктов, изготовленных из углеродных волокон, — это удочки, велосипеды, оборудование для гольфа, теннисные ракетки, детали для самолетов, мостов и автомобилей.
* Модуль упругости – это сила растяжения, которую может оказывать волокно определенного диаметра без разрыва. Модуль упругости описывается в фунтах на квадратный дюйм или фунтах на квадратный дюйм.
Вопросы? Дайте мне знать в разделе комментариев ниже.
Ищете дополнительную информацию о пластмассах? Загрузите наше бесплатное руководство!
Работа с армирующими материалами из углеродного волокна
Меры предосторожности
Прежде всего, остерегайтесь осколков! Мы рекомендуем надевать перчатки при работе с углеродным волокном или его резке. Мелкие осколки очень острые и довольно хрупкие. Из-за этого осколки очень трудно удалить, поскольку они часто крошатся и ломаются, когда вы пытаетесь их извлечь.
Как и в случае с большинством материалов, пыль, образующаяся при резке или механической обработке углеродного волокна, опасна. Всегда носите пылезащитную маску, чтобы мелкие частицы пыли не попали в легкие и носовые проходы. Защитные очки также необходимы всякий раз, когда вы выполняете операции по резке.
Механическая обработка
Углеродное волокно — очень твердое, хрупкое вещество, которое затупляет режущие кромки ваших инструментов.
Если вам просто нужно укоротить кусок углеродного волокна, мы рекомендуем использовать ножовку, чтобы отрезать его до нужной длины.Мы НЕ рекомендуем использовать электроинструменты для резки углеродного волокна, если в этом нет крайней необходимости.
Если вы решили использовать электроинструмент для резки углеродного волокна, используйте абразивные диски или круги. Производители углеродного волокна используют лазеры или гидроабразивные резаки.
Склеивание
Вы можете использовать цианоакрилаты (суперклей), эпоксидные смолы или клей для дерева.
Типичное использование
Углеродное волокно в основном используется при изготовлении и ремонте струнных инструментов для усиления грифа.Конструкция и размеры грифа, анкерного стержня (если он есть) и другие аспекты помогут определить, какой кусок углеродного волокна подходит.
В показанных примерах вы заметите, что арматурные стержни расположены вдали от анкерного стержня.
Это придает шее большую устойчивость и уменьшает скручивание. Ниже приведены некоторые типичные примеры и используемое углеродное волокно:
.
Пример #1: Это больше относится к ситуации ремонта, но также может быть применено к новой шейке, которая не имеет усиливающего стержня.Снимите накладку грифа с инструмента и прорежьте канал в грифе, чтобы принять арматурный стержень # 4401 (1/8″ x 3/8″ x 18″). В этом или любом из следующих материалов можно использовать любой из рекомендуемых клеев. ситуации
Пример № 2 и № 3: Вот две современные конструкции грифа, в которых используется регулируемый анкерный стержень и два усиливающих стержня для обеспечения жесткости и устойчивости. Размеры поперечного сечения грифа определят, какой пример лучше всего подходит для инструмента № 2 или № 3.Пример №3 показывает, как можно усилить 5- или 6-струнный бас. Многие современные тонкие грифы также требуют настройки, как в примере №3.
Пример №4: Это подход в первую очередь для 5- и 6-струнных бас-гитар, где используются два анкерных стержня в сочетании с тремя усиливающими стержнями. Два анкерных стержня обеспечивают больший контроль над грифом и помогают контролировать деформацию или скручивание. Усиливающие стержни делают гриф намного более жестким, но при этом позволяют анкерным стержням манипулировать грифом по мере необходимости.
Механизмы снижения трения и износа за счет армирования ПЭЭК углеродным волокном
1. Чанд, С.: Обзор углеродных волокон для композитов. Дж. Матер. науч. 35 (6), 1303–1313 (2000). doi:10.1023/a:1004780301489
Артикул
Google Scholar
2. Масуэлли, Массачусетс: Внедрение армированных волокном полимеров — полимеров и композитов: концепции, свойства и процессы.В: Масуэлли, М. (ред.) Полимеры, армированные волокном — технология, применяемая для ремонта бетона.
(2013). дои: 10.5772/54629
3. Giltrow, J.P., Lancaster, J.K.: Полимеры, армированные углеродным волокном, как самосмазывающиеся материалы. В: Труды конференции Института инженеров-механиков, том. 182, нет. 14, стр. 147–157 (1967). дои: 10.1243/pime_conf_1967_182_417_02
4. Flöck, J., Friedrich, K., Yuan, Q.: О трении и износе композитов PEEK, армированных PAN и углеродным волокном.Носите 225–229 , 304–311 (1999). дои: 10.1016/S0043-1648(99)00022-8
Артикул
Google Scholar
5. Чжан, Г., Рашева, З., Шларб, А.К.: Изменения трения и износа короткого углеродного волокна (SCF)/ПТФЭ/графита (10 об.%), наполненного ПЭЭК: влияние ориентации волокна и номинального контакта давление. Носите 268 (7–8), 893–899 (2010 г.). doi: 10.1016 / j.wear.2009.12.001
Артикул
Google Scholar
6.
Schön, J.: Коэффициент трения алюминия при контакте с эпоксидным композитом из углеродного волокна. Трибол. Междунар. 37 (5), 395–404 (2004). doi:10.1016/j.triboint.2003.11.008
Артикул
Google Scholar
7. Фосс, Х., Фридрих, К.: О характеристиках износа ПЭИК-композитов, армированных коротким волокном. Носите 116 (1), 1–18 (1987). дои: 10.1016/0043-1648(87)
-6
Артикул
Google Scholar
8. Li, J., Xia, Y.C.: Эффект армирования углеродным волокном на свойства трения и износа композитов PA6, армированных углеродным волокном. Волокна Полим. 10 (4), 519–525 (2009). дои: 10.1007/s12221-009-0519-5
Артикул
Google Scholar
9. Zhang, X., Pei, X., Mu, B., Wang, Q.: Влияние обработки поверхности углеродного волокна на прочность на изгиб и трибологические свойства коротких композитов углеродное волокно/полимид.
Серф. Анальный интерфейс. 40 (5), 961–965 (2008). дои: 10.1002/sia.2846
Артикул
Google Scholar
10. Zhang, X.R., Pei, X.Q., Wang, Q.H.: Влияние окисления волокна на трение и износ короткорезанных углеродных волокон/полимидных композитов. Экспресс Полим. лат. 1 (5), 318–325 (2007). doi:10.3144/expresspolymlett.2007.45
Артикул
Google Scholar
11. Хан, Ю., Шмитт, С., Фридрих, К.: Микротрение различных фаз в композитной смеси углеродного волокна, политетрафторэтилена, графита и полиэфиркетона, измеренное с помощью атомно-силовой микроскопии. Трибол. Междунар. 31 (12), 715–725 (1998). дои: 10.1016/s0301-679x(98)00051-6
Артикул
Google Scholar
12. Han, Y., Schmitt, S., Friedrich, K.: Наноразмерные вдавливания и царапины на композитной смеси PEEK/PTFE, армированной коротким углеродным волокном, с помощью литографии на атомно-силовом микроскопе.
заявл. Композиции Матер. 6 (1), 1–18 (1999). doi:10.1023/a:1008812915701
Артикул
Google Scholar
13. Молаземхоссейни, А., Турани, Х., Наими-Джамал, М.Р., Хаванди, А.: Наноиндентирование и реакция на наноцарапание гибридных композитов на основе ПЭЭК, армированных короткими углеродными волокнами и нанокремнеземом. Полим. Контрольная работа. 32 (3), 525–534 (2013). doi:10.1016/j.polymertesting.2013.02.001
Артикул
Google Scholar
14. Лин, Л.Ю., Тлатлик, Х., Гралла, Р., Игартуа, М.А., де Баетс, П., Шларб, А.К.: Механические и термические свойства многомасштабных композитов на основе полиэфиркетона. Дж. Компос. Матер. 47 (17), 2087–2096 (2013). дои: 10.1177/0021998312454317
Артикул
Google Scholar
15. Ji, M., Wang, C.
, Bai, Y., Yu, M., Wang, Y.: Структурная эволюция волокон-предшественников полиакрилонитрила во время предварительного окисления и карбонизации.Полим. Бык. 59 , 527–536 (2007). doi: 10.1007/s00289-007-0773-x
Артикул
Google Scholar
16. Savage, R.H.: графитная смазка. Дж. Заявл. физ. 19 (1), 1–10 (1948)
Артикул
Google Scholar
17. Роу, Г.В.: Некоторые наблюдения за фрикционным поведением нитрида бора и графита. Носите 3 (4), 274–285 (1960).дои: 10.1016/0043-1648(60)-1
Артикул
Google Scholar
18. Pei, X.-Q., Bennewitz, R., Busse, M., Schlarb, A.K.: Влияние геометрии с одной неровностью на трение и износ PEEK. Wear 304 (1–2), 109–117 (2013). doi: 10.1016 / j.wear.2013.04.032
Артикул
Google Scholar
19.
