Волокна армирующие: Волокна армирующие, свойства — Энциклопедия по машиностроению XXL
- Волокна армирующие, свойства — Энциклопедия по машиностроению XXL
- Армирующие волокна — — Энциклопедия по машиностроению XXL
- Фибра, волокна для армирования | BAUTECH Полы
- Волокно армирующее — Справочник химика 21
- Перспективные армирующие высокотемпературные волокна для металлических и керамических композиционных материалов Текст научной статьи по специальности «Технологии материалов»
- Классификация армирующих волокон в КМ
- SammaS — Армирующие материалы — Справочник материалов
- Армирующее волокно — обзор
- Виды армирования волокном | Автоматизированная динамика
- Что случилось с бетоном, армированным волокном?
- Бетон, армированный углеродным и стальным волокном — CEMEX USA
- армирующих волокон — Vectorply
- Армирующие волокна | Полимер, сталь, полипропилен для бетона
- FABPRO POLYMERS ’OMEGA ™ II Стальной бетон, армирующее волокно
Волокна армирующие, свойства — Энциклопедия по машиностроению XXL
В качестве армирующих элементов слоистых и волокнистых композиционных материалов с металлической матрицей применяются волокна из углерода, бора, карбида кремния, оксида алюминия, высокопрочной стальной проволоки (сетки), бериллиевой, вольфрамовой и других проволок. Для обеспечения химической стойкости в расплаве матрицы и сцепления волокна с матрицей применяют защитные барьерные покрытия на волокнах из карбидов кремния, титана, циркония, гафния, бора, из нитридов и окислов этих и других элементов. При этом получается сложная многокомпонентная система матрица — переходный слой продуктов химического воздействия матрицы с барьерным покрытием — слой волокна. Механические свойства за счет армирования повышаются в 1,5—3 раза (удельные в 2—5 раз) в зависимости от объемной доли и способа введения армирующих волокон.
[c.78]
При соединении труб из термопластов и других деталей из изотропных материалов способ формования резьбы не оказывает существенного влияния на прочность соединения. При этом приходится соблюдать некоторые общие правила, справедливые и для формования других деталей из термопластов избегать острых кромок у витков резьбы, применять скругления и т. п. [54]. В деталях из слоистых пластиков резьбу рекомендуется выполнять так, чтобы волокна армирующего наполнителя располагались перпендикулярно к направлению действующей нагрузки. При нарезке резьбы в таких деталях (трубах и оболочках) слои наполнителя оказываются перерезанными, и прочность резьбового соединения определяется не столько механическими свойствами пластика, сколько прочностью матрицы при сдвиге (равной приблизительно 5-10 МПа) [22, с. 72 107]. Наибольшая прочность резьбовых соединений достигается в тех случаях, когда волокна наполнителя повторяют рисунок профиля резьбы. При этом разрушающее напряжение материала при сдвиге, а следовательно, и несущая способность резьбы повышаются в 3-4 раза [22, с. 72]. Резьбы такого типа создают формованием различными методами.
[c.302]
Винты — Фиксирование 169 Вкладыши подшипников 120 — Расчет размеров 123 Волокна армирующие 131 Волокнит древесный коротковолокнистый — Применение 35, 137, 138 — Свойства 18 Выступы 81
[c. 210]
Если армирующие волокна во всех трех направлениях имеют одинаковые упругие свойства, т. е. гп1 — т, то из (5.59) имеем [c.136]
Армирующие волокна. В процессе создания углеродной матрицы на этапе графитизации углеродные волокна подвержены длительному воздействию режима термообработки, который приводит к некоторым изменениям их кристаллической структуры. Степень изменения последней зависит от свойств волокон [109]. Подтверждением этому служат опыты, проведенные на волокнах Торнел 25 ( = 172 ГПа) и Торнел 40 ( = = 276 ГПа) в инертной атмосфере в течение 10 ч при 2600 °С. В ходе опытов обнаружено существенное повышение степени графитизации волокон — изменение среднего размера кристаллита или высоты пакета параллельно кристаллографической оси. Для волокон Торнел 25 размер кристаллита возрос в 2 раза, а для Торнел 40 в 1,5 раза. Для низкомодульных волокон повышение степени графитизации при длительном воздействии высоких температур было подтверждено повторными опытами. Волокна с более высоким модулем упругости (Торнел 50), выдержанные в течение 24 ч при температуре 2750 С, не проявили явных изменений в структуре.
[c.181]
Композиционные материалы. Представление о влиянии этапов графитизации и числа циклов уплотнения на формирование свойств композиционных материалов дает табл. 6.14. Исследования выполнены на ортогонально-армированных материалах с распределением волокон в направлении осей х,у, гв соотношении 1 1 2. В качестве арматуры были использованы высокопрочные (2,38 ГПа) и высокомодульные (517 ГПа) волокна Торнел 75 (плотность армирующего каркаса составляла 0,75 г/см ). Исходной матрицей служила фенольная смола. Технологический процесс изготовления композиционного материала
[c.181]
Прогресс в области технологии производства синтетических волокон с модифицированными свойствами достиг такого уровня, при котором оказалось возможным получение армирующих материалов, способных конкурировать с неорганическими волокнами.
[c.46]
Для того чтобы пластики можно было использовать в качестве конструкционных материалов, их необходимо армировать с целью увеличения их прочности и модуля упругости. Как правило, это достигается введением в состав материала высокопрочных волокон, при этом волокна и пластичная матрица образуют в совокупности композиционный материал, свойства которого превосходят [c.261]
Дополнительные проблемы при оценке предельных свойств композитов появляются в связи с такими особенностями этих материалов, как неупругость поведения компонент, анизотропия армирующих волокон, разброс прочности компонент, наличие третьей фазы в виде пограничного слоя матрицы вблизи поверхности волокна. Следует учитывать также и специфику их применения — в авиационных конструкциях требуется нечувствительность к локальным разрушениям, в судостроении — стойкость к коррозии и кавитации, в возвращаемых космических кораблях—сопротивление абляции и уносу массы.
[c. 38]
Нам не представляется возможным автоматически переносить результаты взаимодействия металлов с углеграфитовыми материалами на углеродные волокна из-за специфичности структуры последних мелкие кристаллиты, в которых базисные плоскости вдоль границы волокна разделены узкими порами (параллельно оси волокна) и границами наклона, или кручения (перпендикулярно ей). При указанной структуре прочность волокна должна определяться прочностью границ кристаллитов и быть чувствительной к любым изменениям их состояния. Наличие металла на поверхности углеродного волокна может влиять на состояние и свойства волокон, так как при этом возможно протекание таких процессов, как химическое взаимодействие, диффузия, частичное и, в предельном случае, полное растворение волокна. Таким образом, изучение влияния покрытия на свойства углеродного волокна необходимо для того, чтобы знать, насколько покрытие может ухудшать характеристики как армирующего компонента, так и композиционного материала в целом.
[c.129]
Структура, взаимодействие компонентов и механические свойства композиционных материалов в значительной мере зависят от методов и режимов их изготовления [54]. Так, например, ири изготовлении композиции по режимам, характеризующимся отклонением параметров процесса от оптимальных в сторону снижения температуры, давления и сокращения времени выдержки, реализуется лишь начальная стадия физико-химического взаимодействия компонентов механизм разрушения полученного композиционного материала определяется в этом случае прочностью связи матрицы с волокном. Материал ири нагружении разрушается за счет накопления трещин на границе матрица—волокно и последующего раздельного разрыва частично связанного пучка армирующих волокон и матрицы. Разрыв какого-либо волокна приводит обычно к отслоению его от матрицы, вследствие чего в процессе дальнейших испытаний данное волокно не несет нагрузки. При таком механизме матрица разрушается с образованием воронок вокруг индивидуальных волокон или их комплексов зона разрушения матрицы обычно локализована в плоскости, перпендикулярной к направлению нагрузки волокна выдернуты из матрицы на значительную длину, область разрывов отдельных волокон распределена вдоль оси образца. Такой материал характеризуется высокой ударной вязкостью, сравнительно невысокой прочностью ири растяжении, низкими значениями циклической прочности, прочности при сдвиге, сжатии, изгибе, кручении и т. д.
[c.10]
Как известно, прочность и жаропрочность легированных сплавов, из которых изготовляют армирующие волокна (проволока), выше, чем указанные свойства нелегированных металлов. Свойства применяемых и новых армирующих материалов приведены в табл. 4 и 5. [c.44]
КОМПОЗИЦИОННЫХ материалов и деталей из них. Кроме того, позволяет сочетать в одном полуфабрикате армирующие волокна различного состава, что расширяет спектр свойств конструируемых материалов и изделий из них. [c.46]
Перечень сфер применения керамики чистых окислов весьма велик. Можно с уверенностью сказать, ЧТО область ее использования будет непрерывно расширяться. Век космоса предъявляет к керамике новые требования высоких пределов прочности при растяжении, повышенной ударной вязкости, хорошей термостойкости. Улучшить свойства керамики можно, армируя ее металлическими волокнам и. Большое значение при этом имеет геометрия волокон и их ориентация.
[c.61]
Исключительное положение среди конструкционных пластмасс занимают анизотропные материалы, содержащие армирующие элементы, расположенные с различной закономерностью. Эти элементы (бумага, хлопчатобумажные и вискозные ткани, стеклянные рогожки и ткани, асбестовые ткани, стеклянные волокна и т. д.) придают конечному материалу специфические свойства. От остальных пластмасс анизотропные армированные пластики отличаются не только тем, что их свойства не одинаковы во всех направлениях, но и тем, что их свойства предопределяются сочетанием высокоэластического поведения связующего вещества и почти идеально упругого поведения армирующих элементов. [c.43]
Для целого ряда отраслей эффективным является применение разнообразных композиционных материалов, и в частности композитов, имеющих полимерную матрицу и армирующие непрерывные углеродные, стеклянные, борные или органические волокна. В этом случае достигается не только снижение веса и повышение долговечности элементов конструкций, но и обеспечивается ряд специальных свойств.
[c.16]
Поступающий на завод армирующий компонент, например, товарный асбест, представляет собой распушенное на обогатительных фабриках волокно. Однако в нем содержатся довольно большие агрегаты волокон, которые могут привести к неоднородности ФПМ и снизить степень его армирования, что неблагоприятно отразится на свойствах изделий. Поэтому, в частности, для бо ее тонкого расщепления [c.172]
Надлежащий выбор системы координат позволяет существенно упростить исходные матрицы податливости и жесткости, если материал обладает симметрией упругих свойств. Рассмотрим, например, композиционный материал, состоящий из упругого связующего, регулярно армированного в одном направлении упругими волокнами (рис. 1.2). Для описания деформационных свойств такого материала можно воспользоваться моделью однородного анизотропного упругого тела. В произвольно ориентированной системе координат матрица податливости (и жесткости) будет целиком заполненной, а число подлежащих определению независимых коэффициентов не ясным. В системе координат (Xi, х , х ) плоскость (х , Xs) можно считать плоскостью упругой симметрии матрица коэффициентов податливости в этом случае будет иметь структуру (1.11). Еще более полно симметрия упругих свойств рассматриваемого материала выявляется в системе координат (х1, хг, Xj) плоскость х, Хг) тоже можно считать плоскостью упругой симметрии. Следовательно, теперь все координатные плоскости — плоскости упругой симметрии, материал является ортотропным и матрица коэффициентов податливости имеет структуру (1.12). Более того, при равномерном распределении армирующих волокон допустимо считать, что упругие свойства во всех направлениях в плоскости (x l, Хз) идентичны. Теперь становится ясным, что рассматриваемый материал является трансверсально изотропным, матрицы его коэффициентов податливости имеют вид
[c.
13]
Прочность КОМПОЗИЦИОННЫХ (волокнистых) материалов определяется свойствами волокон матрица в основном должна перераспределять напряжения между армирующими элементами. Поэтому прочность и модуль упругости волокон должны быть значительно больше, чем прочность и модуль упругости матрицы. Жесткие армирующие волокна воспринимают напряжения, возникающие в композиции при нагружении, придают ей прочность и жесткость в направлении ориентации волокон. [c.424]
ОДНОГО И ТОГО же материала можно говорить не о постоянной характеристике, а о ее статистическом распределении. Если модуль упругости и предел текучести меняются в узких пределах и расчет по средним значениям достаточно достоверен, то прочность хрупких материалов и их структурных составляющих должна рассматриваться как случайная величина и отвлечься от ее статистического характера принципиально невозможно. Именно статистическая теория позволяет объяснить и оценить количественно так называемый масштабный эффект прочность большого изделия всегда оказывается меньше, чем прочность малой его модели (после пропорционального перерасчета, конечно). Изложение современных статистических теорий прочности заняло бы слишком много места, однако некоторые сведения нам представлялось необходимым сообщить. Эти сведения особенно существенны для понимания природы прочности современных композитных материалов, состоящих из полимерной или металлической матрицы, армированной угольным, борным илп иным высокопрочным волокном. Разброс свойств армирующих волокон довольно велик и для нопимания того, в какой мере эти свойства могут быть реализованы в композите, необходимо некоторое представление о статистической природе его прочности. Именно поэтому изложение элементов статистической теории будет дано ниже, в гл. 20.
[c.654]
В современной технологии композиционных материалов все большее место занимают волокнистые материалы, представляющие собой композицию из мягкой матрицы (оспоБы) и высокопрочных волокон, армирующих матрицу. Материалы, упрочиепиые волокнами, характеризуются высокой удельной прочностью, а также могут иметь малую теплопроводность, высокую химическую и термическую стойкость и т. п. Для получения композиционных материалов используют различные волокна проволоки из вольфрама, молибдена, волокна оксидов алюминия, бора, карбида кремния, графита и т. п. —в зависимости от требуемых свойств создаваемого материала. Вопросами исследования и создания волокнистых материалов занимается новая, быстроразвивающаяся отрасль поронжовой металлургии — металлургия волокна.
[c.421]
В заключение запишем уравнения закона Гука для ортотроппого материала. В последнее время широкое распространение получили так называемые композитные материалы, состоящие, например, из полимерной основы, армируемой волокнами из высокопрочного материала. Упругие свойства такого композитного материала зависят от плотности насыщения и ориентации в пространстве армирующих волокон. В общем случае такой материал рассматривается как анизотропный. В частном случае, когда армирующие волокна расположены в трех взаимно ортогональных направлениях, упругие свойства будут симметричны относительно трех ортогональных плоскостей.
[c.39]
Анизотропия кристаллов объясняется их атомной структурой, но существуют материалы, у которых определяющие их анизотропию структурные элементы имеют значительно большие размеры. Примером может служить древесина, расположение видимых невооруженным глазом волокон создает относительно высокую прочность в направлении оси ствола и малую прочность в поперечном направлении. В этом отношении можно сказать, что природа распорядилась прочностью целлюлозы, из которой, в основном, состоит древесина, наилучншм образом. По этому принципу в технике создают так называемые композитные материалы, примером которых могут служить стеклопластики. Тонкая стеклянная нить имеет высокую прочность, укладывая слои такой нити, пропитывая их смолой и полимеризируя, получают монолитные пластины. Чередуя направления укладки слоев, можно менять степень и характер анизотропии с тем, чтобы использовать прочность волокна наивыгоднейпшм образом. В последние годы были получены и промышленно освоены высокопрочные волокна, значительно превосходящие по своим свойствам стеклянное волокно и, что особенно важно, имеющие значительно более высокий модуль упругости. Наибольшее распространение получили волокна бора и углерода, которыми армируют пластики и металлы.
[c.41]
В качестве арматуры пространственно-армированных композиционных, материалов используют как стекловолокно, жесткость которого сравнительно невелика, так н высокомодульные углеродные волокна. Наибольшее распространение углеродные волокна получили при создании трехмерноар-мированных материалов типа углерод-углерод [90, 91, 110, 111, 116, 123, 124, 125]. В настоящее время уже испытываются многомерные схемы армирования. Созданы и анализируются системы, имеющие пять и более направлений армирования. При равномерном расположении армирующих волокон по диагоналям куба (система четырех нитей) удается получить ква-зиизотропный материал, а изменяя соотношение арматуры в разных направлениях, можно создать материалы с заданными свойствами. [c.10]
Композиционные материалы на основе системы двух нитей целесообразно изготовлять из различных по механическим свойствам армирующих волокон. Высокомодульнь]е углеродные или борные волокна могут быть расположены в направлении утка и частично в направлении основы. Арматуру, искривленную в направлении основы, изготовляют из стекловолокна. При таком комбинировании разных волокон можно значительно повысить жесткость и прочность в направлении основы и утка без заметного снижения прочности на отрыв в трансверсальном направлении и сопротивляемости сдвигу. Хороший эффект в повышении монолитности и надежности таких структур достигается также за счет модифицирования волокон 34].
[c.12]
Нитевидные кристаллы имеют весьма короткие волокна, при этом соотношения длины и диаметра достаточно высоки. Это очень важно при использовании нитевидных кристаллов ( усов ) в качестве армирующего материала. Усы обладают высокой удельт ной прочностью и жесткостью. Их можно вальцевать, разрезать, обрабатывать без заметного снижения прочностных свойств. Существенным недостатком нового класса армирующих материалов — нитевидных кристаллов — является неприемлемость для них обычной технологии изготовления. Вискеризованные материалы требуют создания новой технологии в целях использования всех потенциальных возможностей вискернзации. Технология переработки материалов с вискери-зированными волокнами изложена в работе [102].