Мазеран, П.-Э., Лубе, Ж.-Л.: Нормальная и латеральная модуляция с помощью сканирующего силового микроскопа, анализ: влияние на количественную визуализацию упругости и трения. Трибол. лат. 7 (4), 199–212 (1999). doi:10.1023/a:1019142025011
Артикул
Google Scholar
20. Боуден Ф.П., Табор Д.: Трение, смазка и износ: обзор работы за последнее десятилетие. бр. Дж. Заявл. физ. 17 (12), 1521–1544 (1966)
Артикул
Google Scholar
21. Стюарт, Б.Х., Бриско, Б.Дж.: Исследования стойкости к царапинам полиэфиркетона. Полимер 37 (17), 3819–3824 (1996). дои: 10.1016/0032-3861(96)00212-1
Артикул
Google Scholar
22. Шредер, Р., Торрес, Ф.В., Биндер, К., Кляйн, А.Н., де Мелло, Дж.Д.Б.: Характер разрушения при скользящем износе композитов на основе ПЭЭК.
Износ 301 (1–2), 717–726 (2013 г.). doi: 10.1016 / j.wear.2012.11.055
Артикул
Google Scholar
23. Zhang, JG, Cai, CL: Трение и износостойкость композитов PEEK, армированных углеродным волокном, при смазывании водой. заявл. мех. Матер. 66–68 , 1051–1054 (2011)
Google Scholar
24. Эллиотт, Д.М., Фишер, Дж., Кларк, Д.Т.: Влияние шероховатости поверхности сопряжения и ее эволюция на износ и трение композитов из ПЭЭК и углеродного волокна, связанных с ПЭЭК, на нержавеющей стали. Носите 217 (2), 288–296 (1998).дои: 10.1016/S0043-1648(98)00148-3
Артикул
Google Scholar
25. Шриниваса, В., Шивакумар, В., Наяка, В., Джагадишаи, С., Ситрам, М., Шеной, Р., Нафиди, А.: Морфология разрушения композитных ламинатов, армированных углеродным волокном .
Матер. Рез. 13 , 417–424 (2010)
Статья
Google Scholar
26. Оверт Т.C.: О характеристиках износа продольно (параллельно) ориентированных однонаправленных полимерных композитов, армированных волокном. Трибол. Транс. 38 (1), 27–34 (1995). дои: 10.1080/10402009508983376
Артикул
Google Scholar
27. Ovaert, T.C.: Износ однонаправленных полимерных матричных композитов с ориентацией волокон в плоскости контакта. Трибол. Транс. 40 (2), 227–234 (1997). дои: 10.1080/10402009708983649
Артикул
Google Scholar
28. Чжан, Х., Чжан, З., Фридрих, К.: Влияние длины волокна на износостойкость коротких эпоксидных композитов, армированных углеродным волокном. Композиции науч. Технол. 67 (2), 222–230 (2007). doi: 10.1016/j.compscitech.
2006.08.001
Артикул
Google Scholar
Углеродное волокно для ремонта конструкций
Углеродное волокно — самый прочный искусственный материал в мире. Уже один этот факт примечателен. Но тот факт, что им можно манипулировать множеством способов, в том числе для использования в космических челноках, самолетах, дорогих автомобилях и различном спортивном оборудовании, таком как клюшки для гольфа, а также для ремонта и укрепления бетона и кирпичной кладки, не менее примечателен.
Наряду с большой прочностью углеродного волокна достигается удивительная легкость. Отдельные жгуты, которые обычно сотканы вместе для формирования ткани, состоят из нитей углеродного волокна. Жгуты обычно содержат 12 000, а иногда даже 24 000 отдельных нитей углеродного волокна. Нити представляют собой волокна диаметром около 5–10 микрометров (единица, также известная как микрон — одна миллионная метра или одна тысячная миллиметра) и состоят в основном из атомов углерода, одного из самых легких известных элементов.
Углеродные волокна восходят к 1860 году, когда они были впервые произведены для лампочек путем обжига хлопчатобумажных нитей в процессе, известном как карбонизация, процесс, при котором тепло применяется в среде с недостатком кислорода, чтобы материал не воспламенялся.
Углеродное волокно часто изготавливают из прекурсора полимера, известного как полиакрилонитрил, искусственный шелк или нефтяной пек. Для строительных применений этот предшественник превращается в арматуру, ткань и пластины или листы. Пластины обычно четыре дюйма в ширину и 0.04 дюйма толщиной (меньше толщины десятицентовой монеты) и может иметь прочность, приближающуюся к 10-кратному пределу прочности на растяжение стали с давлением 60 000 фунтов на квадратный дюйм.
Само собой разумеется, поскольку производственные затраты снизились, продукт с таким количеством прочности и таким низким профилем теперь используется для решения ряда проблем в области жилищного строительства. Искривленные стены, потрескавшиеся стены и плиты, а также сломанные углы можно отремонтировать с помощью углеродного волокна.
Однонаправленные ремни из углеродного волокна используются для усиления и придания жесткости этому настилу бриджа.
Новые исследования и рекомендации
Использование армированных волокном полимерных (FRP) композитов для армирования и ремонта бетонных конструкций быстро растет в течение последнего десятилетия или около того. За последние 20 или 25 лет большая часть углеродного волокна монтировалась на поверхность. Когда материал монтируется на поверхность, полосы или листы прикрепляются к поверхности по мере необходимости аналогично обоям, а затем приклеиваются к подложке.
Комитет 440 Американского института бетона по полимерам, армированным волокном, изучает вопрос крепления углеродного волокна.Тодд Джексон, соучредитель Fortress Stabilization Systems в Голландии, штат Мичиган, входит в Комитет 440 и наблюдает за изменениями в отрасли в отношении рекомендаций по поверхностному монтажу углеродного волокна. «Я считаю, что в течение следующих пяти лет все углеродное волокно будет закреплено», — говорит Джексон.
Когда углеродное волокно монтируется на поверхность, ACI снижает большую часть прочности углеродного волокна на 70 процентов из-за долговременной ползучести или расстегивания. Если углеродное волокно используется для наружных работ, таких как что-то вроде моста, углерод со временем подвергается дальнейшей деградации из-за влажности, ультрафиолетового излучения и т. д.Тем не менее, исследования показывают, что если углеродное волокно механически закрепить (для этого изучаются различные способы), вы можете использовать его прочность на 100%. На веб-сайте, разработанном Джексоном, www.carbonanchor.com, рассказывается об испытаниях, проведенных в Университете Майами, на предмет того, как анкеровка увеличивает прочность углеродного волокна.
Вся отрасль также стремится получить одобрение ICC-ES для всех своих продуктов. В коммерческом мире большинство строительных чиновников хотят получить одобрение ICC для любого используемого продукта, но в жилом мире это отстает.
«Они пытаются регулировать это немного больше, чтобы люди знали, что материал делает то, для чего он был разработан», — говорит Джексон.
«Поскольку популярность армирования FRP сохраняется, в [Интернете] можно найти многих дистрибьюторов этих систем, и заявленные значения могут быть неизвестны. В жилом мире поставщики настаивают на том, чтобы их продукция была одобрена ICC. Это дает чиновникам и домовладельцам уверенность в том, что эти продукты являются одобренными и протестированными системами».