[c.19]
Феноменологическое исследование механических свойств композиционных материалов может быть проведено двумя путями. Первый основан на рассмотрении армирующего материала как конструкции и учитывает реальную структуру композиции. В этом случае задача состоит в установлении зависимостей между усредненными напряжениями и деформациями. Второй путь основан на рассмотрении армированных материалов как квазноднородных сред и использовании традиционных для механики твердых деформируемых тел средств и методов их описания. Краткая схема аналитического расчета упругих констант композиционного материала методом разложения тензоров жесткости и податливости в ряд по объемным коэффициентам армирования приведена в монографии [60, 83]. Установлено, что при малом содержании арматуры можно ограничиться решением задачи для отдельного волокна, находящегося в бесконечной по объему матрице. Однако такой подход заведомо приводит к грубым погрешностям при расчете упругих характеристик пространственно армированных материалов, объем которых заполнен арматурой на 40—70 %. К тому же следует учесть, что пространственное расположение волокон в этих материалах приводит к росту трудностей при решении задачи теории упругости по определению напряженно-деформированного состояния в многосвязанной области матрица—волокно. Коэффициент армирования при этом входит в расчетные выражения нелинейно, что приводит к очередным трудностям реализации метода разложения упругих констант материала по концентрациям его компонентов.
[c.55]
Влияние типа армирующих волокон и схем армирования на формирование свойств. Для изготовления пространственно-армированных углерод-угле-родных композиционных материалов применяют армирующие волокна различных видов (нити, жгуты, стержни и т. д.) с различными физикомеханическими свойствами. Кроме того, армирующие каркасы, имеющие одну и ту же структурную схему, могут быть созданы различными методами (см. с. 168), что оказывает определенное влияние на свойства материала. О влиянии типа волокон на формирование свойств композиционного материала свидетельствуют данные (рис. 6.8), полученные из опытов на изгиб образцов, вырезанных из материала в направлении г [111]. Армирующий каркас был создан прошивкой в направлении 2 пакета, набранного из слоев низкомодульной графитовой ткани. Для прошивки использовали как обычные непропитан-ные углеродные жгуты и нити с различной площадью поперечного сечения, так и предварительно пропитанные и отвержденные (в виде стержней) нити. При изготовлении материалов изменялись только содержание и тип волокон направления z в двух других направлениях параметры армирования сохранялись постоянными.
[c.172]
Примером безмоментных оболочек являются сосуды, изготовленные методом намотки. Расчет таких конструкций основан на нитяной модели материала, согласно которой внутреннее давление и силы, приложенные по краям оболочки, воспринимаются армирующими волокнами и вызывают в них только растягивающие напряжения. Такие конструкции и методы их расчета рассмотрены в работах Рида [67], Росато и Грове [6в], Шульца [75]. Современные методы расчета сосудов давления и корпусов двигателей изготовленных методом намотки [24, 42], учитывают изгиб оболочки, вызванный соответствующим характером нагружения, а также несимметрией распределения геометрических параметров или упругих свойств материала по толщине. Изгиб-ные напряжения, предсказываемые в этом случае теорией малых деформаций, могут оказаться значительными. Однако рассматриваемые оболочки обычно деформируются таким образом, что в процессе нагружения остаются безмоментными. На безмоментной теории, предусматривающей большие деформации системы, основан метод определения равновесных форм армированных оболочек. Обзор исследований, посвященных оптимизации безмоментных оболочек из композиционных материалов, приведен в работе Ву [901.
[c.148]
Книга посвящена рассмотрению результатов изучения поверхности раздела упрочнитель — полимерная матрица в композиционных материалах волокнистого строения. В ней подробно обсуждаются проблемы, которые были только затронуты в книге Современные композиционные материалы . Среди них такие, как химия поверхности армирующих волокон, природа связи на поверхности раздела, роль различных обработок поверхности волокон (в основном силановыми аппретами) в формировании границы раздела полимер — минеральные волокна, механизм передачи напряжений через поверхность раздела, влияние начальных термических напряжений на механические свойства композитов, стабильность композитов при воздействии влаги.
[c.5]
Электронно-микроскопическим методом при большом увеличении изучались реплики, снятые с поверхности стекловолокон, обработанных силановым аппретом. Было установлено, что оптимальными свойствами обладают однонаправленные композиты, которые армированы стекловолокнами, обработанными 0,1—0,25%-ным раствором силановых аппретов, в то время как для образования мономолекулярного слоя требуется всего лишь 0,02—0,04% силана. На электронной микрофотографии стекловолокна, обработанного о, 1%)-ным водным раствором силана, можно видеть большое количество гидролизованного силана в матрице между волокнами (рис. 2). Промывание стекловолокон горячей водой приводит к разрушению большей части силановых мостиков, не ухудшая свойств композитов, армированных таким стекловолокном. Отсюда следует, что для прочной связи волокна с полимером достаточно наличия на стеклянной поверхнасти мономолекулярного слоя аппрета. На практике обычно используются силаны более высокой концентрации с учетом неоднородного осаждения их на пряди (пучке) волокон. Видимые островки аппрета, осевшего на поверхности стекловолокна, незначительны, что подтверждается результатами электронно-микроскопичеокого исследования реплик. Даже при самом большом увеличении на стекловолокне нельзя обнаружить монослоя аппрета. В работе [47] было показано, что осаждение равномерно деформируемого пластичного слоя силиконового полимера на поверхности раздела зависит от природы силанов.
[c.18]
Еще более усложняет изучение проблем, связанных с разрушением, разнообразие материалов арматуры и матрицы, которые позволяют создавать композиты с любыми необходимыми свойствами. Наиболее распространены следующие типы армирующих волокон. Волокна Е- и S-стекля—низкомодульные, умеренно прочные при растяжении и сжатии с большими предельными деформациями. Волокна бора — высокомодульные, высокопрочные при растяжении и сжатии. Углеволокна могут сочетать различные свойства — высокую прочность и низкий модуль упругости или низкую прочность и высокий модуль. Органоволокна (Кевлар-49) — высокомодульные, высокопрочные при растяжении, весьма низкопрочные при сжатии. Волокна FP ) —высокомодульные, высокопрочные при сжатии, довольно низкопрочные при растяжении. В качестве связующего (матрицы) используются, как правило, синтетические смолы (термореактивные и термопластичные), графит и сплавы алюминия.
[c.38]
Волокна определяют уровень прочностных свойств композиционных материалов при условии их совместимости с матрицей. Напряжения, возникающие в колгаозиции при нагружении, воспринимаются в основном армирующими волокнами, которые придают композиции прочность и жесткость в направлении ориентации волокон.
[c.33]
Волокна бора и карбида кремния применяют в качестве армирующих компонентов композиционных материалов с алюминиевой, магниевой и титановой матрицами. В случае нагрева выше 500° С волокон бора с алюминиевой матрицей (при изготовлении композиции) имеет место химическое взаимодействие с образованием фазы AlBj. Активное взаимодействие приводит к снижению свойств волокна и к падению прочности композиционного материала в целом. Это вызывает необходимость нанесения на борные волокна тонкого слоя покрытия (3—5 мкм). Такими покрытиями, защищающими волокна от взаимодействия с матрицей, являются карбиды кремния и бора, нитриды титана, бора и кремния и др. [c.36]
Свойства волокнистых композиционных материалов, особенно их механические свойства, при одном и том же содержании упроч-нителя, сильно зависят от ориентации волокон в матрице и от угла между направлением действия приложенной нагрузки и ориентацией волокон [77 ]. Примером тому являются приведенные на рис. 80 кривые изменения предела прочности в зависимости от направления приложения нагрузки материала алюминий — 50 об. % борного волокна с тремя схемами укладки армирующих волокон и на рис. 81 кривые изменения модуля упругости и модуля сдвига одноосноармированного материала алюминий — 50 об. % борного волокна [10,30]. Значения предела прочности, модуля упругости и удлинения композиционного материала на основе алюминиевого сплава 6061, упрочненного волокнами бора и борсик, с различными типами укладки волокон, приведены в табл. 44, 45. Представленные на рис. 80, 81 и в табл. 44 и 45 данные свидетельствуют о широких возможностях изменения свойств композиционного материала в зависимости от типа укладки армирующих волокон при одном и том же их общем содержании. Это позволяет с максимальной степенью реализовать прочностные свойства композиционного материала в детали, сконструированной таким образом, что количество и направление укладки волокон учитывают ее напряженное состояние. Приведенные в табл.
45 данные позволяют также получить представление о прочностных свойствах при сжатии композиций алюминий — бор. 206
[c.206]
Титановые сплавы обладают максимальной удельной прочностью по сравнению со сплавами на основе других металлов, достигающей 30 км и более. В связи с этим трудно подобрать армирующий материал, который позволил был создать на основе титанового сплава высокоэффективный композиционный материал. Разработка композиционных материалов на основе титановыг сплавов осложняется также довольно высокими технологическими температурами, необходимыми для изготовления этих материалов, приводящими к активному взаимодействию матрицы и упрочни-теля и разупрочнению последнего. Тем не менее работы по созданию композиционных материалов с титановой матрицей проводятся, и главным образом в направлении повышения модуля упругости, а также прочности при высоких температурах титановых сплавов. В качестве упрочнителей применяются металлические проволоки из бериллия и молибдена. Опробуются также волокна из тугоплавких соединений, такие, как окись алюминия и карбид кремния. Механические свойства некоторых композиций с титановой матрицей приведены в табл. 58. Предел прочности и модуль упругости при повышенных температурах композиций с молибденовой проволокой показаны в табл. 59.
[c.215]
Однонаправленные структуры получают укладкой первичного армирующего материала (волокна, нити, жгута, шпона, ленты) в одинаковых направлениях в каждом слое. Примером изделий на основе ОС может служить листовой однонаправленный СВАМ, бондажные кольца, кольцевые шпангоуты, полученные намоткой на оправку элементарного волокна, нити или жгуты, профильные изделия, полученные протяжкой (стержни, уголки, тавры, швеллеры и т. д.). К материалам, имеющим ОС, можно отнести древесину и материалы на основе облагороженной древесины (фанера, древеснослоистый пластик и др.). Отличительной особенностью их является максимальная прочность вдоль направления волокна и минимальная — в перпендикулярном направлении, в котором прочность определяется адгезионными свойствами связующего.
[c.7]
В табл. 3 приведены типичные свойства высокомодульных волокон, которыми армируют пластики для низких температур. Kevlar 49 является разновидностью арамидно-го волокна производства Е. I. Du Pont orporation , часто используемого в композитах на органической основе. Это волокно по сравнению со стеклом обладает повышенным модулем упругости при относительно низкой стоимости. Недостатками этих материалов является сравнительно низкая прочность при сжатии, пониженная поперечная прочность и очень большое отрицательное значение коэффициента линейного расширения в продольном направлении. [c.74]
Большой интерес представляют комбинированные наполнители, состоящие из указанных выще наполнителей, взятых в различных соотношениях и позволяющие улучшить комплекс свойств наполненных фторопластов. Износостойкость наполненных фторопластов увеличивается более чем в 500 раз, теплопроводность в 5—10 раз, сопротивление деформации при сжатии в 3—4 раза, твердость на 10% и т. д. При выборе наполнителей необходимо учитывать условия эксплуатации наполненных фторопластов для целей химического машиностроения целесообразно применять графит, стеклопорошок и волокно, ситалл, керамику, асбест для электроизоляционных деталей — слюду, кварцевый порошок, стеклочешуйки, стеклопленку для пар трения, работающих без смазки,— графит, дисульфид молибдена в сочетании с армирующими наполнителями (волокнистыми наполнителями).
[c.181]
Описание механических свойств композитных материалов, которые могут обладать весьма высокой прочностью (особенно статической и ударной), можно производить двумя путями. В первом случае композитные материалы рассматриваются как квазиодно-родные (гомогенные), обладающие в случае объемного дисперсного армирования изотропией деформационных и прочностных свойств, а в случае армирования волокнами, плоскими сетками или тканями — определенного типа анизотропией. Обычно применяют модели ортотропного или трансверсально-изотропного тела. При таком подходе речь идет о механических характеристиках, осред-ненных в достаточно больших объемах, содержащих много однотипных армирующих элементов. Другой, несравненно более сложный, но и более информативный путь состоит в раздельном рассмотрении механических свойств каждой фазы с последующим теоретическим прогнозированием свойств всего композита в целом. При этом приходится рассматривать фактически еще одну дополнительную фазу зоны сопряжения основных фаз, например, матрицы с армирующими волокнами. Механизм повреждений, развивающихся на границах фаз, обычно весьма сложен и определяется помимо свойств основных компонентов гетерогенной системы еще рядом дополнительных факторов, таких как адгезия фаз, технологические и температурные местные напряжения, обычно возникающие вблизи границ, наличие дефектов и др. Границы фаз как зоны концентраций напряжений играют особенно важную роль в развитии много- и малоцикловых усталостных повреждений композитов.
[c.37]
Рассмотрим материал, обладающий анизотропией прочности, которая в большинстве случаев сочетается с анизотропией деформационных свойств материала. Допустим, что материал составлен из матрицы, армированной перекрестными взаимно перпендикулярными волокнами. Отнесем систему армирующих волокон к осям XYZ так, что сопротивление растяжению или сжатию элемента материала с гранями, параллельными координатным плоскостям, будет в направлении одной из осей, например ОХ, наибольшим (вследствие наибольшей плотности расположения волокон), в направлении оси 0Y — ниже (вследствие меньшей плотности), а по оси 0Z, где может совсем не быть арматуры, — наименьшим. Анизотропия такого типа называется ортогональной, а соответствующие композитные материалы, которые встречаются наиболее часто, — ортотропными. Оси XYZ называются главными осями анизотропии, которые в общем случае конечно не совпадают с главными осями напряжений. Сбпротивления сдвигу, т. е. действию касательных напряжений, в главных плоскостях анизотропии XOY, YOZ к ZOX различны, но предельные значения касательных напряжений Oij = Oji не зависят от их направления, что не имеет места в том общем случае, когда оси XYZ не являются главными осями анизотропии.
Будем считать, что при испытании образцов данного материала в главных плоскостях анизотропии могут создаваться статически определимые и коя-
[c.85]
Были исследованы несмазываемые подшипниковые узлы из листовых материалов группы 36 [57]. Установлено, что модуль упругости при сжатии материалов оказывает на изнашивание более существенное влияние, чем содержание и распределение в рабочем слое ПТФЭ. На упругопрочностные свойства рабочего слоя материалов влияет тип армирующего волокна. Наименьшему изнашиванию подвержен материал с армирующими поли-имид-амидными волокнами. Применение полимерных волокон других видов привело к усилению процесса изнашивания по сравнению с изнашиванием материалов, содержащих в качестве армирующего элемента стекловолокна. Износ уменьшался с увеличением модуля упругости при сжатии. [c.50]
Армирующие волокна — — Энциклопедия по машиностроению XXL
Система трех нитей. Композиционные материалы, образованные системой трех нитей, содержат арматуру в трех направлениях выбранных осей координат. Наиболее типичные схемы армирования приведены на рис. 1.4. Схемы, как правило, образованы взаимно ортогональными волокнами (рис. 1.4, а, б), но встречаются и с косоугольным расположением (рис. 1.4, в, г). Армирующие волокна могут быть прямолинейными (рис. 1.4, а), иметь заданную степень искривления волокон в одном (рис. 1.4,в) или двух (рис. 1.4, г) направлениях. Содержание волокон и интервал между ними в каждом из трех направлений являются основными параметрами композиционных материалов, которые определяются условиями их применения.
[c.13]
Армирующие волокна слоя, как отмечалось на с. 48, могут иметь случайный или заданный характер искривлений. Случайные отклонения волокон от прямолинейности возникают в результате технологических несовершенств при изготовлении композиционных материалов [22] (см. рис. 3.8). Заданный характер искривлений обу-
[c.60]
Построение деформационной модели базируется на математическом принципе суперпозиции двух идеализированных ее составляющих упругого армирующего каркаса с приведенной матрицей жесткости и упругопластического изотропного связующего с заданной кривой упрочнения. Допущения, принятые при построении первой составляющей модели, характерны для пространственной стержневой системы в расчете учитывается лишь одноименная с каждым из четырех направлений волокон жесткость. Сеть волокон считается размазанной по всему объему куба, принятого за представительный элемент. Таким образом, при равномерно распределенной плотности энергии деформации находится эквивалентная матрица жесткости однородного материала. Обозначив ее индексом а (армирующие волокна), приведем полную запись для нее в системе главных осей упругой симметрии 123 [c.79]
Если армирующие волокна во всех трех направлениях имеют одинаковые упругие свойства, т. е. гп1 — т, то из (5.59) имеем
[c.136]
Армирующие волокна. В процессе создания углеродной матрицы на этапе графитизации углеродные волокна подвержены длительному воздействию режима термообработки, который приводит к некоторым изменениям их кристаллической структуры. Степень изменения последней зависит от свойств волокон [109]. Подтверждением этому служат опыты, проведенные на волокнах Торнел 25 ( = 172 ГПа) и Торнел 40 ( = = 276 ГПа) в инертной атмосфере в течение 10 ч при 2600 °С. В ходе опытов обнаружено существенное повышение степени графитизации волокон — изменение среднего размера кристаллита или высоты пакета параллельно кристаллографической оси. Для волокон Торнел 25 размер кристаллита возрос в 2 раза, а для Торнел 40 в 1,5 раза. Для низкомодульных волокон повышение степени графитизации при длительном воздействии высоких температур было подтверждено повторными опытами. Волокна с более высоким модулем упругости (Торнел 50), выдержанные в течение 24 ч при температуре 2750 С, не проявили явных изменений в структуре.
[c.181]
Кинетика разрушения модельных композиций с модифицированными армирующими волокнами/В. Р. Регель, [c.219]
В качестве одного из экспериментов, при помощи которых определяют вид функции S k), рассмотрим испытание на сдвиг прямоугольной пластины, ограниченной плоскостями X = О, X = L и У = 0, Y = D, верхняя и нижняя поверхности которой У = О, Z) соприкасаются с абсолютно жесткими плитами. Армирующие волокна первоначально параллельны оси X. Верхняя плита смещается параллельно направлению оси X, в то время как нижняя остается неподвижной. Боковые стороны X = О п X = L свободны от напряжений. [c.309]
Конструкция кабины и головного модуля высокоскоростного поезда описана Центром развития железнодорожного транспорта [10]. Кабина изготовляется Отделом пластиков Британского центра развития железнодорожного транспорта в Дерби. Обе оболочки кабины изготовлены из трехслойного пластика с крученым армирующим волокном. Внутренняя и наружная стенки изготовляются в одних и тех же формах при по.лучении наружной стенки в форму вставляется 10-сантиметровый вкладыш, а при получении внутренней — вкладыш удаляется. Пространство между двумя стенками заполняется пеной, образуя монококовую конструкцию. Стены выполнены как одно целое с полом, а каркас машинного отделения смонтирован снаружи кабины. Такой метод конструирования позволяет достичь экономии массы приблизительно 30% по сравнению с традиционным конструированием кабин. Большое значение имеет то обстоятельство, что все внутренние поверхности кабины гладкие, так как трубопроводы, кабели и воздуховоды заключены внутри слоистой панели.
[c.186]
В предыдущем обсуждении допускалось, что армирующие волокна в композите обладают четко определенным однозначным разрывным напряжением. Хотя это допущение и может служить хорошим приближением в случае армирования металлами, оно несправедливо для хрупких или любых других волокон, обнаруживающих, как правило, зависимость прочности от длины. В последнем случае прочность композита необходимо оценивать статистическими методами. (Это рассмотрено более детально в гл. 4, написанной Аргоном.)
[c.453]
Рис. 14. Влияние слабых точек в армирующих волокнах на разрушающую нагрузку Р. |
Рис. 15. Влияние слабых точек в армирующих волокнах на вклад в вязкость разрушения Ц от вытаскивания волокон для тех же условий, что и на рис. 14, и сравнение с теоретическими оценками по уравнениям (36) и (38) [13]. |
Разрушение при сдвиге или при растяжении (сжатии) в направлении, перпендикулярном армирующим волокнам
[c.43]
Эти уравнения позволяют рассчитать через упругие константы компонент модуль упругости композита в направлении, перпендикулярном армирующим волокнам,
[c. 181]
У волокнистых и слоистых композиционных материалов несущим элементом является армирующее волокно, проволока, фольга (фаза—упрочнитель). Армирующие элементы по своей природе имеют высокую прочность, весьма высокий модуль упругости и, как правило, сравнительно низкую плотность. [c.5]
Анализируя характер разрушения композиционных материалов, следует отметить, что последний представляет собой ряд последовательных дискретных этапов, каждый из которых отличается от другого перераспределением напряжений между армирующими волокнами. [c.12]
Распределение напряжений в дискретных волокнах. В том случае, когда армирующие волокна непрерывны, напряжения в них постоянны на всей длине за исключением концевых участков. При малом разбросе частных значений прочности волокон в момент разрушения композиции напряжения почти на всех волокнах достигают их предела прочности. Если же композиция армирована короткими волокнами или усами, то активная роль матрицы состоит в том, чтобы путем пластической деформации передать напряжения волокнам и нагрузить их [45].
[c.13]
Жесткие армирующие волокна воспринимают основные напряжения, возникающие в композиции при нагружении, придавая ей прочность и жесткость в направлении ориентации волокон. Податливая металлическая матрица, заполняющая межволоконное пространство, осуществляет передачу напряжений отдельным волокнам за счет касательных напряжений, действующих вдоль границы раздела волокно—матрица. Для металлической проволоки характерно повышенное удлинение при разрыве (2—5%) по сравнению [c.34]
Как известно, прочность и жаропрочность легированных сплавов, из которых изготовляют армирующие волокна (проволока), выше, чем указанные свойства нелегированных металлов. Свойства применяемых и новых армирующих материалов приведены в табл. 4 и 5. [c.44]
КОМПОЗИЦИОННЫХ материалов и деталей из них. Кроме того, позволяет сочетать в одном полуфабрикате армирующие волокна различного состава, что расширяет спектр свойств конструируемых материалов и изделий из них.
[c.46]
Чаще всего нарушение стабильности поверхностей раздела происходит в результате химических реакций между волокном и матрицей, при которых образуются побочные продукты взаимодействия. Поскольку прочность слоя продуктов реакции меньше прочности армирующего волокна, то при нагружении композиционного материала растрескивание этого слоя будет инициировать разрушение волокон и, следовательно, всей композиции. [c.67]
В качестве исходных материалов используют металлические или металлокерамические порошки, образующие матрицу, и армирующие волокна в виде непрерывных или дискретных волокон, либо в виде металлических сеток. Оборудование, применяемое при изготовлении композиционных материалов, как правило, существенно не отличается от оборудования, применяемого в порошковой металлургии. В основном это разного типа вибрационные столы для уплотнения смеси, прессы, печи для спекания и др. [c.150]
При получении волокнистых композиционных материалов с использованием энергии взрыва применяют схему продольного распространения фронта детонации. При этом металл матрицы, заполняющий межволоконное пространство, приходит в соприкосновение с нижним слоем металла и соединяется с ним. Волокна в зоне сварки иногда теряют устойчивость и приобретают волнообразную форму чаще всего это явление наблюдается тогда, когда отношение толщины листа материала матрицы к диаметру армирующего волокна меньше единицы. Образовавшиеся гофры можно удалить путем небольшой подкатки полученного листового композиционного материала. Режимы подкатки (температура, степень обжатия) выбирают в зависимости от состава материала. Э. С. Атрощенко и др. было показано, что при использовании в качестве упрочнителя металлических волокон прокатку можно проводить как в продольном, так и в поперечном относительно волокон направлении со степенями обжатия до 10—15% за один проход.
[c.163]
Пайка боралюминия. Разработано несколько технологических процессов пайки боралюминия. Пайка низкотемпературными припоями производится в температурном интервале, не оказывающем разупрочняющего влияния на армирующие волокна [200]. Паяные соединения, полученные этим методом, способны работать при температурах до 315° С. Было опробовано несколько припоев для низкотемпературной пайки. Припой состава 55% Сс1, 45% Ag рекомендуется для рабочих температур до 90° С он обеспечивает прочность соединения на срез, равную 9 кгс/мм. Припой состава 95% цинка и 5% алюминия рекомендуется для рабочих температур до 315° С, при которых прочность соединения на срез составляет 3 кгс/мм .
[c.191]
В заключение запишем уравнения закона Гука для ортотроппого материала. В последнее время широкое распространение получили так называемые композитные материалы, состоящие, например, из полимерной основы, армируемой волокнами из высокопрочного материала. Упругие свойства такого композитного материала зависят от плотности насыщения и ориентации в пространстве армирующих волокон. В общем случае такой материал рассматривается как анизотропный. В частном случае, когда армирующие волокна расположены в трех взаимно ортогональных направлениях, упругие свойства будут симметричны относительно трех ортогональных плоскостей.
[c.39]
Влияние типа армирующих волокон и схем армирования на формирование свойств. Для изготовления пространственно-армированных углерод-угле-родных композиционных материалов применяют армирующие волокна различных видов (нити, жгуты, стержни и т. д.) с различными физикомеханическими свойствами. Кроме того, армирующие каркасы, имеющие одну и ту же структурную схему, могут быть созданы различными методами (см. с. 168), что оказывает определенное влияние на свойства материала. О влиянии типа волокон на формирование свойств композиционного материала свидетельствуют данные (рис. 6.8), полученные из опытов на изгиб образцов, вырезанных из материала в направлении г [111]. Армирующий каркас был создан прошивкой в направлении 2 пакета, набранного из слоев низкомодульной графитовой ткани. Для прошивки использовали как обычные непропитан-ные углеродные жгуты и нити с различной площадью поперечного сечения, так и предварительно пропитанные и отвержденные (в виде стержней) нити. При изготовлении материалов изменялись только содержание и тип волокон направления z в двух других направлениях параметры армирования сохранялись постоянными.
[c.172]
Примером безмоментных оболочек являются сосуды, изготовленные методом намотки. Расчет таких конструкций основан на нитяной модели материала, согласно которой внутреннее давление и силы, приложенные по краям оболочки, воспринимаются армирующими волокнами и вызывают в них только растягивающие напряжения. Такие конструкции и методы их расчета рассмотрены в работах Рида [67], Росато и Грове [6в], Шульца [75]. Современные методы расчета сосудов давления и корпусов двигателей изготовленных методом намотки [24, 42], учитывают изгиб оболочки, вызванный соответствующим характером нагружения, а также несимметрией распределения геометрических параметров или упругих свойств материала по толщине. Изгиб-ные напряжения, предсказываемые в этом случае теорией малых деформаций, могут оказаться значительными. Однако рассматриваемые оболочки обычно деформируются таким образом, что в процессе нагружения остаются безмоментными. На безмоментной теории, предусматривающей большие деформации системы, основан метод определения равновесных форм армированных оболочек. Обзор исследований, посвященных оптимизации безмоментных оболочек из композиционных материалов, приведен в работе Ву [901.
[c.148]
Трансверсалъно изотропным называют анизотропный материал, который имеет только одну плоскость, в которой все направления эквивалентны… Название трансверсально изотропный используется для того, чтобы отличать такой материал от изотропного. По-видимому, более подходящим было бы название ионотропный , поскольку оно характеризует материал, имеющий включения (или армирующие волокна) только в одном направлении [93]. Если плоскость изотропии совпадает с координатной плоскостью Х1Х , то матрица коэффициентов жесткости по-прежнему определяется равенством (10), в котором следует произвести следующую замену [c.161]
Армирующие волокна в композиционном материале обычно выбирают из соображений максимальных прочностных и жест-костных характеристик. Основное назначение матрицы — соедн-
[c.197]
Для деформаций видов (2) и (4) материалы могут быть армированы волокнами, параллельными образующим коаксиальных цилиндров, являющихся главными поверхностями. В случае (3) волокна могут быть или параллельными, или перпендикулярными главным поверхностям, в начальном состоянии представляющим собой параллельные плоскости. Деформации вида (5) остаются контролируемыми для материалов, армированных волокнами, в начальном состоянии параллельными оси вращательной симметрии. Применение этого вида деформаций для получения решений в случае волокнистых и слоистых композитов несколько более подробно рассмотрено в статье Пипкина [23]. [c.351]
В микрофотоупругих экспериментах используются модели с армирующими волокнами материала-натуры, например со стекловолокнами, волокнами бора, сапфировыми усами и т. д. Эти модели точнее имитируют моделируемый композит, поскольку в них сохраняется трехмерное напряженное состояние и воспроизводятся характеристики сцепления между матрицей и волокнами. Были проведены микрофотоупругие опыты, в которых для определения неэффективной длины волокна и исследования вида и путей распространения микроразрушения изучались распределения напряжений и их концентрация вокруг концов волокон, разрывов волокон и нарушений сцепления волокна с матрицей.
[c.520]
Роллинс [42] впоследствии подтвердил, что усталостное поведение композитов с волокном бора (на примере композита алюминия 6061 с бором) чувствительно к наличию паров воды, и, кроме того, отождествил эту чувствительность со склонностью волокон бора диаметром 0,010 см к продольному расщеплению. Поведение, подобное тому, которое показано на рис. 20, наблюдалось в случае сухой и влажной сред гелия. Введение паров воды в испытательную камеру не оказало никакого заметного эффекта для образцов, которые были армированы волокнами бора диаметром 0,014 см, что согласуется с наблюдающимся предрасположением к продольному расщеплению волокон меньшего, но не большого диаметра [32]. Модуль разрушения волокон бора обоих диаметров не зависел от характера атмосферы это под-
[c. 432]
В оригинале shear-lag model — анализ, рассматривающий перераспределение нагрузок между армирующими волокнами композита посредством касательных напряжений, переводится как сдвиговый анализ , модель сдвигового анализа . — Прим. перев. [c.46]
В работе [11] модель накопления повреждений при растяжении распространена на случай действия касательных напряжений в плоскости слоя. При этом действие нормальных напряжений, перпендикулярных армирующим волокнам слоя, не учитывается. Однако в слоях композита при плоском напряженном состоянии в зависимости от схемы армирования могут возникать все три ко.мпоненты напряжений (нормальные в направлении армирующих волокон, перпендикулярные им и касательные в плоскости слоя). Следовательно, для применения критерия прочности [II] к анализу слоистого композита необходимо учитывать и нормальные напряжения, перпендикулярные направлению армирования. Простые рассуждения показывают, что действие этих напряжений в композите с полимерной матрицей может проявиться в первую очередь в деформировании матрицы, а не волокон. Поскольку подобное предположение справедливо и для касательных напряжений в плоскости, логично ол[c.47]
Обобщенный полиномиальный критерий прочности для материала с любым видом симметрии можно вывести на основе метода, подробно изложенного в [3]. Рассмотрим два наиболее часто применяемых подхода для описания поверхности прочности композитов полиномиальный критерий, записанный в тензорах напряжений, и критерий наибольших деформаций. Ограничимся случаем ортотроиии, которая характерна для большинства композитов с непрерывными армирующими волокнами. [c.106]
По методу Петита и Ваддоупса в качестве исходной ин формации используются диаграммы деформирования мате риала слоя при растяжении сжатии в направлениях армирования и перпендикулярно армирующим волокнам, диаграммы деформирования при сдвиге и зависимость наиболь-щего коэффициента Пуассона от ei,. [c.151]
Наиболее интересными с практической точки зрения являются исследования, в которых определяются условия увеличения долговечности деталей в результате уменьшения скорости роста усталостных трещин. Увеличение прочностных и пластических характеристик материала (ств, стт, i ), уменьшение размера структурных составляющих, увеличение коэффициента асимметрии цикла нагружения, уменьшение жесткости двухосного напряженного состояния, понижение температуры испытания и наличие вакуума — вот далеко не полный перечень факторов, приводящих к уменьшению скорости роста трещины. Увеличение сопротивления усталости, связанное с затруднением роста трещины, происходит и при упрочнении границ зерен дробной механотермической обработкой, и при взрывном упрочнении, приводящем к замораживанию дислокаций [8]. Торможения развития трещин добиваются также применением композиционных материалов, в которых трещина либо вязнет в мягких слоях, либо не может разрушить более прочные армирующие волокна.
[c.7]
К первой группе относятся композиционные материалы, упрочненные дисперсными частицами и хаотически расположенными монокристалличе-скими нитями (так называемыми усами ) (см. рис. 114, I—1). Материалы, получаемые методами порошковой металлургии и состояш ие, например, из частиц карбидов тугоплавких металлов, помеш енных в связующее, образуемое металлами железной группы, иллюстрируются схемой I—2. За рубежом значительное внимание уделяют созданию металлических материалов, например, на медной основе, армированных дискретными отрезками вольфрамовой, молибденовой проволоки (/—3), а также расположенными в металлической основе непрерывными проволоками 1—4) [97 98]. Могут быть изготовлены материалы, имеющие армирующие элементы в виде сеток -— проволочных тканей и сот (/—5). Еще один вид образуют материалы, имеющие непрерывные неориентированные армирующие волокна — типа войлока , в зарубежной практике называемые фелтметалл (/—6).
[c.250]
Волокна определяют уровень прочностных свойств композиционных материалов при условии их совместимости с матрицей. Напряжения, возникающие в колгаозиции при нагружении, воспринимаются в основном армирующими волокнами, которые придают композиции прочность и жесткость в направлении ориентации волокон.
[c.33]
Для повышения высокотемпературной прочности и жаропрочности в армирующие волокна вводят легирующие добавки, повышающие температуру начала ракристаллизации, поскольку последняя приводит к сильному разупрочнению волокон. Зависимость предела прочности от состава проволоки и ее диаметра представлена в табл. 3. [c.44]
В зависимости от модуля упругости наполнителя композиты низкого давления делятся на низко- и высокомодульные. Материалы первого типа армированы волокнами из целлюлозы (хлопок, лен) и стекла. Волокна материалов второго типа—из углерода, бора, корунда, органических арамидов — имеют высокий модуль упругости. В качестве армирующего материала применяют и разнообразные ткани [1]. Терминология, используемая применительно к композитам, приведена в работах [1—4]. [c.72]
Фибра, волокна для армирования | BAUTECH Полы
Полимерное волокно Baumex
Стальные волокна Baumix
Полипропиленовое волокно Baucon
|
ВОЛОКНА ДЛЯ АРМИРОВАНИЯ
Бетон, армированный стальными и полипропиленовыми волокнами, является материалом с повышенной стойкостью, не выкрашивается и обладает высокой прочностью против удара.
|
|
|
Полимерные микроволокна BAUMEX® для армирования бетона
читать далее
| |
60 |
Стальные армирующие волокна Baumix® 60
читать далее
| |
50
|
Стальные армирующие волокна Baumix® 50
читать далее
| |
|
Полипропиленовые армирующие волокна Baucon,
читать далее
|
Теги: полимерные макро волокна, фибра, стальные, полипропиленовые, для армирования бетона, фибра
Волокно армирующее — Справочник химика 21
Волокна, используемые в качестве армирующих наполнителей, должны иметь следующие свойства высокую температуру плавления, малую плотность, высокую прочность во всем интервале рабочих температур, отсутствие токсичности при изготовлении и эксплуатации. [c.69]
К числу современных пластмасс относятся так называемые армированные пластики. В армированных пластиках в качестве наполнителя используют различные волокна. Волокна в составе пластмассы несут основную механическую нагрузку. Органопластики — пластмассы, в которых связующим являются синтетические смолы, а наполнителем — органические полимерные волокна. Их широко применяют для изготовления деталей и аппаратуры, работающих на растяжение, средств индивидуальной защиты и др. В стеклопластиках армирующим компонентом является стеклянное волокно. Стекловолокно придает стеклопластикам особую прочность. Они в 3—4 раза легче стали, но не уступают ей по прочности, что позволяет с успехом заменять ими как металл, так и дерево. Из стеклопластиков, например, изготовляют трубы, выдерживающие большое гидравлическое давление и не подвергающиеся коррозии. Материал является немагнитным и диэлектриком. В качестве связующих при изготовлении стеклопластиков применяют ненасыщенные полиэфирные и другие смолы. Стеклопластики широко используются в строительстве, судостроении, при изготовлении и ремонте автомобилей и других средств транспорта, быту, при изготовлении спортинвентаря и др.