Ткань из углеродного волокна
— лучший выбор, когда нагрузка исходит из нескольких направлений, как, например, эта обернутая опорная колонна.
Больше, чем просто инъекции
Джарред Джонс, директор по проектированию и разработке продуктов Rhino Carbon Fiber, говорит, что подрядчики по ремонту начинают использовать больше тканей из углеродного волокна в дополнение к инъекционным работам по герметизации трещин. По сравнению со стальными балками, стеновыми анкерами и другими традиционными методами стабилизации стен, углеродное волокно намного быстрее и проще в установке.
«Что касается ремонта трещин, многие ребята сейчас не делают инъекцию, не установив поверх нее заделку трещин из углеродного волокна», — говорит Джонс.
«Это дополнительный уровень защиты и добавляет прочности ремонту». Это также хороший метод, который можно использовать, если подрядчик сталкивается с проблемой впрыска или ремонтирует чужую инъекцию, где у него все еще есть проблема с утечкой. Однако, как и в большинстве других методов ремонта, любая вода, протекающая через стену, должна быть остановлена, чтобы обеспечить адекватное сцепление с эпоксидной смолой. Обычно этого можно добиться, выполняя работы в сухой период, используя гидравлический цемент или какой-либо другой метод гидроизоляции.
Скобы и швы
Для ремонта трещин у Rhino есть три варианта: инъекции эпоксидной смолы, ткань, которая может быть нанесена на саму трещину, и их углеродное волокно Concrete Crack Lock, которое Джонс описывает как «стежок», чтобы придать дополнительную прочность ремонту и заблокировать трещину. на месте и не позволяйте ему двигаться.
Для установки Crack Lock установщики вырезают в бетоне тонкую щель перпендикулярно трещине и просверливают два небольших отверстия на каждом конце.
Затем они заполняют разрез эпоксидной смолой Rhino и вставляют Crack Lock в разрез.
«Мы уже давно проповедуем, что для ремонта нужно сделать нечто большее, чем просто инъекцию», — говорит он. «Обычно, если инъекция не удалась, проблема не в инъекции, а в бетоне, прилегающем к ней. Так что, если вы сможете преодолеть это и удержать все вместе, ваш показатель успеха резко возрастет».
Джексон из Fortress также занимается исследованием скоб из углеродного волокна. Его компания разработала «штапельный» анкер из углеродного волокна как средство крепления внешних листов FRP к бетону.Названные Fortec, они доступны в двух разных типах: плоские и круглые. Оба были тщательно протестированы в Университете Майами и Политехническом университете Милана в широком диапазоне обстоятельств и условий. (Полные отчеты об испытаниях доступны в онлайн-версии этой статьи.)
Оба типа анкеров поставляются в виде предварительно изготовленных элементов, которые вставляются в отверстия в бетоне, заполненные эпоксидной смолой.
Оба продукта преследуют одну и ту же цель: улучшить сцепление наружных ламинатов FRP с бетонным основанием.
Плоская скоба менее навязчива и требует меньшего шлифования, чтобы закрепить ее на одном уровне с бетоном. Как и все типы углеродного волокна, после отверждения его можно покрыть паржом, облицовкой кирпичом или покрасить для улучшения эстетики. Он устанавливается так же, как прямые углеродные пластины или сетки.
Типичный якорь имеет длину шесть дюймов и ширину два дюйма с ножками в один дюйм. Анкеры состоят из высокопрочного углеродного волокна, инкапсулированного в термоотверждаемую смолу.К ленте приклеивается отслаивающаяся ткань, которая при снятии оставляет подготовленную склеивающую поверхность для приклеивания к подготовленной подложке. Анкеры можно использовать там, где колонны соприкасаются со стенами, стыки на потолках и там, где требуется дополнительная прочность соединения в подвесных конструкциях.
Новые продукты были разработаны для механического крепления углеродного волокна к бетону, что позволяет сделать ремонт трещин более прочным, чем когда-либо прежде.
Более 500 квадратных метров углеродного волокна было использовано для ремонта этого торгового объекта.Выполненный за 11 дней, бригада из трех человек использовала строительные леса высотой более 20 футов, чтобы добраться до места ремонта.
Углеродное волокно используется во всем мире для ремонта всех типов зданий и сооружений, включая жилые подвалы, мосты и путепроводы, многоэтажки и гаражи. Недавно его использовали для ремонта торгового объекта на острове Маврикий в Индийском океане.
Джарред Джонс сообщает: «Компания PND Contracting связалась с Rhino Carbon Fiber по поводу проекта усиления балки на острове Маврикий, небольшой африканской стране в Индийском океане.В магазине Shop Rite в торговом парке Trianon произошел катастрофический пожар, повредивший бетонную конструкцию».
Когда подрядчик-реставратор ПНД начал работы по ремонту конструкции, инженер владельца обнаружил повреждения основных и вспомогательных балок, поддерживающих крышу, что значительно снизило их прочность.
Инженер владельца определил, что для компенсации этого снижения прочности можно использовать полимер, армированный углеродным волокном (CFRP).PND связалась с Rhino за помощью.
Джонс говорит: «Работая с подрядчиком и инженером владельца, команда Rhino смогла предоставить PND структурный проект с печатью США, который удовлетворял всем требованиям проекта». Инженер владельца рассмотрел и принял проект, после чего можно было приступить к работе.
Владельцы, по понятным причинам, хотели, чтобы проект был завершен как можно скорее, и из-за логистики доставки материалов изолированному островному государству материалы необходимо было отправить на Маврикий до завершения окончательного проекта.Эта поставка была основана на предварительных проектных работах, и ее нужно было разобрать и очень точно упаковать, чтобы соответствовать правилам авиаперевозок.
Представитель Rhino также посетил остров, чтобы убедиться, что установка прошла гладко, ответить на вопросы и обеспечить точное соблюдение конструкции и процесса нанесения.
Проект, включающий более 500 квадратных метров углепластика, был завершен за 11 дней с помощью бригады из трех человек, работающих на строительных лесах высотой более 20 футов.
По завершении установки углеродного волокна инженер владельца провел испытания крыши под нагрузкой и обнаружил лишь часть ожидаемого прогиба.
Джонс заключает: «Благодаря немедленной доступности материала, быстрому изменению конструкции конструкции и готовности Rhino наблюдать за установкой, это был очень успешный проект не только для Rhino, но и для PND Contracting и собственник.»
Ванесса Сальвиа — независимый писатель, специализирующийся на строительной отрасли.Ее работа базируется в Юджине, штат Орегон, и публикуется во многих национальных и региональных публикациях.
Произошла ошибка при настройке пользовательского файла cookie
Этот сайт использует файлы cookie для повышения производительности. Если ваш браузер не принимает файлы cookie, вы не можете просматривать этот сайт.
Настройка браузера для приема файлов cookie
Существует множество причин, по которым файл cookie не может быть установлен правильно. Ниже приведены наиболее распространенные причины:
- В вашем браузере отключены файлы cookie.Вам необходимо сбросить настройки браузера, чтобы принять файлы cookie, или спросить вас, хотите ли вы принимать файлы cookie.
- Ваш браузер спрашивает, хотите ли вы принимать файлы cookie, и вы отказались.
Чтобы принять файлы cookie с этого сайта, нажмите кнопку «Назад» и примите файл cookie. - Ваш браузер не поддерживает файлы cookie. Попробуйте другой браузер, если вы подозреваете это.
- Дата на вашем компьютере в прошлом. Если часы вашего компьютера показывают дату до 1 января 1970 г.,
браузер автоматически забудет файл cookie.Чтобы это исправить, установите правильное время и дату на своем компьютере. - Вы установили приложение, которое отслеживает или блокирует установку файлов cookie.

Вы должны отключить приложение при входе в систему или проконсультироваться с системным администратором.
Почему этому сайту требуются файлы cookie?
Этот сайт использует файлы cookie для повышения производительности, запоминая, что вы вошли в систему, когда переходите со страницы на страницу. Предоставить доступ без файлов cookie
потребует от сайта создания нового сеанса для каждой посещаемой вами страницы, что замедляет работу системы до неприемлемого уровня.