По сравнению со стеклопластиками углепластики (п.ласт-массы на основе углеродных волокон) хорошо проводят электрический ток, в 1,4 раза легче, прочнее и обладают большей упругостью. Они имеют практически нулевой коэффициент линейного расширения по цвету — черные. Они применяются в элементах космической техники, ракетостроении, авиации, наземном транспорте, при изготовлении спортинвентаря и др. [c.650]
Композиционные материалы (композиты)—состоят из полимерной основы, армированной наполнителем в виде высокопрочных волокон или нитевидных кристаллов. Армирующие волокна и кристаллы могут быть металлическими, полимерными, неорганическими (например, стеклянными, карбидными, нитридными, борными). Армирующие наполнители в значительной степени определяют механические, теплофизические и электрические свойства полимеров. Многие композиционные полимерные материалы по прочности не уступают металлам. Композиты 364 [c. 364]
Органические и неорганические покрытия. Лакокрасочные покрытия, хорошо защищающие от атмосферной коррозии, в почве становятся неэффективными уже через несколько месяцев. Рекомендуется наносить толстослойные покрытия на основе каменноугольной смолы с армирующими пигментами или неорганическими волокнами —для уменьшения текучести смолы. Они обеспечивают эффективную защиту при сравнительно небольших затратах. [c.187]
При соединении труб из термопластов и других изделий, которые условно можно отнести к изотропным, способ формования резьбы не оказывает существенного влияния на прочность соединения. Однако в деталях из слоистых пластиков резьбу рекомендуется выполнять так, чтобы волокна армирующего наполнителя располагались перпендикулярно к направлению действующей нагрузки. При нарезке резьб в таких изделиях (трубах и оболочках) слои наполнителя оказываются перерезанными, и прочность резьбового соединения определяется не столько механическими свойствами пластика, сколько прочностью связующего при сдвиге (равной приблизительно 5—10 МПа) [39 48, с. 72]. Наибольшая прочность резьбовых соединений достигается в тех случаях, когда волокна наполнителя повторяют рисунок профиля резьбы. При этом разрушающее напряжение материала при сдвиге, а следовательно, и несущая способность резьбы, повышаются в 3—4 раза [48, с. 72]. Резьбы такого типа создают различными методами формования материалов. [c.111]
В качестве армирующих элементов слоистых и волокнистых композиционных материалов с металлической матрицей применяются волокна из углерода, бора, карбида кремния, оксида алюминия, высокопрочной стальной проволоки (сетки), бериллиевой, вольфрамовой и других проволок. Для обеспечения химической стойкости в расплаве матрицы и сцепления волокна с матрицей применяют защитные барьерные покрытия на волокнах из карбидов кремния, титана, циркония, гафния, бора, из нитридов и окислов этих и других элементов. При этом получается сложная многокомпонентная система матрица — переходный слой продуктов химического воздействия матрицы с барьерным покрытием — слой волокна. Механические свойства за счет армирования повыщаются в 1,5—3 раза (удельные в 2—5 раз) в зависимости от объемной доли и способа введения армирующих волокон. [c.78]
Дефект или острый надрез становится устойчивым, если достигает определенного критического значения, которое для композитных материалов, как правило, меньше расстояния между волокнами армирующего материала. [c.316]
Реальная структура армированного пластика, образующаяся в процессе формования изделий, определяется как природой компонентов, так и технологическим режимом изготовления. На рис. 1.10 представлена микрофотография сечения эпоксидного стеклопластика. Как видно из рисунка, волокна армирующего наполнителя окружены переходным (межфазным) слоем. [c.26]
Мембранные материалы изготавливают методом от-ливания пленок, причем материал является двухслойным сначала отливают пленку с очень мелкими порами и затем покрывают ее более толстым губчатым материалом с крупными порами. Мембранные фильтры наряду с довольно высокой удельной пропускной способностью обладают необходимой механической прочностью, что позволяет применять их при сравнительно больших нагрузках. Для повышения прочности мембранные материалы можно армировать металлическими, стеклянными и синтетическими волокнами. [c.223]
Волокнистые наполнители для армирования полимеров используют при изготовлении стеклопластиков. Стеклянное волокно получают из расплавленного стекла путем продавливания стекломассы через фильеры, при разделении ее струи перегретым паром, сжатым воздухом, под действием центробежных сил и т. д. В зависимости от назначения получают стеклянное волокно с толщиной нитей от 0,2 до 50 мкм. В стеклопластиках стекловолокно армирует обычно эпоксидные и полиэфирные смолы, с которыми обеспечивается удовлетворительная адгезия. Прочность этого материала при значительной его легкости достигает прочности стали. Из стеклопластиков изготавливают трубы, баки, детали для автомобилей, самолетов, контейнеры, вагоны и т. д. [c.394]
Нитевидная форма армирующих элементов имеет как положительные, так и отрицательные стороны. Преимущество волокон состоит в высокой прочности и возможности создать упрочнение только в том направлении, в котором это требуется конструктивно. Недостаток такой формы заключается в том, что волокна способны передавать нагрузку только в направлении своей оси, тогда как в перпендику лярном направлении упрочнения нет, а в некоторых случаях может проявиться даже разупрочнение. [c.69]
К числу наиболее перспективных армирующих элементов относят углеродные волокна. Они обладают низкой плотностью (1430 — 1830 кг/м ), высокими прочностью (3,5 ГПа) и модулем упругости (250 — 400 ГПа). [c.70]
В настоящее время все большее внимание уделяется композиционным материалам на металлической основе, армированной высокомодульными углеродными волокнами. Совместимость армирующего компонента и матрицы в некоторых случаях достигается введением связующего, функцию которого выполняет покрытие. Металлические покрытия необходимы в тех случаях, когда матрица не смачивает поверхность углеродных волокон при температурах получения композиции (алюминий, магний [21), Кроме того, покрытие углеродных волокон такими металлами, как цинк и медь, может впоследствии служить основой или компонентом основы композиционного материала [3]. [c.129]
НИХ изделия сложной формы, повышенной герметичности и низкой пористости, При их формовании остается только обеспечить качественное соединение слоев связующего межд собой (аутогезию) и с армирующими волокнами (адгезию). [c.79]
Уже рассказывалось о формировании многослойной тканевой конструкции с ее пропиткой и связыванием смолой в специальной для каждой детали матрице. После полимеризации в печах аэродинамического нагрева и карбонизации в обычных обжиговых печах нужно было определить пористость детали, с ювелирной точностью отрегулировать ее путем осаждения в порах пиролитического углерода. А после этого провести виртуозную операцию силицирования материала детали с таким расчетом, чтобы не нарушить прочность и упругость армирующего углеродного волокна. И это было сделано Должен признаться, что лично я сомневался в надежности такого процесса, но он был освоен. Приходилось рентгеновским аппаратом определять равномерность свойств по полю детали, лечить повторными процессами, и это тоже удалось сделать. [c.237]
Стеклопластики. Стеклопластиками называются пластические массы, у которых связующим веществом служат синтетические смолы, а наполнителем или армирующим материалом — стеклянное волокно, придающее стеклопластикам особую прочность. [c.400]
Определение фосфора показало, что если, например, фосфор введен в состав КМ с армирующим волокном, то на границе волокно-связующее содержание фосфора составляет 47-52% от его количества в центре поперечного сечения волокна. Обнаружен фосфор и в матрице на расстоянии, превышающем толщину прослойки матрицы в реальных КМ. [c.81]
Волокна асбеста армируют адсорбированные иа их поверхности микрообъемы цемента, что придает бетону дополнительную прочность. Значительная общая поверхность волокон создает условия для образования множества пор, заполненных воздухом, что способствует снижению коэффициента теплопроводности. [c.357]
Анизотропные стеклопластики — пластики с армирующим материалом в виде однонаправленной стеклянной нити. Изделия получают методом намотки стеклянного волокна, предварительно обработанного синтетической смолой. [c.401]
Армированное полимерное покрытие на основе ненасыщенной полиэфирной смолы ПН-1 или ПН-2 с такими армирующими материалами, как стеклянная ткань марки Т и штапельное стеклянное волокно, исследовалось в течение 15 лет на вертикальных резервуарах, предназначенных для хранения реактивного топлива. Установлено, что покрытие обладает высокой стойкостью к длительному воздействию, различных нефтепродуктов в интервале температур от —50 до + 50°С, к действию холодной и горячей воды и атмосферному воздействию. Степень вымывания и набухания покрытия в нефтепродуктах при 50 °С не превышает 0,5%, а в воде—1%. Качество нефтепродуктов при непрерывном контакте с покрытием в течение [c.82]
Нам не представляется возможным автоматически переносить результаты взаимодействия металлов с углеграфитовыми материалами на углеродные волокна из-за специфичности структуры последних мелкие кристаллиты, в которых базисные плоскости вдоль границы волокна разделены узкими порами (параллельно оси волокна) и границами наклона, или кручения (перпендикулярно ей). При указанной структуре прочность волокна должна определяться прочностью границ кристаллитов и быть чувствительной к любым изменениям их состояния. Наличие металла на поверхности углеродного волокна может влиять на состояние и свойства волокон, так как при этом возможно протекание таких процессов, как химическое взаимодействие, диффузия, частичное и, в предельном случае, полное растворение волокна. Таким образом, изучение влияния покрытия на свойства углеродного волокна необходимо для того, чтобы знать, насколько покрытие может ухудшать характеристики как армирующего компонента, так и композиционного материала в целом. [c.129]
Интересной модификацией химически связанных матов является рулонный материал (рядовой мат) из стеклянных волокон, полученных дутьевым методом. Этот материал представляет собой равномерный слой химически связанных, шта-пелированных в процеоое вытягавання стеклянных волокон диаметром 16—20 [г. Стеклянные волокна армированы в продольном направлении непрерывными некручеными стеклонитями. Ниже приводится характеристика этого материала [c.24]
Если один из компонентов КМ непрерывен во всем объеме, а другой является прерывистым, разъединенным в объеме композиции, то первый компонент называют матрицей, а второй — арматурой или армирующим элементом. Армирующие компоненты могут представлять собой различные волокна, порошки, микросферы, кристаллы и усы из органических, неорганических, металлическюс материалов или керамики. В качестве матрицы часто [c.68]
В большинстве работ, посвященных изучению структуры мембран, основное внимание уделено исследованию их микропористости [1, 3-5]. Для выявления микроканалов, в которых содержится раствор электролита, мембраны электролитически заполняли металлическим серебром, после чего срез мембраны фотографировали на э11ектронном микроскопе [3]. Блок [1] для этой цели использовал метод поверхностных реплик. Гомогенность мембран как на макроскопическом, так и па микроскопическом уровне Блок исследовал с помощью ионных красителей, способных взаимодействовать с ионогенными группами ионита [2]. Однако он указывал на возможные ошибки в полученных картинах распределения противоионов и их источники, которыми могли быть сорбция красителя волокнами армирующего материала и вероятность ситового эффекта из-за большого размера ионов красителя. [c.249]
Компоненты композитов не должны растворяться или иным способом поглощать друг друга. Они должны обладать хорошей адгезией и быть взаимно совместамы. Свойства КМ нельзя определить только по свойствам компонентов, без учета их взаимодействия. Каждая составляющая несет определенную функцию и вносит свой вклад в свойсгва композита. Рассмотрим требования, предъявляемые к армирующим наполнителям, например, к волокнам. [c.69]
Часто обсуждается вопрос, находятся ли в сформованном волокне остатки биоструктуры в неизменном или почти неизменном состоянии. Дискуссия по этому вопросу была вызвана работами ряда авторов в-вз Посредством электронно-микроскопических исследований они обнаружили в регенерированных волокнах, особенно при формовании высокополимерных и высоко-хонцентрированных растворов, фибриллярные структуры, которые ими рассматривались как остатки биологических структурных элементов. Этим элементам приписывалось определенное влияние на технологические свойства гидратцеллюлозных волокон. По мнению авторов, такие структурные элементы образуют в волокне армирующую систему. Однако в данном вопросе господствует иное воззрение. [c.190]
Находящаяся на поверхности волокна пленка замасливателя не только должна удовлетворять технологическим требованиям, но и обеспечивать необходимые свойства изделий, которые, как правило, представляют собой композицию из волокна (армирующей основы) и смол или лаков (связующего вещества). Например, большинство стеклотканей является армирующим компонентом в производстве электроизоляционных стеклолакотканей, а также стеклопластиков конструкционного, электротехнического, радиотехнического и другого назначения. Поэтому стеклоткани должны обладать высокими диэлектрическими и физико-механическими свойствами в условиях длительного воздействия на них влаги, повышенных температур и т. д. Замасливатель удовлетворяет этим требованиям только в том случае, если прочно сцепляется с поверхностью волокна, одновременно хорошо совмещается со смолой, обладает диэлектрической прочностью, негорючестью и т. д. [c.94]
УВ впервые были получены Эдисоном еще в 1882 г. Они длительное время применялись в электрических лампах накаливания, но с появлением вольфрамовых нитей УВ потеряли значение в этом направлении. Интерес к ним, появившийся в бО-е годы, обусловлен тем, что в отличие от стеклянных (а также органических) волокон они обладают весьма высоким модулем у-пругости, специфическими тепло- и электрофизическими свойствами. Уже сейчас по своей удельной прочности углеродные волокна в качестве армирующих материалов успешно конк-урируют с другими типами волокон. [c.58]
Метод инжекциояного формования имеияется для получения изделий сложной формы. В инструмент, соответствующий геометрии изделия, помещают армирующий материал из углеродного волокна, после чего впрыскивают требуемое количество связующего. В отдельных случаях производится впрыскивание смеси связуюшего с порошковым графитом или резаным стекловолокном. Далее изделие отверждается, удаляется из формы и окончательно обрабатывается. Применение этого метода позволяет повысить производительность процесса и получать изделия при пониженных давлениях. [c.526]
Свойства полимера, в частности его пластическая деформация до разрушения, определяют оптимальное содержание волокна. Напримеру при применении полифениленсульфида и полиа-рилэфирсульфбна с боковыми кардовыми группами максимальная прочность достигается при содержании углеродных волокон 25% (объем. ). Армирующий каркас из волокон уменьшает деформацию и таким образом способствует увеличению предела текучести и ударной вязкости композитов. [c.560]
Поливинилспиртовые волокна (винол, винилон, мьюлон) относя к высокопрочным и высокомодульным волокнам начальный модуль этого волокна в 2-5 раз выше, чем полиамидного, и в 1,5 раза больше, чем полиэфирного волокна. При повышении температуры прочность поливинилспиртового волокна снижается в меньшей степени, чем у большинства синтетических волокон. Это объясняется н шичием поперечных химических связей между макромолекулами. Наряду с достоинствами, поливинилспиртовое волокно имеет и ряд недостатков более узкая сырьевая база по сравнению с вискозным волокном, необходимость обработки формальдегидом (сшивающим агентом), сравнительно высокая стоимость прои щодства. В связи с )тим, а также с учетом высокой гигроскопичности волокон возможности использования их в качестве армирующих материалов в условиях длительного воздействия влаги и полярных жидкостей весьма ограничены. [c.175]
Тип армирующего волокна Содержание смолы, вес. % Сопротив- ление разрыву, кг/см Сопротив- ление изгибу, кг1см [c.234]
Кроме того, некоторые органические волокна добавляют для увеличения прочности при ударе стеклянного волокна, которое применяют в больших количествах. Применение органических волокон в значительной степени снижает термостойкость материала, поэтому их обычно вводят в небольших количествах. С успехом применяются полиэфирные и полиамидные волокна, а также поливи-нилспиртовые. В качестве армирующих иаполнителей рекомендуют использовать углеродное волокно и полиамидные на основе ароматических мономеров (Кевлар, Аренка). Некоторые другие волокна органического происхождения разрушаются или растворяются в феноле прп высоких температурах. [c.153]
При производстве высокоармнроваиных (высокая прочность при ударе) материалов получаются неудовлетворительные результаты, если используются валки с разной частотой вращения, поскольку при этом происходит измельчение материала и разрыв волокнистого армирующего компонента (стеклянного волокна, кордной пряжи и измельченных хлопковых волокон). В этом случае хорошие результаты дает применение мешалок с сигмоидальными лопастями и пропитка раствором фенольной смолы с последующей сушкой. С помощью червячных экструдеров можно приготовить смеси с удовлетворительными прочностными характеристиками. При введении соответствующих добавок можно получать пресс-композиции в таблетированной форме. [c.155]
Покрывный слой представляет собой покрытие, состоящее из грунтовочного слоя и слоя армипующего материала, пропитанного смолой ЭД-20 или ЭД-16. В качестве армирующего материала используют стеклянные, хлопчатобумажные или другие ткани, а также штапельные стеклянные волокна. Получают покрывный слой следующим образом сначала кистью наносят грунтовку, состав которой указан выше, а затем на нее укладывают внахлестку раскроенные и пропитанные эпоксидной. смолой полотнища армирующей ткани штапельное стеклянное волокно на поверхность наносят методом напыления. Затем слой армирующего материала прикатывают резиновыми или пластмассовыми роликами для удаления воздушных пузырей и улучшения адгезии между слоями. Продолжительность отверждения покрывного слоя при 15—20 °С составляет 12—15 ч. [c.83]
Перспективные армирующие высокотемпературные волокна для металлических и керамических композиционных материалов Текст научной статьи по специальности «Технологии материалов»
ВИАМ/2013-Тр-02-05
УДК 677.071.25
ПЕРСПЕКТИВНЫЕ АРМИРУЮЩИЕ ВЫСОКОТЕМПЕРАТУРНЫЕ ВОЛОКНА ДЛЯ МЕТАЛЛИЧЕСКИХ И КЕРАМИЧЕСКИХ КОМПОЗИЦИОННЫХ МАТЕРИАЛОВ
Е.Н. Каблов
доктор технических наук, академик РАН
Б. В. Щетанов
доктор технических наук
Ю.А. Ивахненко
Ю.А. Балинова
Февраль 2013
Всероссийский институт авиационных материалов (ФГУП «ВИАМ» ГНЦ) — крупнейшее российское государственное материаловедческое предприятие, на протяжении 80 лет разрабатывающее и производящее материалы, определяющие облик современной авиационно-космической техники. 1700 сотрудников ВИАМ трудятся в более чем тридцати научноисследовательских лабораториях, отделах, производственных цехах и испытательном центре, а также в четырех филиалах института. ВИАМ выполняет заказы на разработку и поставку металлических и неметаллических материалов, покрытий, технологических процессов и оборудования, методов защиты от коррозии, а также средств контроля исходных продуктов, полуфабрикатов и изделий на их основе. Работы ведутся как по государственным программам РФ, так и по заказам ведущих предприятий авиационно-космического комплекса России и мира.
В 1994 г. ВИАМ присвоен статус Государственного научного центра РФ, многократно затем им подтвержденный.
За разработку и создание материалов для авиационно-космической и других видов специальной техники 233 сотрудникам ВИАМ присуждены звания лауреатов различных государственных премий. Изобретения ВИАМ отмечены наградами на выставках и международных салонах в Женеве и Брюсселе. ВИАМ награжден 4 золотыми, 9 серебряными и 3 бронзовыми медалями, получено 15 дипломов.
Возглавляет институт лауреат государственных премий СССР и РФ, академик РАН, профессор Е.Н. Каблов.
Статья подготовлена для опубликования в журнале «Авиационные материалы и технологии», №2, 2005 г.
УДК 677.071.25
Е.Н. Каблов, Б.В. Щетанов, Ю.А. Ивахненко, Ю.А. Балинова
ПЕРСПЕКТИВНЫЕ АРМИРУЮЩИЕ ВЫСОКОТЕМПЕРАТУРНЫЕ ВОЛОКНА ДЛЯ МЕТАЛЛИЧЕСКИХ И КЕРАМИЧЕСКИХ КОМПОЗИЦИОННЫХ МАТЕРИАЛОВ
Рассмотрены современное состояние проблемы производства и перспективы применения армирующих волокон для металлических и керамических композиционных материалов (KM). Описаны свойства волокноупрочненных композитов с различными матрицами и волокна, которые целесообразно применять для каждого типа КМ. Приведены области применения керамических и металлических композитов.
Ключевые слова: композиционный, материал, авиация, волокна, металлический, керамический, температура, прочность.
E.N. Kablov, B.V. Schetanov, Yu.A. Ivakhnenko, Yu.A. Balinova
PERSPECTIVE REINFORCING HIGH-TEMPERATURE FIBRES FOR METAL AND CERAMIC COMPOSITE MATERIALS
Current state of production and prospect of application reinforcing fibers for metal and ceramic composite materials (CM) are considered. Properties of various matrix composites and fibers for each type of CM are described. Fields of application of ceramic and metal composites are given.
Keywords: composite, material, aviation, fibers, metal, ceramic, temperature, strength.
Наличие композиционных материалов — полимерных, керамических и металлических — является ключевым моментом при разработке перспективных систем для турбовинтовой и гиперзвуковой авиации. Развитие так называемых высокоэффективных искусственных волокон, имеющих высокую прочность, жесткость, термостойкость, позволит создать новую генерацию КМ.
В том случае, когда термостойкость и прочность материала не являются критическими факторами, используются относительно дешевые полимерные (акрилаты, эпоксиды, поликарбонаты) и металлические материалы (алюминий, сталь, медь, вольфрам). Однако когда высокая эффективность является контролирующим фактором применения материала (аэрокосмическая отрасль, подводные суды), необходимы перспективные материалы с их высокой прочностью, жесткостью, низкой плотностью и высокой стойкостью в агрессивной атмосфере. Традиционные металлические, полимерные и керамические материалы не удовлетворяют многим из этих требований. На рисунке приведены ориентировочные температурные пределы использования различных структурных материалов [1].
Использование волокон приводит к возрастанию прочности и жесткости КМ в направлении оси волокна в десятки раз по сравнению со свойствами материала монолитной формы при одном и том же химическом составе. При этом упрочнение матрицы длинными волокнами будет заведомо больше, чем ее упрочнение частицами и короткими волокнами типа нитевидных кристаллов («усов»). Этим и обусловлен интерес к непрерывным высокоэффективным волокнам.
Высокоэффективные искусственные волокна, к которым относят в первую очередь волокна на основе карбида кремния, углеродные, борные, на основе оксида алюминия и ряд других, представляют в настоящее время основную область разработок волоконной индустрии. Данные волокна имеют свои особенности, которые и обусловливают их применение. Так, бескислородные углеродные волокна сохраняют свою прочность в области сверхвысоких температур при условии отсутствия контакта с кислородом. Полимерные волокна имеют низкую температуру
3000′
2000-
1000-
т к
п п Й н о
-г ®
£ Л
3 ^
К о
2 X
3 ^ ^ I § *
І = ■
и
2 ^ и п
и и
сз
% У
1500
О
1000
— 500
Полимеры Металлы Керамика
Максимальная температура применения различных конструкционных материалов
применения, но при этом они легче углеродных и керамических волокон и радиопро-зрачны. Керамические волокна устойчивы в окислительной атмосфере, но теряют свою прочность при высоких температурах.
Введение волокон в высокотермостойкие сплавы повышает стойкость последних к высокотемпературной ползучести, введение в керамические материалы — повышает тре-щиностойкость. Кроме этого, важными причинами выбора КМ, при равных с традиционным материалом механических характеристиках, является более низкая плотность КМ и возможность относительно простого введения в него сенсоров и оптических волокон для контроля нагрузок и повреждений материала при его эксплуатации.
Суммируя вышесказанное, можно отметить, что волоконноупрочненные КМ отличаются высокими значениями модуля упругости и прочности, низкой плотностью, возможностью контроля жесткости, термического расширения и электропроводности, высокой стойкостью к коррозии и высокотемпературной ползучести, возможностью создания интеллектуальных материалов.
Новая область применения таких материалов — гиперзвуковая авиация — может потребовать дальнейшего прогресса в улучшении характеристик волокон. При температурах эксплуатации существующие волокна отличаются значительным ростом зерна и окислением, что приводит к снижению модуля и прочности, возрастанию ползучести, термического расширения и к взаимодействию с матрицей.
Следует отметить, что для развития работ по волоконноупрочненным КМ необходимо наличие отечественной базы перспективных волокон, играющих ключевую роль в производстве КМ, — существование такой базы зависит от долгосрочной поддержки исследований со стороны Правительства.
Различные типы волокон могут обсуждаться на основании классификации по температурам применения матрицы. Различают полимерные матрицы с температурой применения до 425°С, металлические — с температурой применения 815-1370°С и керамические — с температурой применения 1100-1650°С.
Использование металла в качестве матрицы позволяет передать конечному композиту такие важные свойства, как прочность и жесткость при растяжении (в продольном и поперечном направлении) и при сдвиге. Например, алюминий, упрочненный волокнами бора, демонстрирует прочность, равную прочности неармированной матрицы, и поперечную жесткость, в два раза превышающую жесткость матрицы. Кроме этого, важны также электрические и термические характеристики композита, сходные с характеристиками матрицы. Положительным моментом является возможность использования традиционного
оборудования для получения металлических композиционных материалов (МКМ). С другой стороны, значительные сложности при производстве МКМ вызывают высокая температура их получения и взаимодействие волокна и матрицы, приводящие к деградации их свойств. Кроме того, различное термическое расширение волокна и матрицы приводит к разрушению композита при термоциклировании. Наконец, композит может иметь меньшую коррозионную стойкость, чем матрица, вследствие изменения микроструктуры композита и разницы электрохимического потенциала волокно-матрица.
Потребности рынка в МКМ непредсказуемы. Сравнивать «статус» МКМ в разных странах сложно, вследствие того что основная деятельность ученых сосредоточена на стадии разработки и информация об этих разработках широко не публикуется.
Для аэрокосмического применения США разработали подкосы фюзеляжа для Space Shuttle. Советский Союз приложил значительные усилия в двух областях — разработке бо-ралюминия и SiC-упрочненного титана. Европейский аэрокосмический консорциум разрабатывает МКМ с титановой матрицей, армированной волокнами SiC производства British Petroleum.
В Японии объединение усилий правительства и промышленности привели к широкому применению МКМ для поршней двигателей внутреннего сгорания (фирма «Тойота»). Кроме того, это объединение имеет своей целью развитие высокотемпературных волокон и композитов для гиперзвуковой авиации.
Будущее МКМ связано с их значительным превосходством над монокристалличе-скими металлическими и полимер-матричными системами. Для высоконагруженных конструкций стальные части могут быть заменены МКМ на титановой матрице. Применение МКМ для частей турбины, эксплуатирующихся при температуре выше 500°С, вместо использующихся в настоящее время суперсплавов позволит кардинально снизить массу изделия и повысить эффективность.
Основные проблемы в развитии высокоэффективных МКМ связаны с упрочняющими волокнами. Главной из них является взаимодействие волокна и матрицы при высоких температурах получения и эксплуатации МКМ, что требует дополнительных усилий по разработке защитных покрытий на волокна и значительно повышает трудоемкость получения волокна и его стоимость.
Введение волокон в керамическую матрицу приводит к получению конструкционного керамического материала, который, сохраняя важные свойства керамики — такие как высокотемпературные стабильность и стойкость к воздействию окружающей среды, — при этом снижает хрупкость материала. Превосходная термостабильность керамических ком-
позиционных материалов (ККМ) по сравнению с ПКМ и МКМ делает их уникальными для высокотемпературного применения, — например для таких деталей, как форсунки сгорания турбин. Сочетание химической стойкости, относительно низких плотности и стоимости делают ККМ очень привлекательными для многих потенциальных применений.
Кроме конструкционного применения, существует много областей, где требуются специальные свойства КМ, такие как электрические и электромагнитные, теплопроводность, коррозионная стойкость в агрессивной среде и др. [1].
В настоящее время существует ряд фирм, производящих волокна для перспективных КМ (см. таблицу 1).
Таблица 1
Высокоэффективные волокна для МКМ и ККМ [2, 3, 4] _____________
Произво- Марка Состав (содержание эле- Плотность, Диа- Е СТв ?max,
дитель волокна ментов, %) г/см3 метр, мкм ГПа °C
Nicalon NL2QQ 57 БІ; 31 С; 12 0 2,55 14 22Q 3,Q <13QQ
Nippon- Carbon Hi Nicalon 62 БІ; 32 С; 0,5 0 2,74 14 27Q 2,8 <14QQ
Hi Nicalon-S 68,9 БІ; 30,9 С; 0,2 0 3,10 12 42Q 2,6 <14QQ
Textron SCS-6 БІС на С 3,0 140 39Q 4,Q <14QQ
Nextel 65Q 89 А1203; 10 гЮ2; 1 У203 4,1 10-12 358 2,5 1Q8Q
3M Nextel 72Q 85 А1203; 15 Бі02 3,4 10-12 26Q 2,1 115Q
Nextel 61Q 99 А1203 3,88 14 373 2,93 1QQQ
CeraFib CeraFib 99 99 А1203 9-11 >3QQ > 2,Q 12QQ-
GmbH CeraFib 75 75 АЬ03, 25 БІ02 135Q
Saphikon Saphikon 100 А1203 3,96 125 47Q 3,5 125Q
Следует особо отметить, что достижение высоких механических характеристик вышеприведенных волокон стало возможным вследствие выполнения специальных долгосрочных государственных программ, объединяющих усилия правительства, промышленности и науки. Так, в США, благодаря государственной поддержке, за десять лет удалось повысить прочность волокон Кехіеі 610 почти в два раза [3].
В последние годы в России также предпринимаются определенные усилия по введению долгосрочных государственных программ, направленных на восстановление производств армирующих волокон, таких как БІС, А1203, разработку КМ на их основе. В настоящее время в ВИАМ производит поликристаллические дискретные и непрерывные волокна А1203 — муллит [5] для высокотемпературных керамических матриц, ведутся работы по созданию армирующих волокон состава 99% А1203 для композитов с металлической матрицей [6]
ЛИТЕРАТУРА
1. High-performance synthetic fibers for composite. Report of the Committee on High-performance Synthetic Fibers for Composite.- Washington: Publication NMAB-458 National Academy Press, 1992, 144 р.
2. Ceramic fibers and coatings. Advanced materials for the twenty first sentury. Report of the Committee on Advanced Fibers for Hi-Temperature Ceramic Composites.- Washington: Publication NMAB-494 National Academy Press, 1998, 110 р.
3. Wilson D. M., Visser L. R. High-performance oxide fibers for metal and ceramic Composites //Processing of Fibers & Composites Conference.- Barga (Italy), 2000 (May 22), 31 р.
4. CeraFibGmbH: [сайт]. — D., — Режим доступа http://www.cerafib.de/
5. Ивахненко Ю.А., Бабашов В.Г., Зимичев А.М., Тинякова Е.В., Высокотемпературные теплоизоляционные и теплозащитные материалы на основе волокон тугоплавких соединений: Сб. ст. к 80-летию ВИАМ. — М.: ВИАМ, 2012 — С. 380-385.
6. Щетанов Б.В., Балинова Ю.А., Люлюкина Г.Ю., Соловьева Е.П. Структура и свойства непрерывных поликристаллических волокон a-Al2O3. // Авиационные материалы и технологии. — 2012 — №1.- С. 13-17.
Классификация армирующих волокон в КМ
В теории, армирующим элементом может быть все, от соломы до железной арматуры. Цель статьи – простое перечисление и попытка классифицировать типы армирующих волокон (АВ), применяемые в современном композитостроении.
Существует большое разнообразие АВ, но
применение большинства из них широко не распространено по причине сложной и
дорогой технологии получения.
Классификация
АВ
Самая первая подгруппа, самый высокий класс или признак, по которому принято разделять волокна: происхождение. По этому признаку они делятся на: натуральные и химические. Натуральные — это природные волокна, образовавшиеся в природе без участия человека. Они могут быть растительного (лен), животного (шерсть) или неорганического происхождения (асбест). Химические волокна в свою очередь делятся на три больших класса: искусственные, неорганические и синтетические.
Искусственные нити созданы путем химических превращений из натуральных веществ, то есть в основе химических искусственных нитей лежат натуральные полимеры животного и растительного происхождения.
Неорганические химические волокна – созданы человеком из имеющихся в природе неорганических материалов, таких как: различные металлы, кварц, базальт и т.д.
Синтетические нити сформованы из высокомолекулярных полимеров, которые не встречаются в природе. То есть высокомолекулярные соединения, из которых формуются синтетические нити, получены синтезом природных низкомолекулярных соединений.
Классификация
синтетических АВ
Синтетические волокна принято разделять на две группы: карбоцепные и гетероцепные.
Карбоцепные — это волокна, макромолекулы которых состоят только из атомов углерода. Карбоцепные синтетические волокна:
Полиакрилонитрильные
Поливинилхлоридные
Поливинилспиртовые
Полиолефиновые
В макромолекулах гетероцепных нитей помимо атомов углерода есть еще атомы других элементов. Гетероцепные синтетические волокна:
Полиамидные
Полиэфирные
Полиуретановые
Разделение на карбо- и гетероцепные считается общепринятым, но есть волокна не подходящие к данной классификации. Например, среди множества полиамидных нитей есть нити как с карбо — так и гетероциклами в цепи.
Краткое
описание синтетических нитей
Полиакрилонитрильные нити – по механическим свойствам похожи на шерстяные. Растяжимость порядка 20-30%. Недостатком можно указать низкое противостояние истиранию. ПАН является сырьем для производства углеродных волокон, однако УВ можно получить так же путем переработки и других исходных материалов, таких как вискозных волокон и нефтяных или каменноугольных пеков.
Поливинилхлоридные – известны высокой химической стойкостью, морозостойкостью и низкой электропроводностью.
Поливинилспиртовые – наиболее гигроскопичны из всех видов синтетических волокон, устойчивы к истиранию и имеют высокую теплостойкость.
Полиэтилен — в беспорядочном состоянии молекул, каким мы привыкли вдеть обычно полиэтилен. Материал имеет очень низкие механические свойства. Выравнивание молекул, которое проходит формовании филаментов придает волокну очень высокую прочность на растяжение. Имеет низкую прочность на сжатие в ламинате.
Полипропилен — имеет очень низкую плотность и нулевую гигроскопичность, стоек к действию кислот и щелочей.
Полиэфир – полиэфирные нити обладают хорошей ударной прочностью но низким модулем. Так же выделяется низкой стоимостью и абразивной стойкостью.
Арамид – имеет хорошую ударостойкость, широко применяется в баллистике. Некоторые виды имеют низкую устойчивость к ультрафиолету.
Полиуретан – эластомерная нить, имеет высокую упругость и эластичность.
В заключение
Вообще имеется огромное количество армирующих нитей. Постоянно появляются принципиально новые виды. Так же, активно применяются методы модифицирования нитей с целью придания тех или иных потребительских свойств, таких как: профилирование, изменение надмолекулярной структуры, введение красителей и добавок и т.д. Так что перечислить и затронуть все виды АВ не представляется возможным. Статья позволит иметь общее понимание об используемых волокнах. Даже если останется понимание того что АВ неприлично много, цель статьи будет достигнута.