Что сохраняется в файле cookie?
Этот сайт не хранит ничего, кроме автоматически сгенерированного идентификатора сеанса в файле cookie; никакая другая информация не фиксируется.
Как правило, в файле cookie может храниться только та информация, которую вы предоставляете, или выбор, который вы делаете при посещении веб-сайта. Например, сайт
не может определить ваше имя электронной почты, если вы не решите ввести его.
Разрешение веб-сайту создавать файлы cookie не дает этому или любому другому сайту доступ к
остальной части вашего компьютера, и только сайт, создавший файл cookie, может его прочитать.
Новые марки Ultramid® Advanced с армированием углеродным волокном для легких и высокопроизводительных деталей
- Полифталамиды, армированные углеродным волокном (PPA), с превосходными механическими свойствами для замены алюминия и магния
- Для автомобильных конструкций, бытовой электроники и загруженного промышленного оборудования
В настоящее время компания BASF расширяет ассортимент полифталамидных (PPA) материалов Ultramid ® Advanced, добавляя марки, армированные углеродным волокном, с содержанием наполнителя 20, 30 и 40 процентов.Преимущества этих новых материалов: они делают детали чрезвычайно легкими, могут безопасно заменить алюминий и магний без потери жесткости и прочности, а также обладают электропроводностью.
Новые марки сочетают эти свойства с преимуществами Ultramid ® Advanced N (PA9T), что делает их уникальными среди PPA, армированных углеродным волокном, уже доступных на рынке: высокая размерная стабильность благодаря низкому поглощению воды, отличная химическая стойкость и устойчивость к гидролизу, высокая прочность и модуль.Новые марки, армированные углеродным волокном (CF), могут использоваться для производства автомобильных конструкционных деталей для кузова, шасси и трансмиссии, для насосов, вентиляторов, зубчатых передач и компрессоров в промышленности, а также для стабильных и сверхлегких компонентов в бытовой электронике. Этим предложением BASF дополняет свой портфель PPA, состоящий из более чем 50 марок, уже доступных на рынке.
Механические характеристики новых марок PPA, армированных углеродным волокном, можно регулировать путем выбора и содержания углеродного волокна, а также с помощью технологии присадок.Ultramid ® Advanced N3HC8 с 40% наполнителем из углеродного волокна демонстрирует лучшую прочность и модуль при 80°C (в кондиционированном состоянии), чем магний или алюминий.
«Наши новые компаунды PPA с углеродными волокнами являются идеальной заменой металла», — говорит Майкл Пиларски из отдела управления бизнесом PPA в BASF. «И это не только с точки зрения свойств материала. В последнее время мы наблюдаем проблемы с безопасностью у производителей магния в разных странах, что делает поставки довольно непредсказуемыми. Производство деталей из магния или алюминия также требует дополнительной постобработки и оснастки, которые увеличивает системные затраты.Учитывая возможность снижения веса на 25-30% с помощью наших новых марок PPA, мы можем предложить безопасную, экономичную и высокопроизводительную альтернативу деталям, традиционно изготавливаемым из металла».
Комбинируя эти новые материалы с программным обеспечением для моделирования BASF Ultrasim ® для правильного моделирования поведения деталей и оптимизации геометрии пресс-формы, сплавы Ultramid ® Advanced CF могут, таким образом, способствовать функциональной интеграции и снижению веса в различных отраслях промышленности: ряд автомобилей с e — привод или двигатели на топливных элементах могут быть увеличены за счет уменьшения веса деталей конструкции или силовой передачи; легкие, тонкие прецизионные конструкции в бытовой электронике выигрывают от высокой жесткости и прочности, превосходной размерной стабильности, а также чрезвычайно малого веса и хорошей технологичности новых материалов PPA; Тяжелое, высоконагруженное и долговечное промышленное оборудование, такое как насосы и компрессоры, может быть легко изготовлено благодаря хорошей размерной стабильности, а также высокой химической, термостойкости и стойкости к истиранию новых марок CF.
Композиции PPA, армированные углеродным волокном, также демонстрируют меньший вес и более высокий модуль упругости при растяжении, чем полиамиды (PA), армированные стекловолокном, с аналогичными армирующими элементами. Марки PPA, армированные 20% углеродных волокон, примерно на 20% легче, чем PA6 или PA66, наполненные 50% стекловолокна. Прочность на растяжение компаунда Ultramid ® Advanced, армированного на 20% углеродным волокном, лучше или эквивалентна полиамиду, армированному стекловолокном, наполненному на 50%, при этом демонстрируя лучшую технологичность.Ultramid ® Advanced N3HC8 напр. очень стабилен после старения при высоких температурах: он сохраняет почти 100% своего модуля упругости после теплового старения при 120°C в течение 5000 часов или при 150°C в течение 3000 часов.
Об Ultramid ® Advanced
Ассортимент полифталамидов BASF основан на четырех полимерах: Ultramid ® Advanced N (PA9T), Ultramid ® Advanced T1000 (PA6T/6I), Ultramid ® Advanced T2000 (PA6T/66) и давно используемом Ultramid .
® ТКР (PA6T/6).Они открывают дверь для следующего поколения легких, высокопроизводительных пластиковых компонентов во многих различных секторах, включая автомобильную промышленность, электронику и электрические устройства, машиностроение и товары народного потребления. Портфолио PPA доступно по всему миру и дополняется инструментом моделирования BASF Ultrasim ® и обширным опытом разработки приложений. Он включает более 50 компаундов для литья под давлением и экструзии, продукты с антипиренами или без них.Композиты доступны в различных цветах, от бесцветного до черного, маркируемого лазером, с армированием коротким стеклом, длинным стеклом или углеродным волокном, а также с различными термостабилизаторами.
Дополнительная информация: www.ultramid-advanced-n.basf.com и www.ppa.basf.com.
Растущая роль пластмасс, армированных углеродным волокном
Первоначально опубликовано на Examiner.com
С целью достижения установленного правительством показателя средней топливной экономичности, эквивалентного 54.
4 мили на галлон к 2025 году автопроизводители продолжают искать легкие и прочные материалы для использования в производственном процессе.
Более легкие автомобили помогают сократить расход топлива, а мощные автомобили обеспечивают большую безопасность пассажиров. Пластики, армированные углеродным волокном (CFRP), представляют собой группу передовых материалов, отвечающих обоим требованиям.
Пластик, армированный углеродным волокном: не только для гоночных автомобилей
Когда-то ограниченное миром автогонок из-за факторов стоимости и производства, углеродное волокно теперь начинает появляться в конструкции некоторых основных транспортных средств, и эта тенденция, вероятно, продолжится благодаря прорывам в исследованиях, которые, как ожидается, удешевят углепластик и другие композиты. и быстрее производить.
Они уже являются стабильной альтернативой
.