SammaS — Армирующие материалы — Справочник материалов
Армирующие материалы — для стеклопластиков это основной внутренний каркас, от свойств которого непосредственно зависят физико-механические и прочностные характеристики конечного изделия. Армирующие стекломатериалы предназначены для армирования ламината на основе эпоксидных, полиэфирных и винилэфирных смол. В качестве армирующих могут использоваться самые различные материалы. Но самым распространенным материалом, конечно же, является стеклянное волокно, которое обеспечивает готовому изделию самую высокую механическую прочность (при прочих равных условиях). Способ формования стеклопластиковых изделий во многом определяется выбором используемого армирующего материала. Например: стеклонити используются при окружной намотке оболочек, изготовлении труб и цилиндров; рубленное волокно наиболее удобно применять при формовании методом напыления, а также для предварительной формовки заготовок; стеклоткани и стекломаты хорошо подходят для методов контактного формования и прессования, а также для пропитывания под давлением или при вакуумизации.
Стекловуаль используется для формования слоя, следующего непосредственно за гелькоутом, с целью уменьшения проявления структуры основного стекломатериала на поверхности готового изделия из стеклопластика, а также для создания в трубах и емкостях из стеклопластика слоя с обильным содержанием химически стойкой полиэфирной смолы, обращенного непосредственно к агрессивной среде. Подробнее…
Существуют три основных типа матов из стекловолокон: маты из резаных нитей, из непрерывных нитей и декоративные маты или покрытия. Стекломат — представляет собой нетканое полотно, получаемое резкой стекловолокон или непрерывного жгута на штапельки длиной 25-50мм. Волокна имеют преимущественно случайное распределение в горизонтальной плоскости и связанных друг с другом полимерным связующим (порошковым либо эмульсионным). Плотность таких матов составляет 0,229…0,916 кг/м2. Маты, получаемые из нерезаных непрерывных жгутов стекловолокна раскладываются и соединяются в виде спирали. Такие маты достаточно упруги при сравнительной разреженности структуры, а благодаря механическому переплетению не требуют дополнительной связи для создания необходимой прочности. Подробнее…
Для армирования пластиков могут использоваться самые разнообразные волокна, но для высокопрочных пластиков чаще всего используются стеклянные волокна. Это объясняется удачным сочетанием их свойств и не в последнюю очередь низкой стоимостью большого разнообразия промышленных стекловолокон. Секловолокна по прочности превосходят все другие распространенные конструкционные материалы. Так, прочность неповрежденных волокон из E-стекла равна в среднем 365 кг/мм2, они имеют довольно высокий модуль Юнга (5-11)·103 кг/мм2 и на много превосходят в этом отношении армируемые ими полимеры. Поэтому в стеклопластиках большую часть нагрузки воспринимают волокна. А поскольку плотность стекла сравнительно низкая (~2.5 г/см3), стекловолокна имеют высокую удельную прочность и удельный модуль, что особенно важно при применении этих материалов в авиации и на водном или сухопутном транспорте и т.д. Подробнее…
Стеклоровинг — это непрерывная прядь, которая изготавливается из некручёных нитей стекловолокна. Подробнее…
Стеклосетка — материал ячеистой структуры, полученный переплетением стеклянных нитей и ровингов под прямым углом. Скрепляют нити лазерной или ультразвуковой сваркой, а так же химическим путем. Ткут сетки из аплюмоборосиликатной (бесщелочной) стеклонити с заданным размером ячеек, после чего пропитывают полимерным составом. В зависимости от плотности, размера ячейки и вида пропитки, стеклосетки имеют различное назначение. Подробнее…
Стеклоткань представляет собой полотняной материал из стеклонитей, полученный в процессе ткацкого производства путем переплетения взаимно перпендикулярных продольных и поперечных стеклянных волокон диаметром 3-100 мкм. Этот материал широко используется в самых различных областях автомобиле- и судостроении, химической промышленности, при проведении строительных и ремонтных работ, приборостроении, электромашиностроении и т. Отличительными особенностями материалов, изготовленных на ее основе, являются: долговечность, повышенная устойчивость к коррозии, высокая прочность, большая стойкость к разложению, воздействию химикатов и износу. А так же нетоксичность, негорючесть, невзрывоопасность и большой диапазон рабочих температур. Подробнее… |
Армирующее волокно — обзор
17.2.2 Волокна
Армирующие волокна — это либо натуральные волокна (животные, минеральные или целлюлозные волокна), либо синтетические искусственные волокна (стекло, углерод и полимер). Здесь основное внимание уделяется искусственным стеклянным волокнам, которые в целом являются доминирующими волокнами, используемыми для больших недорогих конструкций, таких как лопасти ротора ветряных турбин. Три основных компонента стеклянных волокон — это диоксид кремния (SiO 2 ), оксид кальция (CaO) и оксид алюминия (Al 2 O 3 ). Смешивание основных компонентов в различных соотношениях и добавление других минералов, таких как MgO, B 2 O 3 , F и т. Д., Приводит к значительно разным стеклам с различными механическими, химическими и термическими свойствами, что придает стеклу качества для различных применений. Очевидно, что существует несколько видов стекловолокна, обладающих различными характеристиками, свойствами и стоимостью.
Свойства отдельных волокон, которые следует учитывать при применении лопастей ротора, — это плотность, диаметр, жесткость и, в определенной степени, прочность.Основным движущим фактором при выборе качества волокна является стоимость жесткости (ГПа / евро). Волокна из E-стекла (электронного качества) с жесткостью 72–74 ГПа доминируют на рынке из-за низкой стоимости. Однако развитие рынка в сторону более крупных лезвий привело к увеличению спроса на волокна с более высокой жесткостью, и большинство производителей волокон ввели конкурентоспособные по стоимости волокна из H-стекла с жесткостью 80–88 ГПа, что на 10–20% выше. по жесткости, чем у E-стекла, примерно при такой же стоимости жесткости.Кроме того, композиты с волокнами H-стекла демонстрируют повышенную устойчивость к усталости, что также является причиной промышленного интереса.
Свойства стекловолокна обычно сообщаются производителями, и конечный пользователь должен знать, что методы, используемые для измерения, особенно жесткости, различны и часто несопоставимы. Жесткость волокна можно измерить с помощью измерения звукового модуля, используя соотношение между скоростью звука, массой и жесткостью. Обычно это дает завышенные значения жесткости по сравнению с механическими измерениями отдельных волокон, пучков волокон или обратными расчетами для ламинатов с однонаправленной намоткой.Жесткость отдельного волокна можно измерить как испытание на статическое растяжение; однако, поскольку площадь поперечного сечения волокна зависит от погрешностей измерения непостоянного поперечного сечения, часто наблюдаются отклонения до 2–7%. Другой метод, который следует использовать, — это испытания собственной частоты вибрации, при которых параметрами, дающими неопределенность, являются контроль предварительного напряжения и плотности отдельных волокон. Погрешности обратных расчетов по измерениям на пучках волокон и однонаправленных ламинатах или тканях являются оценкой содержания волокна и прямолинейности волокон в тестовых образцах.Для наиболее равномерного сравнения необходимо хотя бы убедиться, что производитель волокна и конечные пользователи используют один и тот же метод тестирования.
Предел прочности и усталостные характеристики чистых стекловолокон измеряются при испытаниях отдельных волокон или пучков и однонаправленных ламинатов. Эти измерения показывают те же неточности, что и измерения жесткости; однако для лопастей ротора характеристическая прочность стекла намного превышает критические расчетные значения прочности, обычно допускаемые в конструкции лопастей.В конце концов, прочность часто не является большой проблемой при выборе волокон, а жесткость является доминирующим свойством. Что касается осевой расчетной деформации ламината, Germanischer Lloyd (Germanischer Lloyd, 2010) предоставляет следующие пределы деформации: 0,35% (растяжение) и -0,25% (сжатие). Эти предельные значения ниже обычной деформации разрушения стекла Е в диапазоне около 2–3% при сжатии и растяжении, соответственно, что также указывает на довольно низкие значения деформации, допустимые в конструкции лопасти.
Стекловолокно обрабатывается путем плавления стекла в печи с последующей экструзией расплавленного стекла через пластину втулки с большим количеством сопел. Количество сопел дает количество волокон в пучке, также называемом ровингом, жгутом или прядью. Поскольку диаметры стекловолокна в ровинге могут значительно различаться, размер ровинга часто задается как значение TEX, определяемое как линейная массовая плотность волокон с единицей измерения в граммах на 1000 м. Типичные значения TEX для стеклянных ровингов колеблются от 100 до 9600.Число волокон в ровинге называется числом K , и его можно связать со значением TEX, зная плотность стекловолокна, ρf, и средний диаметр волокна, Af:
K = TEX / [ρf ∗ Af ]
Игра цифрами: плотность стекла 2,63 г / см 3 , диаметр волокна 23 мкм → K примерно равен TEX. Влияние числа K и диаметра волокна на усталостные характеристики композитов еще предстоит определить.
Виды армирования волокном | Автоматизированная динамика
Существует много различных типов волокон, которые можно использовать для армирования композитов с полимерной матрицей.Наиболее распространены углеродные волокна (AS4, IM7 и др.) И стекловолокно (S-стекло, E-стекло и др.). Как и в случае с матрицей, выбранное волокно будет определяться конечным применением.
Углеродные (графитовые) волокна
Углеродные волокна являются проводящими, имеют отличное сочетание высокого модуля упругости и высокой прочности на разрыв, имеют очень низкий (слегка отрицательный) КТР и обладают хорошей устойчивостью к высоким температурам.
Углеродные волокна часто классифицируют по модулю упругости. Обычно в композитах используются пять категорий углеродных волокон; низкий модуль, стандартный модуль, промежуточный модуль, высокий модуль и сверхвысокий модуль. Точное пороговое значение для этих категорий будет варьироваться в зависимости от использованной справочной информации, но в целом волокна с низким модулем упругости имеют модуль упругости менее 30 Msi, а волокна со сверхвысоким модулем имеют модуль упругости более 75 Msi. Для сравнения: сталь имеет модуль упругости при растяжении 29Msi.
По мере увеличения модуля волокна становятся более хрупкими, более дорогими и сложными в обращении. Кроме того, прочность на разрыв волокон обычно увеличивается по мере увеличения модуля от низкого до среднего, но затем имеет тенденцию к снижению в волокнах с высоким и сверхвысоким модулем.Т.е. прочность на разрыв углеродных волокон имеет тенденцию быть наибольшей для волокон с промежуточным модулем упругости. По этим причинам волокна со стандартным и промежуточным модулем упругости, как правило, дают наилучшие общие характеристики, если только приложение не ориентировано на жесткость. Это становится еще яснее, если принять во внимание цену и доступность волокна.
Изображение №1: Монтажная пластина из композитного материала, армированного углеродным волокном. Углеродное волокно было выбрано из-за его очень низкого КТР и высокой прочности.
Стекловолокно
Стекловолокно, как следует из его названия, представляет собой стекло, из которого скручены волокна. Стекловолокно не такое прочное или жесткое, как углеродное волокно, но его характеристики делают его востребованным во многих сферах применения. Стекловолокно не проводит электричество (т. Е. Изолятор) и обычно невидимо для большинства типов передач. Это делает его хорошим выбором при работе с электрическими или радиовещательными приложениями.
Существует пять основных типов стекловолокна.A-стекло (щелочное стекло) с хорошей химической стойкостью, но с более низкими электрическими свойствами. C-стекло (химическое стекло) с очень высокой химической стойкостью. E-стекло (электрическое стекло), которое является отличным изолятором и сопротивляется атакам воды. S-Glass (структурное стекло), оптимизированное по механическим свойствам. D-стекло (диэлектрическое стекло), которое обладает лучшими электрическими свойствами, но не имеет механических свойств по сравнению со стеклом E и S.
E-стекло и S-стекло, безусловно, являются наиболее распространенными типами, встречающимися в композитах.Эти типы имеют хорошее сочетание химической стойкости, механических свойств и изоляционных свойств. Из этих двух стекло E предлагает более привлекательную экономику, а S-стекло предлагает лучшие механические характеристики.
Изображение №2: Изоляционная втулка из композитного армированного стекловолокном материала. В этом случае волокно было выбрано из-за его изоляционных свойств и прочности для передачи нагрузок между металлическими компонентами.
Прочие волокна
Хотя углеродные волокна и стекловолокно являются наиболее распространенными армирующими элементами в термопластичных композитах, существуют и другие варианты.Арамидные волокна (такие как Kevlar® и Twaron®) и борные волокна используются в композитах и обладают некоторыми полезными свойствами (превосходной ударной вязкостью и прочностью на сжатие, соответственно). Однако они обладают характеристиками, которые ограничивают их использование (восприимчивость к легкой / сложной механической обработке и хрупкость, соответственно). Третьи включают керамические волокна, такие как SiC или оксид алюминия. Они могут быть привлекательны своими компрессионными, изоляционными или высокотемпературными свойствами.
Персонал
Automated Dynamics может помочь с выбором наилучшего оптоволокна для вашего приложения на основе потребностей программы, доступности, экономики и других соображений.
Что случилось с бетоном, армированным волокном?
Укрепляет ли бетон добавление фибры или как?
Бетон, армированный сталью, является основой нашего современного общества. Армирование в бетоне создает композитный материал, при этом бетон обеспечивает прочность против напряжения сжатия, в то время как арматура обеспечивает прочность против напряжения растяжения. Но, хотя стальная арматура устраняет одно из величайших ограничений бетона, она создает совершенно новую проблему: коррозия встроенной стальной арматуры является наиболее распространенной формой разрушения бетона. Так что мы с этим делаем?
Эй, я Грейди, и это практическая инженерия. В сегодняшнем выпуске мы тестируем некоторые инновации в армировании бетона.
Хотя незащищенная сталь естественно склонна к коррозии или ржавчине, когда она врезается в бетон, определенные факторы обычно работают для ее защиты. Во-первых, это очевидная защита, заключающаяся в простой защите от внешней среды относительно непроницаемым и прочным материалом. Вода и загрязнения обычно не проходят через бетон к стали.
Вторая форма защиты — щелочная среда. Высокий pH нормального бетона создает тонкий оксидный слой на стали, который обеспечивает защиту от коррозии.
Но в некоторых случаях этой защиты недостаточно. Одним из основных источников коррозии арматуры является соль. Будь то воздействие соленой воды вблизи морской среды или применение противообледенительных солей, чтобы сделать дороги более безопасными в зимний период, эти ионы хлора могут проникать через бетон, разъедая стальную арматуру. А когда сталь корродирует, образуется оксид железа, который расширяется внутри бетона. Это расширение создает напряжение, иногда называемое оксидным подъемом, и является одной из основных причин разрушения бетона.
Трещины в крышке
Итак, как же предотвратить попадание ионов хлора и других загрязняющих веществ в сталь и появление коррозии? Первая линия защиты — укрытие.
Покрытие — это минимальное расстояние между внешней поверхностью бетона и арматурной сталью.
И, в зависимости от воздействия и области применения, определенные коды указывают разное количество бетонного покрытия, обычно от 25 до 75 миллиметров или от 1 до 3 дюймов. Укрытие — одна из причин, по которой хорошая бетонная работа требует так много усилий, прежде чем бетон вообще появится на стройплощадке. Установка прочной опалубки и большого количества проволоки, связывающей всю арматуру вместе, помогает быть абсолютно уверенным, что, несмотря на все толчки, хождение и общий хаос, который возникает, когда пора на самом деле укладывать бетон, арматурный стержень остается там, где он был задуман. встроены в конечный продукт.Игнорирование этих шагов может привести к тому, что арматурный стержень опустится на дно плиты или окажется слишком близко к внешней поверхности до того, как бетон затвердеет, что в конечном итоге приведет к преждевременной коррозии арматуры из-за отсутствия покрытия.
Но даже при соответствующем укрытии любая трещина в бетоне может привести к прямому контакту загрязняющих веществ и воды с арматурой. И вас не удивит, что трещины в бетоне встречаются не так уж и редко. Большинство бетонов дает усадку при отверждении, что может привести к образованию трещин.Изменения температуры также вызывают расширение и сжатие, что может привести к растрескиванию. Бетон также может треснуть при нормальных, ожидаемых условиях нагрузки из-за того, как сталь воспринимает напряжения в материале.
Одним из способов решения этой проблемы является предварительное напряжение арматурного стержня. Эту тему я кратко обсуждал в предыдущем видео, и я хотел бы углубиться в нее в будущем. Но сегодня я хочу показать еще один вариант уменьшения этих трещин.
Бетон, армированный волокнами
Бетон, армированный фиброй, — это во многом именно то, что вы ожидали.Это ни в коем случае не новая идея, но наше понимание и использование различных видов волокон в бетонной смеси продолжает расти. Добавление стекла, стали или синтетических волокон в бетон может дать много преимуществ, но одним из наиболее важных является контроль трещин .
Я построил три почти идентичных железобетонных балки, чтобы показать, как это работает, и дал им настояться около недели. У первого в качестве арматуры используется только стальная арматура. Я использую свой гидравлический пресс, чтобы проверить прочность каждой балки и посмотреть, как она работает до отказа.И я использую тонны в качестве меры силы на этих балках, просто потому, что это то, что говорит датчик, но единицы измерения совершенно произвольны для демонстрации. (Если вы предпочитаете SI [Système Internationale, или метрическую систему], просто представьте, что это метрические тонны. )
Когда я увеличиваю нагрузку на балку, вы видите трещины, начинающиеся всего с 3 тонн. Эти трещины образуются из-за того, что сталь немного растягивается, принимая на себя растягивающее напряжение в бетоне. Балка прекрасно выдерживает нагрузку и даже не близка к разрушению, но бетон не может растягиваться вместе со сталью, поэтому он должен треснуть. Вы можете себе представить, как эти трещины могут позволить воде и воздуху контактировать с арматурой и, в конечном итоге, разрушить бетон.
(Эти трещины — важная часть этой демонстрации, но я пошел дальше и увеличил нагрузку до тех пор, пока балка не сломалась, потому что, эй, вот для чего гидравлические прессы подходят?)