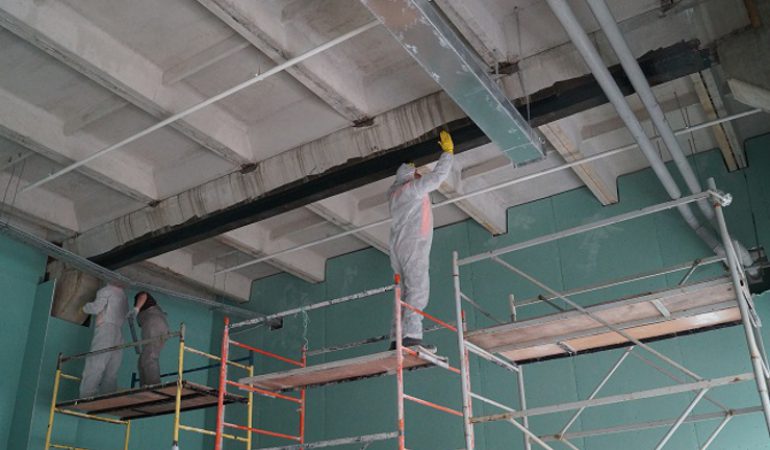

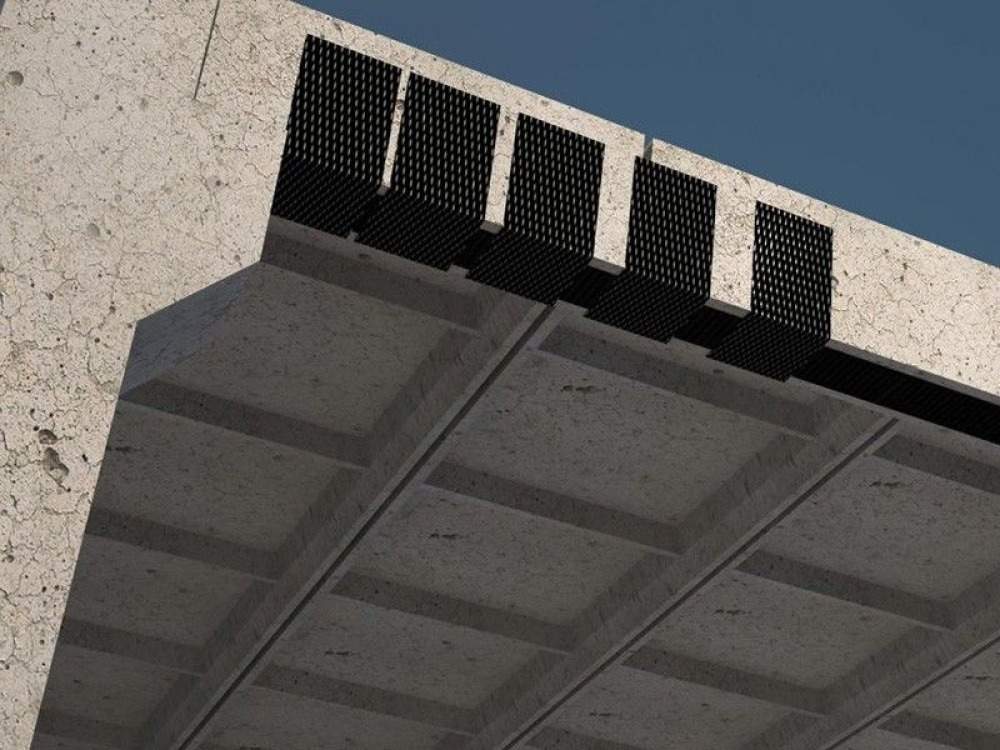


Чанд, С.: Обзор углеродных волокон для композитов. Дж. Матер. науч. 35 (6), 1303–1313 (2000). doi:10.1023/a:1004780301489
Артикул
Google Scholar
Масуэлли, Массачусетс: Внедрение армированных волокном полимеров — полимеров и композитов: концепции, свойства и процессы.В: Масуэлли, М. (ред.) Полимеры, армированные волокном — технология, применяемая для ремонта бетона. (2013). дои: 10.5772/54629
Giltrow, J.P., Lancaster, J.K.: Полимеры, армированные углеродным волокном, как самосмазывающиеся материалы. В: Труды конференции Института инженеров-механиков, том. 182, нет. 14, стр. 147–157 (1967). дои: 10.1243/pime_conf_1967_182_417_02
Flöck, J., Friedrich, K., Yuan, Q.: О трении и износе композитов PEEK, армированных PAN и углеродным волокном.Носите 225–229 , 304–311 (1999). дои: 10.1016/S0043-1648(99)00022-8
Артикул
Google Scholar
Чжан, Г., Рашева, З., Шларб, А.К.: Изменения трения и износа короткого углеродного волокна (SCF)/ПТФЭ/графита (10 об.%), наполненного ПЭЭК: влияние ориентации волокна и номинального контакта давление. Носите 268 (7–8), 893–899 (2010 г.). doi: 10.1016 / j.wear.2009.12.001
Артикул
Google Scholar

Schön, J.: Коэффициент трения алюминия при контакте с эпоксидным композитом из углеродного волокна. Трибол. Междунар. 37 (5), 395–404 (2004). doi:10.1016/j.triboint.2003.11.008
Артикул
Google Scholar
Фосс, Х., Фридрих, К.: О характеристиках износа ПЭИК-композитов, армированных коротким волокном. Носите 116 (1), 1–18 (1987). дои: 10.1016/0043-1648(87)
-6
Артикул
Google Scholar
Li, J., Xia, Y.C.: Эффект армирования углеродным волокном на свойства трения и износа композитов PA6, армированных углеродным волокном. Волокна Полим. 10 (4), 519–525 (2009). дои: 10.1007/s12221-009-0519-5
Артикул
Google Scholar
Zhang, X., Pei, X., Mu, B., Wang, Q.: Влияние обработки поверхности углеродного волокна на прочность на изгиб и трибологические свойства коротких композитов углеродное волокно/полимид. Серф. Анальный интерфейс. 40 (5), 961–965 (2008). дои: 10.1002/sia.2846
Артикул
Google Scholar
Zhang, X.R., Pei, X.Q., Wang, Q.H.: Влияние окисления волокна на трение и износ короткорезанных углеродных волокон/полимидных композитов. Экспресс Полим. лат. 1 (5), 318–325 (2007). doi:10.3144/expresspolymlett.2007.45
Артикул
Google Scholar
Хан, Ю., Шмитт, С., Фридрих, К.: Микротрение различных фаз в композитной смеси углеродного волокна, политетрафторэтилена, графита и полиэфиркетона, измеренное с помощью атомно-силовой микроскопии. Трибол. Междунар. 31 (12), 715–725 (1998). дои: 10.1016/s0301-679x(98)00051-6
Артикул
Google Scholar
Han, Y., Schmitt, S., Friedrich, K.: Наноразмерные вдавливания и царапины на композитной смеси PEEK/PTFE, армированной коротким углеродным волокном, с помощью литографии на атомно-силовом микроскопе. заявл. Композиции Матер. 6 (1), 1–18 (1999). doi:10.1023/a:1008812915701
Артикул
Google Scholar
Молаземхоссейни, А., Турани, Х., Наими-Джамал, М.Р., Хаванди, А.: Наноиндентирование и реакция на наноцарапание гибридных композитов на основе ПЭЭК, армированных короткими углеродными волокнами и нанокремнеземом. Полим. Контрольная работа. 32 (3), 525–534 (2013). doi:10.1016/j.polymertesting.2013.02.001
Артикул
Google Scholar
Лин, Л.Ю., Тлатлик, Х., Гралла, Р., Игартуа, М.А., де Баетс, П., Шларб, А.К.: Механические и термические свойства многомасштабных композитов на основе полиэфиркетона. Дж. Компос. Матер. 47 (17), 2087–2096 (2013). дои: 10.1177/0021998312454317
Артикул
Google Scholar
Ji, M., Wang, C. , Bai, Y., Yu, M., Wang, Y.: Структурная эволюция волокон-предшественников полиакрилонитрила во время предварительного окисления и карбонизации.Полим. Бык. 59 , 527–536 (2007). doi: 10.1007/s00289-007-0773-x
Артикул
Google Scholar
Savage, R.H.: графитная смазка. Дж. Заявл. физ. 19 (1), 1–10 (1948)
Артикул
Google Scholar
Роу, Г.В.: Некоторые наблюдения за фрикционным поведением нитрида бора и графита. Носите 3 (4), 274–285 (1960).дои: 10.1016/0043-1648(60)-1
Артикул
Google Scholar
Pei, X.-Q., Bennewitz, R., Busse, M., Schlarb, A.K.: Влияние геометрии с одной неровностью на трение и износ PEEK. Wear 304 (1–2), 109–117 (2013). doi: 10.1016 / j.wear.2013.04.032
Артикул
Google Scholar

Мазеран, П.-Э., Лубе, Ж.-Л.: Нормальная и латеральная модуляция с помощью сканирующего силового микроскопа, анализ: влияние на количественную визуализацию упругости и трения. Трибол. лат. 7 (4), 199–212 (1999). doi:10.1023/a:1019142025011
Артикул
Google Scholar