Для следующих двух балок я включил волокна в бетонную смесь: одна балка имеет стальные волокна, а другая — стекловолокна. Стальная арматура и волокна объединяются, чтобы противостоять растягивающим напряжениям в балках.Арматурный стержень обеспечивает крупномасштабное армирование, чтобы противостоять растяжению по всему элементу конструкции, а волокна обеспечивают мелкомасштабное армирование, чтобы противостоять локальному напряжению, которое вызывает растрескивание.
Когда я нагружаю эти балки по 3 тонны, не видно ни единой трещины. Фактически, для обоих этих балок я не заметил образования трещин, пока они не увеличились вдвое. да и то трещины были намного меньше. Обе балки вышли из строя примерно при той же нагрузке, что и первая, чего я и ожидал. Как я уже сказал, волокна на самом деле не добавляют большой прочности балке, но вы легко можете видеть, что они могут иметь большое значение для предотвращения коррозии стальной арматуры.
Альтернативы стальной арматуре
Вы можете спросить, почему мы вообще используем сталь для армирования? Сталь относительно недорогая, хорошо испытанная и прочная, но существует множество других материалов с превосходными механическими свойствами, которые не подвержены коррозии. Для очень агрессивных сред мы иногда используем арматуру с эпоксидным покрытием или даже нержавеющую сталь, но есть некоторые новые альтернативы, такие как армированные волокном полимеры или стержни из стеклопластика. Это арматура из базальта, переплавленного вулканического камня, пропускаемого через крошечные сопла для создания чрезвычайно прочных волокон.
Такие варианты часто стоят дороже, чем стальная арматура, а в некоторых случаях намного дороже. Но основным препятствием для использования этих новых, более инновационных типов арматуры является не только стоимость. Легко видеть, что эти дополнительные затраты могут быть компенсированы увеличением срока службы бетона. Еще одно препятствие происходит просто из-за отсутствия повсеместного использования. Инновации в гражданском строительстве происходят медленно, потому что последствия отказа очень велики. Обретение уверенности в конструкции имеет такое же отношение к инженерной теории, как и к простому наблюдению за тем, насколько хорошо аналогичные конструкции работали в прошлом.
Но многие инженерные катастрофы произошли не из-за плохой конструкции, а из-за плохого обслуживания, поэтому долговечность может быть так же важна для общественной безопасности, как и другие критерии проектирования. В будущем мы обязательно увидим более инновационные способы армирования бетона, в том числе варианты, которые я упомянул в этом видео.
Спасибо за просмотр и дайте мне знать, что вы думаете!
— Это видео взято с канала YouTube Practical Engineering, на котором есть гораздо больше видео с пояснениями по инженерным вопросам.
Бетон, армированный углеродным и стальным волокном — CEMEX USA
Использование армирования фиброй в жилых проектах обеспечивает экономичный способ использовать все лучшее в бетонных технологиях. Синтетические волокна, стальные волокна и инженерные смеси обоих материалов можно использовать для улучшения всего, от плит, проездов и патио до бассейнов, тротуаров и настилов. Волокнистое армирование также идеально подходит для использования с изолированными бетонными формами (ICF), обеспечивая домовладельцев одними из самых технологически продвинутых конструкций, доступных сегодня.
Волокна используются в строительных материалах на протяжении сотен лет. В прошлом натуральные волокна, такие как солома или шерсть животных, использовались для создания «армированного волокном» бетона. За последние несколько десятилетий волокна изменились как по форме, так и по назначению.
Описание продукта
Бетонная смесь, включающая волокнистые материалы в качестве альтернативы сварной проволочной сетке для вторичного армирования.
Волокна в бетоне обычно рассматриваются как микроволокна или макроволокна в зависимости от относительного размера волокна.Микроволокно имеет диаметр менее 0,3 мм (0,012 дюйма), а макроволокно имеет диаметр, равный или более 0,3 мм (0,012 дюйма). Существует четыре основных категории бетона, армированного фиброй, в зависимости от материала, из которого он производится.
- Тип I: Сталь, армированная волокнами бетон — нержавеющая сталь, легированная сталь или волокна из углеродистой стали, соответствующие ASTM A820
- Тип II: Бетон, армированный стекловолокном — устойчивое к щелочам стекловолокно в соответствии с ASTM C1666
- Тип III: Бетон, армированный синтетическим волокном — искусственные волокна, такие как углерод, нейлон, полиэстер и полиолефины
- Тип IV: Бетон, армированный натуральными волокнами, целлюлозные волокна различных растений
Использование / применение
Обычно используется в плитах перекрытий, приподнятых металлических поддонах и плоских работах. Также используется в изоляционных бетонных формах (ICF) для жилищного строительства.
Техническая информация о продукте
Не вызывает коррозии, повышенная ударопрочность, ударопрочность и абразивная стойкость; многомерное армирование; всегда позиционируется в соответствии с нормами.
Преимущества продукта
Армирование по всей бетонной секции: добавляя миллионы волокон к бетонной смеси, бетон достигает трехмерного армирования.
Повышенная скорость строительства: добавление арматуры в бетонную смесь ускоряет строительство и снижает трудозатраты.
Специальное оборудование не требуется: добавление армирования волокном в обычно используемые конструкции бетонных смесей и обычные бетононасосы не требует дополнительных затрат на оборудование.
Волоконное армирование также препятствует образованию трещин пластической усадки, снижает образование трещин в результате пластического оседания, увеличивает прочность в сыром виде и улучшает когезию смеси, что дает вам прочный бетон, не требующий особого ухода.
Волокна улучшают свойства свежего и затвердевшего бетона.В свежем бетоне волокна помогают уменьшить просачивание, оседание и растрескивание, связанное с оседанием. Волокна также помогают свести к минимуму развитие трещин пластической усадки, которые имеют тенденцию образовываться при неблагоприятных погодных условиях, таких как жаркая, сухая и ветреная погода.
В затвердевшем бетоне основным преимуществом волокон является их способность улучшать несущую способность бетона после растрескивания или его прочность на изгиб.
Дополнительная информация
http: //www.nrmca.org / aboutconcrete / cips / 24p.pdf
армирующих волокон — Vectorply
Стекловолокно: E-стекло
Стекло Е (стекло «электрического» класса) на сегодняшний день является наиболее часто используемым волокном в армированных пластиковых композитах. Во многих отраслях промышленности на его долю приходится более 90% используемого армирования.
Его основные преимущества:
- Низкая стоимость
- Высокая прочность
- Легкий вес (относительно стали)
- Высокая химическая стойкость
Основные недостатки:
- Низкий модуль (по сравнению с другими армирующими волокнами)
- Низкое сопротивление усталости (по сравнению с углеродными волокнами)
- Большой вес (по сравнению с другими армирующими волокнами)
- Сильноабразивный при механической обработке
- Подверженность коррозии под напряжением
Из-за широкого использования преимущества имеют тенденцию перевешивать недостатки.Почти все стекловолокна продаются в виде прядей из сгруппированных волокон или ровниц, связанных с определенным выходом. Урожайность — это количество ярдов ровницы на фунт. Метрическая единица измерения — TEX, которая представляет собой вес в граммах на километр (1000 метров). Уравнение для преобразования TEX в доходность (YPP):
Для армирующих тканей, соединенных стежком, типичные размеры ровницы находятся в диапазоне от 1800 до 113 выхода (от 276 до 4390 TEX).
Некоторые общие параметры выхода стекла и диаметры нитей накала приведены в таблице ниже:
4400 113 24, 94, Т 2400 206 17, 67, MN 1100 450 17, 67, MN 735 675 13, 51, К 276 1800 13, 51, К
Диаметр отдельных нитей может иметь значение, поскольку он представляет собой отношение площади поверхности волокна к его объему.Меньший диаметр нити дает более высокое отношение площади поверхности к объему, что означает, что у смолы больше площади для сцепления.
В некоторых случаях более мелкие нити могут давать немного лучшие свойства.
Стекловолокно: стекло E-CR
Стекло
E-CR (стекло «Электротехническое», «устойчивое к коррозии») представляет собой разновидность стекловолокна E, которое более устойчиво к разрушению в сильно кислой среде. Основное различие между стеклом E и E-CR заключается в отсутствии оксида бора (B2O3) из основного состава.Это различие привело к тому, что свинцовое стекло E-CR обычно называют «стеклом, не содержащим бор», и его можно найти во многих применениях в области коррозии композитных материалов, таких как трубы для отверждения на месте (CIPP), резервуары и трубы для хранения химикатов.
Стекловолокно: S-стекло
S-Glass (стекло с высокой «прочностью») — это улучшенное стекловолокно для использования в более требовательных к структуре приложениях. Оно имеет значительно более высокую прочность и умеренно большую жесткость, чем стандартное стекловолокно E. Плотность S-стекла немного ниже, чем у E-стекла (2.
49 г / куб. См против 2,54 г / куб. См), следовательно, можно ожидать, что ламинат будет на 20-35% легче, чем аналог из стекловолокна E. Стекло S-2 (а теперь и S-1) представляет собой коммерческую версию S-стекла, изготовленную с менее строгими невоенными спецификациями, но его свойства аналогичны. Существуют и другие варианты высокопрочного стекловолокна, такие как базальт (также известный как R-стекло), которые пытаются обеспечить эквивалентные свойства S-стекла при более низкой стоимости.
Арамид
Арамидные волокна представляют собой высококристаллический ароматический полиамид, получаемый путем экструзии кислого раствора патентованного предшественника.Арамидные волокна имеют очень низкую плотность и высокую удельную прочность на разрыв по сравнению с обычно доступными армирующими волокнами. Они наиболее известны своим использованием в пуленепробиваемых жилетах, брюках для бензопил, защитных перчатках и других областях, где требуется устойчивость к порезам и устойчивость к повреждениям.
Основные преимущества арамидных волокон:
- Легкий
- Высокая устойчивость к ударным повреждениям
- Высокая прочность на разрыв
- Умеренно высокий модуль упругости (на полпути между стеклом E и углеродом HS)
- Отличное гашение вибрации
- Низкое (отрицательное) продольное тепловое расширение
Основными недостатками арамида являются:
- Очень низкая прочность на сжатие
- Восприимчивость к УФ-излучению
- Сложно обрабатывать
- Высокое влагопоглощение
- Очень высокое поперечное тепловое расширение
Арамидные волокна часто используются в сочетании с другими типами волокон.Это позволяет конструктору воспользоваться их уникальными свойствами и малым весом, избегая при этом недостатков. Арамидные волокна продаются в нескрученных жгутах по денье (г / 9000 м), который связан с выходом или текс следующими уравнениями:
Углеродное волокно
Углеродное волокно в последние несколько десятилетий все чаще используется в высокопроизводительных приложениях, таких как аэрокосмическая промышленность, производство спортивных товаров, морской транспорт и инфраструктура.
Сочетание превосходной жесткости, прочности, сопротивления усталости и небольшого веса делает его идеальным армирующим волокном для высокоэффективных композитов.
Недвижимость
По сравнению со всеми другими текущими коммерчески доступными армирующими волокнами, углеродное волокно обеспечивает наибольший удельный модуль и удельную прочность (модуль и / или прочность, деленную на плотность волокна), а также наибольший диапазон этих свойств.
Другие свойства, такие как высокое сопротивление усталости, теплопроводность и электрическая проводимость, а также низкое тепловое расширение, позволяют использовать углеродное волокно в тех областях, где это невозможно со стандартным Е-стеклом или арамидами.Многоосные арматуры, такие как VectorUltra ™, позволяют адаптировать эти уникальные свойства к конкретным потребностям любого приложения.
Типы углеродного волокна на основе PAN
На основе PAN: наиболее широко доступный и используемый тип углеродного волокна, производится из волокна-предшественника полиакрилонитрила (PAN) специальной формулы.
Углеродное волокно PAN обычно делится на 3 группы в зависимости от модуля:
* Примечание. Модуль упругости, прочность и удлинение углеродного волокна до изгиба являются идеальными значениями, полученными при испытании пропитанной пряди, и могут не напрямую отражаться на соответствующих свойствах ткани / композита из-за смещения волокон, совместимости со смолами и повреждения во время обработки.
Углеродное волокно со стандартным модулем упругости (SM) или высокой прочностью (HS)
является наиболее широко используемым и экономичным волокном для промышленных применений, таких как морская промышленность, энергия ветра и транспорт. Этот тип волокна получил свое название от первых лет углеродного волокна, когда прочность на растяжение значительно снизилась при увеличении модуля. За это время предел прочности на разрыв для волокна со стандартным модулем упругости достигал максимума около 500 фунтов на квадратный дюйм (3450 МПа), в то время как у высокомодульного волокна был намного ниже, около 275 фунтов на квадратный дюйм (1890 МПа).
Углеродные волокна HS по-прежнему обладают одними из самых высоких значений прочности среди всех армирующих волокон промышленного класса, а также по модулю примерно в 3 раза выше, чем у стандартного стекла E. Относительно высокое удлинение до разрушения (1,5–2,0% идеальных значений волокна) углеродных волокон HS также позволяет использовать их в высокодинамичных приложениях, таких как корпуса яхт, летучие мыши для софтбола и защитные кожухи лопастей реактивных двигателей.
Волокна
с промежуточным модулем упругости (IM) были разработаны для высокоэффективных аэрокосмических применений, которые требовали как большей прочности, так и модуля упругости, чем стандартные углеродные волокна HS.Углеродные волокна IM по-прежнему используются в основном в аэрокосмической отрасли, но также используются в высокопроизводительных сосудах под давлением, лонжеронах парусных лодок и других промышленных приложениях, где производительность превышает цену.
Волокна
с высоким модулем упругости (HM) обычно используются в высококачественных спортивных товарах и космических конструкциях, где высокая жесткость и малое или нулевое тепловое расширение обеспечивают оптимальный вес и характеристики.
Обычно при увеличении модуля прочность снижается из-за повышенной кристаллизации волокна.За прошедшие годы были разработаны разработки, направленные на повышение прочности волокон HM, снижение их хрупкости (идеальное удлинение волокна до разрушения по-прежнему составляет около 0,5–1,4%) и увеличение их использования. По мере увеличения модуля увеличивается и цена, что делает волокна HM наиболее дорогими и наименее производимыми углеродными волокнами на основе PAN. Углеродные волокна IM и HM меньше по диаметру, чем волокна HS (5 мкм и 7 мкм соответственно), что дает более тонкий выход или значение TEX для того же размера жгута.
Буксирный размер
Количество нитей на пряжу углеродного волокна обозначается как размер его жгута.Размер жгута обычно указывается в единицах «К» или тысячах нитей. Стандартные размеры жгута варьируются от 1K (1000 нитей) до 48K (48000 нитей), а иногда и выше. В большинстве аэрокосмических приложений используются небольшие буксировочные буксиры, такие как 3K и 6K, в то время как в более промышленных приложениях используются буксиры 12K, 24K и 48K.
Как правило, жгуты меньшего размера производят более легкие ткани с хорошим охватом, в то время как более крупные жгуты производят более тяжелые ткани. Жгуты меньшего размера также требуют больших затрат на производство, чем жгуты большего размера (при данной технологической установке производится меньше материала), и, следовательно, они более дороги.
Армирующие волокна | Полимер, сталь, полипропилен для бетона
Полимерное волокно Baumex®
Стальная фибра Baumix®
Полипропиленовое волокно Baucon®
Бетон , армированный полимерными, стальными и полипропиленовыми волокнами (фибробетон) относится к так называемым композиционным материалам.По сравнению с обычным бетоном, фибробетон характеризуется улучшенным контролем трещин, лучшим сопротивлением усталости, более высокими показателями прочности на растяжение.
Уровень характеристик волокон сильно зависит от качества и количества нанесенных волокон, их формы и размеров, а также их адгезии к зрелому бетону. Используя наш опыт производства промышленных полов и в сотрудничестве с ведущими исследовательскими центрами в Польше, мы разработали и запатентовали наш собственный ассортимент полимерных волокон Baumex®, стальных волокон Baumix® и полипропиленовых волокон Baucon®.
РЕКОМЕНДУЕТСЯ ПОЛИМЕРНОЕ ВОЛОКНО
Полимерное волокно BAUMEX® — запатентованное инновационное синтетическое волокно, использующее свойства современных полимеров: исключительную прочность и гибкость. Специально разработанная форма вместе с передовыми материалами приводит к созданию уникального волокна, способного заменить традиционную стальную сетку или арматуру из стальных волокон, а также обеспечить впечатляющую прочность бетона на растяжение.
Каталог Технический лист
СТАЛЬНОЕ Волокно
Благодаря относительно коротким и тонким стальным волокнам Baumix® — фибробетон становится более однородным , чем традиционный бетон. Это связано с крючковатыми окончаниями волокон Baumix, которые отлично закрепляются в бетонной матрице. Тем не менее, волокна Baumix® еще более эффективны из-за их тонкости (отношение длины к диаметру). Чем выше тонкость, тем эффективнее волокно и ниже доза на кубический метр.
d — диаметр, l — длина, λ — тонкость (отношение длины к диаметру)
Стальная фибра , как альтернатива традиционной арматуре, также поддерживается по экономическим причинам, например возможно, гораздо более тонкая бетонная плита , меньшие затраты на материалы, рабочую силу и транспортировку, необходимые для традиционного армирования бетона сварной сеткой.
Бетон, армированный стальными волокнами Baumix® — это однородный материал с однородно распределенным армированием, в результате чего получается:
- Повышенная прочность на разрыв при изгибе
- Повышенная прочность
- Усадка уменьшена на 20-40%
- Повышенное сопротивление сжатию
- Повышенная пыленепроницаемость
- Высокая ударопрочность при статической и динамической нагрузке
- Морозостойкость повышенная
- Повышенная стойкость к ржавчине
- Повышенное сопротивление усталости
- Сопротивление резким изменениям температуры при высоких температурах
Технический лист
ПОЛИПРОПИЛЕНОВОЕ волокно
Полипропиленовые волокна BAUCON® используются для предотвращения усадки бетона.