Боуден Ф.П., Табор Д.: Трение, смазка и износ: обзор работы за последнее десятилетие. бр. Дж. Заявл. физ. 17 (12), 1521–1544 (1966)
Артикул
Google Scholar
Стюарт, Б.Х., Бриско, Б.Дж.: Исследования стойкости к царапинам полиэфиркетона. Полимер 37 (17), 3819–3824 (1996). дои: 10.1016/0032-3861(96)00212-1
Артикул
Google Scholar
Шредер, Р., Торрес, Ф.В., Биндер, К., Кляйн, А.Н., де Мелло, Дж.Д.Б.: Характер разрушения при скользящем износе композитов на основе ПЭЭК. Износ 301 (1–2), 717–726 (2013 г.). doi: 10.1016 / j.wear.2012.11.055
Артикул
Google Scholar
Zhang, JG, Cai, CL: Трение и износостойкость композитов PEEK, армированных углеродным волокном, при смазывании водой. заявл. мех. Матер. 66–68 , 1051–1054 (2011)
Google Scholar
Эллиотт, Д.М., Фишер, Дж., Кларк, Д.Т.: Влияние шероховатости поверхности сопряжения и ее эволюция на износ и трение композитов из ПЭЭК и углеродного волокна, связанных с ПЭЭК, на нержавеющей стали. Носите 217 (2), 288–296 (1998).дои: 10.1016/S0043-1648(98)00148-3
Артикул
Google Scholar
Шриниваса, В., Шивакумар, В., Наяка, В., Джагадишаи, С., Ситрам, М., Шеной, Р., Нафиди, А.: Морфология разрушения композитных ламинатов, армированных углеродным волокном . Матер. Рез. 13 , 417–424 (2010)
Статья
Google Scholar
Оверт Т.C.: О характеристиках износа продольно (параллельно) ориентированных однонаправленных полимерных композитов, армированных волокном. Трибол. Транс. 38 (1), 27–34 (1995). дои: 10.1080/10402009508983376
Артикул
Google Scholar
Ovaert, T.C.: Износ однонаправленных полимерных матричных композитов с ориентацией волокон в плоскости контакта. Трибол. Транс. 40 (2), 227–234 (1997). дои: 10.1080/10402009708983649
Артикул
Google Scholar
Чжан, Х., Чжан, З., Фридрих, К.: Влияние длины волокна на износостойкость коротких эпоксидных композитов, армированных углеродным волокном. Композиции науч. Технол. 67 (2), 222–230 (2007). doi: 10.1016/j.compscitech. 2006.08.001
Артикул
Google Scholar

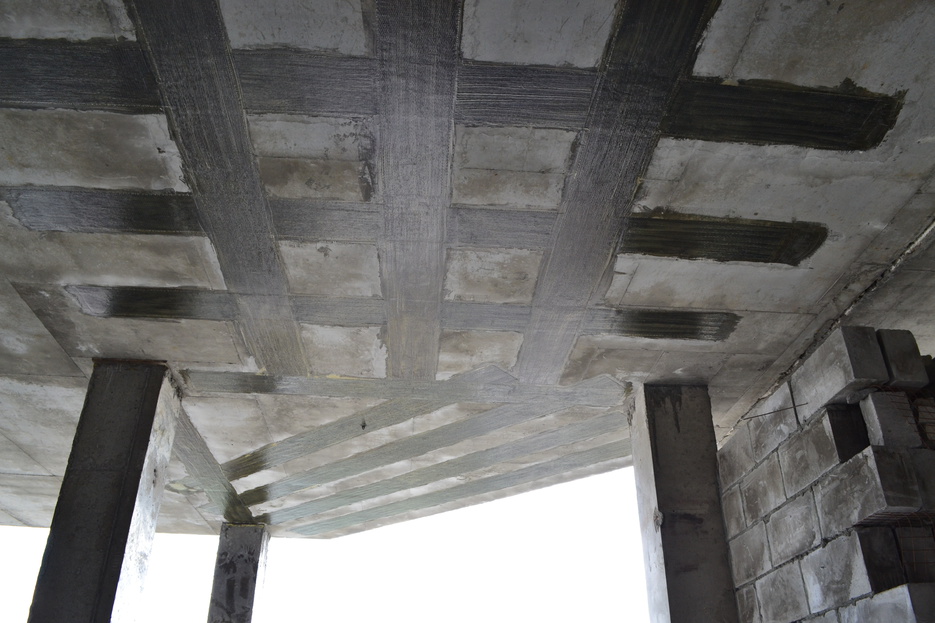
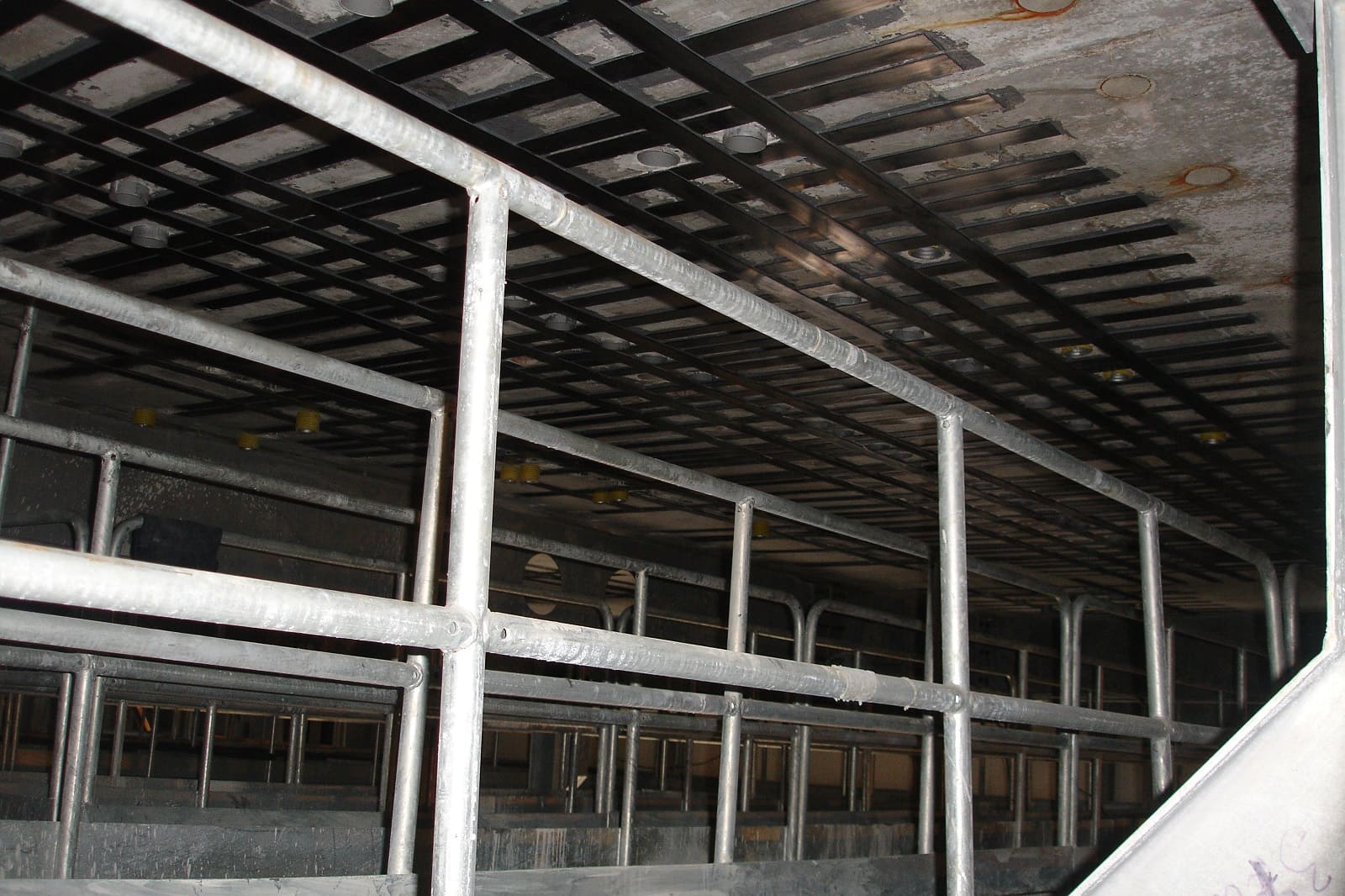



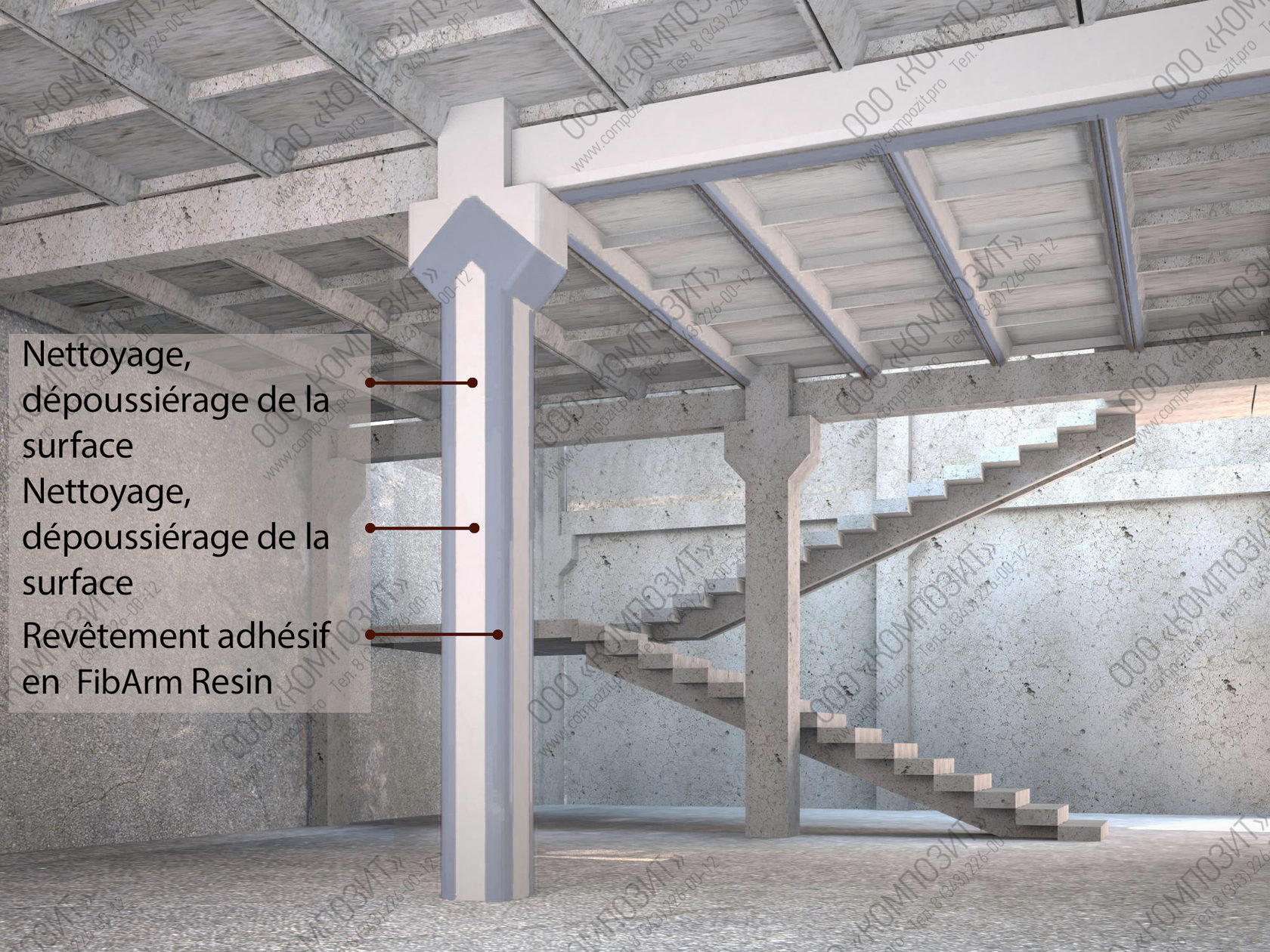

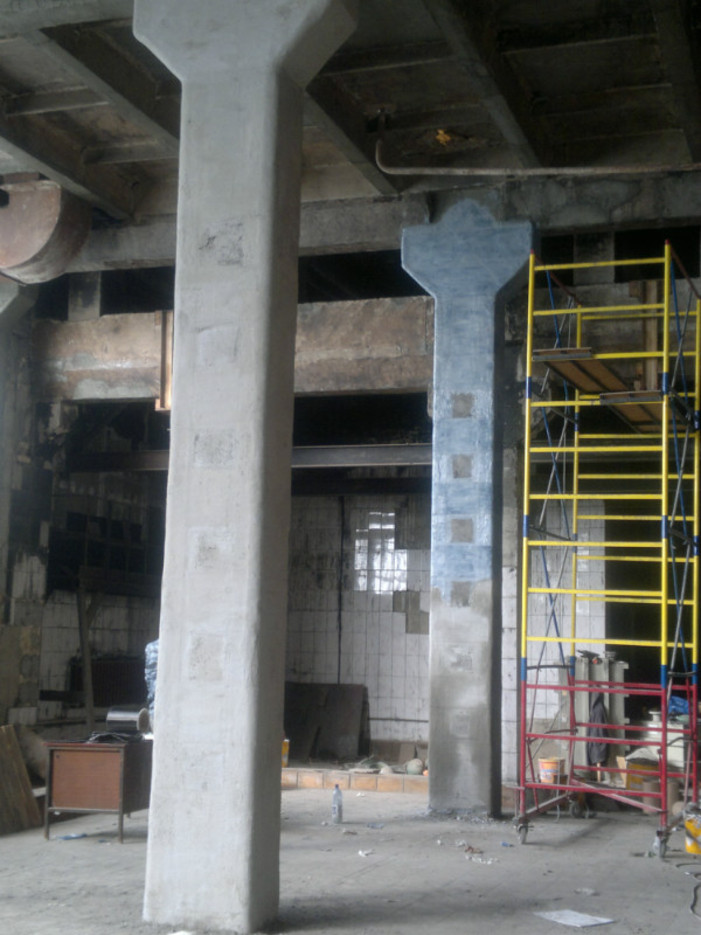


Чтобы принять файлы cookie с этого сайта, нажмите кнопку «Назад» и примите файл cookie.
браузер автоматически забудет файл cookie.Чтобы это исправить, установите правильное время и дату на своем компьютере.