Они работают до тех пор, пока сам бетон не сможет выдерживать большую нагрузку, чем полипропиленовое волокно. Инновационная форма полипропиленового волокна Baucon® позволяет использовать только 600 г волокна на кубический метр. м, чтобы бетонная смесь была достаточно прочной.
Волокна полипропиленовые
Добавьте полипропиленовых волокон в бетон, чтобы получить следующее:
- предотвращение трещин при затвердевании бетона
- избегать стальной сварной проволочной сетки
- минимизировать водопоглощение
- Повышение морозостойкости
- улучшить однородность бетона
- улучшить защиту от ржавчины
- повысить пыленепроницаемость
Технический лист
Полимерное армирующее волокно BAUMEX®
Чрезвычайно прочные и гибкие синтетические полимерные волокна.
Они могут как заменить стальную сетку или арматуру из стальной фибры, так и сделать вспомогательное армирование бетонной плиты, стены и т. Д.
Дозировка от 1,5 кг фибры на 1 м 3 бетона.
подробнее
См. Также
Теги: фибра, фибра, для промышленных полов, бетон, полимер, сталь, полипропилен
FABPRO POLYMERS ’OMEGA ™ II Стальной бетон, армирующее волокно
Детали
Описание продукта
FABPRO POLYMERS ’OMEGA ™ II Steel Reinforcing Fibre — это низкоуглеродистая листовая стальная фибра.Это проверенное в отрасли волокно обеспечивает систему армирования, которая устраняет ограниченную усадку в бетонных плитах. Стальные волокна OMEGA ™ II равномерно распределены по бетону, чтобы гарантировать владельцу, подрядчику и инженеру превосходный контроль трещин. Стальное армирующее волокно OMEGA ™ II может значительно повысить прочность на прямое растяжение и устранить WWM и арматуру в жилых, коммерческих и промышленных применениях.
OMEGA ™ II соответствует требованиям ATSM A820 / A820M, тип II «Стандартные технические условия на стальные волокна для бетона, армированного волокном», а также одобрен для использования в системах композитных металлических настилов Институтом стальных настилов.
Нужно взять с собой некоторую информацию?
Информация о продукте
Характеристики / Свойства
Точка плавления
2760 ° F (1516 ° C)
точка возгорания
1500 ° F (816 ° C)
Прочность на разрыв
60 — 120 тысяч фунтов / кв. Дюйм
Длина волокна
1.0 ”(25 мм)
Количество волокон
8000 волокон / фунт
ТЕХНИЧЕСКИЕ ХАРАКТЕРИСТИКИ
Волокна
OMEGA ™ II предназначены для контроля растрескивания из-за усадки при высыхании, теплового расширения и сжатия, а также для снижения ударопрочности и устойчивости к разрушению.
Волокна OMEGA ™ II от FABPRO POLYMERS соответствуют действующим строительным нормам и правилам ASTM C1116 / C1116M, раздел 4.1.3, тип I, и одобрены для использования в системах композитных металлических настилов Институтом стальных настилов.
OMEGA ™ II рекомендуется использовать в бетонных плитах:
- Для ограничения ширины трещин между стыками
- Для усиления сцепления агрегатов в шарнирах
- Для повышения ударопрочности
- Обеспечивает превосходный контроль трещин
- Для борьбы с растрескиванием из-за усадки и температурным растрескиванием
Волокна OMEGA ™ II компании FABPRO не должны использоваться для замены конструкционной несущей арматуры.Волокна OMEGA ™ II не должны использоваться как средство уменьшения толщины бетонных секций по сравнению с исходной конструкцией или для увеличения расстояния между стыками, превышающего размеры, рекомендованные отраслевыми стандартами PCA и ACI, без предварительной консультации с нашим инженером-проектировщиком и программой проектирования для правильных дозировок.
.
ДОЗИРОВКА
Волокна
OMEGA ™ II обычно добавляются с дозировкой от 15 до 25 фунтов / ярд3 (от 8,9 кг / м3 до 14,8 кг / м3) в стандартные сочлененные полы в соответствии с рекомендациями по проектированию ACI 360.Дозировка до 65 фунтов / ярд³ (38,6 кг / м³) может использоваться в расширенных сочлененных полах. Для перекрытий с удлиненным швом, выходящих за рамки стандартных руководств ACI 360 по проектированию плит на поддерживаемом грунте, FABPRO рекомендует проконсультироваться с нашим инженером-проектировщиком и программой проектирования для правильной дозировки.
СМЕШИВАНИЕ, РАЗМЕЩЕНИЕ И ОТДЕЛКА
Волокна
OMEGA ™ II упаковываются в коробки по 50 фунтов / ярд³ (29,7 кг / м³) и могут быть загружены в грузовик до, во время или после дозирования. Пожалуйста, следуйте надлежащим процедурам смешивания, указанным в ASTM C94 / C94M.Волокна OMEGA ™ II можно перекачивать и размещать с помощью обычного оборудования. Можно использовать ручные стяжки, но рекомендуется использовать вибрационные и лазерные стяжки, чтобы обеспечить дополнительное уплотнение и помочь скрыть волокна под поверхностью.
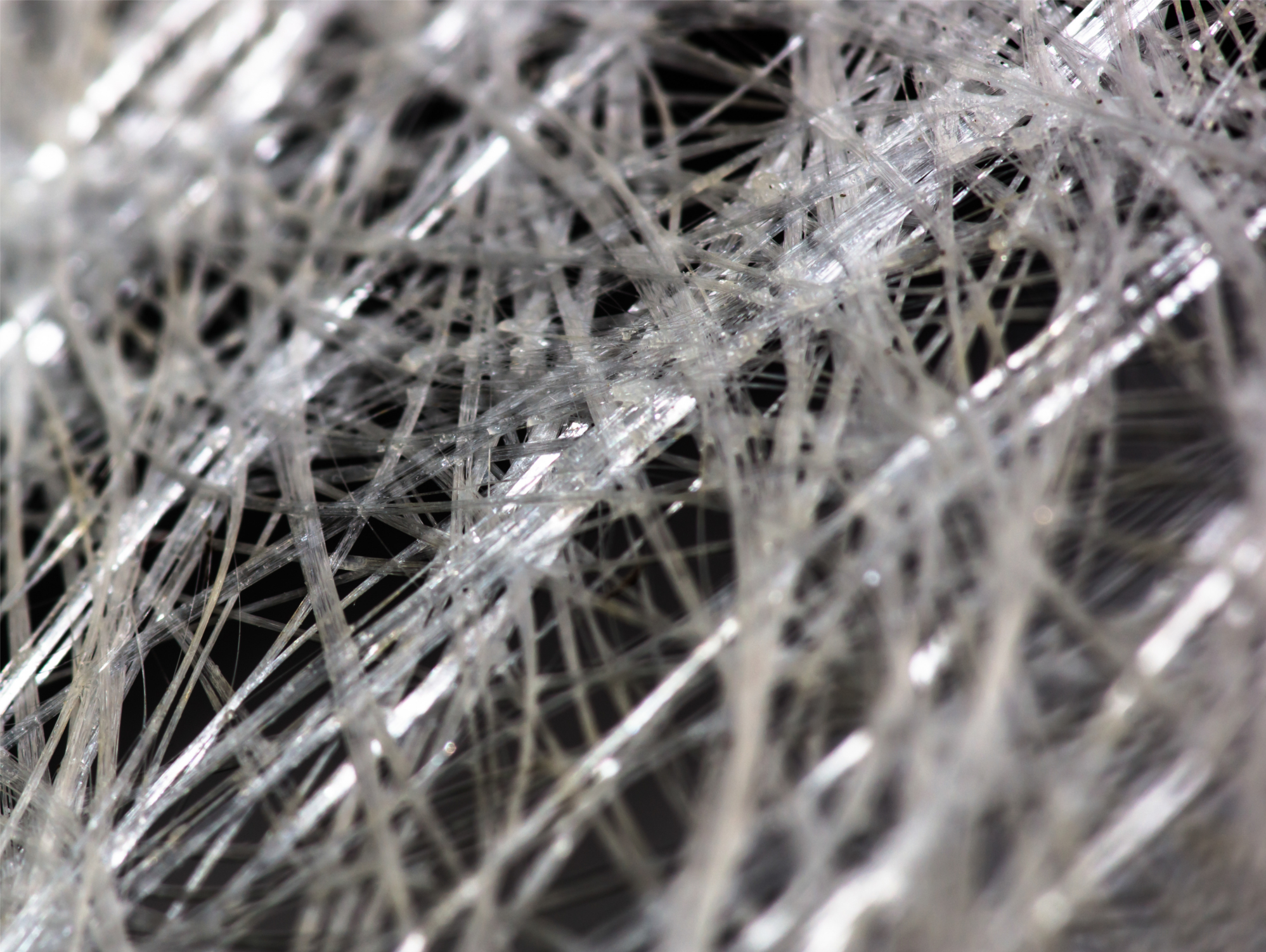

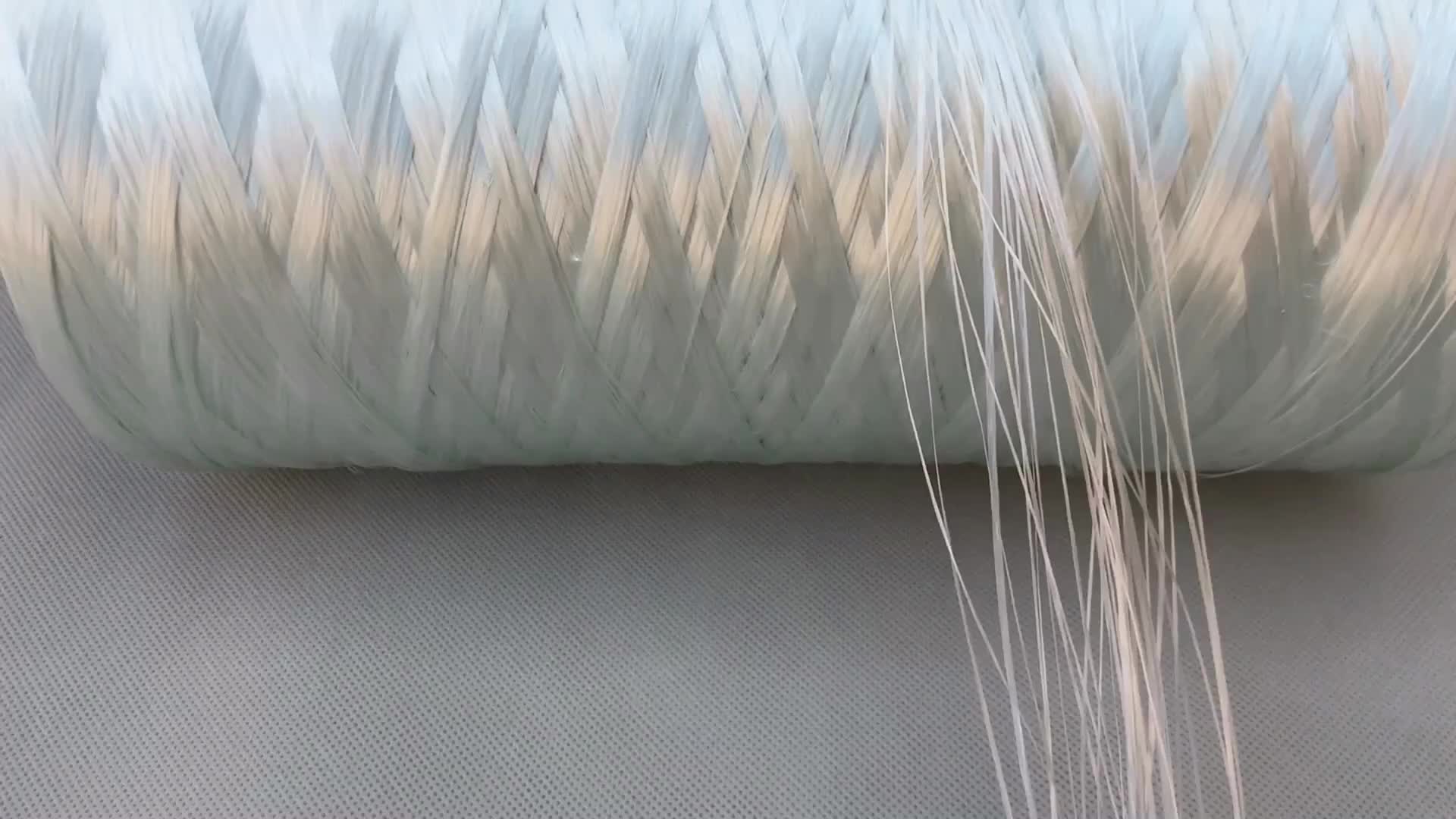



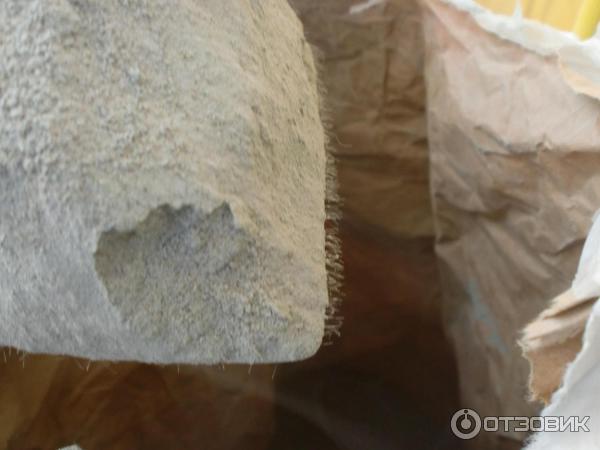



Полимерное волокно Baumex®
Стальная фибра Baumix®
Полипропиленовое волокно Baucon®
Бетон , армированный полимерными, стальными и полипропиленовыми волокнами (фибробетон) относится к так называемым композиционным материалам.По сравнению с обычным бетоном, фибробетон характеризуется улучшенным контролем трещин, лучшим сопротивлением усталости, более высокими показателями прочности на растяжение. Уровень характеристик волокон сильно зависит от качества и количества нанесенных волокон, их формы и размеров, а также их адгезии к зрелому бетону. Используя наш опыт производства промышленных полов и в сотрудничестве с ведущими исследовательскими центрами в Польше, мы разработали и запатентовали наш собственный ассортимент полимерных волокон Baumex®, стальных волокон Baumix® и полипропиленовых волокон Baucon®.
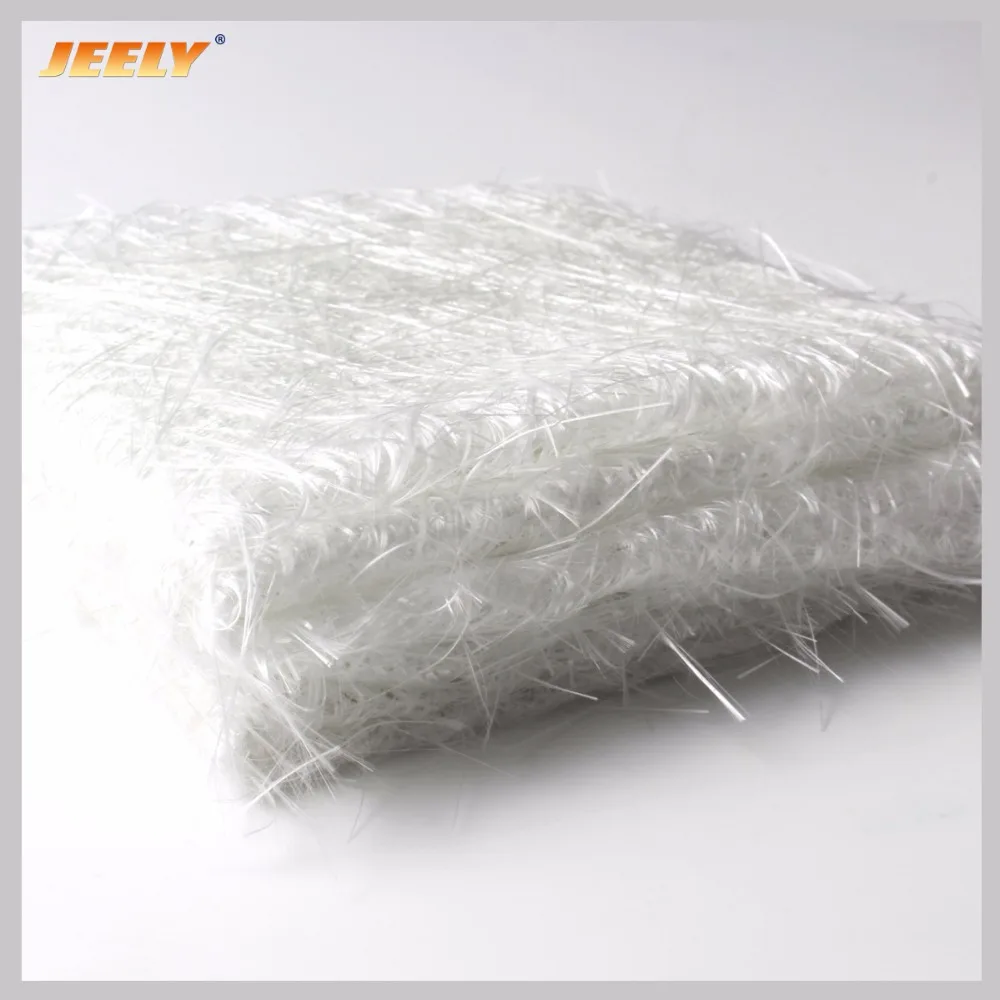

Полимерное армирующее волокно BAUMEX®
Чрезвычайно прочные и гибкие синтетические полимерные волокна. Они могут как заменить стальную сетку или арматуру из стальной фибры, так и сделать вспомогательное армирование бетонной плиты, стены и т. Д.
Дозировка от 1,5 кг фибры на 1 м 3 бетона.
подробнее