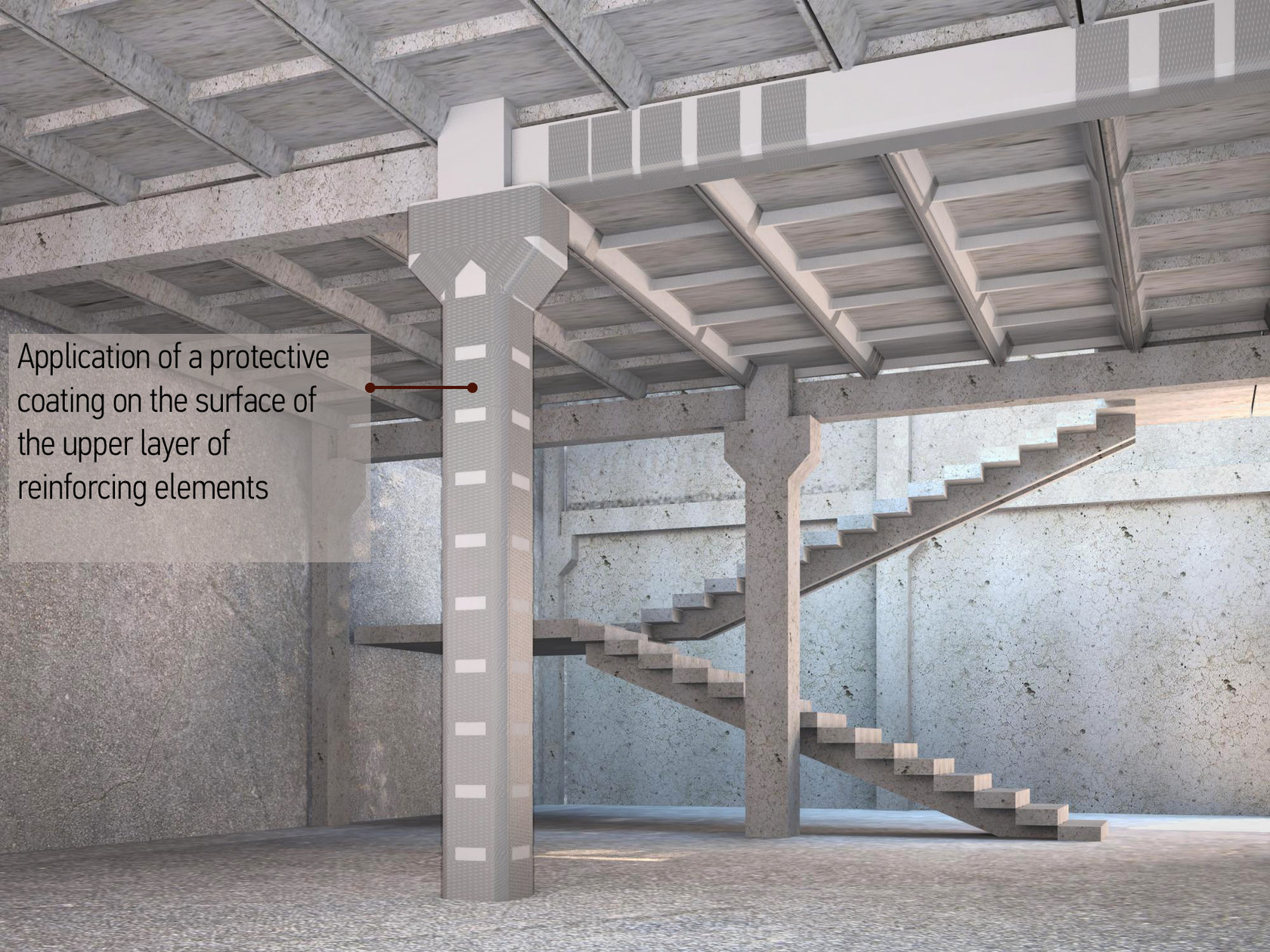
Вы должны отключить приложение при входе в систему или проконсультироваться с системным администратором.
потребует от сайта создания нового сеанса для каждой посещаемой вами страницы, что замедляет работу системы до неприемлемого уровня.
не может определить ваше имя электронной почты, если вы не решите ввести его.
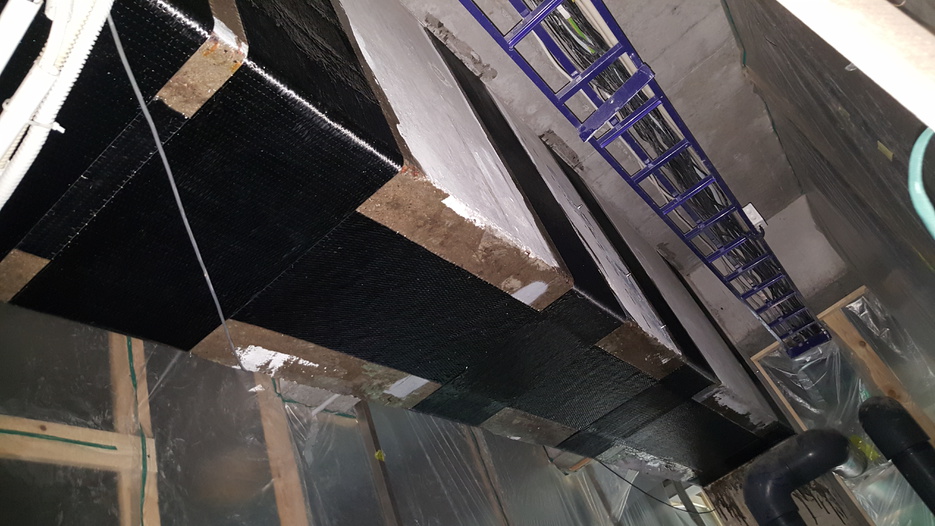
остальной части вашего компьютера, и только сайт, создавший файл cookie, может его прочитать.





GM уменьшил вес Chevrolet Corvette Stingray 2014 года на 37 фунтов, оснастив его капотом и крышей, усиленными углеродным волокном. Ford еще более широко использовал углеродное волокно в конструкции своего суперкара GT. И BMW обратилась к углеродному волокну для салонов своих первых полностью электрических автомобилей BMW i3 и i8, чтобы повысить эффективность использования топлива, а также безопасность.
Что такое углеродное волокно?
Что же это за чудо-материал?
По сути, углеродное волокно представляет собой очень тонкое, но исключительно прочное (вспомните алмазы) волокно, состоящее в основном из атомов углерода, которые можно связать вместе, чтобы сформировать нить, из которой затем можно сплести ткань.Его необходимо комбинировать с другими материалами для использования в производстве автомобилей или других предметов, требующих прочной и легкой конструкции, таких как фюзеляжи самолетов (например, Boeing 787 Dreamliner) или спортивного инвентаря. Но углеродное волокно чаще всего комбинируют с пластиком. Таким образом, правильным термином для материала является армированный углеродным волокном пластик (CFRP), но его часто называют просто углеродным волокном.
Автомобили F1 из углеродного волокна
Теннисные ракетки и клюшки для гольфа из углепластика
помогли изменить подход к этим видам спорта, а также произвели революцию в гоночных автомобилях Формулы-1, сделав их легче, прочнее, жестче, а их детали легче формовать в различные формы.
В легковых автомобилях его можно найти в таких компонентах, как задние спойлеры, капоты, крыши и даже внутренние детали, такие как приборная панель и внутренняя отделка. Косметически он может иметь привлекательный внешний вид при сохранении веса.
Значительное снижение веса
CFRP обычно на 30-50 процентов легче, чем обычные материалы, используемые в автомобилестроении, и, таким образом, может помочь потребителю сэкономить топливо. В целом, пластмассы и пластмассовые композиты составляют около 50 процентов объема типичного автомобиля, но только 10 процентов его веса.
В целом, пластмассы и пластмассовые композиты составляют около 50 процентов объема типичного автомобиля, но только 10 процентов его веса.
Несколько автопроизводителей делают ставку на широкое использование углепластика в своих будущих моделях автомобилей. Идея состоит в том, чтобы еще больше сократить вес автомобилей, а снижение веса на 10 процентов может привести к увеличению экономии топлива до 8 процентов.
В апреле Ford подписал соглашение с DowAksa, совместным предприятием 50:50 между Dow Chemical и Aksa Akrilik Kimya Sanayii A.Ş., чтобы вывести «углеродное волокно на более широкий рынок». Компания Aksa, базирующаяся в Ялове, Турция, является крупным производителем акриловых волокон, основного сырья для производства углеродных волокон.
Использование в водородных топливных баках
Toyota использовала топливные баки из углепластика при разработке своего электромобиля Mirai на топливных элементах, который будет доступен покупателям в Калифорнии этой осенью. Mirai работает на водороде и может проехать около 300 миль на полном баке. Японский автопроизводитель также использовал акценты из углепластика в моделях Lexus с пакетом «F Sport», включая седан GS F и суперкар LFA.
GM планирует включить углепластик в смесь материалов, чтобы облегчить нагрузку на свои будущие автомобили, а Chrysler Group также готовится использовать больше элементов из углеродного волокна в своей линейке, включая Dodge Dart, а также экзотический SRT. Гадюка.
Снижение веса без ущерба для безопасности
Поскольку Министерство энергетики США поставило перед собой цель снизить себестоимость производства углеродного волокна на 50 процентов, углепластик полагает, что он станет еще более эффективным инструментом в постоянном поиске более экономичных автомобилей.Министерство энергетики утверждает, что следующее поколение композитов из углеродного волокна может снизить вес легкового автомобиля на 50 процентов и повысить эффективность использования топлива примерно на 35 процентов без ущерба для производительности или безопасности, что может сэкономить более 5000 долларов на топливе в течение всего срока службы автомобиля при сегодняшних ценах на бензин. .
.